The combination of art and technology comes to life through laser etching machines. From professionals to hobbyists, everyone can benefit from engraving tools. These machines allow the integration of art and creativity by incorporating refined and sophisticated designs on wood, acrylic, glass, and metal. This guide is meant to assist you in understanding the fundamentals of laser etching technology. In particular, we’ll explore its functionalities, evaluate its necessary features, and analyze its capabilities. Furthermore, we will offer guidance on selecting the most suitable machine, ensuring it performs at its best, and effectively utilizing laser engraving’s boundless creative potential. Ultimately, this article intends to transform your approach to engraving by providing you with advanced techniques and methodologies at the tips of your fingers.
What is a laser etching machine and how does it work?
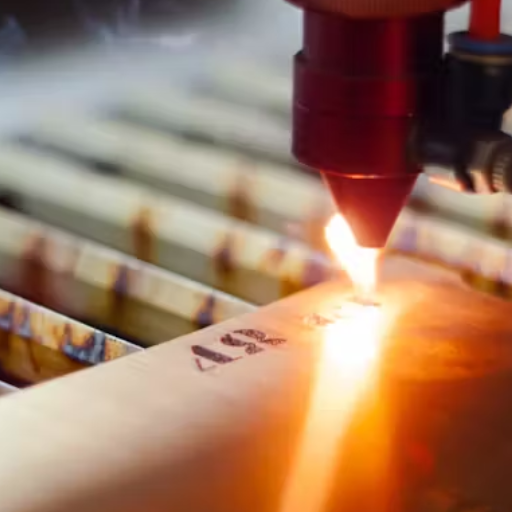
A laser etching machine is a sophisticated device that utilizes a laser beam to mark materials superficially. The beam’s intensity can carve out almost every – if not the entire – surface layer of the material it is focused on, which then vaporizes. An etched mark will then be left behind. One notable area where laser etching differs from engraving is its surgical precision. It can apply shallow cuts while simultaneously accommodating intricate patterns and scratches. For maximum efficiency and accuracy, it utilizes software alongside various laser components like diodes and mirrors, which ensures precision, speed, and reliability with every single task – all of which make it ideal for industrial, creative, or even personal use.
Understanding the basics of laser technology
A laser signifying a light amplifier emitting radiation is built on the premise of and is equated to the emission of radiation. Understanding the laser mechanism requires grasping an energy source (pump), a gain medium, and the optical cavity, which comes with mirrors to magnify the light, as these are its fundamental pieces. The energy source excites atoms of the gain medium to the point where they emit photons. These photons will then be reflected and, while doing so, will gain support from the optical cavity until they form an exceedingly delicate and coherent beam of light.
The gain medium used to define the laser’s specific features, like output power and wavelength, depends on its type (solid, liquid, gas, or semiconductor). These features allow using laser-cut materials for intricate surgical procedures and data transmission through telecommunications. Control systems such as computer software and feedback loops are also necessary for effective laser operation to provide precision and stability and maximize optimal performance.
These components help explain lasers’ flexible nature and how they can be utilized across many sectors of modern technology.
Types of lasers used in etching machines
Surprisingly, CO2 crystal, fiber, and UV lasers were widely preferred in etching machines. CO2 lasers are versatile as they work well on non-metal materials like wood, acrylic, and glass. Fiber lasers have a reputation for being the best for etching metals because they are very accurate and can work at very high speeds. For UV lasers, these are best suited for more fragile materials, including composites and plastics, owing to their low thermal effect. The choice of laser to use depends on the material to be etched and the desired etching quality.
The process of laser etching explained
Laser etching is the technique that concentrates a high-powered beam of light to cut or engrave surfaces through marking or carving. This technique starts with preparing the design, usually done using a computer for precision. After completing the design, the laser system must be set according to the etching material. The material settings include power, speed, and intensity, which must be adjusted to achieve the desired depth and quality.
Straightforward, a laser beam is always aimed toward the material surface. The beam is directed with such power that it deeply heats and vaporizes the material layer, causing an everlasting mark. Fiber lasers, CO2, and UV lasers have come on the market recently, and their supposed interaction will vary based on the material. For instance, fiber lasers are excellent for metals because they are rough and need a firm surface. CO2 lasers are for light materials such as wood or glass.
