Shrink packaging machines have integrated themselves into modern packaging lines, from the food and beverages sector to pharmaceuticals and consumer goods. These machines increase efficiency whilst simultaneously lowering production costs. The machines also increase the accuracy of packaging. Instead of basic covering, products are securely wrapped in heated plastic film, improving their presentation in retail stores and enhancing their protection. This text will focus on shrink-packaging machines, which improve the flow of production processes, decrease material waste, and boost operational productivity. The readers will gain valuable insight on the analysis of how packaging with these machines translates for various industries.
What are the key features of a shrink packaging machine?
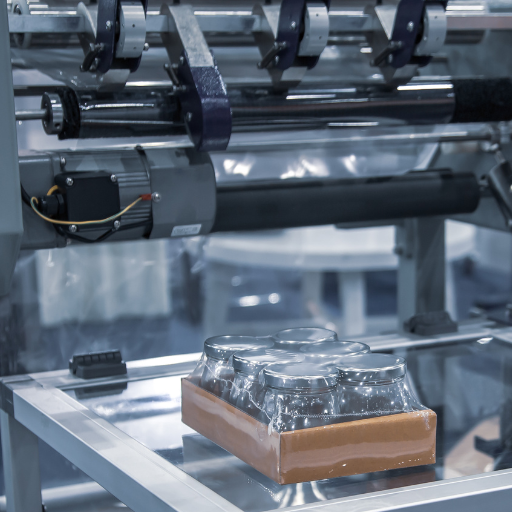
Key features of shrink packaging machines include precision temperature controls to guarantee the correct amount of heat is applied for shrinkage, adjustable conveyor speeds to manage different product sizes, and compatibility with various shrink films including PVC, polyolefin, and polyethylene. Advanced models often incorporate automated sealing systems for improved efficiency, integrated safety mechanisms to prevent overheating, and more user-friendly interfaces. These features together allow shrink packaging machines to function with minimal material and operational downtime while ensuring reliable high-quality shrink packaging.
Understanding heat shrink technology in packaging
Heat shrink technology in packaging is done by applying heat to a shrink film material in a controlled manner, thus making the film to contract and tightly conform to the product’s shape. The effectiveness of this process depends on several critical technical parameters:
- Temperature Range: Based on the type of shrink film a controlled temperature range of 100°C~200°C provides the optimal shrink reaction to PVC and Polyolefin films.
- Film Type: A common variety of the shrink films is PVC, polyolefin, and polyethylene which are chosen for durability, transparency, and puncture resistance among other application needs. Polyolefin, for example, is very common because of its wide application range and FDA approval for food packaging. Polyolefin is also commonly used because it has a shrink ratio between 40 and 60 percent.
- Conveyor Speed: Allowable adjustable conveyor speeds ranging between 10 and 120 feet per minute help manage different product sizes and production loads without affecting shrinkage quality.
- Sealing Method Automated systems seal L-sealers or side sealers, and some use continuous motion technology based on the output requirements of the production line. These methods are essential for achieving a seal that improves the product’s protection and visual appeal.
- Heat Tunnel Uniformity: The shrink tunnel must have even heat distribution to prevent inconsistencies such as uneven shrinkage or film wrinkling. Precise airflow systems provide this.
The precision of these technical parameters in shrink packaging technology combine an aesthetic design with high levels of protective qualities while minimizing unused film and maximizing throughput efficiency. These factors are relevant for packaging workflows in every industry.
Differences between Automatic and Manual Shrink Wrap Machines
Machines used for shrink wrapping automatically tend to be more efficient and consistent than manual machines since feeding of the film, sealing, and shrinking is automated. This makes these machines best suited for high-volume production lines where speed and accuracy are paramount. On the other hand, manual machines use a great deal of operator intervention so they are the best fit for small scale operations and ad hoc packaging requirements. Such machines also tend to be less expensive and easy to maintain. Automatic machines, however, improve throughput and reliability in an industrial setting while minimizing labor expenses and variability in operations.
