Polyvinyl chloride, commonly called PVC, is a widely used thermoplastic material known for its durability, cost efficiency, and versatility. However, despite its prevalence in various industries, PVC poses significant risks when processed through laser cutting. This blog aims to examine the hazards associated with laser cutting PVC, focusing on the chemical, environmental, and equipment-related dangers that arise during the process. By understanding these risks, readers will gain a deeper appreciation for why alternative materials or cutting methods should be considered when working with PVC.
What makes PVC unsuitable for laser cutting?
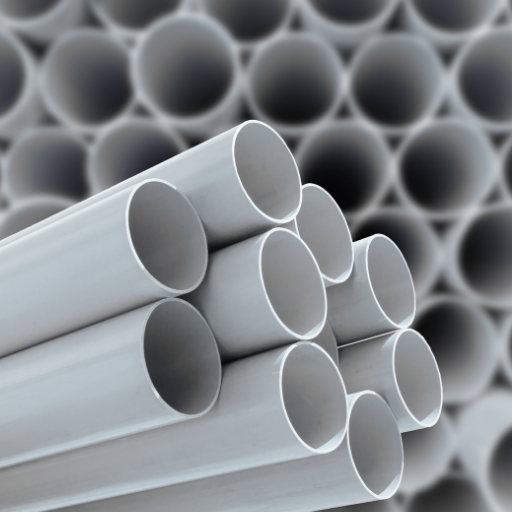
Polyvinyl chloride (PVC) is not recommended for laser cutting because it generates harmful byproducts when heated with a laser. During the cutting process, PVC releases hazardous chlorine gas and hydrochloric acid, which can injure the operators. These damaging substances can also erode the cutting tools over time which can lead to higher maintenance costs and system failure. The damage is not only structural, but the environment also suffers since the PVC residue from combustion adds to pollution. For these reasons, PVC’s chemical makeup renders it unsuitable for efficient and safe laser cutting.
Chemical composition of PVC and its reaction to laser
PVC, or polyvinyl chloride, is a thermoplastic plastic material comprising 57% chlorine from industrial salt and 43% carbon from hydrocarbons. When a laser is applied to it, the heat is so hot it breaks the polymer chains and releases Chlorine gas (Cl2) and Hydrogen Chloride (HCl). The chemical reaction is toxic and corrosive, making it detrimental to people and machines.
Further combustion of PVC will undoubtedly cause more hazards, adding to the danger of dioxins released from combustion. It is important to stress that laser cutting of PVC is dangerous, and one can understand this from the lack of focus on its use in the industry.
Toxic Fumes from Laser Cutting PVC
During the laser cutting of PVC, chlorine gas (Cl₂) and hydrogen chloride (HCl) fumes are released into the atmosphere. Chlorine is a bi-product of all polymerization reactions, HCl is produced when PVC is heated. Both of these chemicals are very toxic and can cause harm to human health and wellbeing. Chlorine, as an irritant on its own, is very capable of inflicting respiratory system damage, and HCl, on the other end, when meeting a moist environment, turns into Hydrochloric acid, which is very corrosive and harmful to humans as well as machinery. In addition to these, incomplete incineration also yields dioxins which are hazardous to health in many ways and can have prolonged repercussions. Considering these facts, people should avoid using laser cutting on PVC.
Dangers of Cutting PVC with Laser Equipment
Cutting PVC using a laser is dangerous to the laser equipment due to the byproducts produced during the process. PVC, when heated, emits harsh gases like hydrogen chloride which are capable of corroding parts of the laser system, such as lenses, mirrors, and even the ventilation ducts. Due to prolonged exposure, the corrosion may lead to degradation of performance, increase in maintenance expenses, and if it is left unchecked, reasons to worry about the irrevocable damage to the internal mechanisms of the equipment. Hence, the internal mechanisms and the equipment as a whole can be permanently damaged.
What are the specific risks of laser cutting PVC?