Laser etching stands out from other laser marking methods because it can create superficial marks that don’t compromise the material’s structure. It is commonly used in manufacturing, electronics, and medical devices to provide high-quality, durable markings. Laser engraving guarantees efficient output and consistent results across various applications through its accuracy, quickness, and flexibility.
How to choose the best laser etching machine for your needs?
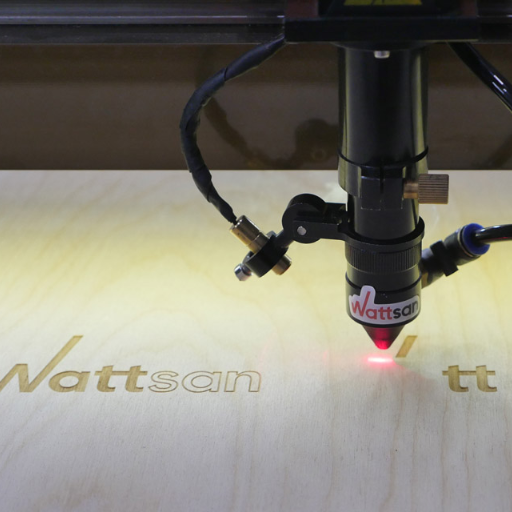
Selecting the most suitable laser etching machine involves carefully understanding your precise needs, material compatibility, and goals for the future. Start by determining what kind of materials you are interested in etching. Machines accommodate different substrates, such as metals, plastics, glass, and ceramics. Each laser type, usually a CO2, fiber, or UV source, will have varying capabilities depending on its application. For example, CO2 lasers work with non-metals, while fiber lasers are known for their proficiency in marking metals.
Next, consider how precise and fast your process has to be. Generally, machines with higher power ratings will have faster etching speeds. However, speed can lower the detail given to fine etching, meaning that accuracy must be carefully considered based on each use case. Also, make sure that the machine’s software compatibility meets your requirements. The machine should be able to integrate with design applications and offer efficient operational interfaces.
Lastly, consider model reliability, ruggedness, available customer service, and brand image. Strive for machines with proven robust build quality and excellent customer support. Balancing operational features cost-effectively guarantees a machine that effectively meets both current and future production needs.
Comparing CO2, fiber, and diode laser engravers
My comparison of CO2, fiber, and diode laser engravers demonstrates that each type has its specific advantages regarding material use and purpose. For example, CO2 lasers are highly flexible and can cut and engrave non-metal materials such as wood, glass, and acrylic while doing some light engraving on metals with special coatings. On the other hand, fiber lasers are superlative at metal marking and engraving, which they do with the most incredible precision and speed for industrial works like engraving bar codes or serial numbers. Though weaker, diode lasers are inexpensive, making them suitable for hobbyists or light-duty engraving on wood and soft materials. For each user, the right engraver will depend on how they come up with the ideal blend of factors such as material type, production scale, and expenditure limits.
Key features to look for in a laser etching machine
Throughout my research, I found plenty of features that a good laser etching machine must have, but I try to remain focused on a few areas to save time while also being efficient. First, power output is one of the most critical features since the higher the wattage, the deeper the engraving is and the faster the processing speeds, particularly with rigid materials like metals. Second, material compatibility does matter, as I try to work with machines that support a wide array of materials. Third, Windtmiller Integration stands out due to ease of use and customization, which hugely affect workflow and quality. Also, bed size or fixed work area is something I look at since these dimensions are necessary for a wide variety of projects. Lastly, the machine’s longevity and the manufacturer’s support, like warranties and customer service, are vital for reliability. These aspects work together when deciding which laser etching machine to purchase.
Desktop vs. industrial laser engraving machines
Understanding the differences gives us insights that stem from value and level of operational use, with the core differences stemming from size, application, and system function. If we focus on the desktop units, they tend to cater to small-scale users like hobbyists and small businesses in home or office environments. They have a low power output, making them very effective for softer materials such as wood, acrylic, and leather. The footprint of these models is more compact than many, making it easy to set them up, but it also limits the working area and, hence, has lower adaptability to project size. For new entrants into the field or those that do not have high work demands, these models are more economical because they are lower in price.
Industrial laser engraving machines are more suited for heavy-duty applications requiring high-intensity work as they can cater to high volumes of work. These tools have higher power outputs, making them effective in cutting or engraving metals, ceramics, and composites. They come in large bed sizes, which makes it easier to carve complex, bulky parts. They are designed for high endurance and continuous working. Industrial systems efficiently work with speed, precision, and accuracy, which has increased their adoption in manufacturing environments for mass production. They have more floor area, maintenance, and initial expenditure.