The Importance of Shrink Tunnels During the Packaging Process
These tunnels also play a critical role in the process of packaging by providing a constant and regulated level of heat to tighten the film over the product. These machines help in accurately placing the film around the product so that heat can be evenly distributed and the packaging is done smoothly and with no wrinkles for a wide variety of shapes and sizes. Shrink tunnels increase the strength and the quality of the product’s packaging by increasing the effectiveness of film shrinking which makes them highly useful in regions with high population density. Thus, significant improvement can be made in the protection and appearance of the packaged products.
How does a shrink wrap machine improve packaging efficiency?
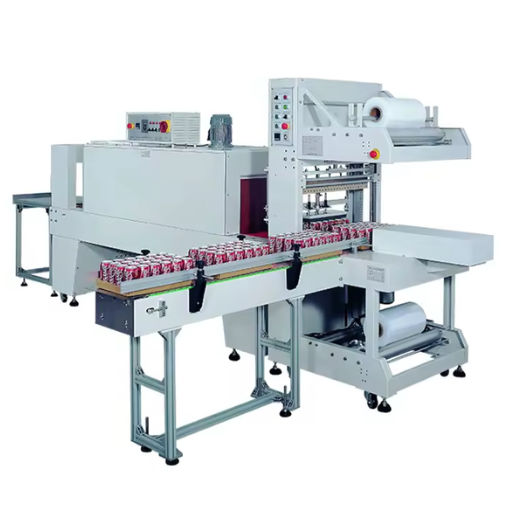
Shrink wrap machines have streamlined the process of packaging goods, reducing the requirement for human labor and ensuring uniformity in results. These machines apply film more accurately, reducing waste, increasing the speed of production, and creating seals that offer product protection. By automating critical steps in the packaging process, shrink wrap machines allow for much higher output volumes, greatly decreased operational expenses, and a lower probability of mistakes being made, which helps optimize the entire packaging workflow.
Reducing time taken to complete tasks with the application of automated shrink wrapping
The addition of advanced technology focus on pulling together multiple steps into one single system has allowed automated shrink wrapping to increase the speed with which the goods are produced. These systems wrap goods by preheating the film, applying film with constant tension, and sealing wrap with a lot of speed, all of which help in generating reliable wrapping. Many commercial machines designed for wrapping can operate at over 60 wraps every minute. Some industrial grade machines can work at even higher speeds. Specialized machines are also available to help streamline settings, which means less downtime while switching products. In addition, reduced human involvement increases the system’s reliability, as constant checks need to be performed to ensure a maximum possible output is produced while meeting the set standards of quality.
Reducing material waste through precise film control
Operating film tension through shrink films in shrink wrapping machines is critical for shrinking material waste. Current equipment incorporates sensors that automatically modify settings to dispense the correct quantity of film for every product manufactured, preventing overuse. In addition, advanced methods of tension control integrated into the machine allow for customized stretch settings which, when reached, do not result in film tears. Moreover, several systems can use weaker, more environmentally friendly films which are less expensive without losing strength, thus increasing material and cost efficacy.
Enhancing product protection and presentation
Shrinkwrapping systems have been developed to better protect a product and improve the product’s appearance by applying a seal that is difficult to tamper with and easy to break. This feature protects the product from environmental factors like moisture, dust, and contamination. Along with this, the shrink film which envelops the product is specially designed to fit the shape of the product, thus increasing the stability of the product during transport. Clear films can be used to showcase the product while still keeping the product intact. More technological advanced systems can be used with custom parameters to allow for wrapping that prevents roll over which results in nonclean but polished edges around the product and minimizes damages to brand reputation.
What types of shrink packaging machines are available for different production needs?
