With the competitive nature of the business industry, it is imperative to have your products packaged effectively and attractively, for this is the only way you will be able to keep customers satisfied and the business thriving. Shrink wrap machines seem to be one of the most appropriate solutions for businesses considering improving their packaging processes. This all-encompassing article looks at the main features and advantages of some of the best shrink-wrap machines available today and ensures that you are fully equipped to choose the right one for your packaging requirements. What we shall do here includes a review of several aspects of different models and industries as well as research of the new trends aimed at making shrink-wrapping machines even better than they are now. Whether you know nothing about shrink-wrap technology or want to change your old system, this article will teach you how to choose the best machine for your packaging purposes.
What is Shrink Wrap Equipment and How Does it Work?

Shrink wrap machinery includes many machines intended to wrap items in polymer film plastic foil efficiently. It is a two-step method wherein heat is applied to the film to get it to shrink onto the product, which then results in a detailed and attractive package. This equipment usually comprises of a tape that first cuts the film at the required length and seals it around the item, and after that a heat source, be it a heat tunnel or a heat gun, that shrinks the film. Such packages enable tight protection against dust, moistness, and other atmospheric conditions and make the product more attractive. Shrink wrap machines are widely used in many industries today since they are suitable for various types of products of different sizes and shapes and have become important packing components in contemporary times.
Understanding the Basics of Shrink Wrap
A good starting point would be to have a look at the original materials, mechanisms, and benefits of the shrink wrap process, and in this perspective, it is easy to comprehend the shrinks’ workings. Indeed, shrink wrap is defined as a polymer plastic film, such as polyolefin, PVC, and polyethylene, all of which have different characteristics that are valuable for different functions. Often, this choice is material dependent, be it clarity, strength, cost, or others.
In the short term, shrink wrapping starts with a product wrapping one’s product with the shrink film, which is first cut and then sealed with a sealer. Next, the sealed product is heated, whereby the film shrinks and molds over the product at a snug fit. The heating part can be done using heat tunnels or heat guns. This guarantees that the film fits well over the item behind it, providing tamper separateness and beautifying the product’s appearance.
Determining the efficiency of shrink-wrap machines involves several technical parameters. Some of the parameters include shrink temperature, which is normally set between 250°F and 400°F (approximately 121°C to 204°C), the thickness of the film gauge, which ranges from 16 to 100 microns, and speed of the machine, which varies from 30 to 200 packages in one minute depending on the model and complexity of the machine.
Shrinky plastic is used for many things, such as food, medicine, electronics, and items sold in stores, giving it a lot of room for use. This versatility, together with the added advantages of protection from foreign elements and better marketing, makes shrink wrapping a worthy packaging solution in modern times.
How Does a Shrink Wrap Machine Operate?
For those who understand how shrink-wrap machines work and operate, let me explain the whole sequence. First, the product is put in shrink film, and then a sealing device, usually an L-bar sealer, is utilized to cut and weld the film together. This process guarantees the complete coverage of the product to prepare it for the next stage. As per the sequence, once the sealing is done, the product is heat-treated through a hot air tunnel or blasted by a heat gun, activating the shrinking process. When heat is applied, the film moves and shrinks to hug the product tightly. All of these processes seem to be thought out sequentially, and they are suitable for different tasks while offering effective, tamper-proof containers and, at the same time, increasing the beauty of the product.
Key Components of Wrap Equipment
To satisfy the requirements associated with the wrap-covering equipment, I will attempt to outline the main points in a few words. In the first place, the sealing system is of utmost importance: It is normally an L-bar or rotary sealer and aims to make high-quality seals enclosing the products. This part of the system automatically cuts and seals the shrink film according to the size and complexity of the products. Then, the heat source heat tunnel or heat gun comes third. If it is a “tunnel” type of heat source, this component continuously delivers energy to the product’s outer surface. This allows the shrink film to be uniformly contracted over the product surface, ensuring a well-fitting case. Mechanized conveyor systems are essential in situations where shrink-wrapping processes are computerized to ensure products are integrated smoothly between different operations. Thus, integrating components ensures the system sustains its productivity while conferring on a certain amount of packaging quality standards.
