Strip packaging machines have become an integral component of contemporary manufacturing processes, particularly in industries where precision, efficiency, and product protection are paramount. These machines are designed to individually seal products, such as tablets, capsules, or small components, between layers of protective film, ensuring product safety and extending shelf life. Their ability to streamline packaging workflows while maintaining stringent quality standards has made them a preferred choice for pharmaceutical, food, and electronics sectors. This article outlines the primary advantages of utilizing strip packaging machines, highlighting their role in optimizing production, minimizing material wastage, and complying with regulatory requirements. By understanding their capabilities, manufacturers can make informed decisions to enhance their operational efficiency and product presentation.
What is a Strip Packaging Machine and How Does It Work?
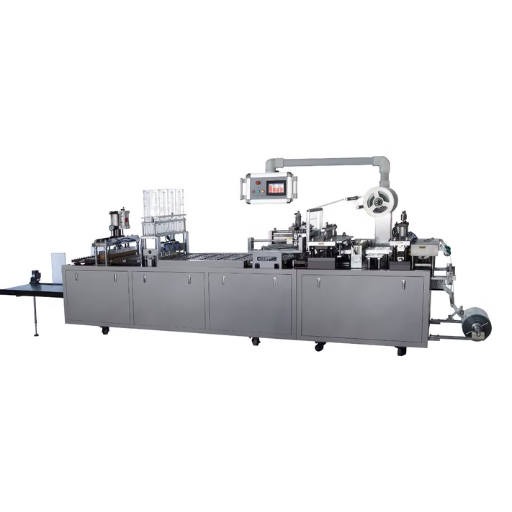
Strip packaging machines encase single doses, such as tablets or capsules, in a protective layer of aluminum foil or plastic film. The machine works by passing the packaging material through rollers that precisely seal the pouch around each individual item under heat and pressure. At the same time, trim excess material to produce uniform hermetically sealed strips. The sealing ensures protection from environmental factors such as contamination and moisture while providing compliance to stringent packaging requirements, thus maintaining product quality and longevity.
Grasping the Fundamentals of Strip Packaging Technology
Efficiency and precision lie within the key principle of the strip packaging technology. The procedure starts with the selection of appropriate packaging materials, including aluminum foil, laminated film, or plastic, depending on the level of protection from moisture and light the product requires. The aluminum foil is assumed to be between 20 to 30 microns while plastic film ranges from 50 to 100 microns.
Crucial to the machine are the cutting sealing systems which function based on the material utilized. This means they have controlled temperatures between 150°C and 200°C. Moreover, the pressure settings are just as vital as they aid in achieving uniform sealing of all strips without destroying the enclosed item. In addition, accurate cutting is just as important and is often completed with tolerances of ±0.1 mm to make certain that every strip has the same dimensions.
With rear and front gates on the machines set within optimal parameters, production rates of up to 300 strips per minute are possible without the loss of alignment of the materials and final products. A guide for the edges of the strips with roller tension, dwell time in the sealing zone, and trimming all aid in accomplishing effective and operationally ready equipment. The technology generally guarantees a strong and safe packing method that can be done within a certain timeframe while complying with all pharmaceutical standards.
Parts of a Strip Packing Machine
Heating System
The heating system serves as the main part of the sealing process. The sealing region is heated within the range of 150 to 200 degrees centigrade. This makes it possible to achieve an even seal across the entire surface of the chamber. Such accuracy is important for all materials used in aluminum-polymer laminate and the plastic films.
Sealing Rollers
These rollers create a seal that is uniform throughout the packaging by applying adequate pressure. The sealing rollers maintain consistent and supporting pressure while adjusting to various material thickness levels to avoid distortion or harm to the packed items.
Cutting Mechanism
The cutting system utilizes a dimensional allowance of ±0.1 mm to separate individual strips. This allowance is important for achieving uniformity and ensures compatibility with downstream operations like cartoning or inspection machines.
Feed System
The feed system is able to maintain synchronization with the movement of materials and tagged items within the machine. The system is able to maintain operational alignment and support production speeds of up to 300 strips per minute due to adjustable feed rates and algorithms.
Tension Control Unit
The tension control unit helps measure and manage the tightness of the tag fed into the machine. Proper packing tension prevents unwanted wrinkles, misalignment, and excessive material waste while also optimizing sealing and the accuracy of cuts.
