Laser marking is a highly versatile technology used across numerous industries for applications ranging from product identification to industrial manufacturing. This process involves using focused laser beams to etch, engrave, or otherwise mark materials with precision and durability. The technology’s adaptability allows it to be applied to various materials, including metals, plastics, ceramics, and more. This article explores the various types of laser marking technologies, providing a detailed overview of their mechanisms, advantages, and typical use cases. By understanding these methods, industry professionals can select the most suitable laser marking solution to ensure high efficiency, accuracy, and long-lasting results for their specific needs.
What are the main types of laser marking technologies?
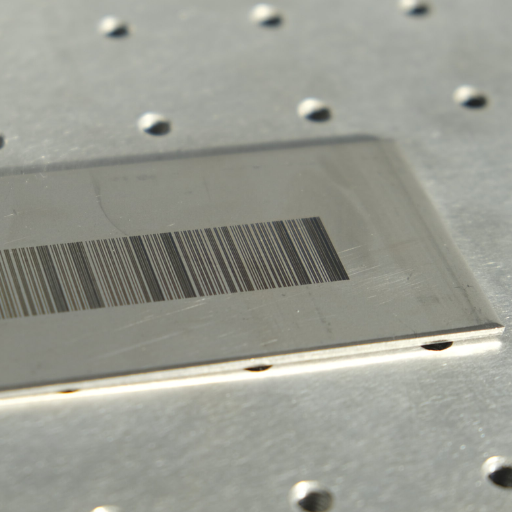
There are four primary types of laser marking technologies. Each marking technology is appropriate for particular materials and applications. Laser engraving is a marking technology that removes material to achieve deep, clear marks. It is frequently applied to logos and serial numbers. Laser etching creates marks by melting the material’s top layer, which raises the soft materials’ markings such as plastics. Laser annealing applies localized heating to change the material’s color and is often used on metals because it does not disturb the surface integrity. Finally, laser ablation is a marking technology that removes paint and anodization from the surface of metals to reveal the base layer. This method is suitable for contrast marking.
Fiber laser marking: The versatile powerhouse
Fiber laser marking is undoubtedly easily adaptable to a wide array of materials, from metal and plastic to ceramics. This technology is based on utilizing a laser beam with a wavelength of the order of 1064 nm that delivers high power and is focused to a tiny area. It can easily penetrate the metallic surfaces and be used for marking with excellent precision while ensuring durability. Some of the key technical indicators are power output, which for varying applications is between 20W to 100W, and beam quality measured by the M² factor, where high precision zones is close to 1. Fiber lasers are fitted with an air-cooled system, which allows them to operate efficiently while requiring minimum maintenance. In high throughput facilities, marking is done at speeds up to 7000 mm/s, narrowing the time window for processes and operations. Different industries utilize the technology for product marking, barcoding, compliance marking, and many more, where quality and durability come first. Further, the system’s life span and energy consumption make it ideal for use in varying production settings.
CO2 laser marking: Great for non-metal materials
CO2 laser marking systems for non-metallic materials are very effective because of their longer wavelength of 10.6 µm, which is suited for absorption by organic compounds. These systems are efficient with marking wood, glass, paper, plastics, textiles, and ceramics. The technical parameters are laser power output, which is usually between 10W to 150W and the material’s required depth or speed of marking. The spot size controlled by lenses makes it possible to control the line accuracy and marking density. CO2 lasers have galvo scanning heads that mark at high speeds, between 5000 to 10,000 mm/s, which is ideal for mass marking. The systems are air or water cooled depending on the power levels which creates stability and longer operational hours. These lasers are unmatched in creating clear, permanent marks, making them invaluable in the packaging, engraving, and aesthetic branding industries, which are highly sensitive to raw material compatibility.
