UV laser marking machines are the newest trend in the industry of precision engraving, enabling flawless and versatile marking on various materials. This mark guides its readers on how these machines work, the advantages they provide, and their common uses. Suppose you are a professional looking for advanced tools or a company examining engraving procedures. In that case, this article will explain the needs in detail alongside the technology behind UV lasers, how they differ from other marking systems, and important parameters when it comes to selection.
What is a UV Laser Engraving Machine and How Does It Work?

A UV laser engraving machine is equipment that precisely marks, engraves, or etches materials using an ultraviolet beam. It uses the steps of a photochemical process, utilizing a wavelength-shortening laser, usually around 355nm, which has a low thermal effect on the working piece. This method of marking works best when it employs high precision and sensitive components, as it requires no further damage or distortion.
The machine focuses on the material’s surface to start a photochemical reaction that vaporizes the material on a microscopic level. High-frequency, detailed, and precise markings can be done on heat-sensitive materials like glass, plastic, or certain metals. Unlike traditional laser engravers, UV laser machines have advantages, the most valuable being clear and contrast-rich engravings while maintaining optimal material integrity.
Understanding UV Laser Technology
UV laser technology uses short-wave ultraviolet light, usually 355 nanometers, to make precise marks and engrave through a photochemical process. This dramatically reduces thermal stress, making it perfect for projects requiring accuracy and material preservation. The core mechanism of a UV laser works by aiming a high-frequency beam onto the surface. This breaks molecular bonds within the material on a microscopic level without generating significant heat.
UV laser technology can achieve clean, clear, and high-contrast marks on sensitive materials such as plastic, glass, and metal. It’s imperative in electronics, pharmaceuticals, and aerospace industries, where the parts must be kept intact. UV lasers outperform traditional systems by ensuring precise, distortion-free results on sensitive, heat-absorbing substrates. Therefore, it is the most advanced damage-free technology for engraving and marking intricate items.
The Basics of the UV Laser Marking Process
In simpler terms, UV lasers mark by utilizing an advanced photochemical reaction. The lasers interact with the material’s surface and vaporize it to create permanent marks. This process does not rely on building heat and does not damage the substrate. The UV laser’s high frequency enables it to focus on the material with great precision, making it easy for the laser to interact with fine details and tricky surfaces.
Comparing UV Lasers to Other Laser Types
UV lasers are unique among laser types, like fiber and CO2 lasers, because of their shorter wavelength, which operates at 355 nm. Compared to other lasers, UV lasers have higher precision with cleaner results, especially for sensitive materials such as plastics, glass, and semiconductors. Unlike fiber lasers that employ thermal mechanisms on metals, UV lasers use cold marking, which does not include any thermal deformation or color changes.
What Are the Advantages of Using a UV Laser Marking Machine?
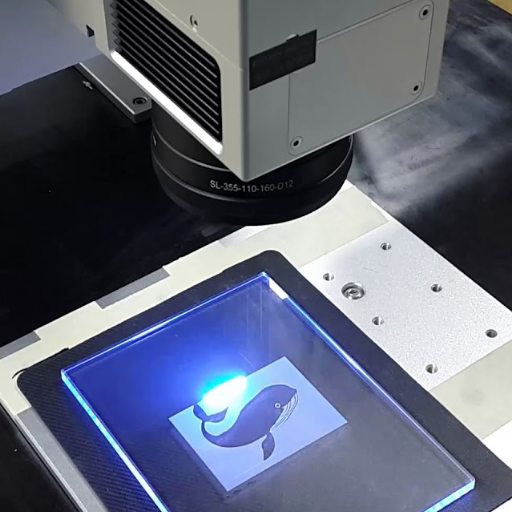
Because of their short wavelength of 355 mm, UV laser marking machines have outstanding precision and adaptability. This makes cold marking possible, eliminating thermal damage and retaining the integrity of more sensitive materials like plastics, ceramics, and glass. They are perfect for forming subtle and high-contrast marks on even the most sensitive and low-heat surfaces without scratching or discoloring them. Furthermore, UV lasers can have a broader range of materials, so they are heavily used in other sectors, including electronics, medical devices, and aerospace. Being able to engrave clear and detailed marks makes working within manufacturing and industrial applications much more effective.