Control Systems
Modern Strip packing machines are fitted with integrated electronic control systems stretch enabling the precision adjustment of parameters. Their capabilities include adjusting heat, pressure, cutting speed, and product alignment in real time for consistency in production quality.
Inspection Module
Inspection units have the responsibility of confirming seals and looking for flaws like cuts that are not aligned, loose sealing, and contamination. Vision systems or sensors are also embedded into these modules to ensure that all units are checked for quality as they move along the production line.
The Step by Step Process of Strip Packaging
The procedure for strip packaging starts with the provision of the packaging material, which is fed into the device in the appropriate position to ensure high efficiency. The item is introduced into the product between layers of packaging material, either using machinery or doing it by hand. Then, the next step consists of placing the product in dash heated or dash pressure sets, which permanently seal it against the packaging material, thereby preventing external interference and allowing the product’s integrity to be maintained. After this, the material is cut into precise strips to achieve desired strain, ensuring that all units of the system are within range. Measures of maintenance for such an automated control system include automated ones that allow the detection of random and systematic mistakes that transcend accepted norms.
What Are the Main Benefits of Using Strip Packaging Machines?

The foam form fill seal (FFS) packaging machines exhibit high productivity that arises from combining high-speed and high-volume production with a high level of automation. In all industries, packers are concerned about the efficient protection of the product for logistics and storage purposes. All packers aim for the most efficient protection of products, both during transportation and storage. In addition to high levels of operation, accuracy and consistency are of utmost importance in the pharmaceutical and food industries. In order to reduce the need for human interaction during the packaging process, businesses have increasingly resorted to the use of advanced technology, which enables the automation of repetitive tasks. This is achieved through the utilization of strip machines, which results in minimal contact and better hygiene.
Automation Reduces Operating Times and Increases Output.
Manual operation processes such as cutting, sealing, dispensing, and other actions are often highly repetitive and do not require deep thought or strategy. Hence, the utilization of advanced sensitive technologies enables the automated control of these processes through the employment of Sensitive Technology Control Methods. Ultimately, these advancements allow for greater output to be achieved in less time, with a more streamlined approach.
Improved Safety during Storage and Longevity of Products
The use of strip packaging machines guarantees superior protection of sensitive compounds through an airtight seal that easily mitigates the penetration of moisture, contaminants, light, etc. The materials used in strip packaging, such as aluminum foil or laminates, are highly regarded for their effectiveness against external elements such as air, ensuring the validity and stability of the packed item. Such sealing not only preserves the integrity of the product but also increases its shelf life which is invaluable in especially sensitive products such as pharmaceuticals and other perishables. In addition, the risk of contamination is also greatly reduced due to the salient features of the controlled environment in which packages are done, thus meeting rigorous requirements in the industry about safety and hygiene.
Affordable and Faster Packaging for Companies Across Different Fields
The strip packaging machines provide an economic edge in addition to effective packaging by mitigating material loss as well as lower operational expenses. Their speed makes them ideal for companies with slim profit margins that depend on economized packaging as well as rapid production. These machines also cover a lot of ground in terms of versatility, as they can handle different materials and products and still maintain high standards. They are also economic due to their robust construction, simple functionality, and lack of maintenance – all important when considering long-term ROI for pharmaceutical, food, and industrial businesses.
Which Industries Can Benefit from Strip Packaging Machines?
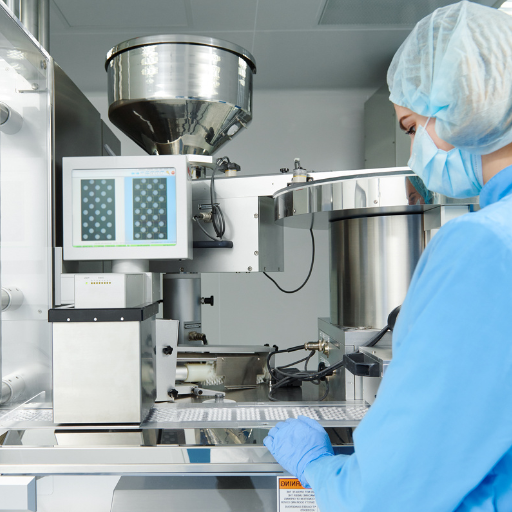
The pharmaceutical sector makes use of these machines for packaging tablets, capsules, and diagnostic products by safeguarding the correct dosage whilst preventing cross-contamination. Strip packaging machines offer pharmaceutical companies unmatched accuracy, cleanliness, and productivity. The food industry also uses these precision machines to package intricate blended spices and candies in bulk while ensuring extended freshness. Moreover, industrial companies utilize these packaging machines to safely store small electronics parts and hardware bulk components that need to be saved from impacts during shipping and handling. These machines are crucial for maintaining product integrity across different industries.