The choice between the desktop and industrial models is subjective and depends on one’s operational requirements, the materials used, the magnitude of work being done, and the available budget. It is in the users’ best interest to consider these factors when choosing a machine so that it appropriately fulfills their needs.
What materials can be engraved or cut with a laser etching machine?
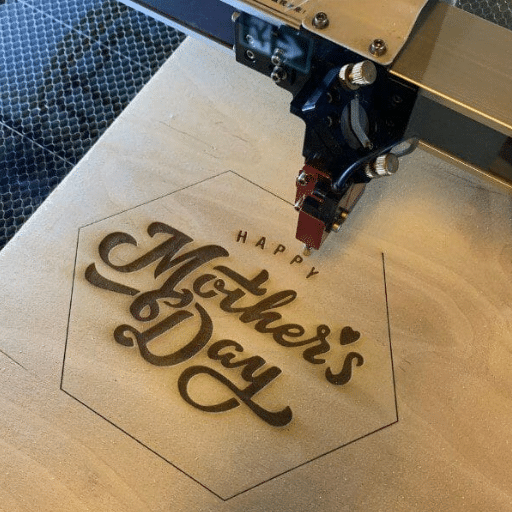
Laser etching machines can engrave or cut metallic and non-metallic materials. These may include stainless steel, aluminum, brass, wood, glass, leather, and acrylic. Depending on the laser’s type and power settings, etching or cutting certain plastics, ceramics, and even some fabrics is possible. Users should check whether the machine suits the material to avoid damage and achieve the best results.
Suitable materials for laser engraving
Laser engraving machines are used across various manufacturing, crafting, and industrial applications because they can work with multiple materials. Metals like stainless steel, aluminum, brass, and titanium are often engraved to improve identification or decorative purposes due to their durability and precision. Wood, acrylic, leather, and glass are non-metal materials that provide flexibility for artistic and commercial endeavors. Certain plastics, such as ABS, polycarbonate, and PMMA, can be used as long as appropriate laser settings are used to prevent melting or warping. Certain ceramics, along with anodized aluminum, which is a coated material, permit engraving with high contrast. Since the type of laser and its power significantly affect the results, it is highly recommended to follow specific material directions or machine standards to guarantee the required output.
Materials that work best for laser cutting
Various non-metals, metals, and some composite materials are the best suited for laser cutting. Acrylic is considered one of the best options as it has a shine and a smooth edge when cut. Other common non-metals include plywood and MDF, which can be charged only with the correct settings and applications. Thin sheets of metals such as stainless steel and aluminum are also very appropriate, particularly when utilizing higher-powered laser systems for metalworking. In addition, polycarbonate and Delrin plastics can be laser-cut, but safety measures should be taken to avoid inhaling toxic vapors. Knowing the machine limits and the material properties ensures better-cut quality.
Limitations and safety considerations
Although laser cutting is exceptionally efficient, there are also some limitations and concerns regarding safety. Not every material can be used for laser cutting, like polyvinyl chloride (PVC) or some fibers, because they emit hazardous gases or corrosive fumes that are dangerous to safety and equipment. Material thickness is perhaps the most critical limitation; if the material is too thick, there is a greater chance that the laser will not be effective and will lower the cut quality.
To avoid exposure to laser radiation while working, operators must wear appropriate protective eyewear suitable for the task. Health risks and potential fires can result from specific material processes due to hazardous fumes that are poorly vented, thus making proper ventilation very important. Fire safety measures are equally necessary, such as having extinguishers on hand because of the intense heat created while cutting. Lastly, routine upkeep on the laser cutting machine is critical to ensure it continues to work correctly and to alleviate hazards from failing parts.
How to set up and use a laser etching machine for beginners?

As a novice looking to operate a laser etching machine, start by unboxing and assembling it according to the provided instructions. Confirm that all connections and components are properly arranged. After that, position the device on a stable surface, plug it into the power source, and run the software with it. Remember to follow any calibration protocols as directed by the manual, such as adjusting the focus of the laser to correspond with the thickness of your material. Lastly, ensure you are fully protected with laser safety goggles and that your workspace has the ventilation needed before commencing any work.
