The global market acknowledges the superiority, flexibility, and adaptability of high-density polyethylene (HDPE) plastic pipes, which makes them crucial to numerous industries. This article discusses in detail the HDPE Pipes, their applications, their benefits, and the range of sizes offered. Remembering these details will help professionals and policymakers consider the use of HDPE pipes as an optimum solution to their project needs in water supply systems, gas distribution, industrial processes, and environmental engineering. This overview brings clarity about the reasons why the use of HDPE pipes has increased in modern construction and engineering projects.
What are HDPE pipes?
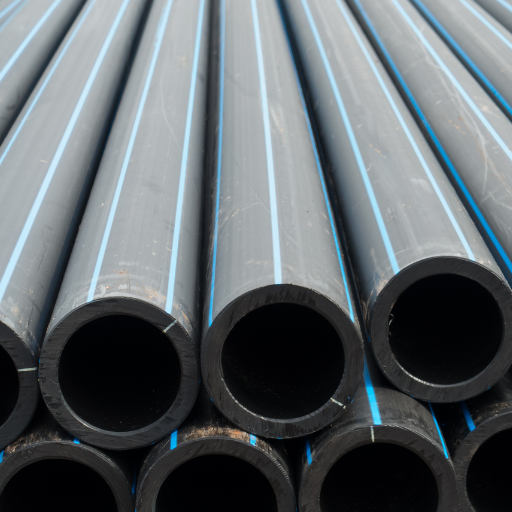
High-Density Polyethylene pipes (HDPE) are a type of thermoplastic pipe that is easily formed and long-lasting, featuring a high-weight bearing polyethylene manufactured from a versatile composite material. These items,just like every other plastic around, have specific applications that they are suited for due to exceptional chemical resistance, flexibility, and strength to density ratio. These pipes can be found in water supply systems, gas distribution networks, sewer systems, and in several industrial processes. As compared to other materials, these pipes are offers incredible value considering their corrosion resistance, as well as the ability to withstand high pressure. These characteristics and optimal environmental stress resistance put them far above their competitors in terms of value for long-term, cost-effective infrastructure projects.
What Makes HDPE Pipes Distinct From Other Plastics?
HDPE pipes stand out from other plastic products, including enhanced chemical resistance, strength to density, flexibility, and other engineered conditions. HDPE pipes have extreme bending, pressure, and temperature endurance and appear slightly sturdier when set against PVC or ultrathermoplastic materials. Furthermore, their gas and liquid permeability is remarkably low. Coupled with their ultra sound welding, they can be set in place without the worry of leakage, setting them apart from other supples. Combining these properties makes them a widely acceptable choice for industrial and infrastructural projects.
HDPE vs PVC: Which pipe material is better for your project?
Choosing between HDPE and PVC pipes is a matter of selecting the best materials to serve the specific purpose of a project. Projects that need significant flexibility, resistance to extreme environmental factors, and leak-free joints created through fusion welding, are best suited for HDPE pipes. These pipes adapt well to ground movement and will outperform other materials for pressure, chemical exposure, and long-term durability. In contrast, PVC pipes are efficient to use in more forgiving environments. Their rigid support also makes them appropriate for above ground projects. Analyzing other aspects of your project, like the level of pressure and temperature and the installation method, will give good insights into the most appropriate material to use.
What are the key properties of HDPE pipes?
The most outstanding trait of High-Density Polyethylene or HDPE pipes is the strength-to-weight ratio, allowing them to be light and strong. In addition, these pipes are highly resistant to corrosion, abrasion, and chemicals, increasing their lifespan in tough conditions. These pipes are also flexible, which eases their handling and installation even in difficult places. Also, HDPE pipes have a very low friction coefficient which makes them ideal for efficient fluid flow. Their ability to withstand long-term high pressures makes them applicable in various industrial and infrastructural needs. Most importantly, these pipes are resistant to UV radiation and microbial growth, thus enhancing their durability and performance in outdoor and buried installations.
What are the main applications of HDPE pipes?