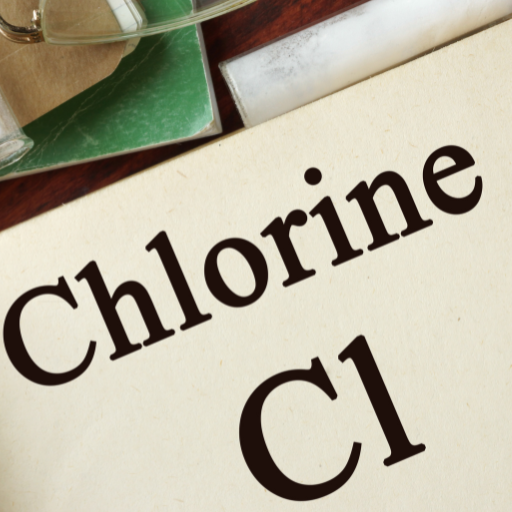
Cutting PVC with a laser has a number of unique disadvantages. For starters, laser cutting generates toxic fumes, such as hydrogen chloride and other chlorinated compounds, that are detrimental to the health of the operators. Such fumes require proper ventilation and filtration to make the workplace safe. Additionally, the fumes produced are corrosive and can destroy the internal parts of the laser machine, for example, the mirrors, lenses, and other metal components, which will increase the expenses on maintenance and repairs. Last but not least, the toxins produced from burning PVC can also introduce pollutants into the environment, which means that methods of disposal and handling have to be appropriately regulated.
Release of chlorine gas and hydrochloric acid
Laser cutting PVC cuts the material by a laser, which in turn causes thermal decomposition of the material, releasing chlorine gas (Cl2) and hydrochloric acid (HCl). Chlorine gas, for instance, is extremely toxic; however, the most hazardous feature of it is that is very reactive, meaning even in small doses it can be harmful to Health. Hydrochloric acid on the other hand is also a hazard as it is very corrosive and can inflict severe injuries to both man-made machinery and the human body parts. As such, such emissions make it mandatory to use advanced extraction systems with such filtration methods as activated carbon or chemical scrubbers to mitigate as many risks as possible.
From a technical perspective, hydrochloric acid has a boiling point of around 110 degrees Celsius and appears as a solution when it interacts with water vapor. If these byproducts are left unattended, they can damage inner parts of metal laser-cutting equipment. They can cause damage unless materials that can withstand being corroded are used or a protective coating is applied. Usually, when a system requires constant ventilation, the calculation for management of hazardous gasses is tailored in cubic feet per minute (CFM) according to the system’s capacity, and compliance is almost always met. Gas monitoring units and other protective equipment, as well as regular upkeep of the system, make working conditions safe and extend the life of the equipment.
Health risks for workers and onlookers
Workers and onlookers risk serious health hazards if proper control measures are not implemented. Inhalation of Hydrogen chloride (HCl) gas can lead to serious consequences, it can cause severe irritation in the throat and lungs, intense coughing, and choking; if someone continues to be exposed, it can lead to aggressive lung problems like chemical pneumonia. Additionally, contact with HCl gas can lead to skin burns, eye irritation, and in more aggressive cases, blindness. The longer a person is exposed to the HCl gas, the greater the risk of toxicity. To control these health risks, the use of PPE, adequate ventilation, and constant air quality monitoring are the primary steps that need to be taken.
Environmental concerns of PVC laser processing
The concern with polyvinyl chloride (PVC) laser processing focus on the problematic compounds released at high temperatures. PVC cutting with lasers produces hydrogen chloride (HCl) gas at high energies along with dioxins and furans which are also environmentally persistent and toxic. Dioxins and furans are examples of chlorinated organic compounds that are very harmful to both humans and the environment. They accumulate in the food chain and wreak havoc. Strong mitigation methods include using proper exhaust systems with advanced filtration systems like activated carbon or chemical scrubbers to capture emitted toxins and comply with the pollution control regulations. Further, using alternative materials or less aggressive cutting increases the ecological sustainability of PVC processing.
What are safe alternatives to laser cutting PVC?
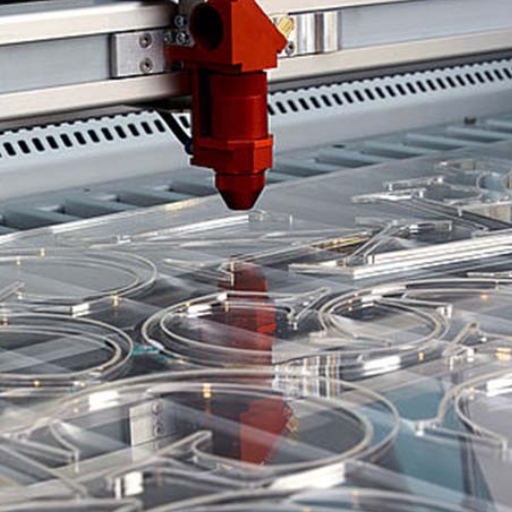
The safest methods for cutting PVC without a laser center around mechanical techniques and the use of alternative materials. A PVC cutter knife, router and saw do not emit any harmful gasses when used on PVC. These methods work on PVC through force rather than heat, so there us no toxic waste created like hydrogen chloride or dioxins. Furthermore, combustion products from laser cutting other polymers, such as polyethylene (PE), polypropylene (PP), or other chlorine-free polymers, are less harmful, so they can be used instead of PVC. Implementing these alternatives can lower the pollution and health hazards coming from PVC.