Now that everything has been prepared ensure the material you want to engrave is compatible with the etching machine. Secure the material on the etching machine bed to prevent any shifting mid-operation. Design the required pattern using the software, then set the powers, speed, and resolution based on material specifics. If possible, use the test run on scrap material to confirm settings. When the settings are confirmed, begin the engraving process after closely monitoring the advancement while following all safety procedures. Cleaning and maintaining the machine after working will ensure it properly functions in the long run.
Basic operations and software navigation
The very first thing that must be done before using a laser engraving machine for the first time is to sit down with the control software. Proprietary software comes with most engravers, although some support designs are from third-party programs such as LightBurn or RDWorks. Make it a point to have the relevant software installed before commencing. You can import a design or create one using svg, dxf, or pdf files when the software runs. You can also edit the file by shifting the placement, form, and other components that must be altered to complete the design according to your preferences.
Most programs have basic navigation buttons to move the essential editing factors like percentage or watts of laser power, speed in mm/s, and dpi resolution. The final step before engraving is to see how well the design is on the machine’s bed. To facilitate this, most pieces of software have a “frame” or “trace” function that outlines the work zone without using the laser, which is essential to help make sure the design is correct before being engraved.
Moreover, higher-order functions such as the layer settings can assign unique power and speed values for each section, optimizing multi-material jobs or complex designs. Lastly, the design can be uploaded to the engraver using a USB flash disk, Wi-Fi, or any other supported connection, and the job can be executed. Knowing your software’s capabilities and practicing these steps will improve efficiency and quality.
Tips for achieving professional results
To achieve professional results, I clean and firmly fix the material on the engraver’s bed so there is no movement during operation. I set the laser power and speed appropriate for the material and core sampled my parameters on scrap pieces. Other parts of the laser system, such as the lens, require frequent cleaning, and the system must be calibrated in alignment to maintain the precision and efficiency of the laser. In addition, the files containing designs are of high resolution, and every project is thoroughly checked on the software for the correct scaling and alignment before setting the engraving process in motion. Following these procedures enables me to achieve quality and consistency.
What are the applications and business opportunities for laser etching machines?
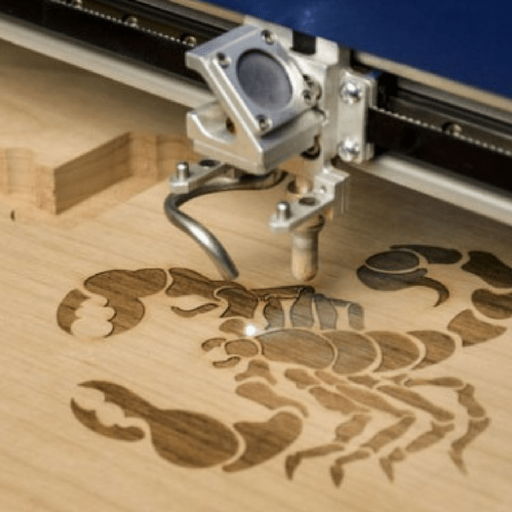
Considering the broad spread of industries that could benefit from laser etching machines, they might be one of the most helpful business investments as they can be utilized widely. In manufacturing, they serve as identification tools and can engrave barcodes, logos, and even serial numbers for easy product identification on metals, plastics, and glass. In the creative industry, these tools help to etch customized promotional gifts, jewelry, and even custom gifts, allowing individual clients or corporations to be satisfied. Laser etching is also used in the electronics industry to mark circuit boards and components, which require utmost precision and durability. Moreover, architectural firms and interior designers use them to create wood, glass, and even stone patterns. Due to the increased demand for permanently marked and personalized goods, many businesses can capitalize on the lucrative market while using laser etching technologies, creating opportunities for expanding enterprises and smaller firms.
Popular products and services using laser engraving
Adding and engraving customization are the most distinct features, which is why laser engraving is considered fundamental for offering various other services and products. Among all, the design of personalized gifts, jewelry, awards, and souvenirs stands out as the most popular. As the products and services are designed for individuals and corporations needing unique items for special occasions, branding, or events, embedding a memorable touch serves a highly recommendable user experience.
The application of laser engraving technology greatly enhances product branding and design and significantly contributes to the commercial sector. This technology is commonly used to produce promotional items, business signs, and custom packages. These applications aid in increasing brand recognition and product identification, enabling companies to stay competitive in their markets.
