The rise of laser cutters for metals has brought about a paradigm shift in metalworking by improving accuracy, efficiency as well as versatility. These tools are superior because they use focused laser beams for cutting metals with exceptional accuracy that exceeds traditional techniques. Apart from precision, metal laser cutters increase productivity, decrease material wastage, and provide the ability to design intricate and sophisticated pieces which make them fundamental in many sectors such as automotive and aerospace industries. This article analyzes the main advantages that metal laser cutting technology offers, and presents the new approach to modern metalworking technologies of laser cutting.
What are the advantages of using metal laser cutters over traditional methods?
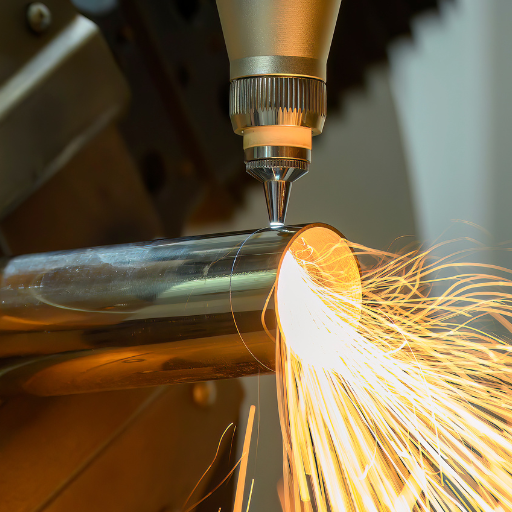
With metal laser cutters, the precision and accuracy of the traditional techniques is unmatched. Complex designs can be done with additional ease and sophistication. These machines save a lot of material with their optimal paths for cutting. This also raises the balance of manual work needed, further improving efficiency. Furthermore, these machines work with a variety of materials with different thicknesses so any application from a variety of industries can make use of these machines. Their productivity output is maximized without the compromise on quality, as their high speed of execution and low setup times help attract business.
In what ways does the laser cutter for metals elevate the precision of the cut?
Metal laser cutters enhance cutting precision and accuracy through focused laser beams that provide control during cutting. The kerf width of the cut/caliper width of the cut is equal to or lesser than 0.1 mm – 0.3 mm which is dependent on the material and thickness of the material. The narrower kerf width ensures Reduced material waste and ensures design intricacies. Additionally, the advanced CNC Computer Numerical Control systems are able to guide the laser to the precision of tolerance as tight as 0.05 mm which is remarkable. Furthermore, the precise cutting nature of laser creates no mechanical distortion ensuring that the material’s structure is not compromised. Features such as automated calibration and adaptive optics promote better beam focus and alignment which ensure quality in all levels of cutting complexity regardless of the detail that is present in the pattern. Combining all these factors, contributes to exceptional accuracy on metal laser cutting operations.
Which materials are processed by laser cutting machines?
- Steel: Both carbon steel and stainless steel can be cut using laser cutting machines. Smooth cuts can be performed with carbon steel using laser cutting machines as it is composition of steel type. On the other hand, stainless steel is also benefited on as the edges of stainless steel is exceptionally clean and formation of burrs is minimal with the use of nitrogen as assist gas.
- Aluminum: Cutting lasers remain effective for aluminum sheets and plates despite the material’s high reflectivity. Modern laser systems with high power fiber lasers combined with adaptive optics manage aluminum well, resulting in well-defined cuts with a smooth finish.
- Copper and Brass: These non-ferrous metals are laser cut due to their high reflectivity and thermal conductivity. The advanced optics on fiber lasers allow the cutting of thin and medium-thick sheets of copper and brass, producing very good edge finish.
- Titanium: Laser machining of titanium and its alloys is possible with great accuracy for parts that require good quality of cut such as in the aerospace, biomedical and industrial fields. To cut without oxidation, inert gases like argon or nitrogen are typically employed.
- Tool Steel: Tool steel is notoriously hard and durable which makes it a bear to deal with. That said, laser cutters tear through this steel without any problems. Unlike conventional tools, laser cutting machines can achieve precision cuts into complex patterns for supporting industrial tool-making.
- Alloy Metals: Assortment of alloys is cut with lasers, making it easy to manufacture complex pieces from compositionally broad nickel and chromium alloys. The agility needed to easily perform complex cuts is provided by lasers.
