In this blog post, we will delve into the intricacies of using a wet type fish feed extruder. This specialized equipment plays a critical role in the production of high-quality fish feed, which is essential for the development and health of aquatic life. We will explore the fundamental components and mechanisms of the extruder, explaining how it functions to convert raw materials into nutritionally balanced pellets. Additionally, the article will cover the advantages of using wet type extruders compared to their dry type counterparts, including efficiency improvements and enhanced feed digestibility. Through a comprehensive understanding of the extruding process, this post aims to equip readers with the expertise needed to optimize fish feed production. Whether you’re an aquaculture producer or someone in the fish feed manufacturing industry, this guide will provide practical insights and tips for maximizing the performance and output quality of your fish feed extruder.
What is a Wet Type Fish Feed Extruder and How Does it Work?
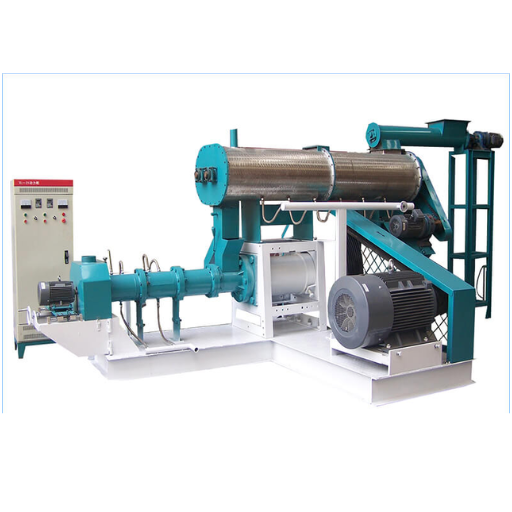
A wet type fish feed extruder is a specialized machine used in the production of aquatic feed pellets. It operates by mixing raw materials with water and steam, creating a cooked mixture that is then passed through a die to form pellets of the desired size and shape. The addition of water and steam helps in gelatinizing starches, improving pellet quality, and enhancing the digestibility of the feed for fish. This process also involves high temperature and pressure, which serve to sterilize the feed, making it safer for aquatic animals. Wet type extruders are known for their ability to produce high-quality pellets with a uniform texture, suitable for various species of fish and other aquatic life.
Understanding the Fish Feed Extruder Machine
A fish feed extruder machine consists of several key components: the feeder, conditioner, extrusion chamber, and cutter. The feeder introduces raw materials into the machine. The conditioner adds steam and water, preparing the mix for extrusion. Inside the extrusion chamber, a rotating screw pushes the mix through a small opening or die, shaping it into pellets. The cutter trims these pellets to the desired length. Wet type extruders apply moisture and heat, promoting starch gelatinization and improving digestibility. They also sterilize the feed, ensuring safety and uniform quality. These machines efficiently produce a consistent product tailored to the nutritional needs and preferences of aquatic species.
The Role of Hot Steam and High Pressure in Extrusion
Hot steam and high pressure play crucial roles in the extrusion process by transforming raw materials into high-quality fish feed pellets. The steam effectively softens and cooks the mix, facilitating the gelatinization of starches and improving pellet cohesion. As pressure intensifies within the extrusion chamber, it helps shape the pellets accurately according to the die’s design while also contributing to the sterilization of the feed. This high-pressure environment enhances the stability and durability of the pellets in water, ensuring they hold together without disintegrating. Thus, the application of hot steam and high pressure results in safe, nutritious, and easily digestible feed tailor-made for various aquatic species.
Comparing Wet Type and Dry Type Extruders
When I compare wet type and dry type extruders, I see a few key differences. Wet type extruders require steam and add moisture to the raw materials, which enhances the gelatinization of starches and increases digestibility. They also ensure sterilization and produce a consistent, high-quality pellet. These machines are ideal for aquatic feeds that need to be stable and nutrient-rich. On the other hand, dry type extruders do not require steam. They rely solely on mechanical friction for cooking, which can result in lower production costs but may not achieve the same level of sterilization or pellet quality as wet type extruders. Ultimately, the choice between wet and dry type extruders depends on specific production goals and resource availability.
Why Choose a Wet Type Fish Feed Machine for Your Feed Production?
