Modern manufacturing is revolutionized by laser cutting machines as they enable accuracy and efficiency across diverse industries. This writing discusses the basic concepts, the science behind cutting using a laser beam, and the application of this technology, thus, giving the audience a complete perspective on its importance. This guide seeks to simplify the complex details of machinery and their industrial use while emphasizing the importance of these machines in improving production execution. This covers everything from the basic processes of material and laser creation interaction, to more sophisticated processes and its application in the industry. Whether you are a query-driven layman or a professional working in the field, this piece is a significant report on how laser cutting machines are destined to change the world of manufacturing.
What is a laser cutting machine and how does it work?
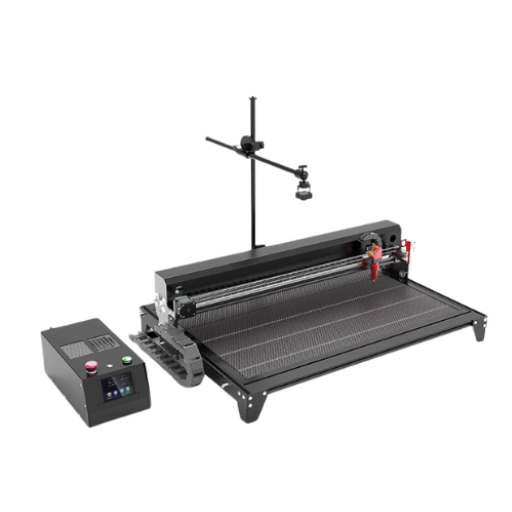
A laser cutter is a machine that cuts, engraves, and shapes materials using a high-power laser. The material is either melted, burned, or vaporized along a specific path. The procedure starts with a focused beam that is amplified and directed through mirrors or fiber optics to the material’s surface. Then CNC systems control the laser movement with great care, allowing cutting complicated shapes and fine details. Nd:YAG, CO2 or fiber laser may be used depending on the material and its application for maximum industrial efficiency.
Understanding the basics of laser technology
Laser technology is based on the principle of stimulated emission of radiation. The process begins in the resonator, where light oscillates between mirrors, and the medium is excited so it can emit photons. These photons get converted into a beam of coherent light and are later amplified into a concentrated beam. The laser then gets prepared for release. Here are some important details that stipulate laser efficiency:
- Wavelength: Determines the type of materials the laser can process. For example, CO2 lasers typically operate at 10.6 µm, making them ideal for cutting non-metallic materials like wood and acrylic, while fiber lasers function at 1.064 µm, better suited for metals.
- Power Output: It is directly proportional to operating speed and the depth of the cut. High-power lamps enable faster processing of thick materials, while low-power lamps are used for refined engraving. It is measured in watts.
- Beam Quality (M²): The focusability of the laster beam indicates spot size, which in turn determines the energy density and the level of cutting precision. A value close to 1 indicates the best spot performance, resulting in more detailed cuts.
- Spot Size: The size of a laser beam with the laser focused on the best focus position. A2 spot sizes result in a more intricate beam that can provide more precise cuts.
- Cutting Speed: Varying materials, laser power, and thickness impact the cutting speed. Cutting speed that prevents thermal degradation optimally tends to lower to make efficient cuts.
- Assist Gases: Oxygen and nitrogen, to name a few, are gasses that can be used for cutting, which is material-dependent, adjusting the process with oxidation control, enhancing cutting efficiency, or cooling down the material.
Parts of a laser cutting machine
- Laser Resonator: It is the central section of the machine emitting the laser beam. Alongside CO2, fiber, and crystal technology, the appropriate type is used to cut particular materials and application ranges. The shape of the resonator determines how stable and qualified the beam will be.
- Beam Delivery System: The laser beam is delivered from the laser cutting head to the workpiece. The cutting head utilizes mirrors, lenses, and fiber optics to preserve the proper cutting alignment and focus of the beam.
- Cutting Head: Erects the laser beam on the material via the focusing lens and has a shaft adjusting mechanism for different material thicknesses.
- Workpiece Table: This is where the materials meant for cutting are placed. It has either a stationary or moving design and often has clamps or a vacuum system to hold the material in place during work.
- CNC Controller: This is the main unit for controlling the machine. It coordinates the laser cutting process by electric means and controls the cutting process automatically. It decodes the design files and moves the machines to the necessary positions for cutting.
