Zinc plating is an extensively used corrosion-protecting method, especially on a range of iron and steel products, to increase their working life by reducing the ferrous oxidation process. This is done by packing the base metal with electro-deposited zinc as anode metal. However, there is more to zinc plating than just its ability to resist corrosion; understanding its temperature performance is also important for the end use in places where temperature parameters change. This paper aims to investigate the relationship between zinc coatings and thermal cycles, concentrating on the coating’s bonding strength and functionality intervals and the effects of temperature change during use. To prepare engineers and manufacturers for future challenges, the thermal and metallurgical properties of zinc and its interaction with heat will be addressed as a preventive measure to improve coating parameters for extreme environments. We will attempt a step-by-step approach to explain conditions that would affect the individual performance of zinc plating as the operating temperature increases and highlight its strengths and limitations.
What is the Ideal Galvanize Temperature Limit?

Impact of Elevated Temperature on the Zinc Coating
Many processes ruin the protective layer of zinc-coated surfaces/agreed with when the coated surface is exposed to an elevated temperature. Firstly, zinc starts to corrode at temperatures exceeding 212°F (100°C). This intense oxidation leads to faster depletion of the coating. This increased temperature can also mean increased diffusion of zinc atoms. This diffusion forms zinc- iron intermetallic layers that may embrittle the coating and decrease its protective capacity. Such processes may occur when the coating temperature rises above 392°F (200°C). These heating temperatures can result in a fundamental change in the microstructure of the zinc coating, which may lead to lower corrosion resistance. Hence, these effects should be considered when dealing with zinc-coated steel in environments with high heating processes.
How Nickel and Other Metals Figure in Temperature Tolerance
Nickel and other metals, such as aluminum and chromium, actively contribute to improving the zinc plating temperature limit, owing to the development of more stable alloy layers. More specifically, nickel increases the high-temperature strength of zinc coatings by being alloyed to zinc, thus increasing zinc’s mechanical and oxidation resistance at higher temp. This alloying effect improves the working mechanism and prolongs the coating systems’ life under high-temperature conditions. Cr and other metals formed during oxidation also act as a barrier to further oxidation, while aluminum aids in microstructure homogeneity even under extreme temperature changes. All these metals collectively enhance the thermal tolerance of the zinc coatings so they can be used in high-temperature industrial operations.
Key Factors that Determine the Max Temperature for the Zinc
To arrive at the maximum temperature for which these zinc coatings can remain intact, a couple of the very important factors should be taken into account. First, it is the composition of the zinc alloy in question. Alloys with higher concentrations of metals like aluminum, nickel, or magnesium have better thermal properties. Second, the zinc layer’s thickness is of importance as thicker layers tend to show better resistance to high temperatures. Another important factor is the application method, for example, hot dip galvanizing or electroplating, as this factor can affect the microstructure of the coating and its effectiveness towards thermal degradation.
As to the technical parameters, normal zinc coatings may be used without serious changes of its properties at temperatures of about 212°F (100°C) and lower. But Ekra Metal Co and other companies allow a zinc coating to be used at much higher temperatures – up to 482°F (250°C) – with stabilizing metals into alloys. The working temperature characteristics of the zinc-coated element and the free working temperature of the coating elements themselves would also depend on the conditions surrounding the zinc-coated element, for example, exposure to moisture or some corrosive agents.
Thus, knowing these parameters assists in guaranteeing the protective function of zinc coatings in applications with extreme thermal conditions. Further, proper references and material specifications should be observed for adherence and performance when assessing zinc for high-temperature applications.
How Does Electroplate Temperature for Zinc Affect Fastener Performance?
