The advancement of laser technology has changed the way manufacturing and design is done in various sectors because of its accuracy, versatility, and efficiency. This technology utilizes a directed laser beam to cut and shape materials, including metals, plastics, wood, and fabrics. Its uses are unlimited, from industrial manufacturing to custom product creation and artistic works. The different applications of laser cutting machines in various industries that allow them to achieve superior accuracy and scale merit are being explored further. Laser cutting is arguably the most critical technology in contemporary fabrication for prototypes, industrial mass production, and intricate designs.
What are the most common laser cutting machine applications?
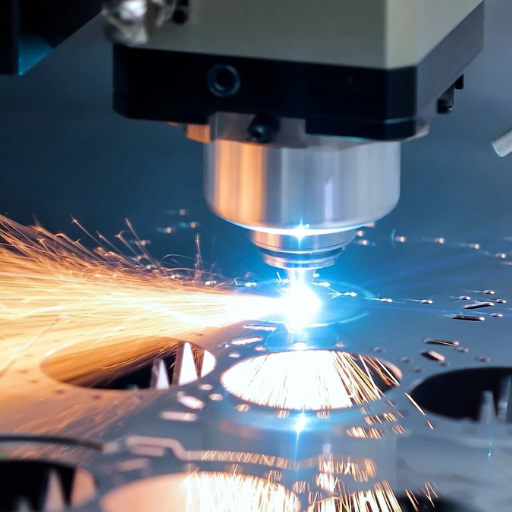
Laser cutting machines are a standard tool when it comes to the fabrication of different metal and non-metal parts like automotive components and sophisticated electronics. About the signage and advertising sector, laser cutting is widely used to craft letters and other images. Furthermore, laser cutters are vital in producing personalized items like jewelry, architectural models, and decorative pieces, showcasing unparalleled versatility and accuracy in diverse materials.
How is laser cutting used in the manufacturing industry?
In the manufacturing industry, laser cutting has its application in developing precise & complex components with delicate details while causing minimum waste in the material. It is very common in manufacturing automotive, aerospace, and electronics parts because of the materials’ intricate design and polymorphic nature. With such technology, efficiency is greatly enhanced in mass production because such works can be done with ease and without the need for other unnecessary production processes. Likewise, laser cutting enables rapid prototyping, making it easier and faster for engineers to create and assess designs before investing too much in them.
What makes laser cutting unique in art and design?
- Personalized Engravings: Custom engravings are made with laser cut for wood, metal, and acrylic. The precision helps artists to craft plaques, keepsakes, and panels for decoration.
- Sculptural Works: Sculptors use laser cutting to construct multilayered, complex geometric pieces, something that would be nearly impossible with traditional methods.
- Typography and Lettering: Designers choose laser cutting for letters used in wall art, branding, signage, and even abstract sculptures where sharpness and creativity are needed.
- Architectural Models: Architects and designers use laser cutting to complete scale models. Cardboard and plexiglass can be cut and engraved to produce clear windows, facades, and other construction features.
- Jewelry Design: Jewelry makers tend to use laser cut for patterning metals and gemstones into delicate and sophisticated pieces with minimal waste.
- Textile and Fashion Design: Fashion designers have adopted laser cutting in the production of garments and accessories because it enables them to achieve precision cutting and unique textures and patterns on fabrics.
- Decorative Panels and Screens: Builders and interior decorators create modern styles of interior walls by using laser-cut panels and screens that serve multiple purposes. They can work as room splitters, wall art, or even shutters, all displaying beautiful design patterns.
- Lighting Fixtures: The creative sector of lighting uses lasers more than others, as they can be used to cut lampshades and light fixtures into any desired shape that will not only enhance the beauty of the light but also diffuse it.
- Signage and Branding: Many of the custom signs created for different businesses, including logos, name tags, and even brand ornaments, are made using laser engraving, which makes the process easier and faster while still maintaining sophistication.
- Prototype and Concept Art: For better innovations, designers and artists turn to laser cutting for their exhibition pieces or other gallery displays to ensure a contemporary piece while also ensuring quality.
In which ways does the automotive industry gain from laser cutting technology?
