Achieving optimal cutting performance in metal fabrication requires a thorough understanding of the relationship between laser power levels and cutting speed. Modern laser cutting technologies, particularly those used in industrial applications, rely on precise configurations to balance efficiency and productivity. Material type, thickness, and thermal conductivity are critical in determining the required laser power settings for maximum cutting speed. This article explores these variables in-depth, offering insights into how laser power can be strategically optimized to enhance processing efficiency while maintaining accuracy and cut quality.
How much laser power do I need to cut metal effectively?
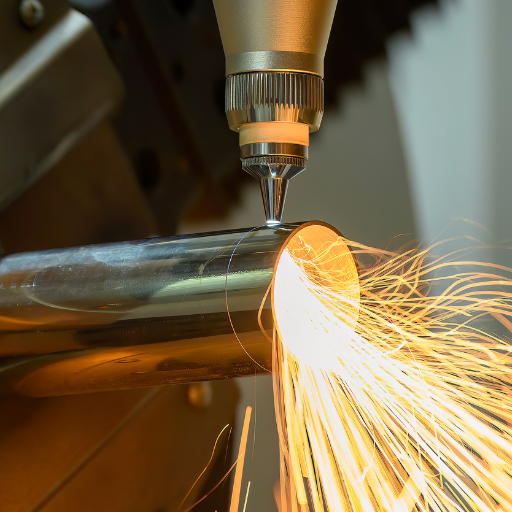
The efficiency and effectiveness of the metal-cutting process depend on the required laser power. Many variables are in play, such as aluminum and stainless steel sheets; they are generally below a specific thickness, so they only need around 500 to 1000 watts. Steel plates over 10 mm thick are a whole different story and will likely need at least 2000 wattts to keep laser precision while remaining efficient. The beam quality, cutting speed, and the type of assist gas used also affect the power settings and optimization. Calibrating all those is quite delicate yet completely necessary if one wishes to get clean cuts on the material without damaging it.
Analyzing The Link Between Laser Power and Cutting Capabilities
The laser machine’s power and its ability to cut are relative and dependent on various tech parameters. The requirements for cutting a thin metal sheet, like 3mm stainless steel, are within the range of 500-1000W, where the cuts are rendered clean and accurate. However, higher power is needed for thick metals whose range starts from 10 mm or above, on average around 2000-4000W. At this range, sufficient energy is provided to break through the material while keeping the edge’s quality intact. Furthermore, the cutting precision relies on laser beam quality, which is measured in BPP (Beam Parameter Product) and should remain low. The speed at which the laser cuts and the pressure of the assist gas also matter; for example, oxygen assist gas at 0.5-1 bar is generally employed for enhanced cutting speeds on thick steel parts. The need to prevent edge distortion and overheating the workpieces guides the setting of these parameters.
Causes that determine the laser power required when cutting metal
The type of material is one of the main determinants of laser power requirement since denser and more thermally conductive metals like aluminum and copper require more energy input than steel. Thickness is equally essential as thick materials do require higher power to cut them while maintaining quality. Focus and alignment of the beam greatly affect energy density at the cutting point, directly affecting precision. Moreover, the choice of assist gas also cuts dynamics – oxygen enables faster cuts due to oxidation, while nitrogen dross-free edges. Accurate machine calibration and environmental factors such as the temperature of the environment and the material surface condition also affect power efficiency.
Suggested ranges for laser power needed for different types of metals with varying thicknesses
- Mild Steel (Up to 5mm thickness): Clean and precise cuts require 500W to 1000W. Thicker sheets, generally 10mm to 15mm require 2000W to 4000W. This depends on cutting speed and edge quality.
- Stainless Steel (Up to 6mm thickness): Most applications can be completed with a laser power of 1000W. For plates over 8mm, the more powerful lasers (3000W to 6000W) will ensure penetration into the material while minimizing edge burrs.
- Aluminum (Up to 5mm thickness): Its high thermal reflectivity means Aluminum needs a laser power of 1500W – 2000W. Engraving plates thicker than 10mm will most likely require 4000W to 6000W.
- Copper and Brass (Up to 2mm thickness): Alloys of copper and brass can be worked with 1500W – 2000W power lasers, and for sheets thicker than 2mm, a laser up to 5000W is required because of their high reflectivity and conductivity.
- Titanium (up to 4mm thickness): Between 1000W and 2000W is needed to achieve a clean cut. For plates over 6mm, 3000W to 5000W are required while still achieving clean edges.
Such performance is also dependent on the specific laser system. Additional factors like cutting speed or the type of assist gas used for the laser machine should be changed depending on the range of powers used.
What are the differences between CO2 and fiber lasers for metal cutting?