Those skills make laser cutting machines very useful across different industries in a multitude of metal oriented applications.
In what ways does the speed of laser cutting exceed that of traditional methods of metal cutting?
When laser technology is involved, processing speeds are significantly higher than those achieved with traditional techniques, especially when working with thin and moderately thick materials. The efficiency derives from the precision and energy density that a focused laser beam delivers, which greatly reduces resistance from the material and minimizes cutting time. Furthermore, laser devices often need little to no physical setup or changes in tools, which greatly increases productivity. Although more conventional techniques such as mechanical sawing or milling do have an advantage in some heavy-duty tasks, laser cutting saves more time than any other method when completing repetitive detailed jobs.
How do fiber laser cutters differ from CO2 laser cutters for metal work?
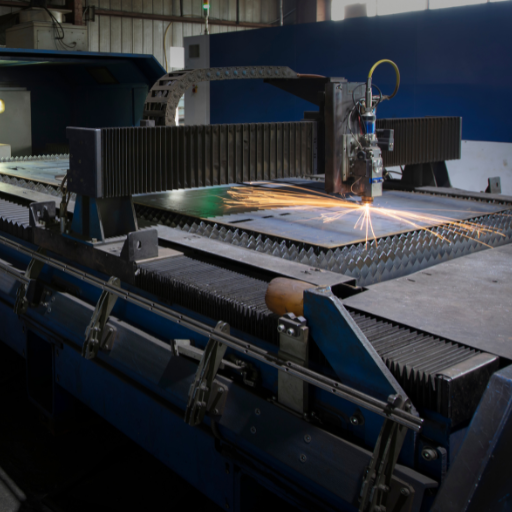
The core distinctions between fiber laser cutters and CO2 laser cutters, are in the method of laser generation, compatibility with various materials, and the overall efficiency. Fiber lasers can use a solid state configuration that has fiber optics embedded into it to help amplify the beam. As a result, they are especially efficient at cutting metals such as stainless steel, aluminum, and brass. CO2 lasers cut non-metal materials like wood or all types of plastics with high precision due to their gas based system. In addition, they can cut some metals, given that they are properly prepped beforehand.
Fiber lasers, as previously stated, can cut through metals with precision and can achieve high speeds while doing so. This is especially true for thin metals due to their lower wavelength achieving much higher absorption rates in the metal. Fiber lasers require less maintenance as well, since they do not have the gas components that the CO2 systems utilize. Furthermore, fiber laser cutters are more cost-effective and operationally economical. Meanwhile, CO2 lasers still have the versatility edge for mixed materials other than metalwork, which makes their use wider in specific fields.
What are the defining characteristics of fiber laser cutting machines?
Precision and efficiency best characterize fiber laser cutting machines. Fiber laser cutting machines use focused and concentrated beams with shorter wavelengths. As such, they are able to cut through metals at high speeds with minimal heat-induced distortion, which in turn allows for mass thermal efficiency, a hallmark of these machines. In addition to reduced expenditure from operational efficiency, low expenditure makes these machines appeal to many business users. Furthermore, these machines don’t contain gas components, allowing them to have longer lifespan, consume less energy, require almost no maintenance, and are compact. Consistent high quality make these machines extremely useful in manufacturing as they are able to cut through numerous other materials like aluminum, brass, or stainless steel, with a high degree of accuracy.
What are the optimal metals for fiber laser cutting?
Metals like aluminum, carbon steel, stainless steel, and brass can easily be processed using fiber laser cutting. Stainless steel yields superior results because of its strong ability to absorb the laser wavelength, allowing for clean edges and precise results. Carbon steel’s high cutting speed and ability to work with metals of different thicknesses make it a popular choice. With proper adjustments, aluminum, a highly reflective material, can be cut efficiently, making it great for lightweight and corrosion resistant applications. Fiber laser technology has made it possible to cut brass, all while maintaining high efficiency. Other materials like copper can be cut, but require careful adjustments of power settings and consideration of reflectivity.
In what ways does the laser power impact the cutting process of fiber lasers?