Which plastics can be cut with a laser?
- Acrylic (PMMA): Acrylic is one of the most famous materials for laser cutting. It is transparent and has great edge quality. Both types of acrylic—cast and extruded—are good, but cast acrylic usually produces better-quality edges.
- Polycarbonate (PC): Although thin polycarbonate plates do not laser cut as easily as acrylic, they can be cut in sections. Thicker pieces, like polycarbonate plates over one millimeter thick, can get discolored and lose edge quality when laser cut.
- Polyethylene Terephthalate Glycol (PETG): PETG is a versatile material suitable for laser cutting and engraving. Compared to PVC, it emits fewer toxic fumes and produces smooth cuts with minimal distortion, making it ideal for applications requiring clarity and strength.
- Wood-Filled Polymers: Aesthetically pleasing applications are increasingly made using composites that contain wood fibers and polymers like wood-filled acrylics because they are laser compatible. Although they are not as easy to cut as other materials, they feature unique added textures within them that allow for the material to be easily cut using laser systems.
- Nylon (Polyamide): Although not as widely used, nylon sheets can be thinned out and laser cut. Because nylon easily melts when exposed to heat, parameter adjustment needs to be done with care. However, if done properly, cutting nylon results in high-quality and highly precise outputs.
- Polystyrene (PS): The thinner forms of Polystyrene are exceptionally compatible with laser cutting and engraving. For intricate designs, a polystyrene cut is clean and low-melting compared to other thermoplastics.
Choosing the right material depends on the application’s requirements, thickness, and the required laser power. However, it is crucial to ensure ventilation is present whenever any plastic is being cut to manage fumes produced and safety.
Comparison of Acrylic and PVC When Laser Cutting Materials
The two materials differ significantly in laser cutting specialization based on their material characteristics and their response to thermal stress. As with cast acrylic, acrylic is one of the most amenable types of materials for laser cutting as it can vaporize easily. This ensures that the edges are smooth and polished without any additional processes. Additionally, acrylic provides very few fumes when cut which allows for easier handling when ventilation is appropriate. Recommended settings for laser cutting acrylic are a power of about 10-100 watts (depending on the thickness) and a cutting speed of approximately 10-20 millimeters per second.
On the other hand, PVC (polyvinyl chloride) is typically not practical for laser cutting because of the hazardous fumes it releases, which contains chlorine gas that can endanger both the operator and the laser cutting machine. Such fume exposure can be dangerous from a health perspective and can also corrode the machine’s components over a period. While it can be cut in principle, it will need specialized fume extraction and can most commonly be substituted by safer alternatives. Certain materials like PETG and polycarbonate can also be recommended as substitutes for laser cutting PVC for some applications that require the same characteristics. In conclusion, acrylic is the ideal material for laser cutting given the cleaner processing and finish.
Is PETG Suitable For Your Cutting Project?
Even with its limitations, PETG (polyethylene terephthalate glycol) is still a good alternative for laser cutting. In comparison to acrylic, PETG has excellent flexibility and impact resistance, and its overall toughness is also better. Therefore, it is moderately laser friendly. Because of this, it makes for a great option where robust components are needed. Unfortunately, PETG also tends to undergo slight edge crystallization or discoloration during cutting. This will require some level of post-processing for the end product to be more visually appealing.
When it comes to the optimal settings for cutting, a power setting of between 30 and 100 watts will do great, with the exact measurements depending on the thickness of the material you wish to cut. The ideal speed to cut is 12 to 20 millimeters per second, as this will ensure precision without guard against excessive melting. Also of note is an efficient fume extraction system. While the chemicals emitted while cutting are lesser than those emitted by PVC, they are still not ideal for the health of the worker or the equipment. Therefore, the fumes should be managed in to keep the operator safe.