Automobile makers can utilize precision cutting because of laser technology development. This technology makes it possible to manufacture complex parts like engine components, airbags, and the body panels of cars with extreme precision and very little material waste. Most importantly, the incorporation of laser cutting to modern manufacturing processes has sped up production significantly, which cut costs in manufacturing. Furthermore, while building lightweight, durable vehicles, steel, aluminum, and composites, among other materials, can be processed. Lastly, components cut with lasers are of much higher quality grade because they have smooth edges and are cut to very precise tolerances. All automotive components are produced with strict requirements, which is why lasers are preferred.
Which materials can be effectively cut using a laser cutting machine?
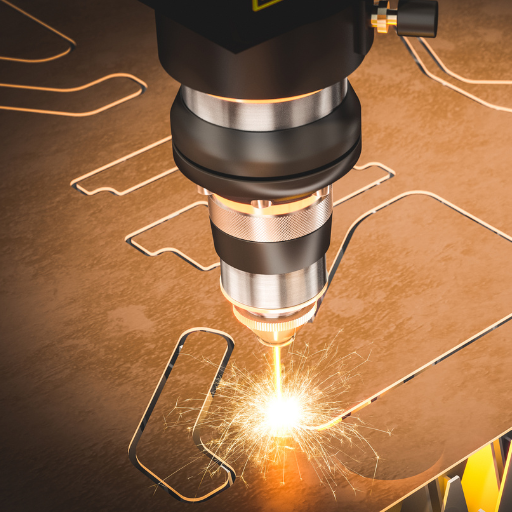
Laser cutting machines efficiently cut a range of materials, including steel, stainless steel, and aluminum, as well as wood, acrylic, plastic, and glass. Furthermore, they can cut fabric and composite materials and some types of ceramics. Because of the precision and clarity that laser machines provide, they are highly suitable for many industries.
What materials are best suited for CO2 laser cutting?
- Wood: Because wood is organic, CO2 lasers are very efficient in cutting and engraving. Furniture construction, model making and custom signs are just some of the popular applications. Softer wood types like balsa and plywood are known for their excellent cut quality and clean edge.
- Acrylic: Acrylic is one of the most used materials for CO2 laser cutting. As the laser cuts the sheet, the edges are polished and flame-finished. Hence, it is great for making decorative displays, cases, and signs.
- Paper and Cardboard: Due to their light weight, these materials can be easily cut using CO2 lasers. They can be used for packaging, crafting, artistic designs, and even prototypes with a low risk of burns when the correct settings are utilized.
- Plastics: Some plastics, such as ABS, polycarbonate, and PETG, can be cut effectively using CO2 lasers. However, different plastics have differing fumes and surface quality, so those processes must be monitored closely.
- Textiles: CO2 lasers can also be used on cotton, polyester, felt, and leather. Their precision in laser cutting allows them to be widely used in the fashion and upholstery business because they eliminate fraying and allow intricate details to be cut.
- Rubber: Rubber materials suitable for lasers, such as stamps or industrial gaskets, can be easily cut using CO2 lasers, which ensures sharp feature detail for custom applications.
These materials are ideal for CO2 laser cutting and engraving because they have low reflection and high absorption of the laser beam which guarantees optimal performance and high-quality work.
How does fiber laser cutting work with other metals?
Thanks to its laser wavelength and energy density, fiber laser cutting can easily process various metals. Fiber lasers deliver concentrated energy to reflective and hard materials, like stainless steel, aluminum, brass, and copper, with very low reflection loss. Because of this, they are able to provide clean and precise cuts on thicker surfaces.
Nitrogen is usually used as an assist gas when cutting stainless steel. This allows the laser to provide high-quality cuts without any oxidation. Parameters, such as cutting speed and power settings, greatly depend on the metal’s thickness. For example, a power output of 1K will be needed to cut 1mm thick sheets, and higher power outputs will be needed for thicker sheets.
Aluminum shall also undergo electric cutting, as fiber lasers are rather good at absorbing it. When cutting aluminum, power levels of up to 4Kw can be provided, while nitrogen or compressed air is used to prevent oxidation and provide smooth edges.
Due to their reflectiveness, cutting copper and brass is extremely simple, but it generally requires very specific parameters, like a cutting power of two to three kilowatts to minimize reflection. Additional settings that need to be modified include adjusting the cutting speed to a moderate level.