Pharmaceutical Industry: The Packaging of Tablets, Capsules and Lozenge
In tablet, capsule, and lozenge production within the pharmaceutical industry, the strip packaging machines are crucial to the device’s safety and integrity. These machines utilize a cutting system that cuts strips from roll stock film using heat-sealable foil or laminated polymeric films. The process uses barrier films that protect against oxygen, moisture, and light contamination. Most strip packaging machines utilize dosing systems and rotary cutting systems, which precisely divide the packed material into predetermined dimensions. Common parameters included a range of adjustable sealing temperatures between 100°C and 250°C, speed of production from 200 to 450 packs per minute, and the use of films with thicknesses of 50 to 150 microns. These settings make it possible to maintain high hygiene and quality standards which are important in pharmaceuticals. Also, these machines are equipped with parts that feed the machines and inspect the quality of products, simplifying the production process in linear with the ever-growing production regulation.
Food and Beverage Industry: Packaging of Single-Serve Portions Gets an Upgrade
The food and beverage industry relies on strip packaging machines to efficiently seal single servings of condiments, sauces, and powdered drink mixes. These machines use a method of heat sealing that surrounds the item in a tamper-proof package that keeps the contents fresh, safe, and uncontaminated. The machines also feature adjustable sealing temperatures and advanced material compatibility, allowing for increased treatment and efficiency on high-demand production lines. They are also ideal for moisture rich environments, as the product remains uncontaminated. In addition to this, incorporating moisture and air quality control systems paired with high-speed machines ensures food safety requirements are adhered to while increasing production. These systems are critical to optimizing production workflow and improving customer satisfaction while ensuring product integrity.
Consumer Goods: Multi-Level Packing for Tiny Capsules
The strip packaging machines facilitate the assembly of consumer goods for use with small-sized products like hardware, batteries, and cosmetics. These systems incorporate advanced automation, allowing for the rapid sealing of pouches using sophisticated methods and, at the same time, enhancing product consumption by making them easy to view while being encased. Hardware like stuffing machines is often incorporated allowing for the swift transition from singular boxes to bulk containers, thus greatly improving productivity. This versatility further increases operational flexibility and allows the delivery of quality products to the market in a timely manner to satisfy consumer and industry needs.
How Do Strip Packaging Machines Compare to Blister Packaging Machines?

Strip packaging machines and blister packaging machines serve distinct purposes, with differences focused on their structural and operational packaging differences. Products that need to be packaged using strip packaging methods are sealed between two layers of foil or film, which is suitable for most moisture sensitive products, especially medicines. On the other hand, the blister packaging cavity is created out of durable plastic and sealed with a backing, which works perfectly for consumer goods as it makes the package tamper-proof as well as eye-catching. While strip packaging is great for single-use unit doses, blister packages can have more visual marketing, making them more appealing for retail settings. Both options serve specific requirements but, in the end, are modified to achieve expected product parameters and usage.
Differences in Packaging Process and Materials
The approaches and components used in strip and blister packaging are worlds apart from each other. Strip packaging processes begin by placing items between two films made of foil or coating plastic. The films are then heated under a certain amount of pressure to create units. This method protects sensitive items from moisture and other environmental conditions, making it ideal for easily damaged items. In contrast, a cavity or pocket is formed in the sheet of foil or plastic in blister pack, and the product is attached to the sheet with a corresponding lidding material. Cavity formation is achieved through a thermoforming or cold forming process. The materials selected for blister packs also ensure product safety and visibility, thus protecting them from tampering whilst making retail promotional display easy. The precision in selection for the materials and sealing technologies for the packaged items is what makes both formats unique.