Types of Shrink Wrap Machines Available
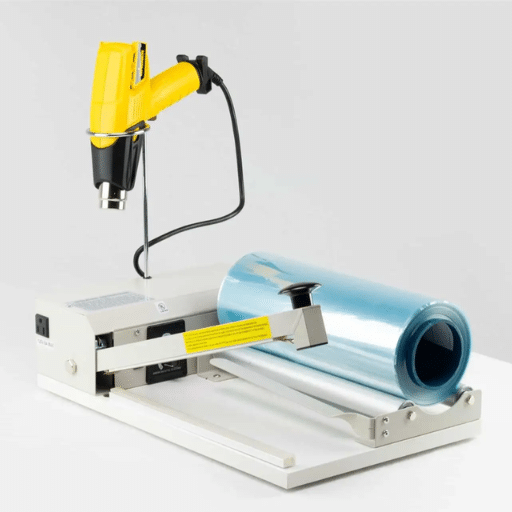
When considering shrink wrap machines, one cannot help but notice the abundant selection of these devices cater to diverse packaging requirements as well as the size of production. The basic forms of shrink wrap machines are L-Bar Sealers, which are well known for their speed in sealing and cutting the film; I-Bar Sealers, which are simple in design and inexpensive, thus suitable for low packaging usage or small businesses; and Shrink Tunnels which are the most suitable for mass production assembly lines due to their ability to contain heat for faster film shrinkage uniformly. There is no other separate machine for sealing and shrinking in the Chamber Machines, all are in one Chamber for easy access and space saving. Not all shrink wrappers operate with identical speeds and dimensions, moreover, there are some fully automated models available, enabling producers to pick a device meeting their particular operational needs and the demanded product parameters. The knowledge of these differences will assist in selecting the appropriate shrink-wrap system to provide the best possible packaging end results.
Exploring Semi-Automatic and Automatic Options
Differentiating between semi-automatic and automatic machines is crucial when using any side of the shrink wrap machine, including semi-dipers. Semi-automatic shrink-wrap machines offer a compromise on kitting and automation. Usually, an operator places the package and starts the packaging activity, providing the means to cope with a diverse range of product shapes and sizes while having low initial costs. This makes them well-suited for small to medium-sized operations where versatility and cost-effectiveness are priorities.
On the other hand, automatic shrink-wrap machines are efficient and fast in high-volume production environments, allowing consistent cycles with minimal human effort. There is no mechanical handling of the products with these covers, making the process faster. With these machines, there is very little manual handling of the products after they have been printed, making the processes fully automatic. They often include touchscreen controls, provide automatic handling of many different products, and allow for integration with systems, such as conveyors and labeling machines, which use different sorts of automation. So, despite being pricey, productivity and the amount of labor required make more economic sense in the long run. In the end, the selection between the two systems remains dictated by the amount of production envisaged and the budget available along with the specific needs and operations, which really stresses the fact that very specific tailor-made solutions need to be used in terms of packaging.
Choosing Between Chamber Shrink and Sleeve Shrink
Aspects that can help in the evaluation include packaging objectives, product sizes, and suitability of the materials used whenever one decides the ideal approach between chamber shrink and sleeve shrink systems. However, chamber shrink systems are more effective for low and medium production levels in providing a neat and flexible solution. This is achieved through shrinking films around the items, enclosing them in a chamber, and applying heat. Its popularity can be attributed to the uncomplicated process, allowing for the deformation of a wide variety of shapes while taking reasonable amounts of space and budget.
On the other hand, sleeve shrink processes proved helpful when dealing with large amounts as the end product, bottles that do not need to be completely sealed, and multipacks. Such systems contain a chain conveyor that moves the material through a shrink tunnel, which then applies heat to material that has been previously placed around the items. Such systems have the advantages of speed and precision and, hence, can be used for industrial purposes.
Technical Parameters to consider include:
- Speed: Chamber shrink systems generally operate at a lower throughput than sleeve shrink systems, which can handle thousands of units per hour.
- Film Type: Chamber systems typically use polyolefin or PVC films, while sleeve systems often use PET or PVC shrink sleeves.
- Product Size Range: Chamber shrink systems accommodate a broader range of product sizes without significant adjustments. Sleeve systems may require specific sleeve dimensions matched to product size.
- Heat Capacity: Due to continuous operation and larger tunnel requirements, sleeve systems might demand higher heat capacity and energy inputs.