High-Contrast and Precise Marking Capabilities
Because of UV laser marking machines’ benefits over other marking machines, they stand out in creating high-contrast and precise marking. The short wavelength also allows for fine energy focus, which results in intricate patterns and texts being greatly engraved. The cold marking process also greatly helps thermal distortion, which is helpful for heat-sensitive materials such as polymers, glass, and thin metals. Compared to the older marking methods, UV’s contrast stands out and brings incredible promise for durability. This is especially true for QR codes, barcodes, and logos because the prominence is ensured in medical equipment and electronics business requirements.
Versatility in Material Compatibility
UV laser engraving machines qualify for various materials such as glass, metals, ceramics, and even plastics. The systems score very high on adaptability. They use a nondestructive, cold-marking procedure that guarantees high-quality results without marring the material’s integrity. This flexibility ensures UV laser marking is perfect in several industries, including automotive, electronics, and medical devices, which require precision and durability to mark different substrates.
Cold Marking Process for Heat-Sensitive Materials
The cold marking procedure used by UV laser marking systems addresses problems relating to heat-sensitive materials. UV lasers utilize a shorter wavelength (355nm) that initiates a photochemical reaction instead of a thermal one, greatly restricting the substrate’s heat exposure. This guarantees that when marked, sensitive structures such as medical-grade plastics, thin films, or coated surfaces do not burn, warp, or discolor. Such precision makes it possible to mark complex geometries with high resolution, so clear and durable markings are guaranteed. This technique is vital in aerospace and biomedical engineering, which depend on material, stability, and detailing.
Which Materials Can Be Marked with a UV Laser Engraver?
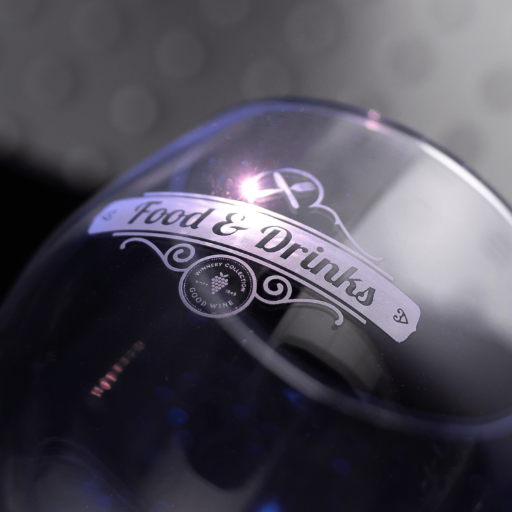
Ultraviolet laser engraving machines have proven flexible in marking different materials, such as plastics (polycarbonate, polyethylene, and medical-grade polymers) and treated metals, glass (borosilicate and quartz glass), ceramics, and even electronic foils. The marking is achieved through a damage-free, automated photochemical process perfect for heat-sensitive materials. Therefore, UV lasers can be integrated into most machines without worrying about causing damage.
Plastics and Polymers
UV lasers are incredibly efficient when it comes to engraving plastics and polymers. Their non-contact nature combined with thermal interaction simply burns a distortion-free process. The photochemical phenomenon provides contrast and engraves permanency for polycarbonate, polyethylene, polypropylene, and medical-grade polymers. Unlike traditional engraving, UV lasers don’t discolor, crack, or degrade the material. This accuracy is beneficial when marking fragile components like medical devices or electronic enclosures. Furthermore, polymers can be marked consistently regardless of the material’s composition and finish due to the high absorption power of UV cutting rays.