- Cooling Systems: They restrain the overheating of the optical components and laser source. Efficient cooling systems are critical to preserving the machine’s overall performance and increasing its lifetime.
- Exhaust Systems: They remove smoke, vapors, and particles produced while cutting. A well-designed exhaust system controlled during cutting ensures a clean environment for work, helps protect optical parts, and conforms to health regulations.
- Assist Gas System: It provides oxygen, nitrogen, or air to facilitate cutting. Each gas has its own functionality, such as improving the cut prior to oxidation or pushing molten material.
- Power Supply: This supplies the energy source for the laser and all additional systems. The right voltage gives stable cutting results.
- Software Interface: A user interface is the front for programming and operating the machine. More advanced software options offer capabilities for designing and optimizing the cutting paths and monitoring actions during the process in real time.
A Brief Outline on the Laser Cutting Procedure
The laser cutting procedure combines various activities working together to achieve effectiveness. Some of the most important ones include:
- Laser Power: The laser’s power level, in watts (W), greatly affects the depth and speed of cuts. Typical industrial laser cutters use a range from 500W to 4000W, with higher number settings ideal for cutting through thicker materials.
- Cutting Speed: This setting, whose units are inches per minute (IPM) or millimeters per second (mm/s), may affect cut quality. Faster speeds suit thin materials, while slower speeds are beneficial for fabricating thicker sheets as they promote reduced edge roughness.
- Focus Position: Assistance systems determine the distance between a material’s surface to the laser beam’s focal point. An ideal focus allows for minimum kerf width and enhanced edge quality.
- Assist Gas Pressure: For certain materials and thicknesses, gas pressures with nitrogen or oxygen are typically between 10 psi and 300 psi. For metals, smoother cuts are created as higher pressures amplify the throwing out of the molten material.
- Material Thickness: It depends on the material used and the power of the laser. For example, a 2000W laser can cut through mild steel up to 12mm thick, but a 4000W laser can cut through steel 20mm thick or more.
- Beam Spot Size: A smaller beam diameter increases the cutting resolution, and decreases heat-affected zones (HAZ).
To ensure that the parameters set are accurate for each material and cutting application, these must be set to achieve maximum performance, efficiency, and material integrity.
What are the different types of laser cutting machines?

Based on their kind of laser source, laser cutting machines are usually classified into three categories. The most common categories are CO2 lasers, fiber lasers, and crystal (YAG/YVO4) lasers. CO2 lasers, which are gas mixture operated lasers, are quite efficient in cutting wood, plastics, fabrics, and even some thinner metals. Fiber lasers dominate the market because of their efficiency and precision in cutting stainless steel, aluminum, and other metal forms, in addition to being less maintenance-intensive. Crystal lasers are the most versatile as they can cut metals and non-metals; however, YAG or YVO4 solid state mediums drive the cost up due to the shorter component lifetimes. Depending on material types and cutting needs, it’s no contest that each type is the best for certain industrial uses.
CO2 laser cutters: Application and Benefits
Due to their versatility and precision, CO2 laser cutters are widely used in industries that deal with non-metals and thin metals. They are perfect for engraving and marking materials like wood, plastic, glass, leather, paper, acrylic, and textiles, making them invaluable in manufacturing, design, and architecture. The power outputs of CO2 lasers range anywhere from 20W to over 150W. These lasers can achieve cutting speed of several meters per second while retaining optimal results on materials under 10mm thick.
While CO2 laser cutters do not differ much from other laser cutters, they provide the best quality edge finishes and intricate designs without any distortion in the material. In addition to that, the cutting wavelengths around 10.6 micrometers are very effective for non-metallic materials. CO2 lasers may be lower in efficiency than fiber lasers, but CO2 lasers are more cost-effective than fiber lasers since their capital cost is lower. The long operational history of CO2 makes them reliable. Moreover, taking proper care of the optical components improves the performance and the longevity of the equipment.
Fiber Laser Cutter: Easily Powerful Yet Powerful
Fiber lasers cut with a concentrated beam of light from an optical fiber, giving them precision and cutting power. Fiber systems have shorter wavelengths, which allows them to interact highly with metals like steel, aluminum, and even copper. The ability to focus energy into a small area means these lasers can cut materials thin and intricate with great detail without breaking or damaging the piece.
Fiber laser cutters are well known for their energy efficiency, frequently converting more than thirty percent of their energy into laser output. Running speeds can accomplish over forty meters per minute, depending on the material and its thickness. this makes cutting ideal for industrial operations that require as much productivity as possible. In addition, since lasers do not have moving parts like mirrors or resonators, they are more stable and robust than CO2 lasers. Because of this, the need for maintenance is reduced.