Specialized fiber laser technologies enable precise control over the beam and work in tandem with modern automation systems. In metal processing, they ensure high throughput performance, while keeping operation costs low. Low maintenance workload and high energy efficiency make it a favorite in industrial production.
Are there any processes that cannot be completed with a laser cutter?
Laser cutters are very flexible, but some materials cannot be cut as they are too thick or too thin for the laser. For instance, thicker than one millimeter polycarbonate sheets tend to discolor and produce burn marks. Additionally, PVC or polyvinyl chloride should never be cut because it emits toxic gas and threatens equipment. Specific grades of glass or mirrors can be tough to cut due to their reflective surface. Flammable materials like foam core boards or some fabric composites are not advised for laser cutting as they can pose a fire hazard.
What are the advantages of using laser cutting technology over traditional cutting methods?

Lasers provide many advantages compared to traditional cutters. They offer a unique level of precision, allowing for complex and detailed designs to be cut with a margin of error that is next to nothing. The process itself is contactless which lowers the chances of material damage or deformation during the cutting phase. The laser cutter is also more efficient since it utilizes higher cut speeds, improving productivity greatly while also cutting down on material loss due to its high accuracy. Besides, it’s compatible with many types of materials, which makes it more applicable to a wide array of industries. This technology usually require less effort to process the output which makes production more effective and economical.
How does laser cutting improve precision and accuracy?
When dealing with materials, whether soft or hard, laser cutting aids in accomplishing high accuracy levels through focused laser beams. In particular, the laser beam’s energy can be focused to achieve a kerf width smaller than one hundred of a millimeter (0.1 mm). With such extreme focus, the system can consistently deliver energy to the cutting region, which reduces thermal distortion and achieves cleaner cuts. In addition, the laser beam can be moved by computer numerical control (CNC) systems offered. Most modern CNC systems offer tolerances as tight as ±0.001 inch for certain systems, which allows the laser to move with extreme accuracy. Since the process of laser cutting is non-contact, any possibility of mechanical interference or material displacement “shifting” during cutting is eliminated, improving accuracy in way. Such features ensure upper limits such as power, pulse rate, and laser cutting speed are set, enabling optimal performance over a wide scope of materials and thickness, providing high precision quality.
What cost benefits does laser cutting offer for businesses?
Laser cutting provides tremendous cost savings to businesses because it minimizes material waste through accurate cutting. For this processes to function, maintenance is not needed, and labor costs are reduced since production robots are in charge. Moreover, working with different materials and intricate shapes is easier and more efficient because no tools or costly molds are required to customize and prototype. These processes lead to savings in time and money for customization and models. All these savings contribute to decreased production costs without sacrificing the quality of the end product.
In What Ways Does Laser Cutting Improve Production Speed?
Using lasers for cutting allows for faster production timelines by employing high speed cutting, minimal initial setup, and decreased lead time. Unlike traditional techniques, there’s no need to prepare physical tools such as molds, which means that all producers have to do is shift from one design to another. The average cutting rate for CO2 and fiber lasers depends on the material type and thickness but can be up to 20 meters per minute for thin sections of stainless steel. Fiber lasers are more energy efficient, and tend to offer higher processing speeds than CO2 lasers, especially when working with materials of medium thickness. Moreover, the addition of automatic software for loading, unloading, and nesting makes production more efficient, as further reduces downtime and ensures that production targets are achieved without compromising quality.
What types of laser cutters are available for different industries?
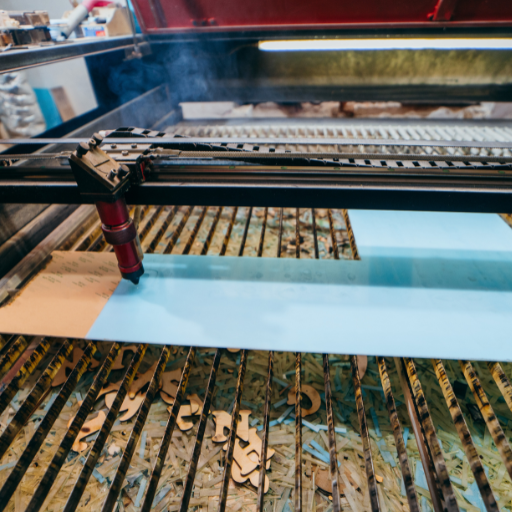
Various styles of laser cutters service numerous industrial uses and different types of materials. Non-metal materials like wood, acrylic, and textiles are precisely cut or engraved by non-metal CO2 laser cutters. Fiber laser cutters use YAG and crystal lasers and specialize on metals. Due to their high efficiency and speed, they cut for stainless steel, aluminum, brass, and precise thin/medium thicknesses. Crystal and YAG are used to cut thick metals or ceramics, which need significant energy. Each laser cutter type is built to address specific industries’ needs and ensure the best output on one or more industries.