Metals and Alloys
While metals and alloys are not as common as plastics for UV laser marking, there are specific niches where it is beneficial. The procedure works well with coated, anodized, or plated metals, providing clear and precise markings without any physical material removal. For some untreated metals, such as stainless steel and titanium, UV lasers can engrave marks by either surface oxidation or working on a pre-treated layer. This approach fosters durability and precision and is suitable for aerospace, medical devices, and luxury goods industries where detail and permanence matter greatly.
Non-metallic materials like Ceramics and Glass
Because of UV wavelengths’ extreme accuracy and low thermal effect, UV laser marking is extraordinarily effective on non-metallic materials such as ceramics and glass. In ceramics, UV lasers permanently mark it by changing the surface structure, resulting in high-contrast markings without compromising the integrity of the material. This benefits the electronics and medical industries, where durability and readability are essential.
UV lasers create exceptional precision and clarity when marking glass by etching microfractures or a frosted pattern on the surface. The UV laser’s cold marking technique reduces the chances of microcracks, maintaining the glass’s strength and clarity. Furthermore, the UV laser method minimizes the risk of microcracks or structural damage while ensuring the strength and clarity of the glass are intact. This process enables engravings on laboratory tools, luxury items like glassware, and even applications in the automotive and architectural industries.
How to Choose the Right UV Laser Marking Machine for Your Needs?
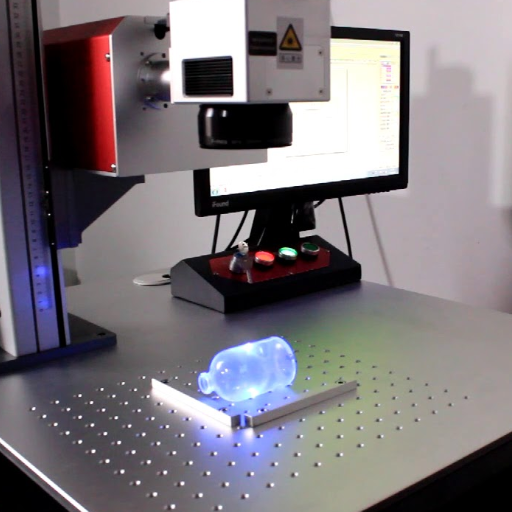
Selecting a suitable UV laser marking machine relies on equally essential factors unique to your needs. The first consideration is the material you want to mark. Different machines have different power ranges, which determine their marking potential on glasses, plastics, and ceramics. If the application is exact and has stringent restrictions on the amount of heat used, then a machine with good beam quality, super high energy stability, and a low heat level is crucial.
After that, you must look into how fast and at what resolution you need the marking done. High-speed automation machines work best for industries with high production rates and low mark legibility. Consider the level of software integration, as higher-level machines tend to have programmable attributes that facilitate the uncomplicated embedding of texts, logos, codes, or other patterns.
Last, ensure the machine is relevant to your industry certifications, like CE and FDA. Cost considerations should also include maintenance costs, as good, reliable machines with proper after-sales support will lower adequate downtime. Incorporating these aspects with your requirements will guarantee rigorous sanitation practices and a high return on investment from a UV laser marking machine.
Considering Laser Power and Wavelength
In assessing the laser power and wavelength suited to a UV laser marking machine, I am keen on the material and properties of the laser as well as the expected outcomes. UV lasers usually employ a marking wavelength of 355 nm, which allows for high precision marking while significantly reducing thermal effects, making it suitable for soft materials such as plastic, glass, and certain alloys. The power level also depends on the speed of marking and material thickness; low power is ideal for delicate tasks, while greater power is more appropriate for rapid engagements or strong engraving. Select application UV lasers can provide the midpoint between speed, accuracy, and detail with proper wavelength and power settings.