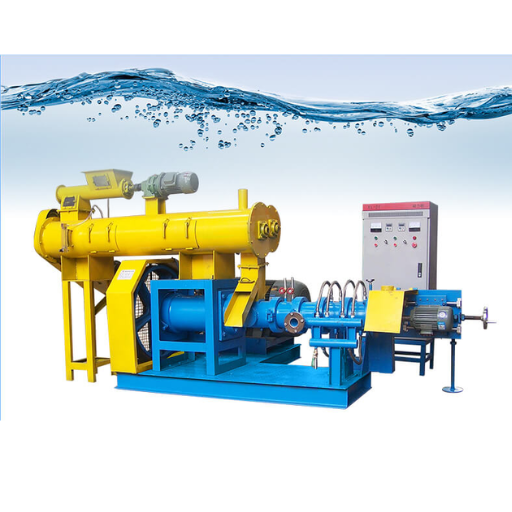
Choosing a wet type fish feed machine for your feed production can significantly enhance the quality and nutritional value of the pellets produced. These machines incorporate steam into the extrusion process, which greatly improves the gelatinization of starches, making the pellets more digestible for aquatic species. The addition of steam also aids in sterilizing the feed, thereby ensuring it is free from harmful pathogens that could affect the health of the fish. Moreover, the consistency and cohesion of the pellets are improved, allowing them to remain stable in water without disintegration. The overall benefits of using a wet type extruder include producing superior feed that is highly suitable for maintaining the health and growth of aquatic livestock, ultimately leading to better resource utilization and potential cost savings in the long run.
Benefits of Floating Fish Feed Pellet Production
Choosing floating fish feed pellet production offers several advantages. First, it improves feed digestion in fish, as the pelleting process enhances nutrient availability. Additionally, floating feed allows me to easily monitor fish feeding activity, reducing waste and improving efficiency. By using floating pellets, I ensure that the feed remains stable in water, which minimizes pollution in the aquaculture environment. Ultimately, this method helps me achieve better growth rates in fish and optimizes resource use, contributing to cost-effective and sustainable fish farming practices.
Enhancing Aquatic Feed Quality with Wet Extruders
In using wet extruders, I enhance the quality of aquatic feed by ensuring thorough gelatinization and sterilization, which boosts digestibility and fish health. The process improves pellet stability, preventing disintegration in water, thus reducing waste and environmental pollution. Consequently, I achieve efficient resource utilization and potential cost savings, supporting sustainable fish farming practices.
Cost-effectiveness and Service Life Considerations
When considering cost-effectiveness and service life, wet extruders offer significant advantages. Investing in high-quality equipment reduces maintenance costs and extends service life, delivering better long-term value. Efficient feed conversion reduces overall feed expenses, making production more economical. Additionally, optimized feed formulations lead to healthier fish, minimizing veterinary expenses and improving profitability. Regular maintenance and the use of durable materials further enhance the extruder’s lifespan, ensuring reliable performance and contributing to consistent cost savings. Overall, the combination of reduced waste, increased feed efficiency, and prolonged equipment durability supports a sustainable and financially viable fish farming operation.
How to Optimize Feed Pellet Quality Using a Wet Type Fish Feed Pellet Mill?

To optimize feed pellet quality using a wet type fish feed pellet mill, start by selecting high-quality raw materials that ensure nutritional balance and promote the health of aquatic species. Ensure that the ingredients are properly proportioned and mixed to achieve consistent pellet composition. Adjust the moisture content appropriately before processing, as optimal levels facilitate gelatinization and improve pellet durability. Monitor the temperature and pressure settings of the extruder to enhance pellet performance while ensuring complete cooking and sterilizing the feed. Regularly maintain the mill to prevent wear and ensure efficient operation. By focusing on these aspects, you can produce superior quality pellets that support sustainable and cost-effective fish farming operations.
Choosing the Right Raw Material for Feed Production
Selecting the right raw material for feed production is critical for enhancing feed quality and ensuring aquatic health. Choose materials rich in protein, essential for growth and muscle development. Opt for plant-based ingredients like soybean meal and corn gluten, which balance nutrition with affordability. Consider fishmeal and fish oil for their rich omega-3 fatty acids, which support immune function and reproductive health. Ensure all materials are fresh to maintain nutrient integrity and prevent spoilage. Regularly evaluate ingredient sources for contaminants and nutritional consistency. By carefully selecting and monitoring raw materials, you can create high-quality feed that supports successful and sustainable fish farming.