Advanced fiber laser cutters enable complete and meticulous cuts on materials that are as thick as 20mm, primarily on metal working or engraving processes. Special considerations include laser power, typically set between 500W and 12kW, and focus diameter since it determines cutting quality. Their compact design and extended operational lifespan underline their status as a superior choice for solid and reflective material cutting in tough working conditions.
Cutting with Solid-state Laser Carving Machines: All-in-one Functions
Solid-state laser cutters pose an impressive multidimensional skill set when dealing with various materials such as metals, ceramics, and even composites. Whether neodymium-doped or ytterbium-doped crystals are utilized, both are remarkable for possessing extremely high peak power with short burst and pulse duration. Because of this, these broad range solid-state lasers are more effective in precision cutting tasks. These systems can operate with high energy efficiency for industrial and laboratory applications. Moreover, they can focus on varying lenses at different wavelengths while still providing perfect targeting when working with delicate or difficult materials.
What materials can be cut with a laser cutting machine?
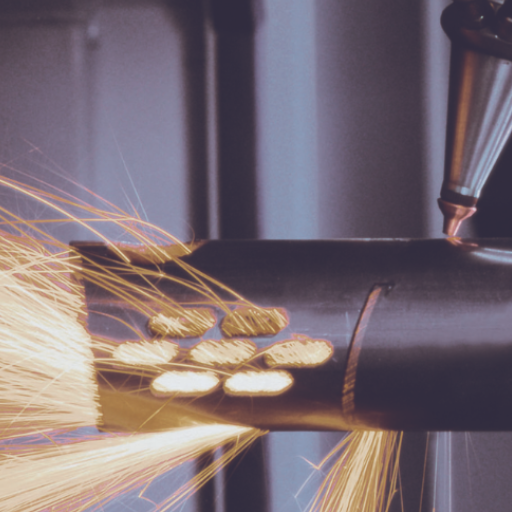
Because of their accuracy and versatility, laser cutting machines can manage various materials. Steels, aluminum, stainless steel, and brass can be cut with remarkable precision and are extensively used in industrial applications. Laser cutting is also used on non-metal materials like wood, plastics, glass, and ceramics, proving the technology’s feasibility in other fields as well. In addition, composite materials and fabrics may also be cut with a laser beam, and key structural elements will remain intact. The compatibility of a material to a laser cutter depends on the laser type used. These types of laser cutters are best for non metals: CO2 laser cutters. Fiber and laser cutters, in contrast, are preferred for metals and high precision jobs.
Capabilities in metal cutting: From alloys to sheet metal
With a modern laser cutter, businesses can rest assured that both the thickness and type of metal can be laser cut with incredible precision and accuracy. Cut edges of standard sheet metals like carbon steel, stainless steel, and aluminum always have great edge quality. Advanced grade lasers can cut specialized alloys like titanium and other nickel-based materials often used in aerospace and medical industries. Due to the flexibility in laser cutting parameters, it is also possible to cut thin foils and thicker plates accurately with reduced material wastage.
Materials other than metal: Wood, or even plastic
A CO2 grade laser cutter can effortlessly cut wood, plastic, paper, and textiles with enhanced precision grades. Wood, acrylic, and sheet plastics are often cut using modern laser systems and CO2 laser cutters because cuts do not over burn or melt. This would include laser cutting elaborate designs on wooden pieces or accurately molded plastic parts for industrial purposes. By optimizing settings like power and speed, the quality of the cut is enhanced along with the minimalistic approach to thermal damage.
Limitations and Considerations for Different Materials
When determining the considerations and limits for laser cutting of various materials, one must first evaluate thermal characteristics, materials composition, and laser compatibility. For metals such as aluminum, cut efficiency is dramatically lowered by high reflectivity, requiring specialized fiber laser units with anti-reflective aids to work. Stainless steel that is thicker than 10mm goes through the same process as other metals and require much higher amounts of power, thicker metals, around 2000 to 4000 watts, and slower cut speed to increase accuracy as well as edge quality.
For non-metals, one of the major factors is deformation. Acrylic and plastics tend to compete easily and can deform shape and change color if improper settings are used. Power settings anywhere from 50 to 150 watts coupled with moderate speeds seem to work best to avoid melting or burning. On the other hand, denser woods may need more precise power settings with an adjustable focus to guarantee clean cuts and limited charring. Lower power settings combined with high speeds are advised for textiles as they are very combustible and can set fire easily.