Choosing the right system depends on aligning these parameters with your specific needs for production volume, product type, and budget.
The Role of L Sealers and Bar Sealers in Shrink Packaging
L Sealers are critical in shrink packaging as they ensure the product is well wrapped. They use the L sealing arm to cut, and fix film around the product in read for the heat tunnel where fitting of the film occurs. This equipment is appropriate for household packing of books, gift boxes, and food products. Technical parameters to consider when using L Sealers include:
- Sealing Speed: Varies but can typically seal between 15 to 30 packages per minute, depending on the model.
- Film Compatibility: Works well with polyolefin, PVC, and polypropylene films.
- Product Size Accommodation: Generally flexible, accommodating a wide range of dimensions due to adjustable settings.
Bar Sealers, however, is intended to emphasize solely the production of a reliably bonded seam extending whereby all sections of the product width are included by a straight sealing bar across the machine. They are simply described as being rigid and exact, which enables them to service heavy and bulky goods that require strong sealing. Their technical parameters are often:
- Sealing Width: Suitable for items up to several feet in width, depending on the machine’s capacity.
- Motor Efficiency: Often optimized to handle continuous or repetitive operations without overheating.
- Film Varieties: Compatible with heavier gauge films, enhancing durability for large packages.
Both systems contribute to the process in an additional way by improving the final appearance of a packaged product and ensuring professionalism. Choosing which one of the two to use is dictated by the operation’s particular requirements, including product dimensions, amount of packaging, and type of film.
How to Choose the Right Industrial Shrink Wrap Equipment?
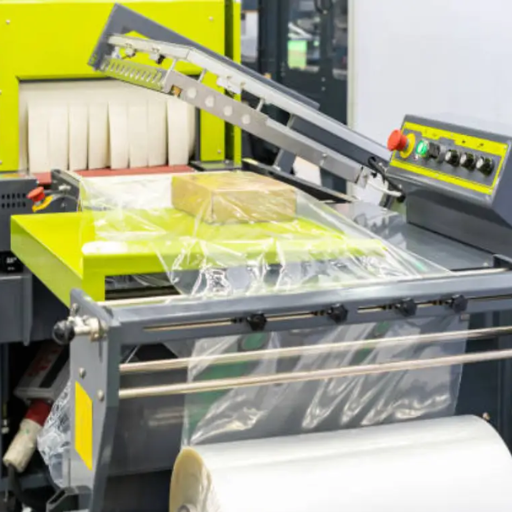
When purchasing the correct industrial shrink-wrap machinery, several aspects require careful consideration to develop the most effective and economical packaging option. First, start by analyzing your required production volume and the rate of production for it as this will determine whether you need semi-automatic or fully automatic machines. Consider the characteristics of the products that you are going to wrap, such as size, shape, and compatibility with the shrink films. Also, take into account the space available in your facility, such as the product chamber machines, which would require less floor space to operate shrink tunnels, which would require more space to set up. The financial aspect is also a major consideration in determining whether to go for increased automation or manual machines, which are less complex and less expensive. Lastly, it is also important to be aware of any changes in product upgrading or production requirements so that the equipment selected is changeable or expandable in the future. By addressing these aspects, there will be assurance that the chosen machine will not just fit the present work but also can give leeway to the company in terms of expansion.
Factors to Consider When Selecting Shrink Film
There are several parameters that I take into account when choosing a shrink film so that it fulfills the requirements of my packaging processes. In the first place, I check out the thickness and durability of the film since my goods require a degree of protection without being too costly. The optical properties of the film are also important, as I want the film to have a desirable and professional appearance when applied to my product. Also, I consider other shrinkage characteristics of the film, including shrink temperature and shrink ratio, because they will determine the equipment used and energy consumed. It is important to note that the remaining films should be compatible with my equipment to prevent awkward resizing or upgrading. Finally, the impact on the environment is another criterion of my choice of shrink films, hence opting for recyclable or biodegradable ones as much as practicable.
Importance of Heat Shrink and Shrink Wrap Heat
Over-emphasis on the need for heat shrink and shrink wrap heat in packaging can be avoided. Heat shrinking is a viable option in packaging, securing goods from tampering, and enhancing their aesthetics. It handles different items and contours by encasing and immobilizing them to minimize impact during movement. Furthermore, heat shrinking provides a key advantage of good visibility, which helps ensure that a product captures consumer attention when placed on retail shelves.