UV laser marking: Fit for heat-sensitive substrates
A unique aspect of UV laser marking is that it operates with a wavelength of approximately 355 nm, which gives it low thermal energy and a high degree of precision in accuracy. UV lasers are especially suited to marking heat-sensitive substrates like plastic, glass, silicon wafers, and to some extent, even alloys. Because the marking is performed with a photochemical reaction instead of a heat source, deformation or damage to the substrate is impossible. Output power from 3W to 20W is sufficient for electronics labeling, medical device marking, and even branding with intricated details. Non-invasive high-quality markings are essential in numerous industries, and this low-power laser does just that.
How do different laser marking techniques compare?

Different types of lasers differ in their marking methods based on precision, speed, the materials used, and their heat effect. Fiber lasers are the best for metals as they are efficient and durable. In industrial identification, fiber lasers leave high-contrast and permanent marks which are ideal. CO2 lasers are the best when marking materials other than metals, such as wood, glass, and ceramics, as they are highly versatile. UV lasers utilize a short wavelength, providing the best focus depth while having low heat output. This allows delicate or heat-sensitive materials, like certain plastics and electronics, to be marked or cut. While fiber lasers are the best of each grade for tough applications, CO2 and UV lasers serve specific material requirements, delivering an ideal combination of precision and relative ease in many industries.
Laser engraving vs. laser etching: Understanding the differences
Both laser engraving and laser etching are techniques that use lasers to alter materials, but they greatly differ in process, use, and other technicalities. In laser engraving, a section of the surface of a material is taken out, resulting in deep and lasting marks. Laser engraving marks have a depth of about 0.1 mm to 0.5 mm. Compared to the other methods of marking, laser engraving requires more significant power. Depending on the substrate, markingable laser power tends to be over 20W. More durable marks are needed for applications like serial numbers or logos on metals and plastics, therefore this method is best suited.
On the other hand, laser cutting does change the material’s surface, but in a way that does not deeply remove the material; instead, it melts and expands the surface. This method is often done at lower power level, roughly around ten to twenty watts. The power level is lower because it only needs to modify the material’s surface. Compared to engraving, etching processes are faster and perfectly suited for sensitive materials requiring high contrast marking, including, coated metals and ceramics.
Marking metals and ceramics with high precision and detail is perfectly suited for laser etching, while laser engraving is perfect for heat-resistant materials which require strong marks. The long-lasting marks made with laser engraving are created using heavy machinery while light machinery provides the precise marks needed with laser etching. The selection of the method depends on thermal resistance of the material and its durability requirements.
Marking With Cold Vs Heat: Advantages and Disadvantages
Cold and heat-based marking differ in their method and purpose. Cold marking does not rely on heat to make an impression on the subsurface. It is ideal for delicate surfaces such as plastics and composites due to its high accuracy and guarantee that no damage will be caused to the substrate. Despite these advantages, its limitations stem from the fact that there is shallow aggression or depth penetration compared to heat-based methods.
Heat-based marking, however, is a technique that uses heat to change the material, which in turn provides more life and durability. This method is appropriate for strong materials, such as metals and harder plastics, which need mechanical strength and resistance to wear. On the other hand, ease of thermal deformation limits its use on sensitive or lightweight materials. The selection of one method over another is based on the particular features of the material, design needs, and operational limitations for the case at hand.
Color marking: Enhancing color for laser marked products
With laser technology, color marking permits the addition of bright eyes, pleasing high contrast colors on different materials that are made by fashioning their surfaces to their preferred grade. This process typically has specification changes in laser parameters such as laser light’s wavelength, pulse width, and energy value to produce oxidation and or other structural alterations to the surface of a material. The result of these modifications is multiple colors on the item, which are important to functional and aesthetic items produced by a consumer’s goods or personalization and even branding activities. The process is usually done on metals like stainless steel and titanium, but can also be fine-tuned for other types of substrates. With the proper setting of laser equipment, it is possible to reduce the effect of laser light on the article’s surface skin without reducing the item’s durability and, at the same time, achieving long-lasting color.
Which industries benefit from specific laser marking types?