Comprehending exhaust and ventilation systems together is critical, especially when laser cutting plastic because it can release toxic gas-filled substances. This narrative shows how material compatibility and operational safety issues can be achieved.
How does laser cutting compare to other cutting processes?
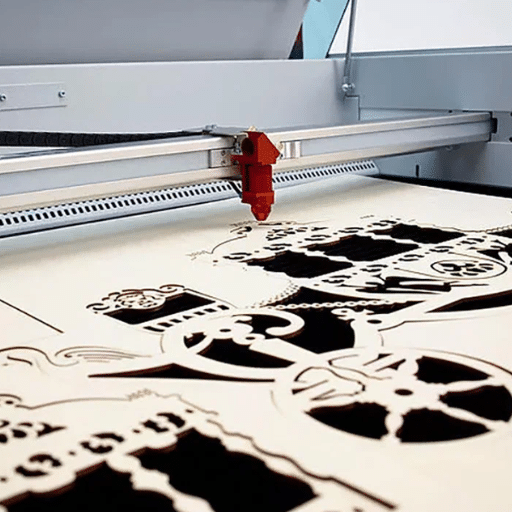
Laser cutting is faster and more precise than all other cutting processes. It is also extremely versatile. Unlike mechanical processes such as sawing or milling, cutting with lasers involves no physical contact. This contactless method eliminates the chances of material defect or tool wear. As a result, it also makes it possible to design extremely complex structures with very low error margins. Alongside these benefits, laser cutting has lower heat-affected zones than plasma or oxy-fuel cutting. Therefore, laser cutting reduces edges that need to be cleaned up post-processing. While plasma cutting may excel in thicker and conductive materials, laser cutting offers unmatched detail and quality for thinner metals and non-metals. Caution must be taken regarding the power required for industrial purposes as it increases the cost of higher-powered laser systems. Careful consideration must be made depending on project specifications and materials used.
Laser cutting vs plasma Cutting, Pros and Cons
Laser cutting should be preferred over plasma cutting when the required cut should be precise and accurate,especially for thinner materials. Laser cutting equipment uses energy, which adds to the total cost. The added expenses come from the higher initial costs and regular maintenance, along with operational taxes. The good side is that the heat-affected zone that is developed is smaller, meaning it causes less warping to the material.
Plasma cutting, as a case in point, works best with thicker materials, particularly conductive metals like steel and aluminum. These applications are typically faster, and plasma cutting is much more economical in heavy-duty projects. On the other hand, plasma cutting is not as accurate as laser cutting and results in a wider heat-affected zone which may necessitate additional edge finishing. The selection between these technologies is influenced by material type and thickness, accuracy needed, and available budget.
Benefits of laser cutting compared to classical techniques
Laser cutting done to a higher standard has clear benefits compared to classical approaches including productivity gains from improved efficiency and accuracy. Unlike mechanical cutting, laser cutting achieves accuracy up to ±0.1 mm. This enables it to work with intricate structures and complicated geometries without added tolling. This heightened accuracy translates into minimal material wastage and increased productivity. Besides, laser cutting can process more steel, aluminum, plastic, and even composites without sacrificing quality.
Since there is no contact with the cutting tool, laser cutting technology does not exert any mechanical stress on the cut material, which greatly reduces the chances of deformation. Moreover, the lesser heat-affected zone (HAZ) makes the chances of warping or burning the material far less likely, which is often the case in conventional processes. Also, the laser systems are highly automated and can be linked with CAD/CAM systems for complete production workflows. This reduces the chances of human errors and setup time. The setup precision and accuracy in laser systems are unparalleled. While the initial investment might seem overwhelming, the long-term savings in the material make these tools indispensable in these accuracy-demanding industries.
When to Choose Laser Cutting for your Project
You should use laser cutting whenever detail and precision are at the forefront of your project’s success. It is also suitable for applications that directly need high speed production or ultra fine features because of the minimum material wastage. The technology is excellent for projects encompassing a wide range of materials because it maintains exceptional edge quality without any additional finishing processes. Furthermore, as laser cutting can create very complex geometries directly from CAD files, it allows for fast prototyping and custom fabrication. Industries such as aerospace, automotive, medical devices, and any other sector that prioritize accuracy and high standards of repeatability greatly benefit from the high quality that these tools has to offer.
