Lasers have been cutting materials far before CNC technology was ever introduced. The power of laser technology, combined with the precision of CNC, allows for great detail when cutting. Moving lasers along designated paths enables machines to engrave with utmost precision. The manufacturing industry can now reap the benefits of using CNC laser cutting and its engaging reach within its field. This article focuses on the intricacies of how CNC laser cutting functions and the many ways it can benefit industries today, such as in terms of accuracy and lower expenses.
What is CNC laser cutting and how does it work?
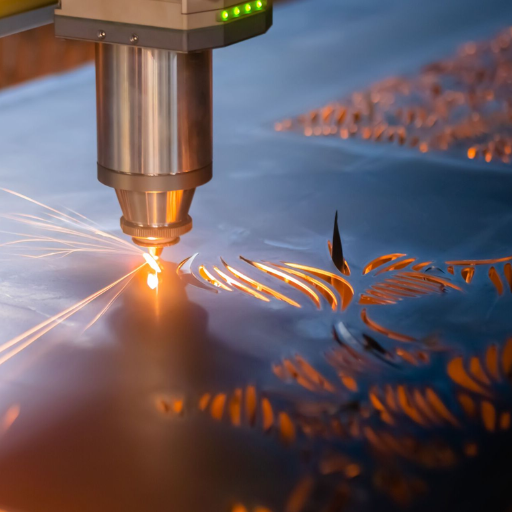
CNC laser cutting is a technology that uses a powerful laser beam to cut, shape, or engrave materials with precision. This process uses a Computer Numerical Control system (CNC) that directs a laser beam to the desired material. The process is accurate and repetitve. A laser closes in on a specific point, generating intense heat, while conveniently, gas removes the remains, which leave behind clean edges. For precise cuts, the system counteracts the behavior to define the shape of the design, allowing complex cuts to be made in metals, plastics, and wood. This method is efficient and adaptable to very tight spaces while having minimal material waste.
Understanding the basics of CNC technology
The CNC technology converts a digital design into automated motions of various machineries. The Computer Numerical Control system directs the tools or equipment, such as laser cutters, to work various paths. The process begins with a CAD software file, which is then translated into code for the equipment guidance. This effectively allows for precision, repeatability, and efficiency while setting complex designs with little to no human help.
Importance Of Lasers In The Cutting Process
Lasers are essential in cutting because of their accuracy, agility, and multi-material usability. For CO2 and fiber lasers, the absorption of different materials defines the effectiveness of the laser, which is determined by the wavelength, normally absent from the range of 10.6 µm to 1.06 µm. Power output, stated in watts (W), determines the depth and speed at which the laser cuts. Based on material thickness and intended use, industrial lasers function within 500 W and 10 kW. The M² factor measures beam quality, which ensures detailed cuts are made. Irrespective of being focused or effective, lower values can lose portion of efficiency. Minimum focusing optics and assist gas, such as oxygen or nitrogen, are also crucial in making precise cuts, as assist gas oxidizes or turns molten material into slag, so that gas does not evaporate during the cuts. With these elements combined, lasers can achieve high accuracy and have minimal thermal deformity, which makes them crucial in industrial manufacturing and construction.
The Integration of CNC and Laser Cutting for Accuracy
CNC and laser cutting systems work together for both system have benefits, joining the control CNC technology with the cutting speed lasers offer. CNC systems guarantee the exact movement and position of the cutting tool, which is essential for calibrating complex geometries and obtaining uniform quality. When comparing it with laser cutting, it works with given parameters which are set to enhance performance like:
- Wavelength: For CO2 lasers, it is usually 10.6 µm and for fiber lasers 1.06 µm; due to high energy absorption, all these wavelengths ensure compatibility with the material.
- Power Output: The output is usually between 500 W and 10 kW, which allows for adjustments based on the thickness of the material. The higher the power, the greater the depth of cutting and the faster the processing time.
- Beam Quality (M² Factor): Anything between 1.0 and 1.5 is considered low and guarantees beam focus, which is essential for clean and detailed cuts.
- Focal Length of Optics: The best focal lengths are optimized for the balance between power density and the size of the spot; shorter focal lengths work best with small details and thin materials.
- Assist Gas: Depending on the application, nitrogen and oxygen can be used. Oxygen is superior for thicker materials, increasing the speeds at which they can be cut, and nitrogen helps prevent oxidation, producing cleaner cuts.