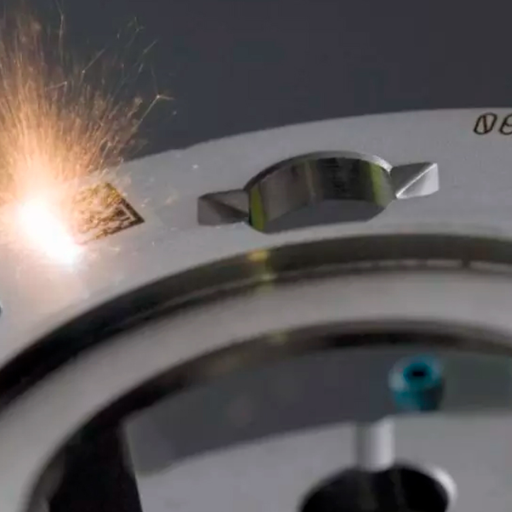
Marking using a laser entails specific techniques for different applications, and for the medical sector, the methods of choice are laser engraving and annealing. This ensures that surgical instruments and implants are marked with a durable and precise trace that allows for compliance with stringent traceability provisions. Laser marking technology also serves the automotive sector, which marks VIN codes, component idents, and brands that can endure harsh environmental conditions. On the other hand, the electronics and semiconductor industry processes use laser etching for micro-sized codes and identification of circuit boards for its high speed and noninvasive processing of sensitive equipment. These industry-focused illustrations present the flexibility and accuracy of modern laser marking technologies.
Metal fabrication: Use of fiber lasers in metal fabrication.
Fiber lasers have proven to be central in metal fabrication because of the exactness, speed, and efficiency it provides. With fiber lasers, cuts and designs of complicated structures can be done with thorough accuracy, less material wastage, and are easier to create. These lasers are most effective on stainless steel, foil, aluminum, and titanium because of their precision. Stated above are some of the main characteristics of fiber laser systems. Power output is ranging from 500W to over 10kW. The second is beam quality, which is assessed via M² value, guaranteeing marking or cutting to a specific standard miles away from poor performance. These systems additionally tend to have high energy efficiency, often operating at 25-30% efficiency which helps cut operational expenses. In addition, fiber lasers have a further advantage over traditional CO2 lasers because they are easier to maintain and have high uptime, optimal durability, and reduced maintenance cost due to having a solid design. Because of these reasons, they are widely used when fabricating parts in aerospace, automotive, and construction industries which demand high accuracy and quality standards.
Electronics: UV Laser Marking Delicate Components Designation
UV laser marking is a distinct, non-contact, and non-thermal means of marking that is best suited for delicate electronic parts. These lasers operate within ultraviolet wavelengths of the nanometer order and achieve minimal marking with little impact because of the very low heat produced, thus eliminating the potential for the components being marked to be damaged or distorted. This technique is very accurate and can reproduce small and delicate markings on boards, microelectronics, and other small-sized electronic components. UV laser systems provide high resolution and contrast marking required for industrial traceability and identification. They can also be used for a wide range of materials, such as plastics, ceramics, and coated metals, which are common in today’s electronics manufacturing.
Automotive: Permanent marking solutions for part identification
The automotive industry relies on traceability, quality assurance, and meeting regulations and standards. Like with other industries, automotive marking requirements vary in scope. Accordingly, Fiber laser marking systems are optimal for the automaker industry as they provide high contrast and durable markings on plastic and metal. The markings include but are not limited to serial numbers, barcodes, and identifiers. These markers can endure extreme temperatures, abrasives, and chemicals. Laser marking technology increases the accuracy and speed of production stages which helps to streamline processes, minimizes waste, and maintains parallelism in components. Furthermore, this siethod helps to address the increasing need of coding VINs and other parts for authentication as it helps eliminate counterfeiting or piracy of essential materials in the supply chain.
What materials can be processed with different laser marking systems?