Multiple sectors widely use HDPE pipes owing to its versatility and durability. They are used in water supply systems, like potable water and irrigation, due to their resistance to corrosion and leaching of chemicals. Additionally, they are extensively applied to sewage and drainage systems for pressurized and non-pressurized fluid transport. There are also significant applications of HDPE pipes in the industry, such as transportation of chemicals, mining slurry, and gas distribution, because of the materials’ chemical resistance and mechanical strength. Their flexibility allows them to be installed using trenchless methods like horizontal directional drilling and slip-lining.
How are HDPE pipes used in water and wastewater systems
Water processing departments rely on HDPE pipes for their exceptional durability, leak-proofing properties, and flexibility. They may be used in potable distribution systems, where HDPE pipes are used to distribute its drinking water because the pipes do not corrode and undergo any chemical reactions. HDPE pipes are reliable for electrolytic dissociation for sewage and stormwater systems due to the excessive rotary and bounding particulate solid pressure abradement. They are constructed as lightweight non-complex structural elements, allowing them to be used in projects that do not require routine maintenance and offer long-term reliability. Also, their ability to be installed without the need of excavation lowers the environmental impact and expenses of the entire project.
What role do HDPE pipes play in the oil and gas industry?
The oil and gas sector relies heavily on HDPE pipes for their durability and capacity to resist heat and corrosive environments. Their use inthe construction of onshore and offshore facilities in transporting crude oil, natural gas, and other petroleum products is commonplace. Offshore and onshore refrigerate operational temperatures are tolerable within the range of -40°F to 140°F (-40°C to 60°C). These pipes are also highly flexible and can be welded together using fusion welding techniques. These characteristics not only make these pipes easy to install in remote locations, but also help seal off any potential leaks that may pose an environmental risk. The rest of the pipe material is also lightweight, making it easier to transport and increasing its utility. Overall, less maintenance is required in addition to the pipes’ long operational life, proving cost effective for the industry.
What role do HDPE pipes play in irrigation and drainage systems?
HDPE pipes are popular in agriculture for irrigation systems because of their flexibility, light weight, and environmental endurance. These pipes ensure effective water delivery through precise distribution with a low chance of contamination. The pipes also help facilitate the operations of a drainage system because they are durable and resistant to corrosion, which helps in handling waste and stormwater effectively. Their resistance to pressure fluctuations and UV degradation makes these pipes ideal for outdoor use, aiding the long-term efficiency and reliability of the water management system.
What sizes and fittings are available for HDPE pipes?
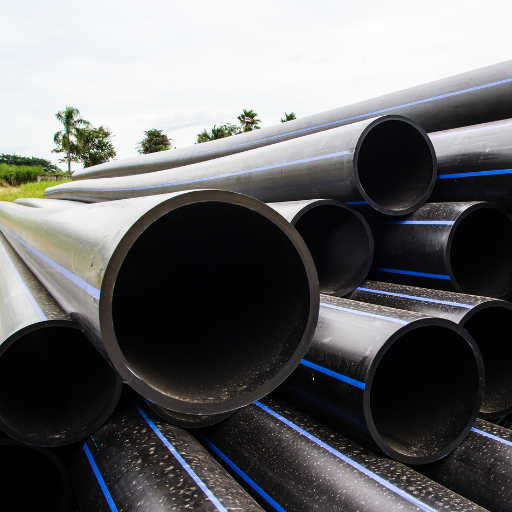
HDPE pipes are available in various sizes, typically ranging from small diameters such as 20mm (0.75 inches) for residential use to large diameters exceeding 2000mm (78 inches) for industrial and municipal applications. They come in varying pressure ratings designed to accommodate different operational requirements. Fittings for HDPE pipes include couplers, tees, elbows, reducers, and flanges, allowing for versatile configurations in piping systems. These fittings are often joined using methods like heat fusion or mechanical connections to ensure leak-free assemblies suitable for a variety of applications.
What are the usual dimensions of HDPE Pipes?
Different applications require high-density polyethylene pipes of various sizes. A standard measurement for residential and irrigation use diameter is 20mm (0.75 inches), 25mm (1 inch), 32mm (1.25 inches), 50mm (2 inches), and respectively. These pipes can have diameters from 160mm (6 inches) to over 2000mm (78 inches) for larger, industrial, or infrastructural applications. The Standard Dimension Ratio (SDR), also called the pressure rating, is one of the significant aspects of these pipes. It is the indicator of how much pressure the pipe can withstand internally. Different SDR classifications have different ratings aligned with system requirements like SDR 11 (16 bar or 230 psi) and SDR 17 (10 bar or 145 psi). Advanced agricultural practices and irrigation alongside industrial use these technical specifications for the efficient operational and structural requirements of high-density polyethylene pipes.