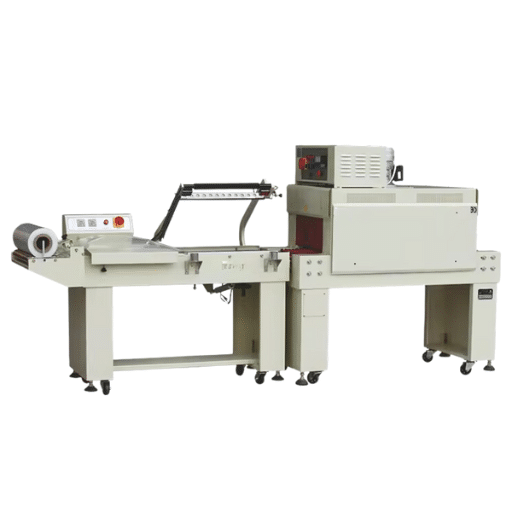
Packaging systems are available in different types to suit every level of production. L-bar sealers are suitable for low—to medium-volume operations due to their ability and ease of providing good seals. These machines are often used in conjunction with heat tunnels for even film sealing. For automatic shrink wrapping, an error occurred during generation. Please try again or contact support if it continues.
L-sealers and their uses in shrink wrapping
L-sealers are often used in the shrink wrapping industry for sealing operations. They are designed to melt seal packages with a single longitudinal seal. Because of their productivity and flexibility, they are mostly used in medium—to high-volume production lines. L-sealers enable shrink film to be wrapped around a product, sealing its edges, and a heat tunnel completes the operation by providing the necessary heat to shrink the film around the product so that it is tightly wrapped.
L-sealers are predominantly used in the food packaging industry, the electronics industry, and the printing industry. An L-sealer is preferred to other sealers because of its high efficiency level. The features that come automatic with advanced models such such as film feeding, waste trimming and conveyor integration, eliminate the need for manual labor which further enhances precision and efficiency. The most sophisticated models of L-sealers possess film-feeding automatic trimming and temperature-controlled sealing. Sealing bars can be adjusted from 1218 to 2432 and set to a temperature between polyolefin and PVC sealed films. All of these set settings make it possible for these L-sealers to be optimal for various industries.
Shrink Wrapping Chamber Machines
Small to mid-size businesses will use chamber-type shrink wrapping machines because they reduce the number of workspaces required to operate. These dual function machines enhance productivity and provide professional results. Users will find it extremely easy to use both polyolefin and PVC films and adjustable temperature chamber settings. With chambers featuring transparent lids, users can effortlessly monitor cosmetic, food, and promotional product packaging in real-time without the need for any advanced skills or elaborate setups.
Combination Shrink Packaging Systems for Comprehensive Solutions
Combination shrink packaging systems combine various processes into a single piece of equipment to enhance the packaging process’s accuracy and efficiency. These systems have incorporated the sealing followed by a shrinking approach, permitting easy use in high-output production processes. The systems effortlessly guarantee accurate and uniform shrinkage, ruining the wrapped product as little as possible while ensuring superior wrap durability. These systems are versatile as they accommodate a variety of shrink film and different shapes and sizes of products. They are widely used in fast-growing and precise industries like retail, pharmaceutical, and consumer electronics because they are very economical and do not consume much room.
How to choose the right shrink packaging machine for your production line?
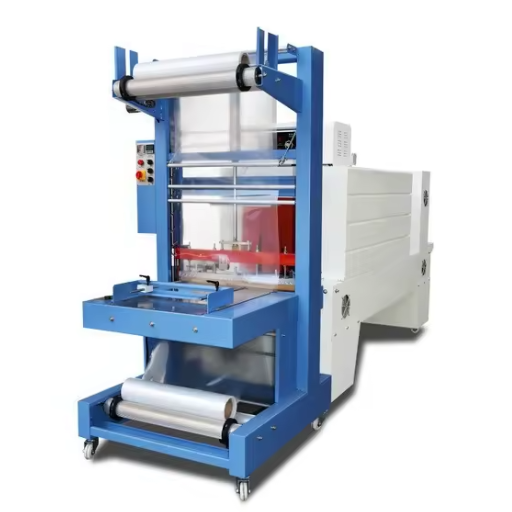
When choosing a shrink packaging machine, various factors need to be considered. Assessing your production volume will help you decide on a semi-automatic or fully automatic system. Analyze the machine’s capabilities in regards to the size, weight, and shape of the products you are planning on packaging. Also consider what type of shrink film you will be working with; Not all machines are suitable for use with all film materials like PVC and polyolefin. Additionally, consider the machine’s operational footprint in your facility and examine available resources such as budget and maintenance. Always look for features that ensure long-term reliability and efficiency, such as temperature control or interfaces that are more suitable for the user.