The setting of the laser directly corresponds with each variable associated with the fiber laser cutting process, meaning the results in speed, quality, or even efficiency will all differ depending on the setting. When the laser is set to a higher power, it is capable of cutting through thicker materials at a much faster rate. This is due to the high energy output ensuring faster material removal while simultaneously ensuring deeper penetration. For thin metals, lower power settings would be ideal. Utilizing low power settings results in a far cleaner and precise cut and minimizes the chances of distortion of the material.
To achieve the best results, specific parameters need to be met. For instance, laser power from 500W to 2kW is used when cutting thin aluminum or stainless steel sheets that are 6mm thick. When it comes to thicker metals, 20mm carbon steel for instance, power levels of 6kW and higher are recommended to ensure edge quality and cutting efficiency. Moreover, providing the right balance of power while considering the cutting speed, assist gas pressure, and position of focus helps to optimize performance, while lowering the waste of material as well as wear on the machine.
What factors should be considered when choosing a metal laser cutter?
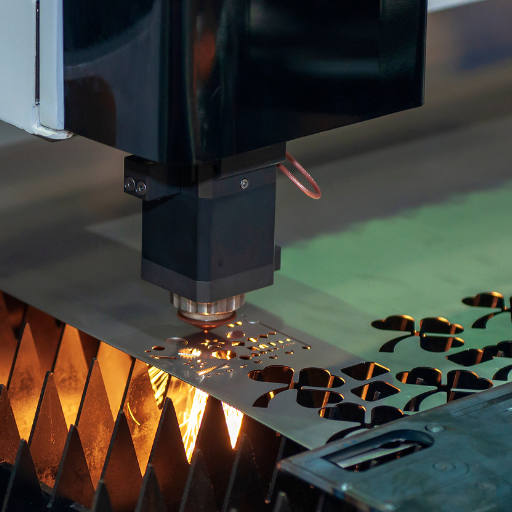
Evaluating your metal laser cutter of choice prompts a review of essential features. For instance, what kind of material and thickness do you intend to cut? This is critical as each machine can support a particular range of metal types and thicknesses. Consider the laser cutter’s power, the stronger the machine, the more adept it is at cutting thicker or harder metals. Precision is paramount as burns and other abrasions are common, especially in industries that work with fine tolerances. Productivity is also dependent on the met cutting speed, therefore, it is vital to choose a cutter that maintains high speeds without sacrificing the quality of the cut. Also, factors such as compatibility with specific devices, ease of use, maintenance, and spare part acquisition matter. All costs such as the upfront purchase money, operating expenditure, and the return make a huge impact on the decision.
What impact does the source of the laser have on the performance and versatility of the cut?
The laser source is a crucial element determining cutting efficiency and flexibility. While fiber lasers excel in efficiency, they can also precisely cut reflective metals like aluminum and copper, along with numerous other metal types. CO2 lasers are good for cutting thicker materials but are not as flexible as fiber lasers when it comes to processing reflective metals. Moreover, the beam quality and wavelength produced by the laser affect the cutting speed, edge quality, and unwanted thermal effects on the workpiece. Furthermore, the laser source’s maintenance and durability costs impact operational effectiveness and long-term performance. When the cutting task is made with specific parameters in mind, adequate sources of lasers will ensure the best quality of results.
What role does cutting speed play in metal laser cutting efficiency?
Cutting speed is proportional to overall efficiency in metal laser cutting. At higher cutting speeds, productivity improves significantly due to the decreased time taken to process each part; however, too fast cuts can cause defects due to excessively low laser power, high material thickness, poor edge quality, etc. The correct cutting speed also results in low energy consumption, reduced heat-affected zones, and ensures precise cuts that are clean and tailored to the specific applications.
How important is the laser head design in metal cutting machines?
The laser head design is the most critical part of metal-cutting machines because it determines the level of precision and efficiency the machine can achieve. A good laser head will target focus dramatically, improving cutting quality by ensuring the proper mainstream of aid gases. It will also allow for the targeting of different materials and thicknesses of the aid for proper focusing, thus greatly decreasing the chance of wear and maintenance over time. Additional design features, including adaptive optics and cooling, will improve the ability to quickly cut with low power while increasing the level of downtime, thus, the efficacy of the machine, therefore, making the laser head the most crucial component to achieve improved results.
Can metal laser cutters handle both cutting and engraving tasks?