What fittings are compatible with HDPE pipes?
- Electrofusion Fittings
These fittings create a robust, leak-proof connection through electrofusion, where an embedded metallic coil is heated to melt the contact surfaces. Common types include couplers, elbows, tees, and end caps, which are widely used in applications requiring secure and durable joints.
- Butt Fusion Fittings
Butt fusion fittings involve heating two pipe ends or fittings until their material softens, then pressing them together to form a seamless, consistent joint. They suit long-term projects and include reducers, elbows, and flanges.
- Compression Fittings
Designed for quick and easy installation, compression fittings are ideal for low-pressure systems. They consist of nuts, rings, and sleeves that tighten around the pipe, ensuring a reliable seal. Typical applications include irrigation and potable water systems.
- Stub Ends and Flanges
Stub ends paired with backing rings or flanges enable easy assembly and disassembly of HDPE piping systems. Often employed in high-pressure systems or where regular maintenance is required, these fittings ensure reliable mechanical joint connections.
- Transition Fittings
Transition fittings facilitate the connection between HDPE pipes and pipes made of other materials, such as PVC or steel. They are equipped with one end made of HDPE material and the other with a material suited to the connecting pipe, ensuring seamless integration.
- Saddle Fittings
Saddle fittings are used to create branch connections in HDPE pipelines. They clamp onto the main pipe and are available in options like electrofusion saddles for high-pressure systems or mechanical saddles for more straightforward setups.
- Reducers
Reducers connect pipes of different diameters and are highly useful in managing transitions in flow capacity. Depending on alignment requirements within the pipeline, they are available in concentric or eccentric designs.
How are HDPE pipes joined together?
Managers often wonder how everything is compacted in reliable methods, eliminating any chances of leakage. The most common method, butt fusion, involves heating the ends of two pipes and then pressing them together to form a joint. Electrofusion uses a specially designed fitting with an embedded resistive wire that fuses the HDPE. Electrofusion is the most common and considered the easiest. And nowadays, most people use mechanical joints, including several bolts and nuts along with the pipe within the flange, providing maximum sealing. Each method has its own benefits, and the choice depends on application, required pressure, and the setting of the environment.
What are the benefits of using HDPE pipes over traditional materials?
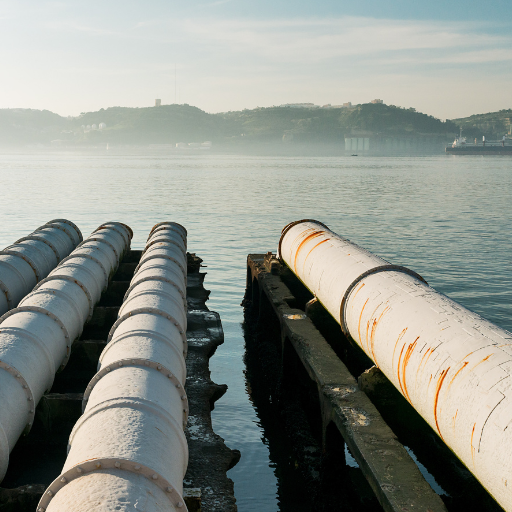
Compared with older materials, HDPE pipes have significant advantages that make them suitable for newer infrastructure projects. They are very durable and corrosion-resistant, increasing their lifespan even in extreme chemical or saline conditions. The lightweight nature of HDPE pipes lowers transportation and installation costs while making them easy to maneuver. Moreover, their flexibility makes it easier to go around obstacles while replacing fittings, which reduces the chance of leaks. Furthermore, impact resistance and tolerances of high-pressure makes HDPE pipes suitable for various applications such as potable water systems, gas distribution, and sewage systems.
In what ways are HDPE pipes capable of withstanding corrosion and environmental factors?