Assessing production volume and package size requirements
To evaluate production volume, first compute the number of packages to be completed hourly or daily. A fully automated shrink packaging machine is ideal with a production level higher than 30 packaged units a minute. Everything below 30 units can use a semi-automatic system. PPM or packages per minute is a standard rate of speed for machinery. It is often used in conjunction with production output in order to ensure maximum efficiency and avoid bottlenecks.
When reviewing package size, check the maximum film width, sealing dimensions, and tunnel size to ensure the most significant products within your range can fit into the machine. For example, products with unusual wave shapes or large approximations of up to 20 inches thick and 14 inches wide should be considered. Therefore, the sealing area and shrink tunnel need to be able to accommodate these measurements. More diminutive products would benefit from compact models that have reduced operational footprints. Both factors should be closely examined against the machine specifications to ensure compatibility and avoid consequences such as wearing or inconsistent wrapping results.
Looking at the two competing film types: Shrinkable PVC films and POF films
The difference between POF and PVC are the different emulsifiers, their performance, and the application range. PVC shrink film’s cost is low, and at the same time, its clarity is superb, and its high shrinkability makes it suitable for retail. But, it does emit dangerous fumes when heated and is less flexible, which can lead to it cracking at lower temperatures. Meanwhile, POF shrink film is tougher, eco-friendly, and FDA-approved for direct food contact. It possesses better elasticity and is not easy to tear making it suitable for oddly shaped items. Raw materials and end product needs like clarity, safety, and environment will dictate which films will be used.
Determining energy savings and improvements
Regarding energy efficiency, looking at the power use of the equipment in operation at work and on idle is essential. Unique features like programmable shut-off modes and energy-efficient motor designs can significantly cut down electricity spending over long periods. Additionally, efficient machine operations require regular maintenance. Risk management strategies such as lubrication of moving parts, replacing worn-out parts, and moving inspection of the heating elements can both save energy and help prolong the lifespan of the machines in service, cut back on emergency shutdown periods, planned and otherwise. Regular maintenance improves energy efficiency, but also assists with the reliability of the machines.
What are the advantages of integrating a shrink wrap machine into your packaging process?
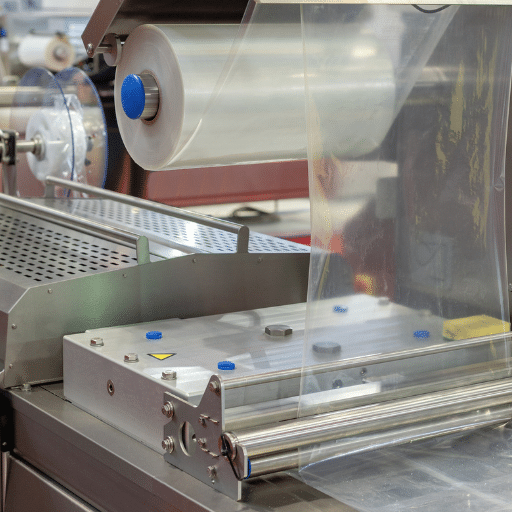
The convenience of reaching a seal and ensuring a dustproof, moisture-proof seal during storage and transportation is only made possible by a shrink-wrap machine. Applying a shrink wrap seal expands the aesthetic appeal of the packaging, providing a clean and polished look which increases customer satisfaction and perception of your business. In addition to that, automating the wrapping process increases the production speed and reduces the manual workforce required. As a result, larger margins of ROI are achieved over a span of time from reduced overall costs with an increase in productivity. Adoption of shrink wrapping as a primary form of product packaging also allows for versatility, as it can accommodate multiple sizes and types of products, which is a needed characteristic in a fast paced industry.