Evaluating Marking Area and Spot Size
Determining the marking area and spot size for UV laser marking machines extends beyond the boundaries of application specifications. The marking area, which outlines the working field of the laser system, establishes the largest possible area of the design or text that can be marked in a single action. Larger marking field machines are ideal for larger objects or multiple components that need marking done in one action, but too large of a marking field may cause marking precision to suffer.
The term spot size describes the figure created when the laser beam is focused, determining how precise and detailed the marking will be. With a smaller spot size, micro-markings, and detailed designs are achieved with higher precision. On the other hand, larger spot sizes allow for more straightforward coverage but compromise fine detail. In most cases, applications that combine acceptable accuracy and larger marking areas often require optics with the flexibility to adjust or galvo mirrors. The selection of marking spot size and marking area determines the efficiency and accuracy in meeting the application’s specific requirements, enabling flexibility without compromising output quality.
Assessing Additional Features like Rotary Attachments
These attachments significantly improve the capabilities of laser marking systems, making it possible to mark cylindrical or round objects with ease and precision. According to numerous online sources from manufacturers and industry experts, these attachments capture the object in a rotating mount while performing the marking; this allows the implementer to perform marking with flex on rounded surfaces while maintaining high quality. Using a rotary attachment on items like bottles, rings, or pipes is understandable because it easily marks complex angles. Laser systems with rotary tools make it easy to serve different marking applications without compromising quality and efficiency.
What Are the Key Components of a UV Laser Engraving System?
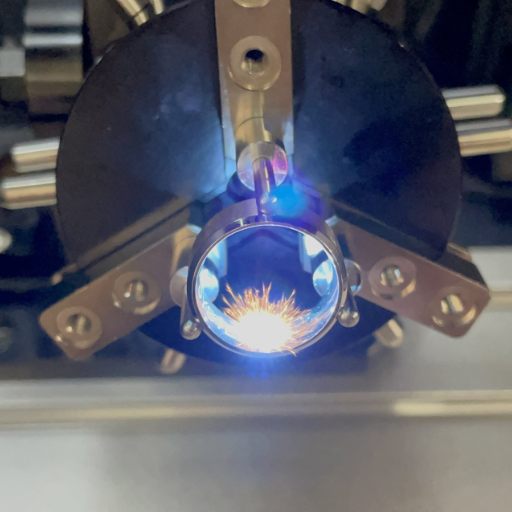
A UV laser engraving system comprises a UV laser source, a galvo scanner, a cooling system, and control software. The source employs a UV laser with a wavelength of 355 nm, and this is the most crucial part as it enables high precision and minimal thermal impact on sensitive materials. The engravings produced are precise since the galvo scanner rapidly and accurately directs the laser beam. A robust cooling system is necessary to maintain thermal stability and preserve the lifespan of the laser. The engravings also need to be customizable, and therefore, the control software allows for adjustment to patterns to make them compatible with various applications. These components are essential and work simultaneously, producing constant, high-quality results.
UV Laser Source and Laser Head
Ensuring high precision and minimized heat-impacted zones makes it possible for glass, plastic, and circuit boards to be engraved by the UV laser source single-handedly. The UV laser head features advanced focusing systems and intricate optics that ensure smooth delivery of the laser beam at a 355 nm wavelength, enabling exceptional reliability and accuracy. This amalgamation of technology makes it possible for the electronics industry, medical manufacturers, and industrial labelers to produce delicate items effortlessly and with maximal care. Moreover, better energy efficiency and increased customization ensure that enhanced modern design aids in prolonging the lifespan of the source.
Cooling Systems and Water Chillers
A perforated cooling system paired with water chillers optimally maintains the efficiency and stability of the UV laser engraver system. The system helps maintain an ideal temperature by precisely dissipating heat generated during use, increasing the overall lifespan of critical parts. Chillers have now been designed to operate energy-efficiently while still providing optimum performance. They help ensure the safe operation of higher-power lasers by preventing unnecessary overheating interruptions.