Importance of Conditioner in Feed Processing
Conditioning feed is vital for quality and efficiency. A conditioner improves feed by adjusting moisture and temperature, which enhances pellet quality and digestibility. By using steam, it softens raw materials, allowing for better compression and bonding during the pelleting process. This not only increases pellet durability but also ensures complete cooking, which helps in sterilizing the feed. Managing the conditioning process boosts production rates and contributes to energy savings. By focusing on optimal conditioning, I ensure the feed meets the nutritional needs of aquatic species while enhancing the overall efficiency of the feed production process.
Maintaining Optimal High Temperature and Pressure
To maintain optimal high temperature and pressure in feed processing, closely monitor these parameters throughout production. High temperatures facilitate starch gelatinization and protein denaturation, improving feed digestibility. Maintaining pressure during compression enhances pellet durability and reduces moisture levels, minimizing mold risks. Adjust machinery settings to keep temperatures consistent and pressures adequate for the desired feed quality. Regular calibration of equipment ensures precision and reliability, while routine inspections help identify and address deviations promptly. By focusing on these factors, you ensure efficient processing, yielding nutritious and stable feed products.
What are the Key Components of a Wet Type Fish Feed Extruder System?

A wet type fish feed extruder system comprises several essential components, each serving a specific function to ensure efficient feed production. The main components include:
- Feeding System: This component precisely regulates the flow of raw materials into the extruder, ensuring consistent feed input.
- Conditioner: It pre-treats the raw materials with moisture and heat, utilizing steam to improve the physical properties and nutritional quality of the feed.
- Extrusion Chamber: Where the actual extrusion process occurs; it includes a screw and barrel that compresses, mixes, and cooks the feed under controlled temperature and pressure conditions.
- Die: This component shapes the feed into the desired form and size by pushing it through specifically designed openings.
- Cutting Mechanism: Positioned at the extruder’s die exit, it slices the extruded feed into uniform pellets.
- Drying System: Post-extrusion, this component is responsible for removing excess moisture from the pellets, ensuring stability and prolonging shelf life.
- Control Panel: Facilitates monitoring and adjustment of various processing parameters like temperature, pressure, and rotational speed, ensuring optimal operation.
These components work together to produce high-quality, nutrient-rich feed for aquaculture, tailored to the dietary needs of fish species.
The Function of Single Screw and Pellet Mill
In a single screw extruder, I use a rotating screw to mix, compress, and cook the fish feed. The single screw provides efficient propulsion and processing of materials through the extrusion chamber, ensuring consistent quality feed production.
The pellet mill, on the other hand, compresses the feed into pellets with high density and uniformity. By applying heat and pressure, I bind the raw materials together, creating durable pellets that cater to the specific dietary requirements of various fish species.
Role of Boiler in Feed Production Line
The boiler plays a crucial role in the feed production line by generating steam used for cooking and conditioning the feed. It provides the necessary heat to ensure optimal gelatinization of starches, improving feed digestibility and binding. The steam produced by the boiler also sterilizes the materials, reducing the risk of contamination and enhancing the safety of the final product. Additionally, steam aids in moisture adjustment, contributing to the desired texture and cohesion of the feed pellets. By efficiently delivering steam throughout the process, the boiler supports consistent, high-quality feed production.
Integration with Feed Pellet Machine and Production Line
Integrating the feed pellet machine into the production line involves a seamless flow of materials from one process to the next. I ensure that the extruder, pellet mill, and boiler coordinate efficiently, creating a streamlined operation. By managing timing and adjusting operating parameters like temperature and pressure, I maintain product quality and consistency. Such integration increases the productivity of the feed production line, minimizing downtime and waste. I constantly monitor the system, performing checks to immediately address any issues, ensuring that the entire operation functions smoothly from start to finish.
What are Common Challenges in Fish Feed Production and How to Solve Them?

Fish feed production faces several common challenges, including ingredient variability, precise nutritional formulation, and maintaining product quality. Ingredient variability can affect the nutritional value and consistency of the feed, but using standardized raw materials and routine quality checks can minimize these variations. Additionally, achieving precise nutritional formulation is crucial, as it directly impacts fish growth and health. This can be addressed by employing advanced formulation software and expert nutritionists to tailor feeds to specific species and growth stages. Lastly, maintaining consistent product quality is vital for performance. Regular equipment maintenance, along with implementing stringent quality control measures throughout the production process, can help ensure a high-quality final product.