Judging Efficiency and Output Parameters
When considering efficiency and output parameters, the performance of strip packaging tends to be more efficient than blister packaging when it comes to high volume production speed. Strip packaging machines have less frequent interruptions such as pauses or breaks and are therefore often constructed to run non-stop, increasing throughput. However, blister packaging is much more flexible with regards to customization in shape, size, tamper evidence features, and product visibility, which may set production speed back based on the complexity of the design. Moreover, the precision that is required during the thermoforming and cold-forming stages in blister packaging can slightly decelerate the process due to material handling. Ultimately, the selection between the two boils down to product protection, presentation, and company’s intention in manufacturing.
When to Use Strip Vs. Blister Packaging
As for the airtight sealing and protection from elements like moisture, light, or oxygen, strip packing is appropriate. It is most suitable for unit-dosed tablets and capsules. The continuous sealing mechanism in strip packaging ensures superior hermetic integrity without relying on complex thermoforming processes, making it a preferred choice for sensitive pharmaceuticals.
Blister packaging, however, works well for products which need to be seen, where branding is valuable, and where tampering is suspected. Its design offset areas can be made to unique shapes and sizes, making it suitable for a variety of products, including medical devices, consumables, and food. Blister packaging is particularly proficient at providing mechanical protection during the transport and handling of a product while also enabling easy dispensing of the product.
From a technical perspective, strip packaging is effective when there is a need for light seal strength and simplicity instead of speed, as it works on average 120-160 packs per minute. Blister packaging machines are more versatile; they typically process 80 to 150 cycles per minute depending on features such as the cavity design, the type of material used, lids, and whether the package is perforated. Material selection also plays a vital role; strip packaging primarily uses aluminum foils for barrier properties, while blister packaging combines PVC, PVDC, or aluminum laminated materials for durability and presentation.
To select the best method requires identifying the balance that can be struck between how efficient the process is, what the product demands, and how environmentally friendly or promotional the exercise needs to be. For example, strip packaging is relatively simple but provides less scope for brand identification compared to blister packaging, which provides the necessary custom branding but at the chutney of production speed.
What Features Should You Look for in a High-Quality Strip Packaging Machine?
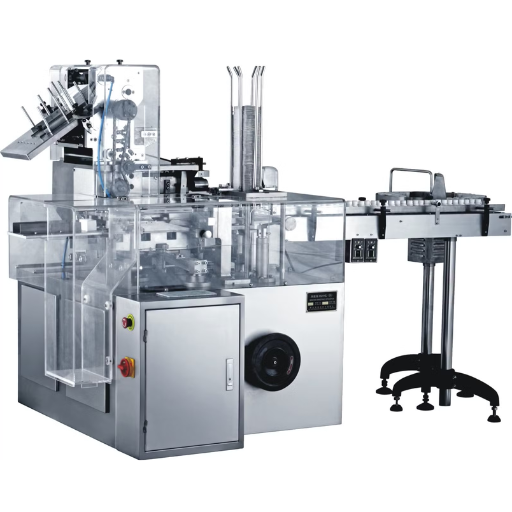
While choosing the best strip packaging machine, focus on sturdy construction to guarantee a long life while maintaining high performance levels. It should have a flexible configuration that can deal with numerous product shapes and materials, as this improves the adaptability of the machine for different uses. It should possess the ability to maintain the required temperature and sealing pressure in order to ensure package integrity and material economy. Features such as automated accurate product feeding and efficient synchronization are important for maximizing productivity, as well as decreasing human error. Any models that are easy to maintain, straightforward to use, and properly designed to save space in a manufacturing environment should also be considered.
Automation Features and Intuitive Controls
Innovative strip packaging machines have additional features that drastically improve efficiency and accuracy. These include automatic product feeding devices, electrically controlled sensors, and programmable logic controllers (PLCs). Touchscreen interfaces often result in intuitive controls that allow operators to adapt settings, check active parameters, and resolve potential problems as they arise. These features, together with streamlining production, reduce breakdown time and ensure consistent high-quality packaging work.