Laser engraving also has a wide variety of uses in manufacturing, especially in marking essential parts. This includes engraving identification serials, barcodes, and other relevant details of machines, tools, and electronic devices in an everlasting manner. These engravings can withstand harsh conditions and adhere to the needs for identification and monitoring in the aerospace, automotive, and manufacturing industries. Such diverse applications underscore the broad scope and significance of laser engraving technologies in various sectors.
Starting a laser engraving business from home
With the right intentions, beginning a laser engraving business working from home is very doable. Over time, I created a robust portfolio, starting with purchasing an affordable laser engraver that could process wood, acrylic, and metal and welding safety goggles to operate my designated workspace that maintained beneficial ventilation. I designed samples and marketed my services on Etsy, social media, and my website to establish a clientele. By cultivating satisfying customer relations and keeping up to date with emerging markets, I could simultaneously grow the reach of my business while working from the comfort of my home.
Expanding your existing business with laser etching services
Adding laser etching services can help broaden your business and expand your customer base. It can be achieved by investing in a laser etching machine that has multi-material and detail-oriented features. Enhanced precision in work enables the creation of more intricate designs on glass, ceramics, leather, and some metals, which can be leveraged to promote your brand further. While expanding the portfolio, consider adding personalized gifts or corporate branding items requiring detailed etching. Use the power of marketing, as it is crucial in promoting new services. Advertise through social media, target specific customer groups, or appeal to past clients with tailored offerings. Remember to continuously look ahead by studying new materials and technologies in laser etching so your business stays modern and can address diverse needs.
How do you maintain and troubleshoot your laser etching machine?
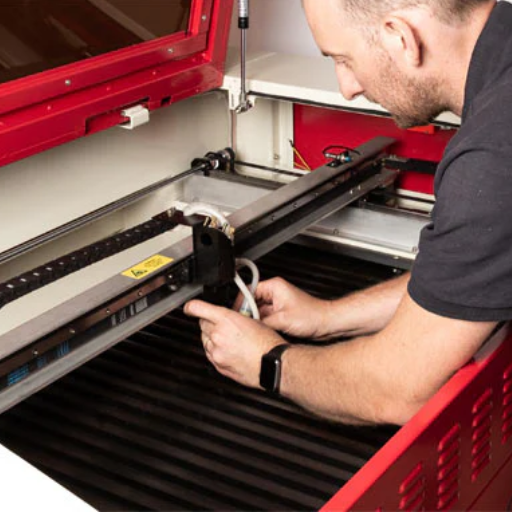
I pay special attention to cleaning and inspecting parts like the laser lens, mirrors, and exhaust system to maintain my laser etching machine. I need to ensure that dust and debris are wholly cleared after every use, employing cleaning equipment suggested by the manufacturer. Besides that, I also analyze whether any software or firmware updates need to be attended to so that the machine operates optimally. As for troubleshooting, I consider looking at the error messages on the interface first, then checking the manual to see what needs to be done to fix it. Other than that, I checked the manual to see how to solve the problem. If I can’t figure it out, I start looking at the rest of the system: the connections, the cooling system, and the laser alignment, which are the essential points of failure. To solve complicated problems, I sometimes need to contact the manufacturer or a skilled technician; for those, I don’t hesitate to take the necessary steps. I usually perform my regular maintenance tasks, and if something is not working, I try to solve it, which is why I have been able to keep the downtime of the machine low for a long time.
Regular maintenance tasks for optimal performance
Good maintenance habits must be followed to maintain the optimum functionality of your laser etching machine. First, thoroughly clean the laser lens, mirrors, and exhaust system. Accumulated debris can negatively impact precision. Use lint-free cloths and manufacturer-approved cleaning solutions for delicate components. They will avoid damage. Next, make checking of laser and mirror alignment a habit. Misalignment significantly reduces the accuracy of engravings. Moreover, consider the cooling system. Check to see if there are any blockages or leaks. These could cause overheating, which is detrimental to the machine. Checking the electrical connections and cables for wear and looseness also reduces the chances of interruptions. Finally, periodic software and firmware updates will add new features and resolve known bugs. Knowing and understanding these steps will result in less downtime, greater machine longevity, and user consistency.