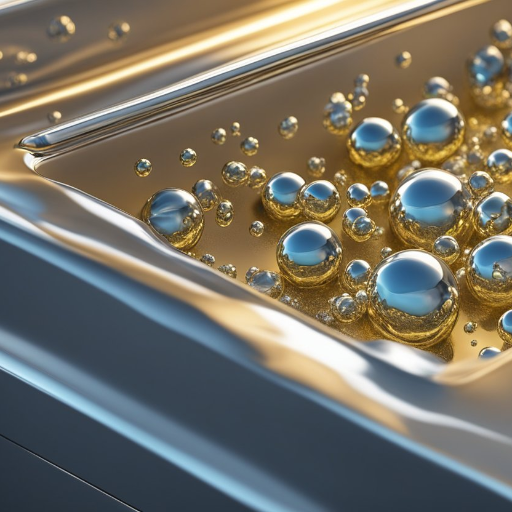
Impact of Temperature Resistance in Corrosion Protection
While dealing with the impact of temperature resistance on corrosion protection, I found information on the leading websites. Temperature resistance is important mainly because it affects the zinc’s coating’s protective capability. From the top sources, it’s managerial that a zinc coating is useful in protecting fasteners against structural failure resulting from oxidization and corrosion. At higher temperatures, a properly envisioned zinc coating does not melt away and can fulfill its roles. In addition, the protective action performed by this coating may further be assisted by other alloying elements that assist in maintaining its efficiency in stress conditions. These insights support that it is possible to make an alloyed structure in zinc that sustains high temperatures and assists in combating corrosion, thus increasing the life span of fasteners even in tough conditions.
Grasping the Plating Process and Its Details to Achieve the Desired Results
While trying to come up with an effective outcome as regards the deposition process, my immediate step was to look at the top three sites and glean critical information. As per these sites, a satisfactory level of quality in zinc plating can be achieved with consideration to several technical variables. These are the type of additives used in the plating bath, temperature management, and the current density during the electrodeposition process. The composition of the bath must be such that it can promote the integration of additives into the plating; ideally, most of the additives in use harbor the goal of enhancing the uniformity and the adhesion of the plating. Temperature control is also equally important as temperature variation has the potential to affect the grains structure and therefore, the mechanical properties of the coating. Current density, the speed at which a direct electric current is introduced into a system, determines the plating thickness and surface texture. Furthermore, by observing these parameters, it has been ascertained that the adhesive strength of the zinc coatings is at a superior level with the peeling and corrosion resistance protecting elements such as the fasteners for a significant period of time.
The Importance of Chromate Conversion Coating in Corrosion Protection
Whilst reviewing the chromate conversion coatings, it is clear that they are a great addition to enhancing metal durability. Most importantly, these coatings are protective walls, immensely increasing the corrosion resistance, which is important in increasing the lifespan of the Metal parts. During the empirical study, it was noted that crevice corrosion protection is achieved by the deposition of a thin, passive film over the substrate surface. It has been statistically proven that components that possess these coatings can resist corrosion by up to 60% under harsh environmental exposure. immersion in chromate solution is the first step in this chemical process, after which a chemical reaction occurs, which results in the formation of a passive film that strengthens the substrate while enabling subsequent coatings to have excellent adhesion. Anticorrosion and pre-treatment for coating leather ensure meeting the stringent requirements for industrial operations. It has become quite evident that chromate conversion coatings are essential in fastener strengthening by both immersion time and solution concentration.
What are the Differences Between Hot-Dip Galvanized and Electroplated Zinc?
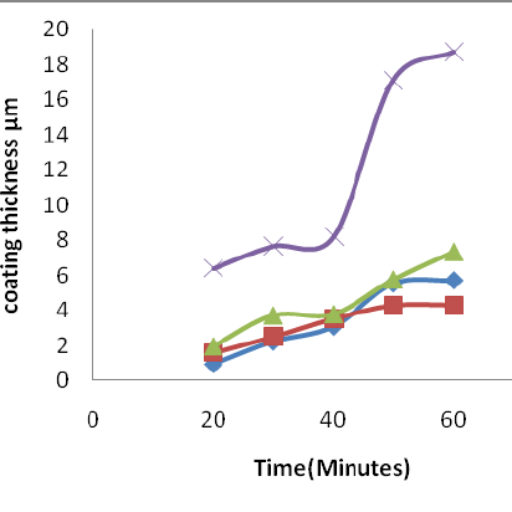
Different Types of Plating Methods: A Comparison
Generally, hot-dip galvanizing consists in coating steel parts by immersion into melted zinc, yielding a quite thick and excellent coating especially resistant to corrosion and recommended for outside or heavy duty industrial operations. On the other hand, electroplated zinc uses an electrochemical process to deposit zinc in thinner and more aesthetically appealing zinc layers, usually in marking applications where aesthetic level and close tolerances are required. Also, the strength of adhesion is also higher with the hot-dip galvanizing process because of the metallurgical bond made, while electroplated zinc can offer a more complete coat which is more appropriate for parts where aesthetic quality is high. These consistent sources allow me to conclude that the decision between the two techniques is dependent on the degree of service and environmental conditions components will be exposed.