Modifiable Capabilities for Varying Product Capacity and Size Portion Requirements
Apart from the extensive strides made in innovation in the strip packaging market, it is worth noting that productivity and ROI per investment are taken into considerations when setting the manufacturing requirements for the strip packaging machines. These specifications range from bolting supporting frameworks to the packing tape available. These features include adjustable sealing settings, modular feeder systems, and selectable interchange-forming plates, all of which enable the machine to accommodate various product ranges. Apart from these specifications, different material types, antenna-grade aluminum foils, heat-settable film, multilayer laminate, etc., are also commonly used, and this helps ensure that the product is compatible with the specified requirements. Such freedom helps manufacturers fine-tune production processes for both general and niche cases, productivity flexibility, and operational effectiveness.
Packaging Effectiveness and Contaminant Protection Techniques
As mentioned, the primary issue in strip packing is the seal integrity and, therefore, the performance of the strips and products inside the pack can greatly differ. In addition to the above-stated reasons, modern strip package packing machines are designed so that the functionality of packing strips is manufactured with resilient, airtight, and tamper-proof seals. These seals enable protection from environmental contaminants like water, oxygen, and bacterial factors. Furthermore, the risk of contamination during packaging process is eliminated due to cleanroom design compatible with construction and features of automated material handling systems. Furthermore, by deviating from standard operating parameters for sealing strips while adhering to more suitable parameters for production hygiene, the set standard of quality and sanitary standards for packs can be maintained, ensuring compliance requirements, and protecting the trust of the end user.
How Can Strip Packaging Machines Improve Pharmaceutical Packaging?
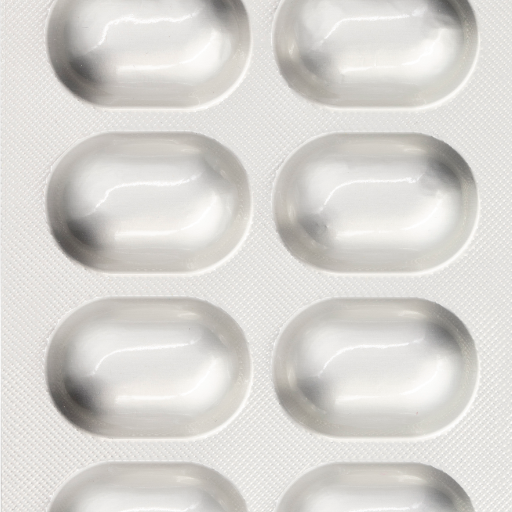
Strip packaging machines have been developed to suit the delicate requirements of pharmaceutical packaging. They allow for careful dosing, greater product protection, and extensive shelf life of the goods. With the machines’ capability of forming airtight and tamper-resistant seals, medications are secure from humidity, light, air, and other factors that may lessen the quality of the product. The automation features also enhance the speed, precision, and uniformity of the packaging process, thereby minimizing wastes in materials and production mistakes. In addition, these machines aid in achieving the demanding regulatory requirements by using serialization and track-and-trace systems for easy identification and tracking of medicines within the supply chain.
Maximizing Patient Compliance and Controlling Dosage Accuracy
In the pharmaceutical section, strip packaging machines are important in maximizing dosage precision and improving patient compliance. These machines have exceptional accuracy in packaging individual doses through advanced metering systems and will always maintain the right measurements. They encase medications in unit doses, which helps in preventing both overdosing and underdosing, which greatly puts the safety of a patient at risk. In addition, the use of clearly visible labels and different forms of unit dose packaging further ensures that patients will comply with the prescribed medication minimizing the possibility of medication errors.
From a technical viewpoint, machines used for strip packaging achieve exceptional dosage accuracy precision through servo-controlled systems and micro-dispensing technology. They dispense specific amounts of drugs, with a tolerance margin of dispensation as tight as ±0.5%. For patient compliance assurance, the automated micro-dispensing systems allow clear monitoring of dose intervals and medication tracking, and compact digitalization improves adherence monitoring. The materials, which are also actively managed to prolong the effectiveness of the medication, are designed to capture high demand barriers, thus ensuring proper pharmaceutical grade requirements are met while providing optimal medication preservation. The amalgamation of these features complies with standard industry regulations under Good Manufacturing Practices (GMP) and ISO 15378 for the pharmaceutical packaging processes.