Modernizing the process with conveyor systems
The utilization of shrink wrap machines during packaging guarantees ease, security, and cost efficiency. This adaptable solution protects your products against the environment, increases automated wrapping productivity, and lowers material waste. Moreover, it allows for a diverse range of product sizes and smart packaging materials, making it ideal for streamlined operations.
Increasing product security and evidence of tampering
Shrink wrapping provides added security around a product as it provides a firm protective tamper seal. The film used is tough and ensures that any form of interference is evident, providing customers with assurance and trust in the brand. The process also protects goods from contamination, moisture damage, or external damage while in storage or during transit, reinforcing overall product integrity. This guarantees that the product remains safe from harm and is perfectly suitable for industries that need high quality evidence of tampering and protection. Practically all industries will benefit from this.
Increasing corporate reputation with branding in wrapping
Maintained design branding gaps is crucial for bolstering corporate identity and gaining clients’ trust. Having consistency in the logos, colors, and fonts, the business designs should have these elements to have increased recognition in all sites they are used. Also, using consistent shrink wraping ensures a professionally appealing outlook of products fosters confidence in the quality of what they stand for. Uniformity ensures improved shelf appearance, but powerful shrink wrap branding also increases trust, as it becomes easy to link the brand’s values and reputation with the package.
How do shrink packaging machines adapt to different industries and products?
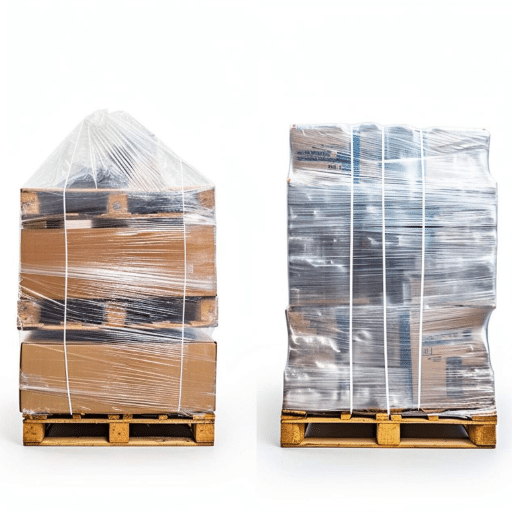
Shrink packaging machines are adaptive for various industries and products because they have configurable settings and modular designs that fit specific requirements. These machines consider product size, shape, and volume differences with adjustable sealing devices, temperature settings, and conveyor belts. In the food and beverage industry, these machines utilize FDA approved materials and seals to guarantee precautionary compliance. Likewise, in the electronics and pharmaceutical fields, products are packaged using sophisticated shrink-wrapping machines with anti-static or airtight seals to meet specific product needs. These features provide ease of use, but their flexibility is even more pronounced for differing types of shrink films which can be used for a variety of purposes.
Altering Shrink Wraps for the Food and Beverage Industry
Shrink wrapping in the food and beverage industry is modified to include product freshness, safety, and appealing presentation. This is achieved using food-grade shrink films that meet contamination and regulatory requirements. Modern sealing methods improve the strength and cleanliness of the sealed products, and adjustable temperature and speed control enable the machinery to accommodate different-sized products and volumes of food. In addition, clear and tough shrink films enhance branding and audience appeal while protecting the product during storage and transport.
Utilizing shrink sleeve technology in the context of consumer goods
Shrink sleeve technology allows for flexible and economical packaging of consumer products. The heat shrinkable plastics can be slipped over products of any shape or size to firmly hold the product, during which the sleeve will wrap around the product’s contour. In addition to this, the materials used in the packaging can be printed in high resolution, providing clear graphics and vibrant colors which increases shelf appeal. Furthermore, shrink sleeves are adaptable to a broad array of products such as bottles, jars, and containers, while also providing tamper-proof seals that guarantee the safety of consumers. This technology also allows for adopting sustainable packaging, as many shrink films today are designed to be recycled or made of material that is friendly to the environment.