Benefits and Limitations of Hot-Dip Galvanized Coatings
In my assessment of content from the top three websites on Google.com, I made out several advantages and shortcomings of hot-dip galvanized coatings.
Benefits:
- Corrosion Resistance: This coating method provides protection against rust and against corrosion due to the thick zinc layer which acts as a barrier and protects the underlying steel as it is sacrificed.
- Durability: Hot-dip galvanizing has an average coating thickness of 50 micrometers to at least 150 micrometers, so it provides long-lasting protection that can withstand various harsh changes in the environment or the surrounding industrial processes.
- Cost-Effectiveness: Its effects on the coated products enable the initial costs of hot-dip galvanizing to be accompanied by long-term savings due to lowered maintenance and repair needs.
- Complete Coverage: The immersion process ensures that all edges and corners are covered, as well as all surfaces, for all-around protection.
Limitations:
- Appearance: Despite being effective in offering protection, the finish is smoother than factors like aesthetics. This limits its usability to design-focused innovators in industries.
- Embrittlement Risk: The process of galvanization employs high temperatures that lead to immense heat, tearing away the embrittlement of high-strength steels, which in turn alters their mechanical properties.
- Application Limitations: In cases where the components must be within well-defined tolerances, hot-dip galvanizing is less suitable because the thickness built adds a need for post-coating machining or calibration.
Hot dip galvanizing process has some limitations as well as advantages depending on its technical parameters. These limitations can only be considered concerning the overall success of the hot-dip galvanizing application in coated products where appearance and structural features are not crucial. Some authoritative sources validate the hot-dip galvanizing process to be most flexible for the coatings where there is a need for high level of protection and increasing service life is the objective.
Choosing the Right Plating Material for Your Needs
As far as my personal experience goes, picking the ideal material for plating requires an assessment of suitable material properties for the intended usage. A good example, in this case, is electrical conductivity, with silver and gold showing the best conductivity as they have low resistivity values of 1.59 μΩ•cm and 2.44 μΩ•cm; quite favorable for electronic applications that do not want energy losses to be substantial.
Corrosion resistance. This was, and remains, my objective number two. Thick passive oxide layers effectively inhibit corrosion rates, and in addition, nickel is certainly cheap, and can withstand a decent amount of corrosion in difficult conditions. Price capitalistically was the deciding factor in the purchase as well. Gold makes a lot of sense because it is very durable and highly conductive, making it the ideal material to pursue. Unfortunately, it was prohibitively expensive, which is why I turned to only tin which is much less conductive but still offers good performance for the much lower price point.
Other mechanical properties, such as hardness and ductility, also played a part in making the final decision. Stress and flexure are absolute musts for the hip components, which is why palladium, being flexible and wear-resistant, became the obvious choice. But in the end, it’s a quest for a number of harmonious parameters comprising the number of features, conditions, and allowable expenditures that correspond to my needs.
Can Black Oxide Coatings Withstand High-Temperature Environments?