What are the differences between CO2 and fiber laser cutting machines?
Like with other tools, CO2 and fiber laser cutting machines are essential for particular industries because of the differences in their structure, efficiency, and the range of materials that can be used. Lasers employing CO2 technology are electrically stimulated by a gas mixture that features carbon dioxide. These lasers flawlessly cut non-metal materials such as wood, acrylics, and plastics. They also process other organic materials and produce better quality engravings as compared to other lasers. As for fiber lasers, they cut metals with extreme efficiency, especially reflective metals like stainless steel, copper, and aluminum. These metals require a solid state laser design for maximum efficiency. This laser design amplifies light through glass fibers that are doped with rare-earth elements, meaning they endorse a wavelength of about 1.06µm. CO2 lasers, on the other hand, have a base wavelength of about 10.6µm, meaning they are less efficient in this regard.
The performance parameters unambiguously pronounce these distinctions. Compared to CO2 lasers, fiber lasers are superior in energy efficiency, maintenance requirements and cutting speed, mainly when thinner materials are concerned. Their beam quality enables them to perform cutting at a very detailed level, reducing the amount of waste materials. CO2 lasers do cut slower on metallic surfaces, but they are faster at cutting thick organic materials, and they cut more smoothly with a smaller heat-affected zone. Ultimately, the choice depends on the particular material, its thickness, and the particular production needs of the application.
How do you select the most appropriate laser cutter for your requirements?
Your operational requirements dictate your choice of a laser cutter, so you must consider them carefully. For example, what types of materials do you need to work with? Fiber lasers work well with metals, and CO2 lasers work well with non-metals and organic materials. Determine the thickness of the materials that you need—fiber lasers are more suitable for thin metals, while CO2 lasers are more effective for thicker cuts in specific applications. Evaluate your production volume and speed needs, as fiber lasers are much more efficient than CO2 lasers for cutting thin, non-ferrous metals at high volumes. Think about the costs, such as how much the machine costs, the cost of maintenance and the cost of energy to run it. Lastly, examine the accuracy and quality of the edges that need to be cut, since fiber lasers provide finer details and less waste. In contrast, CO2 lasers provide smoother edges on certain substrates.Carefully matching these factors to your production goals will provide an optimal solution.
What considerations will you take into account when choosing a laser cutter?
Assessing the laser power, its type, and the dimensions of the work area are three crucial factors to consider when selecting a laser cutter. The power of the laser affects how well the machine can cut and engrave—30-50W typically fulfills engraving tasks and cutting to thicker materials such as metals requires at least 100W. Moreover, the type of laser, whether it is fiber or CO2, should be appropriate for the materials being processed. Fiber lasers work best with metals as they have a shorter wavelength; CO2 lasers work better with non-metallic materials such as wood, acrylic, or glass. Furthermore, the machine’s work area should be able to hold the size of your projects. Analyze its bed size and accessibility to ensure that it can support your material’s dimensions without hampering your productivity.
How can laser cutting machines be used for both cutting and engraving?