Control Software and Interfaces
Custom software and interfaces are essential for properly operating and tailoring UV laser engraving systems. These software solutions are designed to control such parameters as laser power, speed of engraving, and focal depth. Modern software control systems usually have a graphic user interface that allows the operator to upload designs, set parameters, and even simulate the engraving operation before carrying it out. Having the capability to use standard industry formats (e.g., DXF, AI files, or BMP files) guarantees effortless incorporation into existing processes.
More advanced systems deal with real-time monitoring and include diagnostic tools with remote or standby modes that assist in monitoring system performance and can identify probable failures. Networked versions allow greater functionality for remote control and integration into broader production systems. The newest software solutions also use machine learning and AI to enhance the quality of the engraving processes while automating intricate tasks to improve productivity and minimize human mistakes.
How Does UV Laser Marking Compare to Fiber and CO2 Laser Engraving?
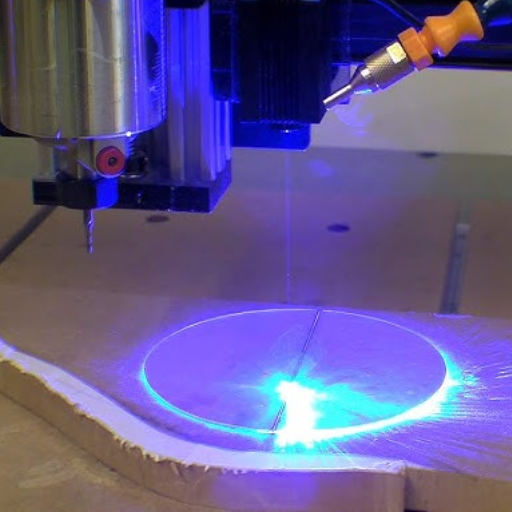
UV laser marking, fiber laser engraving, and CO2 laser engraving have different wavelengths and working mechanisms, making each type more effective for target-specific tasks. A UV laser has very short wavelengths (355 nm), which allows for cold marking as it dramatically reduces the effect of heat on the tool being worked on. Hence, UV marking is best used on heat-sensitive substrates like plastic, glass, and ceramics.
On the other hand, fiber laser engravers operate on long wavelengths (around 1064 nm) and scribe mid-grade on metals and some plastics with great precision and speed. They are very durable and low-maintenance, which makes them suitable for industrial environments. Moreover, CO2 lasers operate on even longer wavelengths (usually 10.6 µm), which makes them best suited for organic materials such as wood, leather, acrylic, and some plastics.
UV lasers are far less powerful and more expensive than fiber and CO2 systems. UV lasers allow for working with a broader range of materials with almost no heat damage. The strength of each technology varies, and its adoption entirely depends on the type of materials, desired results, and even budget.
Differences in Marking Quality and Precision
The precision and quality of laser marking are highly influenced by the properties of lasers, the materials used, and the intended applications. Ultraviolet lasers, for instance, stand out for their precision marking because they can create marks without altering the material’s surface. The short wavelength makes it easy to achieve high-contrast markings. As a result, they are widely used in electronics and medical devices where precision is of the utmost importance.
In the case of metals and some plastics, fiber lasers excel in providing deep, high-quality, durable marks accompanied by high clarity. They also perform high-speed marking with a constant level of accuracy. As a result, they are perfect for the automotive and aeronautical industries, where these features are highly valued.
Longer organic materials CO2 lasers are best suited for substrates like wood, glasses, and leather, where achieving clean and readable rings is essential. On the other hand, the markings done by CO2 lasers are not as fine as those done by ultraviolet and fiber lasers. Like all types of lasers, CO2 lasers have advantages and disadvantages over speed, resolution, and marking depth. The selection of lasers entirely rests on the application’s requirements and the materials’ properties.