Pipes of high-density polyethylene (HDPE) can withstand corrosion and harsh environmental conditions due to the metallic structure of the polymer itself. The salts, chemicals, and acids used in relevant industries cannot cause any rust or destruction to the polymers. Specifically, pipes made from HDPE because having non-polar bonds means it does need to react to aggressive solvents such as the ones used to corrode metal pipes. Moreover, HDPE pipes can work under harsh environmental conditions because the material is able to endure ranges of -40°F to 140°F without any issues. When the material is carbon black stabilized or UV protected, its photodegradation, being exposed to the sun for long periods, is critically reduced, which enhances the polymers’ durability. All of these features makes HDPE pipes ideal for tough conditions with no extra maintenance needed.
What makes HDPE pipes more durable than concrete or steel pipes?
The strength of HDPE pipes when juxtaposed with concrete and steel pipes, comes from remarkable flexibility, resistance to corrosion, and lower external damage susceptibility. Steel pipes rust and then need protective coatings, concrete pipes crack from ground movement, while HDPE pipes remain structurally intact thanks to the material’s elasticity and toughness. These pipes withstand heavy dynamic and static loads without fracturing, making them ideal for seismic active areas or soil settlement.
They have high impact resistance and a tensile strength between 3,200 – 4,000 psi, which is more than enough for many strenuous tasks. Unlike steel, they are chemically inert and can withstand aggressive substances, including acids and bases, without degradation. Friction and abrasion ensure the smooth inner surface doesn’t incur as much wear and tear over time. Furthermore, HDPE pipes have a lifespan exceeding 50-100 years under proper conditions, outdoing steel or concrete options in terms of long-term performance. This combination of properties raises lower maintenance requirements and overall lifecycle costs, which presents HDPE pipes as a durable and cost-effective solution across various industries.
In what ways do HDPE pipes help prevent leaks in pipeline systems?
To begin with, the non-leakage feature of pipelines is aided by HDPE pipes because of the properties of the materials used in their joints. They are commonly connected through heat fusion, which makes joint types redundant, thus eliminating joint failures and leakages. The ductility and flexibility of the material HDPE enable it to easily undergo ground movement and withstand pressure changes without cracking. Furthermore, the pipes being non-corrosive means that there will be no structural damage with, them, HDPE pipes are an excellent environmentally friendly solution to infrastructure problems.
What environmental considerations are associated with HDPE pipes?

HDPE, or high-density polyethylene pipes, offer great benefits towards the environment due to their ability to be recycled, durability, and how energy-efficient they are during the time of production and use. Their long life reduces the need to constantly replace them, reducing the amount of precious resources used and waste generated. Since HDPE is a recyclable material, old pipes can be melted and remolded, preventing them from taking up space in a landfill. In addition to all that, their smooth interior surface lowers energy requirements in fluid transportation by helping reduce friction, which leads to HDPE pipes offering higher operational efficiency and consuming less energy. These combinations of properties makes HDPE pipes a favored choice in infrastructure projects concerned with sustainability.
Are HDPE pipes environmentally friendly?
Yes, HDPE pipes are environmentally friendly due to their lifecycle offering durability, efficiency, and high recycling rates. Unlike some traditional materials, HDPE pipe production line uses less energy, and their recycling at the end of their use period reduces waste in landfills. Moreover, not having to frequently replace them thanks to their corrosion resistance and long lifespan saves more resources and energy in the long run. Being able to perform during friction fluid transportation efficiently helps save energy and makes them a great pick for infrastructure projects.
Is it possible to recycle or reuse HDPE Pipes?
Of course, HDPE pipes can be reused and/or recycled, which makes them eco-friendly. These pipes can be turned into new products and still maintain a superior standard. Reusing HDPE pipes for suitable purposes further supports circular economy concepts as it conserves resources and minimizes waste.
What are the cost implications of choosing HDPE pipes for your project?

Several factors come into play when evaluating the economic impact of HDPE pipes, such as initial payments, installation, and operational savings. Although HDPE material may cost more initially than some traditional materials, its lightweight nature aids in cutting down transportation and installation costs. Moreover, the sturdiness and lack of required servicing during the lifecycle of HDPE pipes result in considerable savings. Their ability to withstand corrosion and chemical destruction also lowers the cost of repairs and replacements, making it a practical solution for various situations.