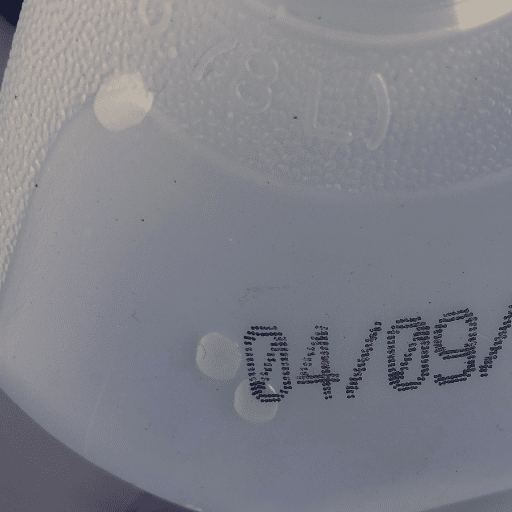
The flexibility of laser marking systems allows processing to be done on a lot of different materials, making them ideal for different industries. Fiber laser systems guarantee metal marking for stainless steel, aluminum, and titanium with high precision and longevity. Depending on the required mark contrast, CO2 and fiber lasers are suitable for marking plastics such as ABS, polycarbonate, and acrylic. Certain laser types, including CO2, which mark organic and brittle materials, can also process ceramics, glass, and wood. All materials differ in the required laser configuration and marking speed, precision, and readability; therefore, every material has a specific requirement that ensures the system’s reliability in different applications.
Metals: Processes performed with fiber and YAG lasers
Fiber lasers are proficient in marking metals because of the precise and permanent, high-contrast marks created by the fiber laser. They are specially used for engravings, etching, and annealing stainless steel, aluminum, and copper. YAG lasers are also appreciated for processing metals’ deep engraving surfaces, altering the material heat-affected zone, and providing good results for detailed and challenging industrial works. Both types of lasers guarantee the accuracy and endurance of the marks made and the performance proves beneficial for various industrial applications.
Plastics: CO2 and UV Laser Applications
CO2 lasers are good in marking plastics because they use long wavelength lasers that interact with organic materials and engrave or cut material with minimal damage. Marking with CO2 lasers find use in acrylic, polycarbonate, and polyethylene. In contrast, UV lasers work at shorter wavelengths, utilizing a “cold marking” technique with very low heat-affected zones. This capability allows UV lasers to be used in sensitive plastics such as medical polymers and electronic-grade devices requiring high precision and detail. In general, both technologies are effective but can be tailored to the specific type of plastic and its intended use.
Glass and Ceramics: Detailed Focus on Specialized Laser Techniques for Marking
Specialized methods are needed to play laser marks on glass and ceramics to achieve precision while maintaining material integrity. UV and CO2 lasers are used for glass since they engrave high contrast marks without producing cracks or undesirable surface stress. Smooth, high contrast marking is achievable with UV lasers, and it outperforms in applications that require intricacy or fine design because the high thermal impact is reduced with short wavelengths. Fiber lasers are becoming more popular for ceramics because they provide deep and rugged engravings that are fit for decoration and industrial work. The structure and beauty of the material can be preserved by careful calibration of intensity and speed of the lasers.
How to choose the right laser marking machine for your needs?
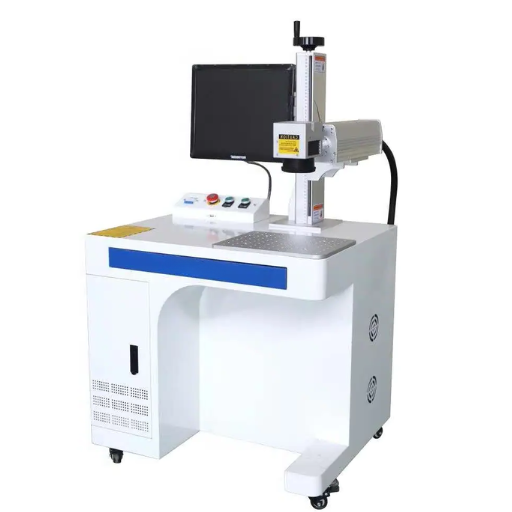
The selection of an appropriate laser marking device varies with the type of laser it can operate with, engraving requirements, and the specific application. Determine the material being marked first (metal, plastic, glass, etc.) and then determine which laser works with it; fiber and CO2 for metal, plastic, and glass, and UV for precise delicate measurement. Determine power output, marking speed, and whether they fit the production volume. Also, consider the machine’s capabilities, maintenance requirements, and financing options. These steps ensure that the company’s decisions are strategic and sustainable.