Shrink wrap heat, in contrast, pertains to the application of heat in the process of shrink wrapping. To be effective, heat also has to be controlled to set the film’s shrinking characteristics, resulting in a firm covering on whichever product it is applied on. Adequate heat application ensures that the required level of shrinkage is achieved and does not jeopardize the quality of the package or the unit itself. In addition, the appropriate application of shrink-wrapping heat can lower energy usage, which is good in terms of setting out objectives to use sustainable technologies. Hence, heat in the shrink-wrapping application may be viewed as an active and integral feature for ensuring the safety of goods and the operational performance of the package since the two are vital for modern packages.
Why High-Quality Shrink Wrap Matters
The application of shrink wrap in the packaging sector is important as it enhances the protection of the product and its presentation. High-quality materials reduce the likelihood of package failure during transit and storage as they ensure that seals are strong and durable. Strong seals made of high-quality materials provide clarity so consumers can easily see into the product’s pack, which often influences their buying behavior. In addition, high-quality shrink wrap film is effective because it leads to higher machine output with fewer adjustments and less downtime in wrapping operations. Important parameters for favorable outcomes are film thickness (usually between 50 to 100 microns, shrink temperature (typically between 150°C and 200°C), and shrink ratio (60 to 70 % shrinkage). These parameters should be optimized for a given item based on its material, form, and dimensions to provide adequate protection and a proper fit. Apart from preventing product loss through damage, investing in high-quality materials has the side benefit of enhancing brand perception and guarding against the degradation of the environment through the minimization of waste and energy loss.
Maintenance Tips for Shrink Wrap Machines
The performance and lifespan of shrink-wrap machines can be enhanced through proper maintenance. To start with, cleaning on a routine basis would be necessary to prevent the build-up of debris, dust, film residue, and other particles that could interfere with the machine’s proper functioning. Ensure regular checks and replacement of worn-out parts such as heating elements, blades, belts, and others to avoid loss of the machine’s operational time. Arrange scheduled maintenance of electrical connections and components to guarantee that the equipment will work effectively and safely. It is important to lubricate the machine’s moving components to ensure its effectiveness and reduce excessive wear. Additionally, you should apply the relevant adjustments to the sensors for temperature and tension controls. Following such maintenance procedures allows you to increase the equipment’s usable term and improve its consistency and functionality, which will jointly affect the continuous production cycles.
Regular Checks for Sealers and Film Sealers
I personally work on sealers and film sealers and give importance to a few things. First, before sealing, I ensure that the sealing bar is aligned and the pressure is set correctly to a level that the seals are complete; otherwise, the pouch will be weak. Then, I analyze the heat settings, ensuring that, in general, the temperature ranges between 150°C and above but never over-exposes polyethylene films, as accuracy is essential in maintaining the integrity of the seal without spoiling the film. I also ensure that the cutting mechanism is well calibrated and sharp to avoid jamming of the films, which could lead to waste materials. Sensor calibration is critical for controlling the sealing speed and maintaining equilibrium of the operation and, therefore, should be carried out regularly. Lastly, all electrical parts and wires should be inspected routinely to avoid any mishaps and ensure compliance with industry best practices.
Cleaning and Managing Heat Shrink Tunnels
Now, it is worth noting that heat shrink tunnels require routine cleaning and maintenance if they are to perform well and last long. But before cleaning, first make sure all the power sources are turned off. Cleaning should be done carefully, not using strong chemicals, focusing instead on soft, non-abrasive cleaning agents to clean the insides from debris, and focusing more on surfaces likely to collect material overspill, like the conveyor belt or heating components.
Technical Parameters for Effective Management:
- Temperature Range: Depending on the film type, maintain a consistent temperature of around 160°C to 200°C to ensure proper heat distribution without damaging the material.
- Conveyor Speed: Adjust the conveyor belt speed to align with the desired shrinkage effect, typically ranging from 20 to 35 feet per minute.
- Air Flow Optimization: Ensure that fans and air vents are clear and operational to promote uniform heat application.