What’s the difference in initial investments made for HDPE and other available materials?
There is a price difference between HDPE pipes and traditional materials like PVC or concrete that often works in favor of the latter. Though this price difference is offset by the low weight of HDPE pipes, which cuts down on transportation and installation expenses, it needs to be noted that a project requiring great HDPE pipes may be more attractive from a service life, maintenance expense, and HDPE pipes in generally offer a cost-effective solution in the longer run.
What are the long term cost benefits of using HDPE pipes?
High-Density Polyethylene (HDPE) pipes have substantial long-term cost benefits because of their toughness, low maintenance costs, and corrosion resistance. Compared to most conventional materials, HDPE pipes incur minimal damage through leaks and structural failures. This reduces the need and cost to do repairs. Additionally, the lightweight nature of these pipes makes them easier to transport and lowers installation cost in turn. Moreover, these pipes can last for more than 50 years, dramatically minimizing the frequency of replacements and resulting in lower lifecycle costs.
Reference sources
Frequently Asked Questions (FAQs)
Q: What is HDPE pipe and how does it compare to PVC and PE pipes?
A: HDPE pipe is a type of polyethylene pipe made from high-density polyethylene. Compared to PVC pipe, HDPE is more flexible and has better resistance to environmental factors. PE pipes are similar to HDPE but have a lower density. HDPE is highly durable and often preferred for applications like water mains, gas mains, and drainage pipes.
Q: What are the main benefits of using HDPE pipes?
A: The benefits of HDPE pipes include excellent chemical resistance, flexibility, durability, and long service life. HDPE is resistant to many chemicals, corrosion, and abrasion. It’s also lightweight, making it easier to install than metal pipes. HDPE pipes are used in various applications, including water supply lines, sewer mains, and slurry transfer lines.
Q: How does the pipe size of HDPE compare to PVC and PE pipes?
A: HDPE pipes are available in a wide range of sizes, similar to PVC and PE pipes. However, HDPE pipes often have a thinner wall thickness for the same pressure rating, allowing for a larger internal diameter and increased flow capacity. This can be advantageous in applications where maximizing flow is important, such as in drainage pipes or rural irrigation systems.
Q: Are HDPE pipes suitable for underground installations?
A: Yes, HDPE pipes are excellent for underground installations. They are resistant to root intrusion, ground movement, and soil chemicals. HDPE’s flexibility allows it to withstand ground shifts without cracking or breaking. Additionally, black HDPE pipes are UV-resistant, making them suitable for both above-ground and underground use in various applications, including water mains and gas mains.
Q: How are HDPE pipes joined together?
A: HDPE pipes can be joined using several methods, including heat fusion techniques like butt fusion, electrofusion welding, and socket welding. These methods create a seamless, leak-proof joint that’s as strong as the pipe itself. For some applications, mechanical fittings or extrusion welding may also be used. Unlike PVC pipes, HDPE pipes typically don’t require additional seals or jointing compounds.
Q: Can HDPE pipes be used for transporting gases and chemicals?
A: Yes, HDPE pipes are widely used to transfer fluids and gases, including chemicals. HDPE is resistant to many chemicals and doesn’t corrode, making it suitable for various industrial applications. It’s commonly used in the plastics industry for chemical transport, as well as in gas mains for natural gas distribution. However, it’s important to verify the pipe’s compatibility with specific chemicals before use.
Q: How does the environmental impact of HDPE pipes compare to PVC pipes?
A: HDPE pipes generally have a lower environmental impact than PVC pipes. HDPE is made from ethylene, a byproduct of natural gas processing, and is 100% recyclable. It doesn’t contain chlorine or other harmful additives found in PVC. Additionally, the longer lifespan and lower maintenance needs of HDPE pipes contribute to their overall sustainability. However, both materials have their place in the piping industry, depending on the specific application and requirements.
Q: What are some unique applications of HDPE pipes?
A: HDPE pipes have numerous unique applications due to their versatility and durability. They are used in rural irrigation systems, mining operations for slurry transfer lines, and as communication conduits for fiber optic cables. HDPE pipes are also used in landfill applications for leachate collection and in marine environments for dredging operations. Their resistance to environmental factors makes them suitable for extreme conditions where other materials might fail.