Evaluating the suitability of materials and the specific marking criteria
When considering material compatibility, it is critical to know the properties of the substrate that will be marked, along with the laser type with which it will be marked. Fiber lasers are tremendously effective for engraving metals such as stainless steel, aluminum, and titanium because of their capability to drill on hard surfaces while sustaining precise detail and accuracy. CO2 lasers rather excel in wood, leather, basic organic materials, and acrylics where their wavelength can conveniently be utilized for clean and precise markings. Sensitive or delicate substrates, for instance, glass or some selected plastics, are best marked with a UV lasers because they operate with low thermal effect, posing little risk of distorting the material.
The technical parameters that ought to be considered include the laser’s wavelength and power output because these have a bearing on the material processing capabilities that will be achieved. Fiber lasers operate with a 1064 nm wavelength, effectively marking metals and hard plastics. CO2 lasers, on the other hand, usually work with 10.6 µm and maintain the same efficiency on other non-metallic materials. UV lasers work on 355 nm and can micro-mark on low heat impactful materials. It is also equally important to change the optimal working parameters, that is pulse frequency and marking speed, for maximum efficiency for the intended purpose.
Comparing Laser Power and Speed for Optimal Performance
In comparing optimization with laser power and speed, focus is placed on parameters balance based on material and outcome needed. Higher laser power permits faster processing of material and deeper engravings or inscriptions but runs the risk of overheating delicate materials. On the contrary, lower power settings are useful for finer details on heat-sensitive substrates, albeit at a reduced production rate. The marking speed directly impacts precision; too slow speeds detract from production output, and faster speeds perform shallow engravings that lower accuracy. Both parameters need to be tuned together to achieve maximum efficiency and quality for specific applications.
Evaluating Software Features and Integration Capabilities
When evaluating software features and integration capabilities, flexibility, compatibility and functionality are deemphasized. The software must support multiple file formats and have design tools that permit precision and customization. Integrating with systems such as CAD or ERP without much difficulty is equally crucial for seamless efficient workflows. For adequate performance and reliability in the application, advanced features such as real-time monitoring, user-programmable parameter settings, and robust error diagnostics are critical.
What are the latest advancements in laser marking technology?

Technological advancements in laser marking today are directed toward increasing accuracy, speed, and the range of usable materials and industries. Innovations are indulging the use of ultrafast femtoliter marking systems, which detail and minimize stressed material by reducing the size of the heat-affected zone. Developments in fiber laser systems have also increased energy and durability, making them more suitable for the industrial level. Integrated IoT and AI functionalities enable monitoring, predictive maintenance, and adaptive optimization in real time, reducing interference to workflows and boosting efficiency. Their combination helps meet the marking requirements within more sophisticated manufacturing systems.
High-speed marking with ultrafast laser systems
Systems that utilize ultrafast lasers operate rapidly thanks to their femtosecond to picosecond pulse width range. Such pulses mark with minimal thermal, material distortion or damage, even when marking metals, plastics or ceramics. Additionally, these systems are super scalable in their processing speed, making them ideal for industrial use in high throughput production. Other fields, such as electronics, aerospace, or medical devices, benefit from the sub-micron precision detailing these lasers give. Ultrafast laser systems optimally satisfy modern marking requirements due to their relative operational cost savings coupled with high speed and accuracy.