Of course, metal laser cutters can both cut and engrave. The difference between cutting and engraving is that cutting penetrates and separates material using high-intensity laser energy while engraving etches text or designs onto the surface using lower energy levels. The capability to execute both functions simultaneously hinges on the machine’s power settings, precision, and adaptability. With more modern laser cutters, users can efficiently perform both functions, making them very versatile.
What kinds of engraving can be achieved with metal laser cutters?
- Deep Engraving: This method of engraving is accomplished by removing a large amount of material profiling undercut in a specific fashion to produce a three-dimensional aesthetic. Deep engraving is very common in industrial applications, especially for serial numbers, barcodes, or permanent labels on tools and machinery.
- Surface Engraving: Surface engraving is defined as etching fine details on the metal’s surface but focusing on the surface without penetrating too deep. This method is prevalent for creating decorative patterns, logos, or intricate designs in jewelry making and personalized gifts.
- Line Engraving: Line engraving is similar to surface engraving using a laser but instead etches fine continuous lines to give a precise outline. It is very common with text and is mostly used in technical or artistic surfaces.
- Photo Engraving: Advanced photo engraving allows laser metal cutting devices to embed or etch images onto metal surfaces. The laser intensity is then modulated to form gradients and textures, resulting in photorealistic engravings.
- Dot Peening or Stippling: Applying quick bursts of laser energy can create dotted patterns known as double peening or stippling. Regarding art, stippling is more aesthetically pleasing, but in industry, punctuated designs can improve surface texture grip.
- Annealing (Heat Marking): Annealing does not remove any material but alters the upper layer of the metal surface. This is usually done by heating the substrate to produce the desired changes. Stainless steel marking, for instance, is a common use of this method as it does not affect the structure of the material.
How does the engraving process differ from cutting on metal surfaces?
In engraving and cutting, both processes have specific differences regarding their aims, methods, and types of lasers to be used. The engraving process is done by decorating or altering the surface of the metal piece by marking, cutting, or etching so as to create a pattern, text, or a particular image. The engraving laser tool utilizes lower power levels than during cutting and higher to thoroughly remove or alter the top layer of the material while ensuring painstaking precision. The size of the spot, intensity of the laser, and amount of pulses marks how deep the engraving goes and how clear the engraving parts are.
Conversely, cutting involves the complete penetration of a workpiece that can be a solid metal. This action demands laser power to be raised considerably as well as the speeds to be increased when juxtaposed to engraving, as the goal is to vaporize or melt the material along the entire contour of the piece being cut out. Factors like laser focus, the kind of cutting gas used (for instance, oxygen and nitrogen), and power density greatly influence the smoothness of edges and the distortion caused by heat. Therefore, either process can be considered as having surface penetration. Still, in case of engraving, the surface is worked upon, and in the case of cutting, the material is both worked upon and separated. Each method is simple in principle, but is sophisticated when it comes to executing it.
What are the applications of metal laser cutting in various industries?
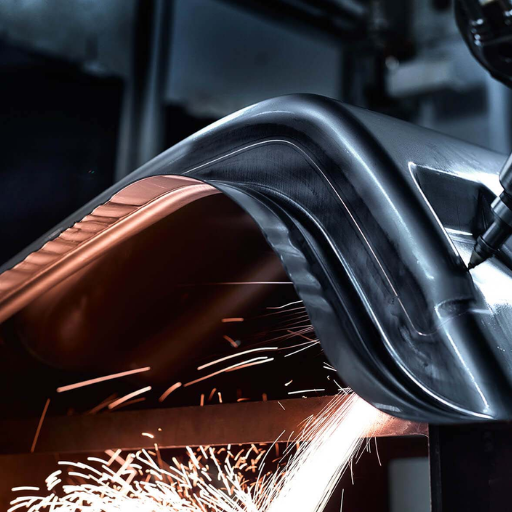
Due to its accuracy and adaptability, metal laser cutting can be used in various fields and industries. In the automotive industry, it is used for precision cutting of components that includes parts of the chassis, exhaust systems, and many custom-designed parts. In aerospace, laser cutting is used to machine complex shapes of lightweight structures made out of titanium and aluminum. Furthermore, the construction industry uses laser cutting to manufacture metal structures, architectural elements, and other precise fittings. The medical sector also uses laser cutting for precision-crafted surgical instruments, implants, and parts of complex devices. The information provided shows that all these industries benefit from optimizing their production with high quality results.