Overall, while PETG can function as a viable alternative, its performance is often project-dependent, and it may not achieve the same level of polish as acrylic in the final outcome. Attempting to test and slow optimize required parameters will ensure PETG’s ability to work with specific applications.
How can PVC be safely cut and processed?
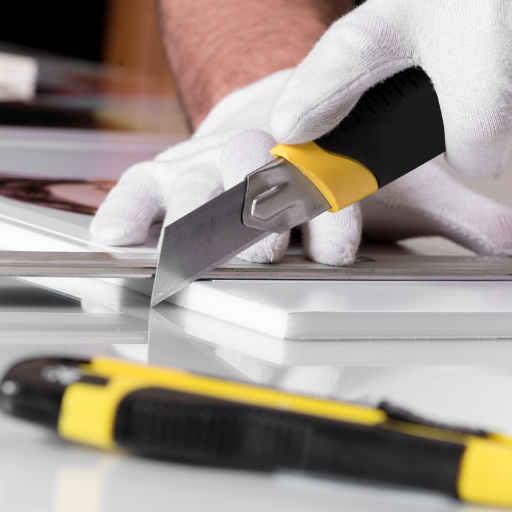
There are pertinent instructions that should be followed in cutting and processing PVC in order to minimize harmful emissions while getting precise output results. Recommended methods of achieving cuts on plastics include mechanical cutting such as sawing with table saws, jigsaws or CNC machines fitted with carbide-tipped blades. During cutting, sufficient ventilation or a dust collection system should be supplied for the non-toxic but irritating dust from PVC. However, non-toxic does not mean thermal cutting methods like laser cutting should be done; this is because the heating of PVC releases dangerous fumes that contain chlorine. One important note is that fume extraction systems should be available in work areas to protect both the health of the workers and the equipment during heat-based processing.
What mechanical cutting methods are useful for PVC?
When cutting PVC, powerful mechanical methods acheive the desired results. These include: Table saws, Circular saws, and Jigsaws. In all these implements a carbide toothed fine blade is best for smooth cuts. For circular saws: blades with over 60 teeth are optimal. The ideal cutting speed lies within 3000 to 6000 RPM. Anything below or above that range will result in chipping or melting of the material. Maintaining an even PVC feed rate is imperative. Overheating will melt the PVC, and lowering the feed rate will compromise cut precision. Considering intricate designs or repetitive patterns being cut by the CNC machine, this plastic bit cutting approach works due to its accuracy. It is important to remain vigilant during debris collection because dust extraction systems poses a hazard to a clear workspace.
Is it easier to cut PVC with a knife or CNC router?
A CNC knife is not as effective when compared to CNC routers. Make no mistake, knives are convenient, albeit for a different purpose; utility or precision knives can create custom designs on thinner sheets of PVC, but a router is a more practical option for complex shapes. Furthermore, knives are fully manual, making them far less efficient when working with thicker material. The decision ultimately depends upon a tradeoff between the material’s thickness and the design’s complexity.
Is it possible to cut PVC sheets with a waterjet cutter?
It is possible to cut PVC sheets with a waterjet cutter, though it may not be the most effective method due to specific material properties. Waterjet cutting offers clean and precise cuts without any heat that could melt or alter the shape of the PVC material, but it has to be careful with pressure setting. High pressure can damage the surface or crack the PVC material. Moreover, abrasive waterjet cutting is customarily banned because it could rub off material or over-scrape the surface of the PVC. Thin or sensitive PVC sheets are best handled with non-abrasive waterjets so that the material does not suffer undue strain and cutting is clean.
What precautions should be taken when working with PVC?