What are the industrial applications of laser cutting machines?

With their exceptional effectiveness, adaptability, and precision, laser cutting machines can benefit any industry. These machines effectively produce automotive parts, employing them for complex cutting, fabricating intricate components, and crafting custom prototypes. Within the aerospace industry, laser cutting is usually performed with lightweight materials with complex shapes due to the lower wastage of raw materials. Moreover, lasers assist in implant creation, surgical instruments, and precise equipment parts manufacturing in the medical field. Other uses are found in electronics, where lasers can cut circuit boards and micro components, and also in the textile industry, where laser cutting can be used for high-speed design modification and fabric cutting.
Automotive and aerospace industries: Precision parts manufacturing
Laser cutting machines provide great advantages regarding precision parts manufacturing in the automotive and aerospace industries by having exceptional precision and low material distortion. These machines aid in fabricating structural elements and engine part components, guaranteeing a high strength-to-weight ratio for advanced parts. Modern laser cutting serves the industry with high-quality and reliable parts without non-contact defective pieces. Furthermore, the non-contact nature of laser cutting helps it provide industry grade parts. In addition, these machines help improve design and reliability of the complete product because of the technology’s rapid prototyping abilities. The entire process greatly satisfies the performance and safety concern in both of the sectors.
Electronics and Consumer Goods: Unique Designs and Details
The role of laser cutting in the electronics and consumer goods market is centered on creating precise designs and engravings on metals, plastics, and composites. This technology enables accuracy on circuit boards, electronic enclosures, and consumer product decorations. Moreover, it allows for customizing engraving and marking, improving branding and product tracking. Laser cutting delivers accuracy with minimal exposure to heat which preserves the integrity and durability of sensitivity electronic components. The overall speed and efficiency of the process meet the requirements of large-scale production while sustaining the need for intricate customization.
Medical and Scientific Fields: Highly Specialized Cutting Needs
In medicine and science laser cutting is crucial because of the laser’s highly specialized requirements. It is popular in producing intricate surgical instruments, implantable devices, and even storable laboratory equipment. The technology ensures clean cuts and edges, which are critical for maintaining sterility of any medical apparatus. In addition, peripheral microfabrication is also performed utilizing laser cutting for stents and endoscopic devices. It does not deform materials because of its non-contact technique, allowing laser cutting to maintain the strength of delicate materials in these industries. Such adaptability means laser cutting is crucial for medical and scientific progress.
How to use a laser cutter safely and effectively?
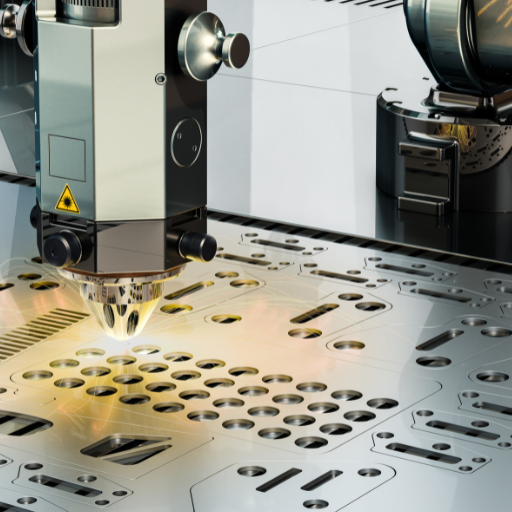
It’s crucial to prioritize safety and proper procedures when working with a laser cutter. So first things first, put on the right PPE, like goggles specifically made for lasers, to shield your eyes from damage. Always ensure the workspace is properly ventilated to reduce the amount of exposure to fumes produced when cutting. Always check that the material being cut is suitable, along with listed restrictions that are known to release harmful gases or damage the cutter. Set the laser’s power and speed according to the material specifications to obtain cuts without overheating or starting a fire. Always have a fire extinguisher near the working area, and do not leave the machine unattended. After cutting, ensure that the parts are cleaned, all debris is removed, and the lenses and nozzles work optimally. Regularly checking these components will guarantee better performance. Striking the balance between performance and safety can very well enhance your working environment.
Essential Precautions and Protective Measures
I always ensure that appropriate eye protective equipment is worn during use during laser cutter operations. The laser goggles used in my case are specifically designed for my specific wavelength. My workspace is kept at a comfortable temperature and is free of any pollutants and I confirm that the materials I intend to cut are not toxic and will not emit any harmful gases. I set the power and speed for the machine according to the particular material I am working with and never leave the device unattended while it is running. Finally, I maintain a portable fire extinguisher close and regularly take apart and clean as well as examine the tools to ensure that they remain in good(safe) condition.