What are the different types of CNC laser cutting machines?
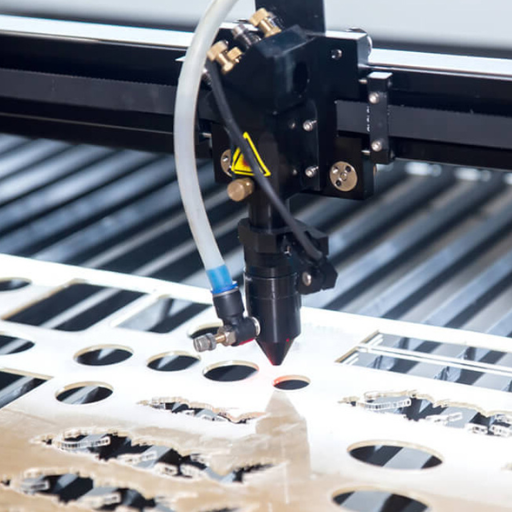
CNC laser cutting machines are categorized based on the type of laser source, the setup used, and processes of interest. The common types are cut-into-CO2 laser cutting machines, fiber laser cutting machines, and crystal(YAG/YVO4) laser cutting machines. Apart from the precision industrial cutting of metals like steel, fiber lasers are also efficient for plastic and brass, which are used for keepsakes. Crystal lasers are known to be expensive with high maintenance costs hence are not stet ratio common. Despite these challenges, they are highly effective for the most demanding jobs. Each type offers distinct advantages depending on the required precision, material compatibility, and operational needs.
CO2 laser cutters: Features and applications
Cutting CO2 laser cutters are known as universal cutters because they can engrave on and cut a wide range of materials. By using a gas mixture of carbon dioxide (the most abundant compound), nitrogen, and helium that is electrically stimulated, a highly concentrated laser beam is produced. These machines can engrave and cut nonmetal materials such as wood, plastic, fabrics, and leather. With some modification, they can also cut thin metal.
CO2 lasers operate at a wavelength of 10.6 microns, making them highly suitable for cutting organic materials with precision and without damage. Depending on the machine’s layout and purpose, the power output fluctuates between 25 and 400 watts. The lasers can be used for both nuanced engravings and powerful cuts. CO2 cutters also provide high position accuracy, around ±0.1 mm, which guarantees precision in complex designs.
They are used as aids for almost every industry which ranges from precision prototyping and signage creation to art. The machines are unique in their ability to execute intricate designs without losing the integrity of the material which is why they are mostly used in industries with great detail. Nonetheless, as much as CO2 lasers are useful in cutting non-metal materials, using them on metal sheets of larger thickness is an issue, unlike fiber lasers. For optimal long-term function effectiveness, maintenance, especially changing optical pieces such as the mirrors and lenses, is necessary.
Uses and Advantages of Fiber Laser Cutting Machines
Fiber laser machines have numerous advantages, making them ideal for different applications. One of the best features is laser energy is delivered directly through fiber optic cables, which ensures high energy efficiency. These machines perform above average when cutting reflective metals like carbon steel, stainless steel, aluminum, and brass because reflexive metals better absorb shorter laser wavelength of 1.06 microns.
When working with thin metals, these machines can cut significantly faster than CO2 laser systems and, depending on power levels, can achieve speeds exceeding 20 meters per minute for materials like 1 mm stainless steel. Common power ratings for industrial fiber lasers are over 500 watts and typically go over 12 kilowatts. A fiber laser with 6 kW power can cut high-precision carbon steel that is 25 mm thick.
Fiber lasers do not require as much maintenance as CO2 lasers since maintenance does not include mirrors, thus having a sturdy structure. Their design also guarantees constant beam quality, thus ensuring clean cuts on edges and in intricate designs. However, while laser processing metals is their strength, it is also their weakness when dealing with non-metals due to the efficiency drop in the laser wavelength.
When to Choose Crystal Laser Systems
Crystal Lasers Systems work best with ultra-high pulse laser beams, which are ideal for precision micromachining and intricate engravings. They excel in industries such as medical device manufacturing, where detail matters. These systems are also adaptive since they can cut off some non-metals which fiber lasers have issues with. Still, they require more maintenance because the expendable parts of their crystal rods need frequent replacement, giving them a lower life span. Because of this, they are best suited for specialized applications rather than mass production.
What materials can be cut using CNC laser cutting technology?