Common issues and their solutions
One common issue is overheating, typically caused by obstructions in the cooling system. To mitigate this, I ensure coolant levels are topped off and routinely check for clogs or leaks within the system. Another common issue is frequent deviation from the engraving depth. This is usually caused by dirty lenses or lenses with misaligned mirrors. I thoroughly rechecked and realigned mirrors and cleaned every optical component to resolve it. Finally, operational disruption can occur due to software issues. In such cases, I usually refresh the machine’s firmware and software, as the latest versions often resolve most issues regarding compatibility and performance.
When to seek professional repair services
Seek help from a specialist after attempting maintenance and other procedures that yielded no results. For example, persistent overheating after coolant level adjustments, blockage removal, and checking the cooling system could cause more complex mechanical problems requiring sophisticated diagnostic tools. Likewise, regularly occurring misalignment of mirrors or inconsistent engraving after hardware cleaning and alignment suggest wear or tear failure that needs a skilled solution. Moreover, a lack of resolution by file updates or software reinstallation may require professional intervention to uncover file corruption or some other unreconciled incompatibility problem. In the end, paying attention to abnormal machine functions such as electrical odor, strange sounds, or complete unresponsiveness should be taken seriously. Taking steps to solve these issues before further damage is caused or safety issues arise should be a primary concern.
What are the latest advancements in laser etching technology?

The precision, efficiency, and versatility of laser etching technology have dramatically improved with the introduction of new ultrafast femtosecond lasers capable of inflicting extreme levels of precision with very little heat damage to the material. The ability to process and etch complex composites has also been enhanced due to the introduction of multi-wavelength lasers. Integrating AI-powered software has automated many processes and improved design accuracy, while green and UV laser systems have revolutionized micro-etching and marking applications. These innovations continue to drive efficiency and the incorporation of laser etching across disciplines.
Innovations in laser engraving and cutting machines
Recent innovations focus on the accuracy and scope of material use of laser engraved and cut machines. The adoption of high-power fiber lasers to cut more substantial materials such as metals has resulted in a shift due to its efficiency, whilst CO2 lasers are still preferred for non-metal materials such as acrylic and wood. Moreover, novel advanced motion control systems enable higher speeds of cutting or engraving while minimizing material waste. The development of dual-source laser machines that utilize fiber and CO2 lasers enhanced functionality because more challenging materials can be processed without relying on other equipment.
Likewise, compact multifunctional systems that allow real-time interaction and AI-assisted design optimization are also rising. User-friendly and low-priced desktop lasers are now available for small businesses and hobbyists. Operators are now protected through enhanced safety features like enclosed cutting areas and advanced filtration systems. All these features and greater affordability are changing how laser engraving and cutting are done for various sectors.
MOPA fiber lasers and their advantages
MOPA (Master Oscillator Power Amplifier) fiber lasers have unmatched agility and detail for numerous multi-purpose tasks. They possess variable pulse durations that allow accurate control of the mark’s quality, depth, and contrast, making them useful for delicate color marking on metals or preventing heat damage on sensitive materials. Their ability to work on various materials at different speeds makes them very efficient and versatile. MOPA fiber lasers are equally unmatched in producing high-contrast, permanent marks necessary in industries with strict marker traceability, such as aerospace and medical devices. These lasers are the most economical option for businesses because of their longer service life, low maintenance requirement, and energy efficiency.
The future of laser etching technology
The development of precision, flexibility, and automation will arguably conquer the future of laser etching technology. Innovative technologies such as ultrafast lasers, which can process materials with an extremely low pulse repetition rate, offer the possibility of finer processes due to a reduction in the heat-affected zone. This is a paradigm shift for industries that deal with microelectronics and medical implants because it provides the required level of detail. Furthermore, AI-powered automation and IoT devices will improve the efficiency of operations through integration and allow for real-time monitoring and predictive maintenance of production systems.
Another significant trend is the development of eco-friendly laser technologies, as industries aim to minimize environmental impact. The modern economy demands higher energy efficiency from laser systems and manufacturers’ greater use of recyclable materials. Also, there is increasing support for hybrid systems that perform laser etching and other functions, including additive manufacturing, to widen the scope of use.
In summary, laser etching technology is evolving to become multi-functional, more integrated with artificial intelligence, and more environmentally friendly. Such transformations will be required to satisfy the constant changes in demand coming from aerospace, electronics, and even healthcare.