Satisfying Pharmaceutical Packaging Regulations
In terms of regulatory requirements, pharmaceutical packaging has to comply with international standards for product safety, efficacy, and quality. “FDA 21 CFR Part 11” requirements call for the use of secure, validated electronic systems that deal with production data and record-keeping. Complying with ISO 15378 guarantees that the primary packaging materials will achieve quality, particularly relating to contamination and patient safety. In parallel, EU regulations, especially the Falsified Medicines Directive (FMD) also require a unique ‘anti-counterfeit’ identification of medicines through Explicit Serialization of all products with a bar-code and unambiguous identification of medicines along with tracing capabilities throughout the supply chain. Undoubtedly, these standards require rigorous documentation and validation of procedures together with effective quality management systems which is consistent with Good Manufacturing Practices (GMP).
Flexibility in Packaging Various Dosage Forms
Flexibility in packaging various dosage forms is crucial to meet different pharmaceutical needs and encourage compliance with prescriptions. Packing solutions should be able to accommodate solids such as tablets and capsules, liquids, which include syrups and amps, semi-solids like creams and gels, as well as special delivery systems, which include transdermal patches or inhalers. What is most important to note is how the material will provide protection from damaging exposure (moisture, light, oxygen), whether it will be compatible with the Active Pharmaceutical Ingredient (API), and if it can be designed with anti-tamper and child resistant features. In addition, new technologies in packaging now allow for unit dose dispensing practices, enhanced shelf life, and overall better standard of servicing to the patient. These changes, taken together, lead to improved patient outcomes.
Reference sources
Frequently Asked Questions (FAQs)
Q: What is a strip packaging machine and how does it differ from a blister packing machine?
A: A strip packaging machine is a type of pharma packaging equipment that forms, fills, and seals products into individual pockets or “strips” made from heat-sealable materials. Unlike a blister packing machine, which typically uses thermoforming or cold forming to create rigid cavities, strip packaging machines create flexible, continuous strips that can be easily separated by consumers.
Q: What are the main benefits of using strip packaging machines in manufacturing?
A: The benefits of strip packaging machines include improved product protection, extended shelf life, enhanced tamper-evidence, easier dosage management for pharmaceuticals, reduced material waste, and increased packaging efficiency. These machines are particularly useful for packaging tablets and capsules, as well as other small items.
Q: What types of products can be packaged using a strip packaging machine?
A: Strip packaging machines are widely used in the pharma industry to pack a wide range of products, including coated and uncoated tablets, soft gelatin capsules, hard gelatin capsules, and powders. They can also be used for non-pharmaceutical items like confectionery, dietary supplements, and small hardware components.
Q: What are some key features of strip packing machines?
A: Features of strip packing machines often include high-speed operation, automatic feeding systems, precise dosing mechanisms, and the ability to work with various packaging materials such as aluminum foil and heat-sealable laminates. Many machines also offer options for customization, such as printing capabilities and adjustable strip lengths.
Q: How do automatic high-speed strip packaging machines improve manufacturing efficiency?
A: Automatic high-speed strip packaging machines significantly increase production output by rapidly forming, filling, and sealing strips. They can handle large volumes of products with minimal human intervention, reducing labor costs and the risk of contamination. These machines often feature multiple tracks, allowing for simultaneous packaging of different products or dosages.
Q: What types of packaging materials are used in strip packaging machines?
A: Strip packaging machines typically use heat-sealable materials such as aluminum foil, polymer films, or laminates. Double aluminum foil is commonly used for moisture-sensitive products, while other combinations of materials can be selected based on the specific barrier properties required for the packaged product.
Q: How do strip packaging machines contribute to product safety and quality control?
A: Strip packaging machines contribute to product safety by creating individually sealed pockets that protect against moisture, light, and contamination. Many machines incorporate quality control features such as vision systems to detect missing or damaged products, ensuring that only properly packaged items reach consumers. The individual strips also facilitate easier tracking and recall procedures if necessary.
Q: Are there semi-automatic options available for strip packaging?
A: Yes, semi-automatic strip packaging machines are available for businesses with lower production volumes or those requiring more flexibility in their packaging process. These machines typically require some manual intervention, such as product loading, but still offer benefits in terms of consistent packaging and improved efficiency compared to fully manual processes.
Q: How can I find a reliable supplier of strip packaging machines?
A: To find a reliable supplier of packaging machines, research reputable manufacturers and exporters in the packaging machinery industry. It’s advisable to contact multiple suppliers, compare features and pricing, and request demonstrations before making a decision. Look for suppliers who offer customization options and after-sales support to ensure the machine meets your specific needs.