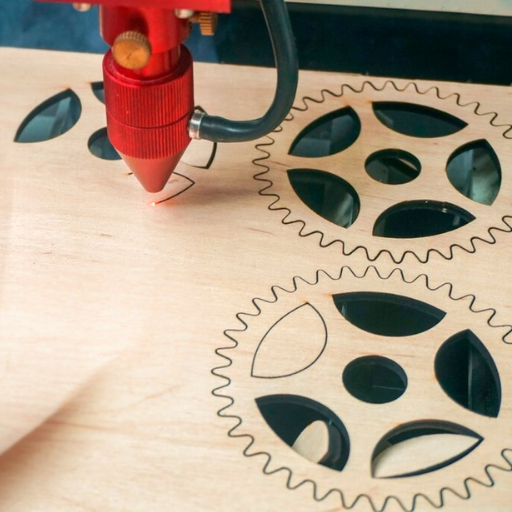
The CNC laser cutting method is known for its reliability and accuracy when processing a wide scope of materials. Metals such as steel, aluminum, brass, and titanium are some of the most common cut materials because laser technology provides high quality edges and very low details. Other materials like wood, acrylic, plastics, and even some composites can also be cut, although this varies according to the type of laser system in place. Furthermore, other complex materials like ceramics and textiles can be cut properly. The material thickness and reflective properties are crucial determinants of the laser’s efficiency and performance.
Cutting metal: Capabilities and limitations
When applied to metal processing, CNC laser cutting technology is comparatively easy and productive, mainly because of the intricate detailing and narrow tolerances. This process stands out with regards to precision when working with metals like mild steel, stainless steel, and aluminum where the cut accuracy is almost always satisfied which is typically within ±0.1 mm. It also allows for excellent productivity about greater speed and accuracy. An example of this would be the CO₂ laser, which reputedly tends to lose productivity when processing highly reflective materials such as copper and brass and only maintain it when cutting harsh metals like 25 mm mild steel. Unlike CO₂ lasers, Fiber lasers are more efficient when cutting reflective metals, as they can manipulate thinner sheets swiftly, because shorter wavelengths enhance strong absorption.
Limitations are based on the type of material, its thickness, and even its temperature conductivity. Thick metals over 25 mm might need slower cutting speeds and multiple passes which in turn reduces efficiency and increases risk for thermal distortion. Some reflective surfaces can pose a problem for some laser types because they tend to reflect a portion of the beam, which reduces energy absorption and cutting quality. Also, drastic shifts in material properties may need alterations in laser power, which usually ranges from 500 W to over 10 kW depending on the type of metal processed and its thickness. The equipment needs to be properly maintained and calibrated to achieve optimal performance with minimal operational limitations.
Laser cutting applications
- Acrylic: Acrylic is one of the most preferred non-metal materials for laser cutting because of its good edge clarity and smooth-to-the-touch, flame-polished cuts. It is widely used in signboards, decorations, and consumer product components.
- Wood: Different types of wood like plywood, reed, MDF, and even hardwood are great for laser cutting and engraving. The state of the art cutting precision even allows for more complex designs, perfect for architectural models, furniture, and art pieces.
- Paper and Cardboard: Paper and cardboard are thin and can be cut or scored by lasers. They can be used in packaging design, making custom invitations, or prototyping.
- Plastics: Thermoplastic materials such as polycarbonate, PETG, and polystyrene have good processing capabilities. However, certain restrictions apply to the types of plastics used. For instance, PVC is not laser-friendly, as it does not cut well and emits toxic fumes.
- Foam: Foam products such as polyethylene foams and EVA foams are easy and clean to cut. As a result, they can be used for packaging inserts, protective cases, and costume props from games, movies, and comics.
- Textiles and Leather: A laser can cut natural fabrics such as cotton, silk, and wool or synthetic fabrics like polyester into detailed shapes without lifting the edges. Leather is also extensively cut for clothing, accessories, and furniture.
- Rubber: Non-PVC special rubbers can be easily cut and engraved with lasers. They are widely used in making gaskets, rubber stamps, and industrial parts.
Picking the best laser for various materials
Choosing the suitable laser for different materials requires considering the material and the processing needs. Take, for example, CO2 lasers: it is cutting non-metallic items like wood, acrylic, and textile because of its efficiency over organic and synthetic substrates. Fiber lasers have an advantage over the cutting and engraving of metals because of their shorter wavelengths and higher energy density, which enable applications on steel, aluminum, and other conductive materials. Reflective or thicker metals are cut with specialized lasers equipped with higher power or dual sources to make precise and clean cuts.