Periodic inspection of the heating elements and conveyor system is necessary. Check for signs of wear or damage and replace such parts if necessary. These practices ought to promote effective functioning while extending the service lifespan of the heat-shrink tunnels.
Ensuring Longevity of Packaging Equipment
To increase the lifetime of the packaging equipment, I emphasize optimizing the necessary maintenance as recommended by the leading professional sources. Such routine maintenance functions of cleaning and examination aid in eliminating dirt while allowing for early detection and troubleshooting of problems before they get worse. I also carefully consider critical operational aspects such as temperature, conveyor revolutions, and pressure to enhance working conditions. Moreover, I ensure that I expand my knowledge on the internet regarding new developments and better practices concerning safety and effectiveness in using my packaging machines.
Common Issues with Shrink Wrap Equipment and Solutions

Even though shrink-wrapping equipment is quite efficient, it is not all perfect, as issues can still slow down productivity. For instance, unbalanced heating is a common problem that may lead to the product undergoing inconsistent shrinkage, hence destruction. To prevent this, ensure proper maintenance of the heating elements and sensors that require adjusting occasionally. Another common problem are film jams that can be attributed to misalignment or improper film tension. To resolve this, make it a point to look at the indicators occasionally and change tension settings for different films. Also, marking the seals due to their age or set temperatures could also be a problem, but all that is required is a thorough examination and replacement of any needed parts. Most importantly, timing can play a role in equipment errors or malfunctions alongside the event of button and software trigger chances overlapping, hence updating all software is highly necessary. Understanding and implementing these solutions will allow you to further smoothen your operations alongside the efficiency of the shrink wrap equipment.
Dealing with Shrink Film Problems
In order to deal with shrink film problems effectively, one needs to appreciate the context surrounding the problem and possible solutions as provided by experts. Low shrinkage is a common problem that is ironically caused by too much or too little temperature, together with the use of the wrong film type. This can be corrected by using the right type of film for the job and altering the heat settings appropriately. Film tearing is another common problem, and it results when the inadequate thickness of the film used is or the tension is set too low. The employment of thicker films and adjustments to the tension during the application of the film and heat setting generally prevent tearing. In addition to this, wrapping films can develop a bad static, cause misfeeds in the machine and be generally uncomfortable for the operator; anti static materials can prevent this from occurring. It remains to be noted that the information from leading industry sources emphasized the fact that proper maintenance routines, regular equipment calibrations, and active troubleshooting go a long way in overcoming these shrink film issues properly and with ease, and the net result is improved efficiency and effectiveness in the packaging process.
Troubleshooting Heat Tunnel Issues
When I am troubleshooting heat tunnel issues, I like to focus on certain crucial points. First, I check the correct temperature settings of all the packs as incorrect temperatures affect the film type being used, causing damage or uneven shrinking of the product. Then I check the conveyor speed as non-conformance with the heat setting may impact the shrink quality. Such a setting can fix risks and be a fair way of improving productivity. Another common issue is poor airflow, which results in uneven seals and wrinkles. To achieve the desired end state, the sealing and shrinking process must be optimally set towards high heat levels, high-pressure airflow, and appropriate time. As a grip-tightening mechanical assembly, I also replace the heating elements in case of excessive wear and tear so that forces acting on the contraction side stay efficient. In this way, I can further increase the performance of my heat tunnel, which will further guarantee efficient operations.
Innovative Trends in Shrink Packaging
The field of shrink packaging is progressing in a new direction with many new improvements enhancing efficiency and sustainability. One such improvement is the application of compostable and biodegradable plastic films, which meet the requirements of increasing environmentally friendly packaging options. Such films are designed to decompose faster than plastics with minimal environmental effect. Along with it, further improvements in automation and smart technologies, like AI-enhanced quality assurance mechanisms and IoT embedded systems, have also made it possible to maximize efficiency in production and packaging attributes. In addition, due to the development of capabilities in digital printing, manufacturers are ready to offer shrink-wrap films containing high-resolution graphics, thus increasing manufacturers’ branding opportunities. Adopting such remarkable trends complements environmental objectives and greatly improves the general efficiency and effectiveness of shrink-packaging processes.