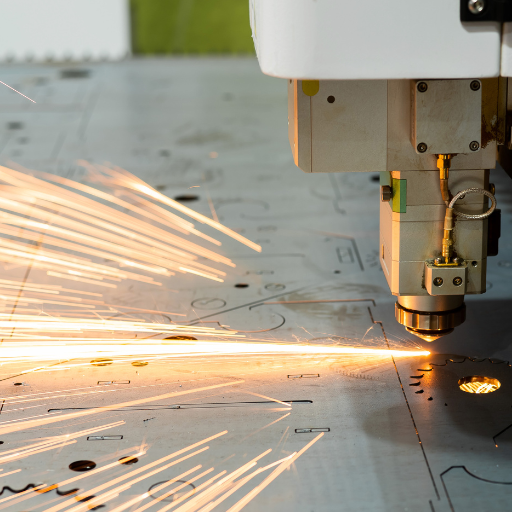
Laser engraving services pittsburgh A laser cutting machine uses specialized laser beams to cut through and engrave a material by applying differing amounts of power, varying the speed, and changing the focus of the laser. In cutting, the laser dissolves the material’s surface at a focused area and guides the material to be cut with software. The laser also enhances the material’s surface in engraving without cutting into its body by using lower settings to etch complex designs, words, or shapes. From manufacturing to creative industries, these machines are deemed suitable for virtually all custom-made tasks across any field due to their wide range operational abilities.
What Are The Unique Features of Laser Engraving?
Because of the unique focus of a laser beam, a material can be permanently glued together as it is transformed with phrases, images, or designs engraved on its surface, embedded in it. The non traditional and adaptable way of using laser engraving also ensures durability of the embedded content alongside the base material. Another added benefit is the efficiency of laser engraving because it is fast and adaptable to many other materials including metals, pales, wood, and glass without sacrificing quality.
In what way does the laser cutting process differ from laser engraving?
Even though cutting and engraving use the same laser technology, the two processes differ in depth. For instance, laser cutting is the complete penetration of the selected material to make cuts or shapes; it is common in manufacturing, prototyping, and construction. It employs high-powered lasers that vaporize, burn, or melt the material using a defined path. In contrast, laser engraving alters the surface of a material to put designs or text without cutting through it. This technique is used mainly for decorative, marking, or identification uses. In addition, unlike engraving, cutting tasks are done with greater speeds and power settings, which makes it optimal for metals, wood, and acrylic that need clean and sharp edges.
What are the most effective ways of achieving quality in terms of cutting and engraving works?
I undertake the necessary and proper steps to achieve both cutting and engraving work by using accurate material which fits the attribute of the laser needed for material. Different materials react differently to the laser intensity and speed, so I modify the laser’s power, focus, and speed before working on the material to make it more precise. Maintenance of the laser equipment is also key to getting rid of any dirt that has collected on lenses or mirrors, which can cause distortion and more extreme differences. Further, I configure the design file as it ought to be configured because it tends to have paths that are not well defined and it has lines that tend to overlap, which makes it prone to burning marks. I change these settings to achieve maximum quality getting rid of subpar work. I propose a piece sample that does not show much detail before the final piece so that I can adjust the cut out based on the original sample provided.
How is laser cutting technology evolving and what future applications can we expect?
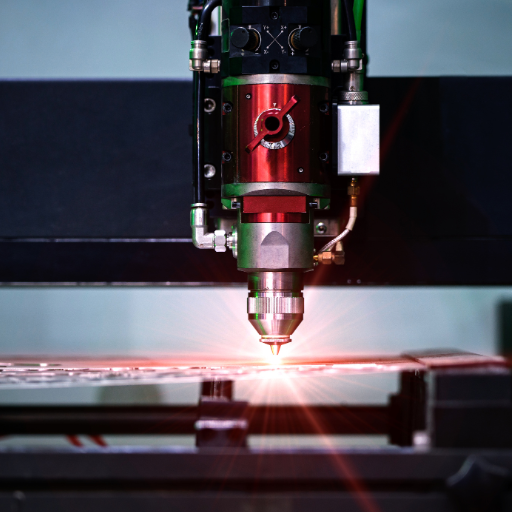
Improvements in speed, power, and versatility are helping to advance laser cutting technology. New technologies like fiber and ultrafast lasers offer higher processing rates, lower heat affected zones, and better energy efficiency than classical CO2 systems. Artificial intelligence and automation is also improving the use of lasers by assisting with workflow, design, and even error correction. Future uses will be in microfabrication and manufacturing of medical devices and aerospace parts, which require exact measures and cutting of materials as minimally as possible. Moreover, once the technology becomes cheaper and easier to obtain, it will also likely be more common in small businesses, prototyping, and custom consumer products.
What advancements are being made in high-power laser cutting?