How does CNC laser cutting compare to traditional cutting methods?

Compared to traditional cutting strategies, CNC laser cutting is more precise, efficient, and flexible. Instead of mechanical tools reliant on physical contact, lasers utilize concentrated beams of light that can easily cut through material without distortion, resulting in immaculate cuts. This make tools incredibly cheap as there is no upkeep required. Along with this, cutting intricate and minuscule details is made easy, unlike traditional techniques. It is often faster in high production, especially with complex designs. So, unlike other industries, laser cutting is favorable for sectors that need scaling. Nevertheless, some traditional methods are still useful and cost effective.
Precision and accuracy comparison: Laser versus conventional cutting
When comparing laser cutting with standard cutting, one can see that the former is holds the upper hand when it comes to shedding accuracy. The main reason is a laser beam’s ability to focus. The precision of laser cutting techniques often gets to about 0.01 inches (0.25 mm) tolerances, but in most cases, the beam cuts to and cannot exceed 0.001 inches (0.025 mm). In most cases, a mechanical cutter is only competent up to an accuracy of 0.01 inch or 0.25 mm. Such laser beam tolerance accuracy is because there are no moving parts to obstruct the laser cutting process physically.
Furthermore, physical interference, imparted forces on the laser beam, or deforming materials is cut out. Aside from that, laser cutters do not need any additional smoothing due to the quality of the cut edges. Standard cutting, when dealing with uncomplicated tasks, produces lower quality results and suffers from tool exhaustion and worn-out edges. Laser cutting also produces better edges on both sides of the cut and is more convenient to use in mass production as well. This aspect makes it more preferable for technologies with high standards of accuracy and significant amounts of detail.
Effectiveness and Sugcutting Laser technologies
As opposed to other cutting techniques, laser cutting is lauded for its speed and efficiency. This process is well suited for rapidly processing materials, especially thin to medium-thickness sheets. Thin stainless steel can be sliced with CO2 lasers at 20 meters per minute. Fiber lasers can achieve even higher speeds. When compared to other cutting processes, laser cutters have faster speeds due to minimal setup time, no physical contact, and an insignificant amount of tool changes needed. Moreover, CNC systems in automation increase productivity by allowing businesses to work non-stop without worrying about operational cycle times. These factors combined demonstrate why laser cutting is the most effective choice, especially in industries where speed and accuracy are necessary.
CNC Laser Cutting Cost Effectiveness
CNC laser cutting is cost-efficient because its accuracy and speed lead to minimal material wastage. It also eliminates the use of tools which reduces maintenance and incapacitates expenses. Since laser-cut components require no further processing, CNC CNC automation achieves greater efficiency alongside faster production cycles and consistent quality, significantly reducing labor costs. Moreover, its elimination of errors when handling different materials reduces rework and optimized resource use, making it an economical choice in various manufacturing applications.
What are the key advantages of using CNC laser cutting machines?
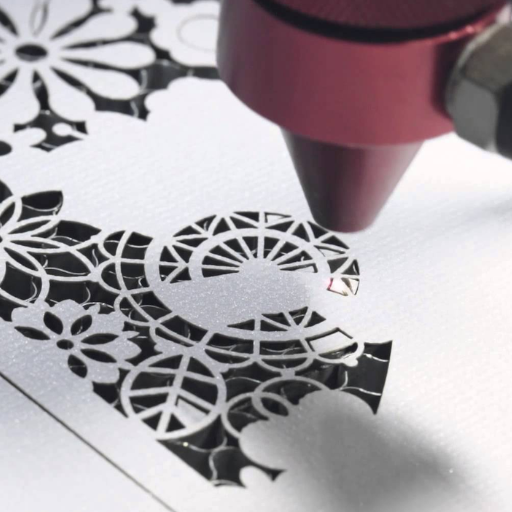
CNC laser cutting machines have one significant advantage. They allow for precise cuts on many different substances. Thus, there is an automation process. This improves the quality and reduces human error. It also boosts productivity in high-volume production terms due to CNC laser cutting machines’ speed and effectiveness. One more advantage is that the cutting process does not put in contact with tools. Physical tools are not required which minimizes costs, maintenance work and downtime. Thus, the features mentioned above, along with the CNC’s non-contact laser cutting mechanism, show that CNC laser cutting works towards and fulfills the requirements of modern manufacturing. CNC laser cutting does incur one or two issues. Just like any process, no system is perfect. But the problems created are much smaller than the benefits achieved.