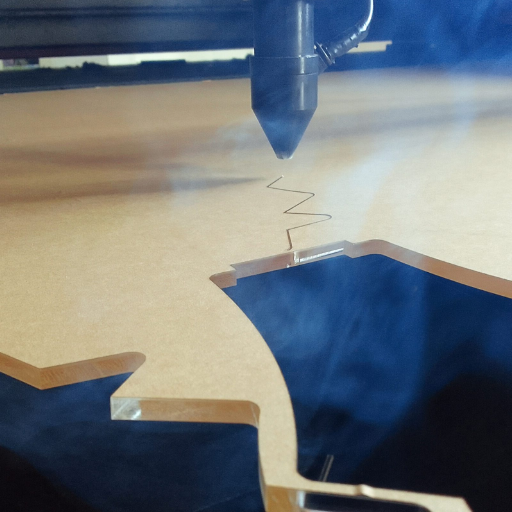
Prior to any work involving PVC, utmost caution must be exercised in handling the material as well as ensuring the area of work is free from any possible threats and hazards for achieving maximum productivity. When cutting or heating PVC, always ensure there is enough circulation of air as the fumes released can be toxic. Always put on gloves and safety goggles to lessen the impact of cuts or broken pieces and other harms. Tools must be set to the appropriate pressures and rotational speeds to avoid cracking and distortion of the material. Furthermore, never apply high temperatures as too much heat can ruin the PVC. Always dispose of scrap material in an environmentally friendly manner as dictated by locality regulations.
How to guarantee ventilation while dealing with PVC materials?
There are two ways to achieve adequate air circulation while dealing with PVC: working in areas that already have sufficient air circulation and using industrial ventilation systems like exhaust fans or even fume hoods. Other windows and doors must be opened when possible to allow air to flow. If one is working in an enclosed area, localized exhaust systems must be positioned close to the fumes to remove them effectively. Home and office air filtration systems claiming to capture dust and harmful gases can also be deployed. Lastly, all ventilation equipment must be serviced and cleaned regularly to perform optimally.
Which items of personal protective equipment are required for working with PVC?
While watching over PVC operations, I ensure that I have gloves constructed of materials that can withstand chemical damage. Eyes are always guarded with safety goggles, face shields, or protective masks to prevent contact with dust and stray chemicals. Where necessary, I also wear a respirator or mask that fits well, particularly when dust or fumes can be inhaled while cutting, heating, and working with the PVC. Finally, in order to reduce exposure, I usually work in long-sleeved clothing and work aprons, along with ensuring personal protection for every activity.
Is there a control measure for regulatory compliant PVC processing in the industry?
Yes, there is one. As with any chemical, there are certain regulations concerning the use of PVC. Examples of such rules include those that OSHA (Occupational Safety and Health Administration) or the EPA (Environmental Protection Agency) have initiated in the United States pertaining workplace safety and environmental controls of PVC use. Such regulations require appropriate workplace cuts such as controlling air flows into and out of the work area, supplying necessary PPE, and limiting dangerous chemicals such as Chloroethene. Moreover, other international regulatory requirements such as ISO give instructions regarding safe construction and dealing with materials as steps towards compliance and risk mitigation.
How does laser cutting compare to other PVC processing methods?

Compared to other ways of cutting PVC, like die cutting and mechanical cutting, laser cutting is significantly faster and more accurate. By cutting with a laser beam, even the most complex shapes can be designed with minute details and very little wasted material. Compared to other methods that involve tools, laser cutting does not use any physical contact which improves the finish and avoids any material deformation. There are many advantages with laser cutting, however, proper ventilation and extraction must be in place to avoid any health and environmental risks due to the disturbing chemicals, like hydrogen chloride, that are released when PVC is cut with a laser. The initial investment for the laser cutting equipment may be high, but it is more cost effective in the long run when dealing with intricate designs or custom pieces.
What are the pros and cons of laser cutting and mechanical cutting?
There are several differences when comparing laser cutting to mechanical cutting, especially in accuracy, efficiency, and how much they affect the material. Laser cutting offers exceptional precision, often achieving tolerances of ±0.1 mm. Because of this, it is perfect for detailed or intricate designs. Mechanical cutting lacks pizzazz, but it can work better with thicker or tougher materials, where laser cutting can be problematic. Moreover, because laser cutting is non-contact, it is able to produce smoother edges and minimal post-processing compared to mechanical cutting where edges can be rough or have burrs that need extra work.
With laser cutting, production time is faster with thin materials because it operates at higher speeds, which is more efficient. On the contrary, with simple cuts or bulk processing of the same shape, mechanical cutting proves to be more economical because of its low equipment and operational expenses. Nevertheless, laser cutting is highly adaptive and can deal with sophisticated shapes faster than any mechanical cutting system.
Aside from the greater expense, one significant disadvantage of laser cutting is the need for adequate ventilation systems when dealing with HVAC. The opposite is true with mechanical cutting: although there are no environmental issues, there may not be sufficient cutting quality for some industrial uses. In the end, one cannot decide between the two until all the parameters of the job such as type of material, accuracy required, and financial constraints are considered.