Advancements in Automatic and Semi-Automatic Machines
Today, technological developments have led to the advancement of automatic and semi-automatic machines in shrink packaging. Take, for example, the shrink packaging machine’s more modular design features, which enhance maintenance, upgrades, and scaling as production requires. Specifically, these machines are, on a requirements basis, designed with adjustable speed settings from between 20 to 150 packs per minute to meet various packing requirements. The enhanced precision control systems used for packing ensure that the seal conditions are kept consistent. Common examples include maintaining the temperature control range between ±5% and ±1%. In addition, servo motors help stir movements smoothly and accurately, enhancing the operation of the whole machinery.
In addition, semi-automatic machines have adjustable conveyors and boxes that cater to cutters of specific heights and depths. Therefore, semi-automatic machines are free from the complete line replacement issue because all products vary in size. An intuitive touch-screen interface and a data acquisition system have become very popular among both machines. This improvement allows the plant operators to quickly change the parameters of the machine and reduce its idle downtime. Owing to these innovations, automatic and semi-automatic machines will always be among the most advanced technologies in shrink packages.
The Future of Industrial Shrink Technology
The industry’s shrinking technology will still be moving towards revolution with Innovative changes and sustainability themes. For starters, IoT (Internet of Things) will make shrink systems smarter, allowing real-time connection and communication that ensures data analysis and improves performance on the go. This, in turn, will increase the efficiency of the production lines, reducing waste and energy consumption. In second to last place, biodegradable and recycled shrink films have gained esteem because they are friendly to the ecology while meeting the shrink film performance. Lastly, robotics and AI will suffice to demand techno-advanced manipulations with a smaller workforce and greater efficiency, which will help minimize production costs. Adapting these technological shifts will allow the industry to keep pace with the times, thus remaining relevant to the new emerging threats and the ever-challenging opportunities.
References
Frequently Asked Questions (FAQ)
Q: What are the key features to consider when choosing a shrink wrap machine?
A: When selecting a shrink wrap machine, consider the type of packaging film it supports, whether it includes a heat shrink tunnel machine, the speed of operation, and whether it offers features like automatic side seal shrink capabilities. You might also want to look for features such as a film dispenser and compatibility with various packaging materials, such as PVC or POF film.
Q: How does an automatic l-type shrink wrap machine work?
A: An automatic l-type shrink wrap machine operates by automatically feeding the packaging film and product through a sealing area, where the film is cut and sealed around the item. The item then passes through a heat shrink packaging tunnel for a tight, professional finish. This type of machine is often used for high-speed, high-volume production lines.
Q: Can shrink-wrap machines handle different types of packaging film?
A: Yes, many shrink-wrap machines are designed to handle various types of packaging films, including POF and PVC. It’s important to verify that the machine you choose is compatible with the specific type of film you plan to use for your products.
Q: What is the advantage of using a machine heat shrink tunnel?
A: The advantage of using a machine heat shrink tunnel is that it provides consistent heat distribution, ensuring uniform shrinkage of the film around the product. This results in a clean, professional appearance and can efficiently accommodate a range of product sizes.
Q: Are there manual options available for smaller operations?
A: Manual shrink sealers are available for smaller operations or businesses requiring less frequent packaging. These machines are typically more affordable and suitable for lower volume needs.
Q: What safety precautions should be taken when operating shrink-wrap machines?
A: Safety precautions include training operators to use the machine correctly, keeping a safe distance from the heat source during operation, and regularly maintaining the equipment to prevent malfunctions. It’s also important to follow the manufacturer’s guidelines for safe use.
Q: How can the efficiency of a shrink wrap machine be optimized?
A: To optimize the efficiency of a shrink wrap machine, ensure that the machine is properly maintained and calibrated for the specific packaging film being used. Additionally, training staff on the efficient operation of the machine and regularly updating any software or hardware components can improve performance.
Q: What is the role of a film dispenser in a shrink wrap machine?
A: A film dispenser is an essential component of a shrink wrap machine. It holds and unwinds the packaging film. It ensures that the film is fed smoothly and evenly to the sealing area, which is crucial for achieving a professional and consistent shrink-wrap result.
Q: Can shrink-wrap machines be customized for specific packaging needs?
A: Yes, many manufacturers offer customization options to tailor shrink-wrap machines to specific packaging needs. This can include adjustments for different product sizes, film types, and production speeds. Contact us for more information on customization options.