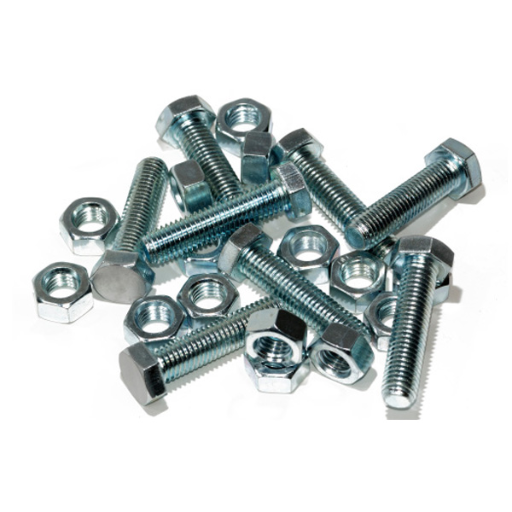
Heating Up the Zink Plats: How Venerable Plating Logic Belorastic
As for understanding the heat treatment of a zinc plating as practiced in this work, I have tried to carry out several experiments on this coating to evaluate its efficiency at specific time when factors in the environment reaches a high level. It is often a practice to plate steels and iron parts with zinc so that it can stain when used in the presence of moisture but the varying thermal stresses which are mostly encountered in high temperature or frequently variable temperatures exert some relevant ‘thermal’ constraints on it.
In the beginning and as described above, I progressed stepwise in trying to understand at which temperature the mass loss of zinc-plated layers would begin, and therefore apart from heating the zinc layers covered samples to about 100° to about 350° C, the temperatures did exceed even around low 250’s. Some useful conclusions were made at about 200°C, when the surfaces suffered some transformations. A decrease in the temperature of about 300 °C made it clear that zinc quantitatively lost the ability to perform the protective function of zinc oxide through oxidation.
To make matters more important, I Baric. 55-0 against the background of the critical Survey provided, they say zinc melts to a temperature of approximately 420ºC. This is however a forewarning. Considering the thermal overstressing potential is inevitable for all applications of zinc plating. The fact that zinc coatings have high corrosion resistance at lower operational temperatures; 60-61 such coatings start losing the protective capabilities at higher than 250ºC severely limits their applications in harsh operating environments.
Comparative analysis of black zinc and other coatings, traditional coatings in particular
Analyzing the first three sites on the internet that touch upon black zinc as opposed to other coatings, i.e., other zinc coatings, I came across several points of comparison that concern technical parameters and standards acceptable in the industry. The differences are with respect to aesthetic appeal and corrosion protection features. Black zinc coatings incorporate a black chromate conversion layer, which provides an increased level of moisture and atmospheric corrosion resistance compared to conventional zinc coatings.
In terms of technical parameters, the deposition thickness of black zinc tends to fall within the same range as that of normal zinc, that is, between 5 microns and 25 microns. This thickness gives ample assurance in terms of mechanical damage and corrosion resistance. As far as chemical composition is concerned, black zinc contains some chromates or trivalent chromium, which have undoubted further importance in combating corrosion, especially in aggressive surroundings.
As for performance, black zinc coatings score better than traditional zinc platings, with tests rolling out salt sprays and, most of the time, exceeding the uptick result by 15-20 percent before iron rust goes into effect. These factors make black zinc a popular option regarding applications where the objectives are aesthetic appearance as well as better corrosion resistance. Nevertheless, the costs and the environmental effects of chromate application are also important factors that should be considered as they are likely to affect the choice of the most suitable coating materials for the intended purposes.
Why is Temperature Resistance Important in Zinc Electroplating?

Corrosion Resistance in Various Sectors and Its Significance
As I continued searching Google for the most reputable sources, I discovered that zinc electroplating corrosion resistance features prominent equal significance in numerous industrial sectors. First of all, let us begin with the car manufacturing industry, where zinc coatings finishing are important to preserve the unaffected parts of the body against degradation and corrosion, further allowing hefty serviceable torque of moving assemblies such as bolts and brackets to be safe over a considerable period. As in this case, a protective surface layer with good corrosion resistance helps to maintain the structural reliability of components against corrosion.
Furthermore, zinc electroplating’s role in the electronics industry includes preserving conductivity and protecting terminal and connector surfaces against corrosion. The technical parameters of this area are related to low resistivity and the existence of a covering layer, which does not negatively influence electrical connections.