Pvc edge quality: comparison between traditional methods and laser cutting
Laser cutting offers much better precision and edge quality than older methods with hardly any effort spent on it. This type of laser is exact and concentrated, allowing for minimal warping of the materials. This makes intricate and detailed designs easier to achieve. While traditional methods of PVC cutting can handle non-complex tasks easier, they do struggle with more detailed patterns, leading to rougher ends. Furthermore, in comparison, laser cutting provides the benefit of reduced additional processes needed, unlike non-laser efficient cutting, which greatly relies on post-processing.
Cost comparison: alternatives to cutting lasering PVC
For laser cutting alternatives, the expenses incurred in waterjet cutting and CNC routing are more expensive than the rivals. But compared to the projects’ specifications, each of the methods have their own pros and cons. Equipment costs, operational efficiency, and material compatibility are important in determining the most effective method. Waterjet cutting is far more expensive due to the high cost of water and abrasives used during the project. Unlike CNC routing, this particular method has a set monthly fee, which eliminates fumes associated with PVC. CNC routing also serves as a viable solution to mechanical expenses and waste, since this method is best suited for thicker materials. A properly executed mechanical method is the fastest and most affordable technique, however, it is expensive in the long run. No matter the technique, the optimal cost will always come down to the scope of the project’s work and materials and how thick the materials were as well as the quality of work needed.
Reference sources
Frequently Asked Questions (FAQs)
Q: What is polyvinyl chloride (PVC) and why is it often used in manufacturing?
A: Polyvinyl chloride, commonly known as PVC, is a widely used synthetic plastic polymer. It’s often used in manufacturing due to its durability, low cost, and versatility. PVC is found in various applications, including pipes, electrical insulation, and vinyl records. It’s estimated that PVC accounts for a significant portion of the whole plastics market.
Q: Why is laser cutting and engraving PVC dangerous?
A: Laser cutting and engraving PVC is dangerous because when heated, PVC releases chlorine gas, which is highly toxic. Additionally, PVC can produce other harmful substances like hydrogen cyanide and halogen compounds when exposed to high temperatures. These emissions pose serious health risks and can also damage the laser cutter itself.
Q: Can I use a laser cutter to cut or engrave PVC pipe?
A: No, you should never cut or engrave PVC pipe with a laser cutter. The process of cutting PVC pipe with a laser releases toxic chlorine gas and can cause severe damage to both your health and the laser equipment. Instead, make use of alternative cutting methods like mechanical saws or specialized PVC pipe cutters.
Q: Is PVC flame-retardant, and does this affect its suitability for laser processing?
A: Yes, PVC is flame-retardant, which actually contributes to its unsuitability for laser processing. The flame-retardant properties of PVC mean it doesn’t combust easily, causing it to melt rather than vaporize cleanly when exposed to laser energy. This can result in poor cut quality and increased production of harmful fumes.
Q: What precautions should be taken if PVC must be processed near a laser cutter?
A: If PVC must be processed near a laser cutter, extreme caution should be exercised. Ensure proper ventilation measures are in place, use appropriate personal protective equipment, and maintain a safe distance between the PVC and the laser. However, it’s strongly advised to avoid processing PVC near laser equipment altogether to ensure the safety of operators and prevent damage to the machine.
Q: Are there any safe alternatives to PVC for laser cutting and engraving?
A: Yes, there are several safe alternatives to PVC for laser cutting and engraving. Materials like acrylic, wood, paper, and certain other plastics can be safely processed with lasers. Always consult your laser manufacturer’s guidelines or the material supplier to determine which materials are suitable for your specific laser cutter.
Q: How can I identify if a material contains PVC before attempting to laser cut or engrave it?
A: To identify if a material contains PVC, check the product specifications or look for recycling codes. PVC is often marked with the number “3” inside a recycling symbol. If you’re unsure, contact the material supplier or manufacturer for confirmation. When in doubt, it’s best to err on the side of caution and avoid laser processing the material.
Q: What should I do if I accidentally laser cut or engraved PVC?
A: If you accidentally laser cut or engraved PVC, immediately turn off the laser cutter and ventilate the area thoroughly. Evacuate the space and do not re-enter until it’s safe. Clean the laser cutter according to the manufacturer’s instructions, as residue can corrode machine components. It’s advisable to have the machine inspected by a professional to ensure no lasting damage has occurred.