Material Compatibility Comparison
Stainless steel, aluminum, brass, and some plastics can be processed accurately and effectively, making fiber lasers highly versatile. They are preferred for high-speed industrial marking on rigid materials. Ceramics, transparent plastics, and glass are better suited for sensitive materials. UV lasers are preferred because they have a shorter wavelength, provide high contrast, and do not damage the substrate. CO2 lasers do wonders on organic and non-metallic materials like wood, leather, acrylic, and glass by giving clean and smooth markings. Like each material requires a unique laser, the choice of laser type heavily depends on the desired marking characteristics.
Cost and Maintenance Considerations
The expenses and upkeep of laser marking systems differ concerning the type of laser, its use, and how intricate the system is. Fiber lasers are generally known for their high initial cost, but owing to their solid-state construction and lack of moving parts, they do not require much maintenance, which increases their lifespan. This makes them a good option for industries with high production rates. While UV lasers are more costly than fiber lasers, they also require specialized parts that must be carefully maintained to sustain precision over time, which could increase ongoing maintenance costs. CO2 lasers, on the other hand, are relatively inexpensive. However, they may need more frequent maintenance for components like the laser tube, a consumable part that must be replaced occasionally. Generally, the decision on a laser system should consider the purchase price, operational productivity, required maintenance, and how all these factors relate to the actual production needs and materials used.
What Are Common Applications for UV Laser Marking Machines?
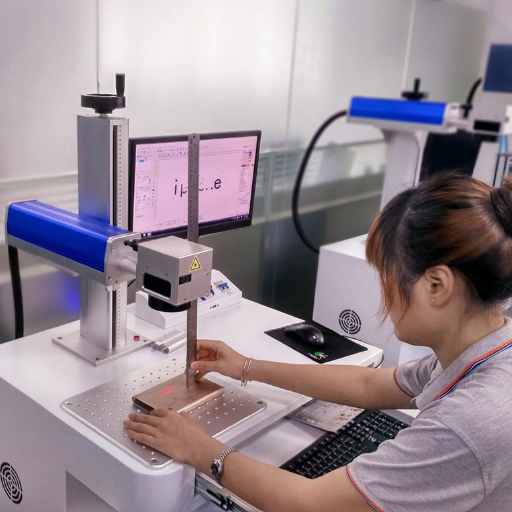
Machines that mark with a UV laser are popular for their precision and low heat damage. The laser adversely damages delicate materials such as glass, plastic, and ceramics. They are common in the electronics industry for marking PCBs, microchips, and display panels and in the medical field for engraving surgical tools, medical devices, and even medicines. Moreover, UV lasers are perfect for applying permanent marks to products that must adhere to stringent traceability and regulatory requirements. It is crucial in quality-centric and accuracy-centric industries because of the ability to produce high-contrast, fine details swiftly and without any material damage.
Industrial and Manufacturing Uses
Because UV laser marking machines precisely and minimally impact the laser-marked object’s materials, they are commonly used in production and engineering automation to mark logos, barcodes, and serial numbers for semiconductors and other electronic devices. In addition, they are also used in the automotive sector for permanent coding for lenses, sensors, and switches, as these parts are subjected to extreme working conditions. They are also extensively used to mark luxury goods like watches and jewelry, owing to the high-quality detail and definition required when performing intricate designs. These machines can be used with different materials in various industries, making them appealing to modern production processes.
Medical Device Marking
The medical device sector relies heavily on UV laser marking machines because they can create high-quality, permanent, and very legible markings on sensitive materials. These markings include UDI codes essential for regulatory compliance and traceability. Markings produced with UV laser technology are free from contamination or raised surfaces, which is necessary for surgical instruments, implants, and catheters. Moreover, UV laser technology extends its usefulness to metals, plastics, and ceramics, which further endears it to the stringent requirements of the medical industry.