The advancements for high-power laser cutting technology lie in minimization of cut time, precision cutting accuracy, and increase of material range to be processed. Modern systems are pushing power output limits, with fiber lasers now commonly reaching 20 kW and beyond, enabling faster cutting of thicker materials such as steel and aluminum. These high-power lasers are far more efficient, allowing for greater throughput while minimizing thermal distortion owing to the focused beam. The quality of the beam, measured by the BPP (Beam Parameter Product), is being improved, with even lower values, which result in greater focus and energy efficiency.
Another notable development is the use of more sophisticated beam shaping techniques, which enable modification of energy distribution on the periphery of the cutting zone. This improvement reduces the need for post-processing, increasing cut quality for complex shapes and reflective materials. The cooling techniques are also progressing with more effective methods that require shorter downtime and a more steady state of the system.
Operational control is being further improved through integrated software and real-time monitoring systems. These systems are programmable with reasonably intelligent algorithms that detect material changes and alter parameters like power, speed, or even assist gas pressure to yield better results with lesser resources.
In which ways is 3D laser cutting set to change the landscape of manufacturing?
With the advancement of 3D laser cutting, the focus on efficiency in the manufacturing sector is bound to revolutionize. This technique’s precision ensures a decrease in production time and material waste. Additionally, through improved automation, manual labor requirements are significantly reduced, which increases efficiency and lowers costs. The precision offered is also well suited for rapid prototyping and designing cuting-edge products across various sectors, including aerospace, automotive, and medical. The cross-industry adaptability and infrastructure improvements guarantee you will witness advancements throughout the manufacturing industry.
Reference sources
Frequently Asked Questions (FAQs)
Q: What are the main applications of laser cutting technology?
A: Laser cutting technology is used in various industries for cutting, engraving, and marking materials. Common applications include metal cutting for automotive and aerospace parts, creating intricate designs for jewelry and artwork, fabricating electronic components, and producing custom signage. The high-power laser beam allows for precise cutting to create complex shapes and patterns in a wide range of materials.
Q: What materials are suitable for laser cutting?
A: Many materials can be cut using laser cutters. These include metals like steel, aluminum, and brass; plastics such as acrylic and polycarbonate; wood and wood composites; fabrics; paper; and even some types of glass. The specific material used will depend on the laser machine’s power and the intended application.
Q: How does laser cutting work?
A: Laser cutting works by focusing a high-power laser beam onto the material surface. The intense heat generated by the laser melts, vaporizes, or burns away the material, creating a clean cut. The cutting head moves along a predetermined path, guided by computer-controlled instructions, to produce the desired shape or design.
Q: What industries commonly use laser cutting machines?
A: Laser cutters are used in different industries, including manufacturing, automotive, aerospace, electronics, fashion, and advertising. They are often used for prototyping, custom fabrication, and mass production. The versatility of laser cutting allows it to be applied in various sectors where precise cutting or engraving is required.
Q: What are the advantages of using a laser cutter compared to traditional cutting methods?
A: Using a laser cutter offers several advantages over traditional cutting methods. These include higher precision and accuracy, the ability to cut complex shapes, reduced material waste, faster production times, and the capability to work with a wide range of materials. Laser cutting also provides a non-contact cutting process, which minimizes material deformation and contamination.
Q: Can laser cutting be used for both industrial and artistic applications?
A: Yes, laser cutting is suitable for both industrial and artistic applications. In industry, it’s used for cutting metal parts, creating electronic components, and manufacturing precision items. In art and design, laser cutters are used to create intricate patterns, custom jewelry, personalized gifts, and unique artwork. The versatility of laser cutting technology makes it valuable in both functional and creative fields.
Q: What are some specific applications of laser cutting in the automotive industry?
A: In the automotive industry, laser cutting is often used for various applications. These include cutting and trimming body panels, creating precise holes for wiring and components, fabricating interior trim pieces, and producing custom parts for prototypes or specialty vehicles. The high precision and speed of laser cutting make it an essential technology in modern automotive manufacturing.
Q: How is laser marking different from laser cutting?
A: While both use laser technology, laser marking and laser cutting serve different purposes. Laser cutting is used to cut through materials, creating separate pieces or intricate designs. Laser marking, on the other hand, alters the surface of a material to create permanent, high-contrast marks without cutting through. This is often used for adding serial numbers, barcodes, or logos to products.