Innovations in Multi-Color Laser Marking
The innovations in laser marking of multi-color capabilities have created a new paradigm in obtaining sharp, vibrant marks on a wide range of materials. Innovations stem from laser parameter manipulation, like controlling the laser’s wavelength, pulse duration, and repetition rate to trigger specific surface interactions. These reactions generate colors via oxidation, phase shift, or laser induced periodic surface structuring (LIPSS). This ability enables the industry to permanently fixed markings of any color without pigments or additives in a non-toxic and environmentally friendly manner. Uses include but are not limited to, consumer goods, marketing, and Production tooling, adding value to both visual and practical purposes.
Miniaturization of laser marking equipment
The expansion in laser marking systems across different industries is most likely due to advancements in laser technology, optical engineering, and the efficient miniaturization of components. Modern systems are now equipped with fiber lasers and diode-pumped solid state lasers, which offer superior energy efficiency, reduced heating, and require less space, as compared to older systems. Furthermore, substantial improvements in servicing cooling systems and power supplies have enabled laser markers’ equipment to be built smaller in size while improving their overall performance. These sophisticated systems can now be fitted into confined spaces, boosting their utility in the broader array of industries and applications.
Reference sources
Frequently Asked Questions (FAQs)
Q: What are the different types of laser marking machines?
A: There are several types of laser marking machines, including fiber laser markers, CO2 laser markers, UV laser markers, and green laser markers. Each type is ideal for different marking applications and materials. Fiber laser markers are versatile and commonly used for metal marking, while CO2 lasers are better suited for organic materials like wood and plastic.
Q: What is the difference between laser marking, laser etching, and laser engraving?
A: Laser marking is a surface-level process that creates high-contrast marks without significant material removal. Laser etching involves slight material removal to create raised marks. Laser engraving is a deeper process that removes more material to create deep, permanent marks. The main difference lies in the depth and amount of material removed during the laser process.
Q: What types of materials can be processed with laser marking?
A: Laser marking can be applied to a wide range of materials, including metals, plastics, ceramics, glass, and some organic materials. The choice of laser type depends on the material being marked. For example, fiber laser markers are excellent for metals, while CO2 lasers work well with organic materials and some plastics.
Q: What is dark marking in laser processing?
A: Dark marking is a laser marking technique that creates high-contrast, dark marks on metal surfaces without removing material. This process, also known as “cold marking,” is achieved by using specific laser parameters to alter the surface structure of the metal, resulting in a dark appearance. It’s commonly used for part marking in industries requiring durable, corrosion-resistant marks.
Q: How do fiber laser markers differ from other types of laser machines?
A: Fiber laser markers are known for their versatility, efficiency, and ability to mark a wide range of materials, especially metals. They offer high-speed marking, excellent beam quality, and low maintenance requirements. Unlike CO2 lasers, fiber lasers can mark bare metals directly and produce finer details. They are also more energy-efficient compared to other laser types.
Q: What are the five types of laser marking processes?
A: The five main types of laser marking processes are: 1) Annealing, which creates color changes through heat treatment, 2) Engraving, which removes material to create deep marks, 3) Etching, which creates raised marks through shallow material removal, 4) Foaming, which creates raised marks on plastics, and 5) Ablation, which removes surface layers to reveal a contrasting underlayer.
Q: What advantages do industry-leading laser marking systems offer?
A: Industry-leading laser marking systems offer several advantages, including high precision, fast processing speeds, and the ability to mark complex designs. They often feature advanced software for easy operation, integration capabilities with production lines, and the flexibility to mark various materials. These systems also provide consistent, high-quality marks that are durable and resistant to wear.
Q: What types of marking applications are best suited for laser technology?
A: Laser technology is ideal for various marking applications, including product identification, serialization, barcoding, QR code marking, logo engraving, and decorative marking. It’s particularly well-suited for industries requiring permanent, high-precision marks such as automotive, aerospace, electronics, medical devices, and jewelry manufacturing. Laser marking is also excellent for traceability purposes in quality control and supply chain management.