Best practices for operating a cutting laser machine
My technique for the optimal experience of operating a cutting laser machine includes precise calibration of the make on every use to ensure that the focus is right for the material thickness. I also try to position and lock materials, which eliminates movement during the cutting phase, which may compromise precision. Moreover, I use tested and recommended settings for laser power and speed for the specific material type to improve efficiency and minimize damage or waste. Cleanings mirrors, lenses, and exhaust vents regularly is important in avoiding failure during operation and maintaining peak performance.
Tips for Maintenance and Troubleshooting
The golden rule is always to perform regular maintenance checks to maximize the performance and lifetime of any equipment or a system. To begin with, I examine every component for wear and tear while also ensuring that the parts are clean and free from debris that may obstruct performance. Moving parts should be lubricated where necessary to minimize friction-related damage. Regularly inspect connections and seals for indications of deterioration or leaks and resolve any issues immediately to prevent further problems.
To solve problems, look for the exact indicators of the problem at hand; a systematic analysis approach can assist in identifying the root cause. Check the power sources and connections to eliminate any simple mistakes and oversights. Built-in system components, such as diagnostic instruments, are used to determine possible issues and focus on error codes or abnormal performance signs. If the issue remains unresolved, contact the manufacturer’s technical support or consult the manual for advanced diagnostics and useful suggestions.
Reference sources
Frequently Asked Questions (FAQs)
Q: How does laser cutting work?
A: Laser cutting works by using a high-powered laser beam to cut material with precision. The laser machine focuses the laser beam onto the material, causing it to melt, burn, or vaporize. The laser head moves along a programmed path, cutting the desired shape. This process can be used to cut a variety of materials, including metal, wood, plastic, and fabric.
Q: What are the main types of lasers used in laser cutting?
A: The main types of lasers used in laser cutting include CO2 lasers, fiber lasers, and Nd:YAG lasers. CO2 lasers are versatile and commonly used for cutting non-metals. Fiber lasers are efficient for cutting metals and are often used in industrial cutting applications. Nd:YAG lasers are suitable for both cutting and laser marking on various materials.
Q: What materials can be cut using a laser cutting machine?
A: Laser cutting machines can cut a variety of materials, including metals like steel, aluminum, and titanium; non-metals such as wood, acrylic, and paper; and even some fabrics. The specific material you are cutting will determine the type of laser and cutting parameters used.
Q: How does a laser cutting machine work?
A: A laser cutting machine works by generating a high-powered laser beam using a laser generator. The beam is then focused through a series of mirrors and lenses onto the material. The intense heat of the focused laser beam melts, burns, or vaporizes the material along a predetermined path, creating precise cuts. The machine’s computer-controlled system guides the laser head to produce the desired shape or pattern.
Q: What are the different cutting methods used in laser cutting?
A: The main cutting methods used in laser cutting include fusion cutting, flame cutting, and vaporization cutting. Fusion cutting melts the material and blows it away with gas. Flame cutting uses oxygen to create an exothermic reaction. Vaporization cutting is used for non-melting materials, where the laser vaporizes the material directly. The method used depends on the material and desired outcome.
Q: What are the dangers of laser cutting?
A: The dangers of laser cutting include exposure to high-power laser beams, which can cause severe eye and skin damage. Other risks include the generation of toxic fumes from cut materials, fire hazards, and electrical risks. Proper safety measures, such as using protective eyewear, adequate ventilation, and following safety protocols, are essential when operating laser cutting equipment.
Q: How are laser cut parts produced?
A: Laser cut parts are produced by first creating a digital design using CAD software. This design is then transferred to the laser cutting machine. The machine uses the design to guide the laser beam, cutting the material according to the specified pattern. The laser intensity and cutting speed are adjusted based on the material and desired outcome. After cutting, the parts may require additional finishing processes.
Q: What are the advantages of laser cutting over other cutting methods?
A: Laser cutting offers several advantages, including high precision, the ability to cut complex shapes, minimal material waste, and a clean cutting edge. It also allows for non-contact cutting, reducing wear on tools. Laser cutting is versatile, capable of cutting, marking, and engraving a wide range of materials. Additionally, it’s often faster and more cost-effective for many applications compared to traditional cutting methods.