Efficient methods to achieve powerful finishes with Creative Technology
CNC laser cutting machines do deliver best results, but the edges and charring do face damage. These issues appear when concentrating a laser beam in one area for a long time. Simply, it mesmerizes a lot of power in a single area. Additionally, the cutting speed, gas assist, power level and many more parameters must be set to achieve smooth edges. These requirements directly affect the surface finish quality from the starting point of laser focus to ending. Regular maintenance and high-quality optics also assist with the materials. So, for intricate works, the applications of these machines are numerous.
Flexibility for laser cuts in detailed patterns and designs
CNC laser cutting provides an unparalleled cutting flexibility for intricate designs and patterns. Different materials accommodate the specifics of the designs and are able to be produced without losing quality; in noncontact cutting, there is no physical force applied to the material, which makes it possible to minimize cutting deformation. The CNC laser cutting position serves as the leading precision tool for demanding industrial and artistic and design manufacturing processes.
Less waste of materials and higher efficiency
CNC laser cutting is advantageous because it lowers operational waste resources and increases efficiency. Because of the traditional methods of cutting, kerf width is maximized. This ensures the wasting of resources and by-products. This level of accuracy also rules out the need for secondary finishing processes, which further facilitates the steps in production. Furthermore, cutting speed and direction changes are done much faster, leading to lower machine idle time and energy spend. For example, fiber laser machines cut thin materials at 20 meters per minute, showcasing high throughput with dimensional accuracy. All of these features increase productivity while supporting more environmentally friendly manufacturing methods.
How to choose the right CNC laser cutting machine for your needs?
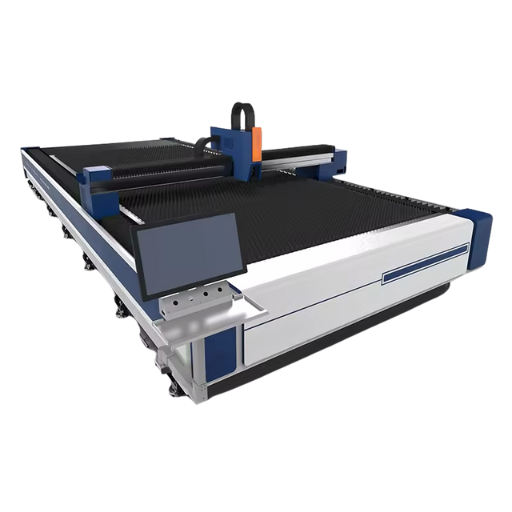
Identifying the right CNC laser-cutting machine requires understanding your needs and the materials you intend to use. Five critical aspects are the laser power of the CNC machine, which identifies its capability of penetrating various material thicknesses; the machine’s cutting precision and cutting speed, essential for time-sensitive operations. Check if the machine is compatible with the materials you intend to use, which may include metals, plastics, or composites, and if it properly enables your operational workflow. Check the machine’s software for user-friendliness and programming provisions, specifically on advanced nesting or designing. Also, long-term considerations such as maintenance, energy cost, and after-sale service should be considered for diligent and consistent operation in the long run. Balancing these factors with your goals and budgetary constraints will help you find the optimal solution for your CNC laser cutting requirements.
How to Analyze Power Requirements for your Cutting Projects
Examining power necessities for laser machining goes hand in hand with not exceeding the range of the material’s properties or the purpose of its utilization. For example, cutting thin parts from plastic and paper usually uses lasers from 20W to 150W for metal and denser materials. Industrial applications typically start with 300W and go up to several kilograms. Non-metallic materials are mostly cut with CO2 lasers, achieving high speed and precision with moderate power, and fiber lasers work best for metal because of their high power and greater efficiency.
These technical measurements include beam quality M² factor, where 1 indicates practical cutting focus, and more significant numbers equal worse focus precision. 1.06 microns is the laser wavelength for fiber lasers, while CO2 lasers use 10.6 microns. The laser’s cutting speed is also concerned with the power levels provided. With the thicker materials, deep penetration cuts as quickly as possible, but higher power grants less detail. In any production workflow, the most crucial factor is the amount of power required, and those factors need to provide the appropriate answer seamlessly.