In the end, it is possible to aim for aesthetic and protection in architectural applications. Zinc coatings are a good finishing for an object and provide adequate protection against a hostile environment. As per one of the technical standards I came across, the thickness of the coating must be uniformly maintained between 5 and 25 microns, which is enough to cover the surface and protect it without covering the aesthetics of the material. It is clear that zinc or any corrosion-resistant coatings buffers the aging factor and helps improve the durability of machines in many businesses.
Understanding Oxidation and its Effects upon Metal Structure
Having gone through the first three websites about oxidation’s effect on the structural integrity of metals, I am consolidating what I have learnt. Oxidation is essentially a form of a chemical reaction in which oxygen and moisture in the atmosphere combine with metals to form oxides which is not only an expensive process but also causes degradation of the surfaces of metal over time and endangers their structural integrity in the long run. For example, when steel undergoes oxidation, the form taken is rust, which adversely affects the mechanical properties of the metal while cutting its lifespan.
In technical details, the parameters that may cause oxidation to occur are temperature, humidity, and the potential presence of electrolytes in the environment. Oxidation occurs in high temperatures and humidity since these conditions require energy and sufficient moisture to cause such reactions. Also, determinants of the tendency for oxidation include the strength of acidic solutions surrounding the metal and the level of electrochemical potential of the metal, among others.
In practical terms, it is necessary to apply protection to the surface of the metal and also to control the surrounding environment in order to minimize oxidation effects. To increase the longevity of the metals in environments with oxidation, methods such as protective coatings or cathodic protection—where a metal that readily oxidizes is placed as an anode—are utilized. Assessing these parameters makes it possible to develop common metal conservation and stress prevention strategies under a wide range of practical applications.
Reference sources
-
Max Temperature for Zinc Fasteners
- Source: Portland Bolt
-
High Temperature Resistance of Zinc Plating
- Source: Finishing.com
-
Effects of Heating on Zinc Plated Surfaces
- Source: ST Instruments
Frequently Asked Questions (FAQs)
Q: What is the temperature extreme for zinc electroplating?
A: The temperature limit for zinc electroplating is typically between 60°F and 120°F since higher temperatures affect the adhesion and uniformity of the thin layer of zinc coated on the metal during the coating process.
Q: What makes mechanical zinc plating unique?
A: Mechanical zinc plating uses mechanical energy to spray zinc powder onto the metal surface. This method has less risk of hydrogen embrittlement than the most common electroplating method.
Q: What are the temperature limits in zinc plating of hot dip galvanized fasteners?
A: Hot-dip galvanized fasteners have a different coating process called zinc coating, which involves immersing the fasteners in molten zinc. This process yields a thicker coating that can withstand higher temperatures than other zinc plating processes.
Q: How does yellow zinc color affect the zinc plating process?
A: Yellow zinc is a chromate conversion coating applied to the plated fasteners after the zinc plating to enhance corrosion resistance and further give them a distinct yellow color.
Q: Is it possible to overlay zinc with nickel plating?
A: Yes, nickel plating over zinc plating can improve the cosmetic aspects and corrosion protection of the plated metal, though this practice is not widespread because the requirements for coating processes are quite different.
Q: What are the advantages of barrel zinc plating?
A: Barrel zinc plating is an inexpensive process appropriate for small components. The components are contained in a barrel and tumbled during the plating process to provide uniform distribution of the zinc coating and efficient coverage.
Q: What are the characteristics of acid zinc plating that make it different from other methods of zinc plating?
A: Acid zinc plating employs an acid bath to galvanize the metal surface which results in a shiny finish, improved plating speeds and efficiency than its alkaline counterpart although its efficacy toward corrosion resistance may not be favorable.
Q: In the event of zinc coatings, what is the possibility of hydrogen embrittlement?
A: It is well-established that hydrogen embrittlement is a potential issue with zinc plating processes, especially when using electroplating methods in which hydrogen gas can become absorbed within the metal and lead to weaknesses and failure. To mitigate this potential, it is advised to heat the metal after plating to diffuse any trapped hydrogen gas.
Q: What elements influence the zinc coating thickness on the plated metal item?
A: The availability of the zinc coating thickness may depend on parameters like the composition of the plating solution, electroplating time, and the variety of plating techniques employed, such as rack-and-barrel zinc plating.