References
Frequently Asked Questions (FAQ)
Q: What is laser marking and how does it differ from laser engraving?
A: Laser marking is a process that uses a laser beam to create permanent marks on a material’s surface without significantly altering its depth. It differs from laser engraving, which removes material to create deeper marks. Laser marking is often used for creating barcodes, serial numbers, or logos on metal surfaces, while laser engraving is better suited for deeper, more visible designs on various materials.
Q: What types of laser machines are available for engraving and cutting?
A: Several types of laser machines are available for engraving and cutting, including CO2 lasers, fiber lasers, and UV lasers. CO2 laser engravers are versatile and work well with organic materials like wood and acrylic. Fiber laser engravers are ideal for metal engraving and marking. UV lasers are suitable for sensitive materials and high-precision work. Desktop laser cutters and engravers are popular for small-scale projects, while larger industrial machines are used for commercial applications.
Q: What materials can a CO2 laser engraver work with?
A: CO2 laser engravers are highly versatile and can work with various materials. They are excellent for cutting and engraving wood, acrylic, leather, fabric, paper, and plastics. CO2 lasers can also be marked on glass and some coated metals. However, they are unsuitable for engraving bare metals, requiring a fiber laser or specialized coating for CO2 laser marking.
Q: What factors should I consider when choosing the best laser engraver for my needs?
A: When selecting the best laser engraver, consider the materials you’ll be working with, the size of your projects, your budget, and the machine’s power output. Look for features like a sturdy frame, reliable laser tube, and user-friendly software. Consider whether you need a desktop laser for small projects or a larger machine for commercial use. Also, consider whether you need a dedicated laser engraver or a laser cutter and engraver combination for more versatility.
Q: How does a laser cutter differ from a laser engraver?
A: While many machines can perform both functions, laser cutting and engraving are distinct. A laser cutter uses a high-powered laser beam to cut through materials, creating clean edges and precise shapes. On the other hand, laser engraving uses the laser to remove surface material to create designs or text. Many modern machines, called laser cutter and engraver combos, can perform both functions by adjusting the laser power and focus.
Q: What is a fiber laser engraver, and what is it best used for?
A: A fiber laser engraver uses a fiber-optic cable to deliver a highly concentrated laser beam. This type of laser is excellent for metal engraving and marking, making it ideal for industrial applications, jewelry making, and creating permanent marks on metal products. Fiber lasers can engrave on bare metals, coated metals, and some plastics with high precision and speed. They are known for their durability, efficiency, and ability to create fine details on hard materials.
Q: How important is laser power when choosing an engraving machine?
A: Laser power is crucial when selecting an engraving machine as it determines its capability to cut and engrave different materials. Higher laser power allows for faster engraving and the ability to cut thicker materials. For example, a 40W CO2 laser might be sufficient for light engraving and cutting thin materials, while a 100W or higher laser would be better for deep engraving and cutting thicker materials. Consider your specific needs and the materials you’ll work with when choosing the appropriate laser power.
Q: What safety features should I look for in a laser engraver?
A: Safety is paramount when working with laser engravers. Look for machines with features such as an enclosed design to contain the laser beam and fumes, especially for CO2 and fiber lasers. A Class 1 laser enclosure provides the highest level of safety. Other vital features include emergency stop buttons, automatic shut-off when the cover is opened, and proper ventilation systems. Some advanced models offer safety features like flame detection and automatic fire suppression systems.
Q: Can laser engravers be used for deep engraving, and what factors affect engraving depth?
A: Laser engravers can be used for deep engraving, but the depth depends on several factors. These include the laser power, engraved material, the number of passes, and the laser’s focus. Higher-powered lasers and multiple passes can achieve deeper engraving. The material’s properties also play a role; softer materials like wood allow for deeper engraving than more complex materials like metal. For very deep engraving, specialized machines or techniques may be required.
Q: What are the advantages of using a dual laser system in laser engraving and cutting machines?
A: Dual laser systems in laser engraving and cutting machines offer several advantages. They can combine different lasers, such as a CO2 laser for cutting and engraving non-metals, alongside a fiber laser for metal engraving. This versatility allows a broader range of materials to be processed on a single machine. Dual lasers can also increase productivity by allowing simultaneous operations or quick switching between different laser types without changing the setup. Some systems use dual lasers to achieve higher power output or provide continuous operation redundancy.