High-Efficiency HDPE Pipe Extrusion Machines from China Manufacturers
Home » HDPE Pipe Extrusion Machine
Built for precision and durability, the HDPE pipe extrusion machine ensures smooth production for water, gas, and industrial piping. Whether you’re looking for a HDPE pipe extrusion line for large-scale operations or an HDPE pipe making machine for specialized manufacturing, these systems offer high efficiency and reliability. Contact us today for more information on HDPE pipe extrusion machine price, models, and factory info.
Get Information on HDPE Pipe Extruder Manufacturer
Find Your HDPE Pipe Extruder Machine
Key factors in selecting an extrusion system include material compatibility, energy efficiency, and control precision. The HDPE extrusion process requires stable temperature regulation and advanced die head technology to ensure uniform pipe thickness. Whether considering an HDPE extrusion line for large-scale operations or a HDPE extruder machine for customized production, evaluating automation levels and maintenance requirements will help optimize long-term performance.
HDPE Pipe Extrusion Machine for Sale
Designed for stable and efficient production, this system ensures uniform pipe extrusion with precise temperature control and energy-saving operation.
Built for high-strength, lightweight pipes, this machine produces durable corrugated structures ideal for drainage, sewage, and cable protection systems.
Features and Advantages of HDPE Pipe Production Line
- High-Precision Extrusion: Advanced screw and die head design ensure uniform pipe thickness and consistent output.
- Energy-Efficient Heating System: Optimized temperature control reduces energy consumption while maintaining processing stability.
- Automated Operation: PLC-controlled system enhances production efficiency, reducing manual intervention and improving consistency.
- Versatile Pipe Diameter Options: Machines are designed to produce a wide range of pipe sizes, meeting various industry requirements.
- Durable and Corrosion-Resistant Materials: Components are made from high-quality steel and wear-resistant alloys for long-lasting performance.
- Efficient Cooling and Vacuum Calibration: Ensures precise pipe shaping and smooth surface quality.
- High Output and Productivity: Capable of continuous, large-scale pipe production with minimal downtime.
- Cost-Effective Manufacturing: Reduces material waste and optimizes resource usage for lower production costs.
- Wide Application Range: Suitable for producing pipes for water supply, gas transportation, sewage systems, and cable protection.
- Strong Pipe Durability: HDPE pipes produced have excellent resistance to chemicals, corrosion, and environmental stress.
- Eco-Friendly Production: Low emissions and recyclable material usage make it a sustainable choice for modern manufacturing.
Extrusion Process Parameters
Parameter | Recommended Value | Effect on Final Product |
---|---|---|
Extrusion Temperature (°C) | 180-220 | Ensures smooth melt flow & uniform thickness |
Screw Speed (rpm) | 10-90 | Controls material mixing and extrusion rate |