What role does a laser sheet metal cutter have with regards to manufacturing?
Beyond having precision over speed, sheet metal laser cutters are crucial to manufacturing because they are highly accurate and very flexible. Cutters can cut through metals at high speeds using laser beams without wasting much material. Such tools are extensively used in custom parts fabrication, prototyping, and even mass production due to the ease and quality of the finishes achieved. Besides cutting, these machines perform engraving and welding as well, which merges several tasks in a single unit to enhance productivity. Applying such tools not only increases the speed of manufacturing, but also eliminates material wastage. These machines can handle a variety of materials ranging from aluminum to steel.
What role do metal laser cutters play within the automotive industry?
Metal laser cutters play an indispensable role within the automotive industry due to their ability to perform cutting processes which are accurate and efficient. These lasers are used for body panels, complex internal parts, and even structural components that require accurate and quick cutting. Moreover, their use enables different materials, such as strong alloys, to be used, which are essential in increasing the car’s performance and efficiency. Introducing these devices in automated systems enhances the consistency, reduces wastage of materials, and facilitates mass production in response to the industry’s stringent requirements.
In what ways are hobbyists and small enterprises exploiting metal laser cutter technology?
Hobbyists and small enterprises exploit metal laser cutter technology due to its precision, variety, and ease of access. They can now produce intricate creations, specialized components, and even prototypes with high accuracy, which is great for crafting, jewelry, and personalized novelties. Alongside this, modern laser cutters made on-demand production available to operate on a small scale. The affordable prices enable professional-grade results, making innovative designs easier to implement and production processes more manageable.
What safety considerations are essential when operating a metal laser cutter?
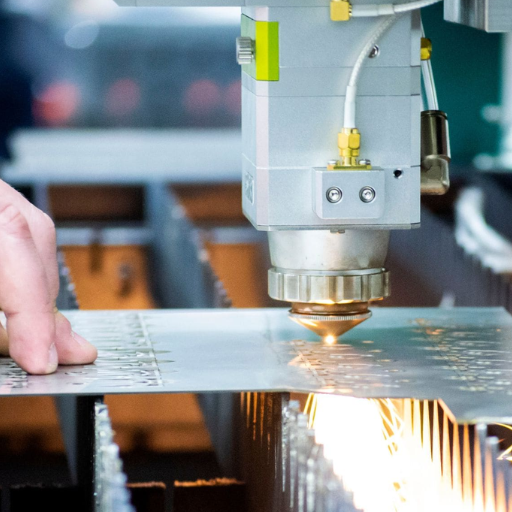
A working environment’s safety has to be maintained when using a laser cutter on metals such that no incidents take place. There has to be suitable exhaust systems in place to capture vapors, dust, and other particulates produced during cutting processes. Appropriate PPE, gloves, and safety goggles must always be worn by the operator to shield them from sharp objects, laser radiation emissions, and sparks. It is also important to inspect, maintain, and service every component within the machinery to prevent malfunctioning or improper operation. Lastly, proper use of the equipment is aligned to understanding the manual, the safety measures in place, how to adhere to materials powering the equipment, and all the conditions that hinder optimal use. After setting up the appropriate equipment, make sure that the emergency shut off controls are functional at all times. These emergency controls are to help in dealing with any incidents that may arise as fast as possible.
Which protective tools must be used to ensure a secure environment during laser metal cutting operations?
Tools and goggles that protect the eyes and allow the person to see without getting hurt from exploding reflections of light need to be worn. In addition, I routinely put on gloves that can handle high temperatures as a precaution against metal pieces and sparks. To keep my body from getting burned or hit from any exposed parts, a flame retardant jacket or apron is necessary. When the operator is exposed to fumes or particles produced during the cutting process, proper respiratory protection, such as a mask or a respirator, needs to be used. All PPE must be in good condition and certified which is a key requirement to ensuring safety.
How should the work area be set up for safe metal laser cutting operations?