Electronics and PCB Labeling
UV laser marking machines are handy in the electronics and PCB labeling sectors because of their speed and accuracy. These lasers can etch detailed markings onto sensitive components such as barcodes, QR codes, serial numbers, and even logos without compromising the part’s functionality. The contrast of UV marks is so high that they can be read accurately even under extreme temperatures, humidity, and in environments filled with chemicals. This feature sets them apart from conventional marking techniques, allowing them to meet the rigorous demands of the industry.
The processing method that does not involve physical contact renders UV lasers optimal for sensitive electronic parts and multilayer PCBs because there is no risk of surface distortion or chemical pollution. Moreover, ultraviolet laser technology is compatible with FR4, ceramic substrates, and flexible plastics, which are regularly used in electronic fabrication. With minimal thermal effect, UV laser marking systems provide high marking quality, thus making these systems critical in providing traceability, quality assurance, and branding inthe modern electronic industry.
References
Frequently Asked Questions (FAQ)
Q: What is a UV laser marker, and how does it differ from a fiber laser engraver?
A: A UV laser marker is a laser machine that uses ultraviolet light (typically 355nm wavelength) for marking and engraving. Unlike a fiber laser engraver, which uses infrared light, UV laser markers are better suited for sensitive materials due to their higher absorption rate and lower heat stress. This makes UV laser machines ideal for marking on various materials, including plastics, glass, and ceramics.
Q: What are the advantages of UV laser for marking applications?
A: UV laser machines offer several advantages for marking applications. They provide high precision and high contrast markings, especially on heat-sensitive materials. The 355nm UV wavelength has a high absorption rate in many materials, resulting in cleaner and more precise marks. UV laser markers also cause less thermal damage, making them suitable for delicate materials. Additionally, they excel in creating fine details, QR codes, and permanent markings on various surfaces.
Q: How does the wavelength of a UV laser marker affect its performance?
A: The wavelength of a UV laser marker, typically 355nm, plays a crucial role in its performance. This shorter wavelength allows for higher energy absorption by many materials, resulting in more efficient marking. The 355 nm UV light interacts differently with materials compared to infrared lasers, enabling marking on surfaces that may be challenging for other laser types. This wavelength also contributes to the UV laser’s ability to create high-contrast marks with minimal heat-affected zones.
Q: What types of materials can be marked using a UV laser machine?
A: UV laser machines are versatile and can mark various materials. They are particularly effective for marking plastics, including acrylic, polycarbonate, and ABS. UV lasers also excel in marking glass, ceramics, and certain metals. They are ideal for sensitive materials damaged by the heat from other laser types. The high absorption rate of UV light in many materials makes these machines suitable for creating high-contrast marks on both light and dark surfaces.
Q: How does a UV laser marker compare to other laser marking solutions?
A: UV laser markers offer unique advantages compared to other laser marking solutions like fiber or CO2 lasers. Due to their shorter wavelength, they provide superior results on heat-sensitive materials and can create finer details. UV lasers typically cause less thermal damage than infrared lasers, making them ideal for delicate components. While fiber lasers may be more suitable for metals and CO2 lasers for organic materials, UV laser markers are versatile, offering high-quality marking across a diverse range of materials.
Q: What power levels are typically used in UV laser marking machines?
A: UV laser marking machines have various power levels for different applications. Standard power ratings range from 3-watt desktop lasers to more powerful 10W systems. The choice of power depends on the specific marking requirements, material properties, and production volume. Lower power systems (3-5W) are often sufficient for many plastic and glass marking applications, while higher power systems may be needed for faster processing or marking on more challenging materials.
Q: How do UV laser markers contribute to traceability in manufacturing?
A: UV laser markers significantly affect manufacturing processes’ traceability. They can create high-precision, permanent markings such as serial numbers, date codes, and QR codes on various products. UV laser markings’ high contrast and durability ensure long-term readability, which is crucial for product tracking and authentication. UV lasers’ ability to mark on various materials without damage makes them ideal for adding traceability features to sensitive components in industries like electronics, medical devices, and aerospace.