Taking into account the limits of machine capabilities and cutting speed
Laser cutting parameters are always affected by a combination of factors: laser power, type and thickness of the material, and beam quality, to name a few. For example, fiber lasers cut metals faster than CO2 lasers for thin sheets, but CO2 lasers cut non-metals like acrylic and wood much quicker. This is because CO2 lasers have a better wavelength for those particular materials.
Some directly influencing factors of cutting speed are the laser wattage, wavelength, and assisted gas pressure. The M² factor greatly impacts how precise and fast the beam will be, and the closer to one, the more reliable the focus. The major two factors considered in outprints are the type and pressure of the assisted gas. For example, nitrogen is used to cut steel cleanly, while oxygen is more suitable with thick-steel outprints.
Each machine model has different capabilities, which are determined by axis speed, acceleration performance, and even the software being used. A machine with great axis acceleration and software path optimisation will give great savings with complex cuts. Thus, in order to achieve optimal performance, machine specification laser parameters must be precisely outlined for nuances.
Software Compatibility and Ease of Use Evaluation
Ease of use evaluation focuses on whether the target customers will be able to use or not based on the user support, documentation resources available, the interface of the software, and how smoothly they can learn to use the software. Software compatibility, on the other hand, evaluates software’s ability to work within the specified hardware and Operating system environment. This evaluation typically focuses on the Supported Platforms, System Requirements and Integration with other tools.
Reference sources
Frequently Asked Questions (FAQs)
Q: What is CNC laser cutting and how does it work?
A: CNC laser cutting is a precision manufacturing process that uses a high-powered laser beam controlled by a computer to cut materials. The CNC laser cutter focuses the laser beam on the material, vaporizing or melting it along a programmed path. This process allows for intricate designs and precise cuts in various materials, including sheet metal, plastics, and wood.
Q: What are the main advantages of CNC laser cutting?
A: The advantages of CNC laser cutting include high precision, speed, versatility, and minimal material waste. It offers clean cuts with minimal heat-affected zones, can handle complex designs, and is suitable for a wide range of materials. Additionally, CNC laser cutting is cost-effective for both small and large production runs.
Q: What types of lasers are used in CNC laser cutting machines?
A: The main types of lasers used in CNC laser cutting machines are CO2 lasers, fiber lasers, and crystal lasers. CO2 lasers are versatile and good for cutting non-metals. Fiber lasers are efficient for cutting metals and offer high cutting speeds. Crystal lasers, such as Nd:YAG lasers, are suitable for both metals and non-metals, providing a balance between CO2 and fiber lasers.
Q: How does CNC laser cutting compare to other CNC cutting methods?
A: Compared to other CNC cutting methods like CNC milling or CNC plasma cutting, laser cutting offers several advantages. It provides cleaner cuts, higher precision, and can work with a wider range of materials. Laser cutting also produces less heat-affected zones and is generally faster for thin materials. However, for thick metals, plasma cutting might be more suitable.
Q: What materials can be cut using a CNC laser cutter?
A: CNC laser cutters can cut a wide variety of materials, including metals (such as steel, aluminum, and stainless steel), plastics, wood, acrylic, fabric, leather, and paper. The type of laser and its power determine which materials can be cut effectively. For example, CO2 lasers are ideal for non-metals, while fiber lasers excel at cutting metals.
Q: How does the power of the laser affect the cutting process?
A: The power of the laser directly impacts the cutting capabilities of the machine. Higher-powered lasers can cut thicker materials and achieve faster cutting speeds. The laser power also affects the quality of the cut, with higher powers generally producing cleaner cuts. However, the optimal power depends on the specific material being cut and the desired outcome.
Q: What are the key differences between CNC laser cutting and traditional CNC machining?
A: The main difference is that CNC laser cutting uses a laser beam to cut material, while traditional CNC machining uses rotating cutting tools. Laser cutting is generally faster for thin materials and complex designs, produces less waste, and can work with a wider range of materials. However, traditional CNC machining is better for thick materials and 3D shaping. The choice between the two depends on the specific project requirements.
Q: How does CNC laser cutting contribute to precision manufacturing?
A: CNC laser cutting significantly enhances precision manufacturing by offering extremely accurate cuts with tolerances as small as 0.1mm. The computer-controlled process ensures consistency across multiple parts, and the non-contact nature of laser cutting eliminates tool wear issues. This precision is crucial for industries requiring exact specifications, such as aerospace, electronics, and medical device manufacturing.