For adequate metal laser cutting procedure safety, the workspace should be systematically arranged alongside incorporating relevant safety measures. The area must be monitored for cross ventilation to remove fumes and particulates suctioned out. Safety covers or barrier laser gates should be used to limit the scope of the laser beam and shield the employees; fire extinguishers should also be available within close range, while combustible materials should also be eliminated in the area. Personnel must prepare an empty and firmly held place for the lasing apparatus where all the electrical wires are plugged in and the earth connection checks out. Personal Protective Equipment (PPE) should be worn everywhere – goggles with laser protective filter winning at a wavelength of the specific laser must be in place. Periodical servicing of the cutter and instruction of the operators is equally important for efficient workspace organization and safety consideration.
Reference sources
Frequently Asked Questions (FAQs)
Q: What is a metal laser cutting machine and how does it work?
A: A metal laser cutting machine is a powerful tool that uses a focused laser beam to cut through various types of metal sheets. The laser, typically a fiber laser or diode laser, heats the material to its melting point, vaporizing it and creating a clean, precise cut. The cutting head moves along a programmed path, guided by CNC (Computer Numerical Control) technology, allowing for accurate and complex cutting work on materials such as stainless steel, mild steel, and aluminum.
Q: What are the main benefits of using a metal laser cutter compared to traditional cutting methods?
A: Metal laser cutters offer numerous advantages over traditional cutting methods. They provide higher precision, faster cutting speeds, and the ability to cut complex designs. Laser cutting also results in a higher quality of cut with minimal material waste. Additionally, it can significantly increase productivity and reduce labor costs, as the laser head automatically follows the programmed cutting path. This technology is particularly effective for cutting thin sheet metal and can handle a wide range of metal types.
Q: What types of metals can be cut using a laser cutting machine?
A: Metal laser cutting machines are capable of cutting a wide range of metals, including stainless steel, mild steel, aluminum, copper, brass, and titanium. The effectiveness of the cut depends on the power range of the laser and the thickness of the material. Fiber laser cutting machines are particularly effective for cutting reflective metals like copper and aluminum, while CO2 lasers are often used for non-metals and some metals.
Q: How does the laser cutting process affect the quality of the cut metal?
A: The laser cutting process typically results in high-quality cuts with smooth edges and minimal heat-affected zones. The focused laser beam vaporizes the material during the cutting process, leaving a clean, precise cut with little to no burring. This reduces the need for secondary finishing operations, saving time and resources in metal fabrication projects. The quality of the cut can be further optimized by adjusting parameters such as laser power, cutting speed, and gas assist type.
Q: What is the difference between 2D and 3D laser cutting machines?
A: 2D laser cutting machines are designed to cut flat sheet metal and are the most common type used in industry. They move the cutting head in two dimensions (X and Y) across the material surface. 3D laser cutting machines, on the other hand, can move the cutting head or the workpiece in three dimensions (X, Y, and Z), allowing for cutting of three-dimensional objects or adding depth to cuts. While 2D machines are more prevalent for standard metal cutting work, 3D machines offer additional flexibility for more complex projects.
Q: Can metal laser cutters be used for engraving as well as cutting?
A: Yes, many metal laser cutting machines are versatile enough to perform both cutting and engraving tasks. By adjusting the power and focus of the laser, these machines can engrave designs or text onto the metal surface without cutting through the material. This dual functionality makes laser systems highly valuable for a range of applications, from industrial manufacturing to artistic metalwork.
Q: How does the power range of a laser cutter affect its cutting capabilities?
A: The power range of a laser cutter directly impacts its cutting capabilities. Higher-powered lasers can cut through thicker materials and at faster speeds. For example, a 2kW fiber laser can typically cut through mild steel up to 15mm thick, while a 6kW laser can handle thicknesses up to 25mm. The power range also affects the range of materials that can be cut effectively. When choosing a laser cutter, it’s important to consider the types and thicknesses of materials you’ll be working with to ensure the machine has sufficient power for your needs.
Q: How can using a metal laser cutter increase productivity in a manufacturing setting?
A: Metal laser cutters can significantly increase productivity in manufacturing by offering faster cutting speeds, reduced setup times, and the ability to quickly switch between different cutting jobs. The CNC-controlled cutting process allows for continuous operation with minimal operator intervention, reducing labor costs. Additionally, the precision of laser cutting often eliminates or reduces the need for secondary finishing operations, further speeding up the production process. The ability to nest parts efficiently on metal sheets also helps to maximize material usage and reduce waste, contributing to overall productivity gains.