Vacuum Calibration Pressure (MPa) | 0.02-0.05 | Helps maintain pipe roundness and stability |
Cooling Time (s) | 30-120 | Affects pipe crystallization and strength |
Pipe Types Produced by HDPE Pipe Extrusion Machines

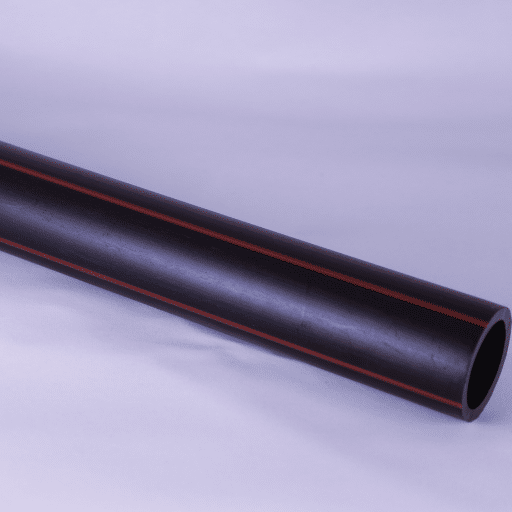
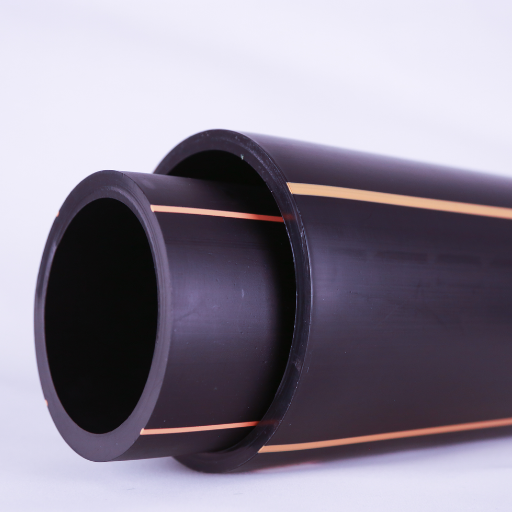
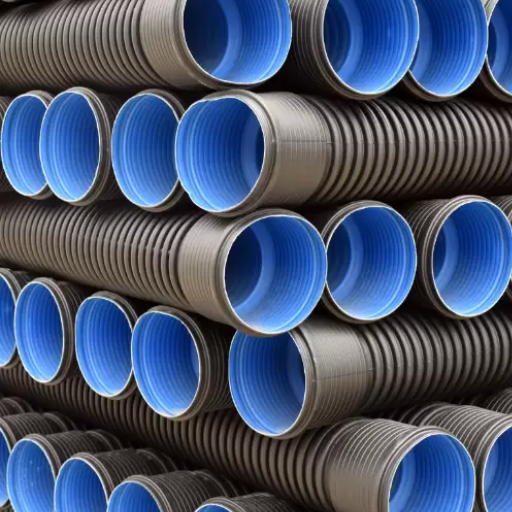

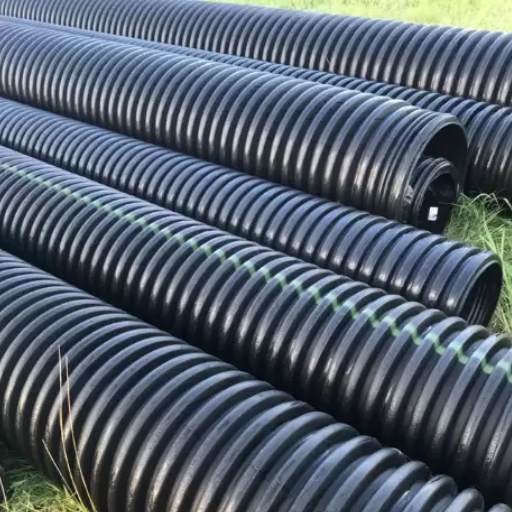
HDPE Pipe Extruder Related Articles
Combining characteristics such as strength, flexibility, and cost-effectiveness has made...
Water, oil, and gas pipelines made from high-density polyethylene (HDPE)...
To ensure accuracy, managing various factors is key to attaining...
The extrusion machines used for high-density polyethylene (HDPE) pipes are...
The extrusion of high-density polyethylene (HDPE) pipes is essential for...
Frequently Asked Questions
What factors affect HDPE extruder machine price?
The cost varies based on screw diameter, production capacity, automation level, and additional features like vacuum calibration and co-extrusion capabilities. Higher output machines and fully automated systems tend to have a higher price but offer better efficiency and lower long-term costs.
What are the main components of an HDPE pipe extrusion line?
A complete system typically includes an extruder, die head, vacuum calibration tank, cooling tank, haul-off unit, and cutting machine. Some setups may also include co-extrusion units for multi-layer pipes and automatic pipe coilers for smaller diameters.
How do I choose the right HDPE pipe extruder machine for my production needs?
Consider factors like pipe diameter range, output capacity, and automation level. If producing high-pressure pipes for gas or water supply, a system with precise temperature control and high-torque motors is essential.
What materials can be processed with an HDPE extrusion machine?
HDPE pipe extrusion machines are designed specifically for processing high-density polyethylene (HDPE), but some models can also handle materials like PPR or PE-RT for different applications.
What is the typical output capacity of an HDPE extrusion machine?
Production output depends on the screw diameter and design. Smaller extruders may produce 100-300 kg/h, while larger industrial-scale systems can exceed 1000 kg/h for high-speed production lines.
How does the cooling system impact the quality of HDPE pipes?
Efficient cooling is critical for maintaining pipe roundness and strength. Most systems use a combination of vacuum calibration and water cooling tanks to achieve consistent pipe dimensions and surface smoothness.
Is it possible to produce multi-layer HDPE pipes with one extrusion line?
Yes, co-extrusion technology allows the production of multi-layer pipes with different material compositions, enhancing strength, flexibility, and resistance to external factors like UV exposure.
What maintenance is required to keep an HDPE pipe extrusion machine running efficiently?
Regular maintenance includes checking the screw and barrel for wear, cleaning the die head, ensuring proper lubrication of moving parts, and inspecting the cooling and vacuum systems for optimal performance.