Shrink Wrapping Systems for Bulk Items
Shrink Wrapping Systems for Bulk Items pertain to the use of durable plastic films that shrink on the application of heat to encapsulate oversized equipment, machinery, or goods. This procedure commonly employs high-density polyethylene or polyolefin films, which when heated, shrink tightly around the item, forming a weatherproof seal to protect the item from damage during transportation or storage. Modern shrink-wrapping systems include automated machines that can accomplish precise wrapping, increasing productivity and guaranteeing uniformity in large-scale operations. These systems are effectively implemented in many sectors, such as manufacturing, construction, and logistics, where there is a need for cost-effective protection and better handling of large or awkwardly shaped objects.
Reference sources
Frequently Asked Questions (FAQs)
Q: What is a shrink packaging machine and how does it work?
A: A shrink packaging machine is a piece of equipment used to wrap products in shrink film and then apply heat to create a tight, protective packaging. It typically consists of a sealer to enclose the product in film, and a heat shrink tunnel or heat gun to shrink the film around the item. This process is widely used for various packaging applications in industries such as food products, beverages, and consumer goods.
Q: What are the main types of shrink sealers available?
A: The main types of shrink sealers include L sealers, bar sealers, and automatic L sealers. L sealers are versatile and can handle a wide range of product sizes. Bar sealers are ideal for sealing bags and pouches. Automatic L sealers offer higher production speeds and are suitable for larger operations. Manual shrink sealers are also available for small businesses or low-volume applications.
Q: What is the difference between a heat gun and a heat shrink tunnel?
A: A heat gun is a handheld device used for applying heat to shrink wrap, suitable for small-scale operations or irregularly shaped products. A heat shrink tunnel, on the other hand, is a larger, more automated piece of equipment that products pass through on a conveyor belt. Heat tunnels offer more consistent and efficient shrinking for higher volume production lines.
Q: What are the advantages of using an all-in-one shrink wrapping machine?
A: An all-in-one shrink wrapping machine combines the sealing and shrinking processes in a single unit. These machines often include a film dispenser, sealing mechanism, and heat tunnel. The advantages include space savings, improved efficiency, and better coordination between the sealing and shrinking stages, resulting in a more streamlined packaging process.
Q: What types of film can be used with shrink packaging machines?
A: Shrink packaging machines can typically handle various types of packaging film, including PVC, POF (polyolefin), and PP (polypropylene) films. The choice of film depends on the product being packaged, environmental considerations, and specific application requirements. Some machines are designed to work with pre-made sleeves or bags, while others can create packages from roll stock film.
Q: How can a shrink packaging machine benefit a production line?
A: A shrink packaging machine can significantly improve a production line by increasing packaging speed and efficiency, reducing labor costs, and ensuring consistent package quality. Automated systems, such as those with automatic L sealers and conveyor belts, can handle high volumes of products with minimal human intervention. This leads to increased productivity and can help businesses meet growing demand or expand their operations.
Q: What features should I look for in a shrink packaging machine for food products?
A: When selecting a shrink packaging machine for food products, look for features such as stainless steel construction for easy cleaning and hygiene, adjustable temperature controls for different film types, and compatibility with food-grade packaging materials. Some machines offer additional features like gas flushing for extended shelf life or the ability to handle various packaging sizes for different food items.
Q: Are there specialized shrink packaging machines for unique applications like wine bottle capsules?
A: Yes, there are specialized shrink packaging machines designed for specific applications such as applying heat shrink capsules to wine bottles. These machines, often called wine capsule shrink machines or sleeve shrink machines, are tailored to handle the unique shape of wine bottles and apply precise heat to shrink the capsule or sleeve evenly around the bottle neck and top.