Addressing Feed Extrusion Issues
When I tackle feed extrusion issues, I start by assessing the equipment’s condition and performance. Regular maintenance and cleaning prevent buildup and wear, allowing for smoother operation. If I notice variations in pellet quality, I adjust the moisture and temperature settings to ensure consistent extrusion. It’s crucial to monitor die pressure and feeder rates closely; any deviation can impact product quality. By consistently checking these parameters, I can quickly resolve issues and maintain efficiency. Additionally, having a clear understanding of the specific nutritional needs of the feed helps me optimize the extrusion process for better digestion and nutrient absorption.
Managing Aquaculture Nutrition Needs
Meeting aquaculture nutrition needs requires a focused approach. I choose feeds specifically designed for each species, ensuring they align with the nutritional requirements derived from their natural diets. Regularly reviewing and adjusting formulations help me meet growth and health objectives. I incorporate high-quality protein sources, essential amino acids, and balanced lipids to promote efficient digestion and absorption. Additionally, I make sure that feed is rich in vitamins and minerals which are vital for immune function. Tailoring the feed strategy according to the life stage of the fish optimizes their overall well-being and minimizes waste in the aquaculture system.
References
-
Fish Feed Extruder – Wet Type Fish Feed Extruder: Provides detailed information on the use of wet type fish feed extruders for producing high-grade aquatic feed pellets.
-
Fish Feed Machinery – Wet Type Fish Feed Extruder: Offers insights into the production of both floating and sinking feed pellets using wet type extruders.
-
Feed Pellet Mill – Wet Type Fish Feed Pellet Mill: Discusses the capabilities of wet type fish feed machines, including their use in aquaculture farms and feed mills.
Frequently Asked Questions (FAQ)
Q: What is a wet type floating fish feed extruder?
A: A wet type floating fish feed extruder is a machine used for the production of aquatic feeds. It operates with water or steam, using temperature and high pressure to puff and shape the feed into pellets that float on water, ideal for fish farming.
Q: How does a wet type floating fish feed extruder differ from a dry type fish feed extruder?
A: The main difference lies in the use of steam and moisture. Wet type floating fish feed extruders use water or steam during the extrusion process, which helps in making pellets that are more digestible and can float. In contrast, dry type extruders do not use steam and are suitable for producing feed with lower moisture content.
Q: Why is it important for fish feed pellets to float?
A: Floating fish feed pellets are important because they allow fish farmers to monitor feed intake and reduce waste. Floating feeds are also generally more attractive to fish, helping ensure that they consume the necessary nutrients for growth and health.
Q: What are the benefits of using a wet type floating fish feed extruder for aquatic feed production?
A: Using a wet type floating fish feed extruder offers numerous benefits, including improved digestibility of feed, ability to produce a range of pellet sizes, enhanced control over pellet quality, and reduced risks of bacterial infections due to the high-temperature processing.
Q: Can a wet type floating fish feed extruder be used for other types of feed production?
A: Yes, a wet type floating fish feed extruder can also be used for making pet food and certain types of poultry feed. Its versatility makes it suitable for producing different feed types with specific nutritional profiles.
Q: What role does temperature and high pressure play in the extrusion process?
A: During the extrusion process, temperature and high pressure are crucial for cooking and shaping the feed ingredients. This combination helps in creating a puffed texture in the pellets, making them float and easier for fish to consume.
Q: What types of feed ingredients can be used in a wet type floating fish feed extruder?
A: Various ingredients such as fish meal, soybean meal, corn, and vitamins can be used in a wet type floating fish feed extruder. The choice of ingredients depends on the nutritional requirements of the fish species being fed.
Q: Is a wet type floating fish feed extruder suitable for medium or large size feed production?
A: Yes, a wet type floating fish feed extruder is suitable for medium or large size feed production. It can efficiently handle larger volumes of feed ingredients, making it ideal for commercial fish farms and feed mills.
Q: How does a single screw fish feed pellet machine work in conjunction with a wet type extruder?
A: A single screw fish feed pellet machine can be used in conjunction with a wet type extruder to achieve specific pellet characteristics. The single screw design allows for precise control over feed density and moisture, complementing the extrusion process.
Q: What maintenance is required for a wet type floating fish feed extruder?
A: Regular maintenance for a wet type floating fish feed extruder includes cleaning the machine after use, checking for wear and tear on parts, lubricating moving components, and ensuring that all control systems are functioning correctly to prevent downtime and ensure consistent pellet quality.