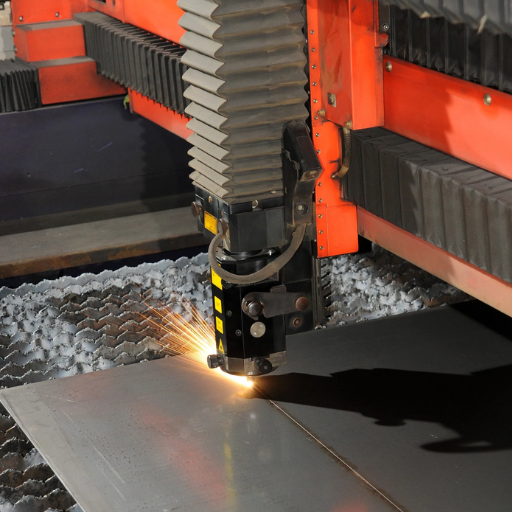
CO2 and fiber lasers have varying distinctions in design, effectiveness, and use when it comes to metal cutting. CO2 lasers are based on a gas medium and can effectively cut metals and non-metals. However, they consume more energy and require high maintenance as compared to fiber lasers. Fiber lasers, however, use optical fibers to amplify and achieve energy efficiency while minimizing maintenance and offering faster cutting speeds for thinner metals. Due to their shorter wavelength, fiber lasers can also cut highly reflective materials like aluminum, copper, and brass with great precision. While CO2 lasers are advantageous for use on thicker materials and can provide smoother cut edges under certain conditions, CO2 lasers are usually preferred for their long lasting feature, lower operational costs, and effectiveness in industrial applications.
Analyzing The Performance of CO2 and Fiber in Metal Cutting Applications
The performance of CO2 laser and fiber laser varies in regard to their technical parameters, which allows them to differ in their usage for different metal-cutting applications. CO2 lasers operate using Electromagnetic Radiation with a wavelength of 10.6 micrometers, which suitable for cutting thicker materials. These materials are cutting by CO2 lasers to achieve smooth edges and clean materials because of the wider power dose and deep range of cutting. When powering CO2 lasers, it is said that CO2 lasers can function between 1 kW to 10 kW, as they perform at lower speeds when cutting more thicker materials.
On the other hand, fiber lasers have a wider range of 500 W to 12 kW. They are contingent upon the beam quality as well as high power dose, Fiber lasers also cut at a higher range of 1.06 micrometers because it enables them to cut highly reflective metals such aluminum and copper. Thinner sheets are also cut at higher speeds with fiber lasers. It should also be noted that fiber lasers are more efficient than CO2 with an efficiency of 35 percent, unlike CO2 with 10-20 percent.
Moreover, CO2 lasers, like many other lasers, require external mirrors for beam delivery and gas replacement. This directly increases the maintenance costs and the complexity of operations. On the other hand, fiber lasers are fully solid state. This makes them compact and increases their robustness while reducing maintenance requirements. Fiber lasers are almost always the best choice for industries that value speed, accuracy, and operational cost. That being said, CO2 lasers still have their uses for applications that require smooth finishes on thicker materials.
Effects of fiber lasers on cutting reflective metals
Compared to other types, fiber lasers have a lot of advantages over reflective metals that make them stand out. The main advantages are the wavelength and high beam quality. The 1.06-micrometer wavelength is more easily absorbed when compared to aluminum, brass, and copper, which reflect light. This minimizes the risk of back reflections damaging the rest of the laser system. This property allows material to be maneuvered freely without worrying about the cutting be set.
On a technical note, the high operational power of fiber lasers allows for exceptionally high cutting speeds with thin sheets. For example, an average fiber laser with a power output of 8 kw can cut aluminum with thickness varying and setup arrangements at rate speeds about 7 m/min. Compared to CO2 systems, fiber laser systems also have much lower operational costs due to their Energy efficiency which can reach up to 35%. Moreover, their focusability, which allows them to focus beams to a smaller diameter, provides an opportunity for more precise and clean cuts without excessive post-processing.
In industrial environments, fiber lasers display solid-state reliability while needing little maintenance, making them robust. The system’s overall reliability is greatly improved without the addition of consumable gases or external optical components, which increases the intervals between maintenance periods and decreases the system downtime. Together with these attributes, fiber lasers being power scalable up to 12 kw and beyond, makes fiber lasers the best choice for industries that deal with high volume, high precision, and reflective metals.
Energy requirements: CO₂ lasers versus fiber lasers across different metals
Cutting metals, fiber lasers generally need less power compared to CO2 lasers, particularly when cutting reflective metals like aluminum and brass. Fiber lasers are more energy efficient, converting higher electrical energy into laser output. For example, a CO2 laser that produces 5kW of laser power from a 25 kW electrical input will only require 14–15 kW with a fiber laser. Also, fiber lasers have better absorption rates for shorter wavelengths, effectively reducing electricity consumption when processing highly reflective metals. These factors make fiber lasers more cost and energy efficient for CO2 lasers when cutting metal types.
Can a 40W laser cut metal, and what are its limitations?
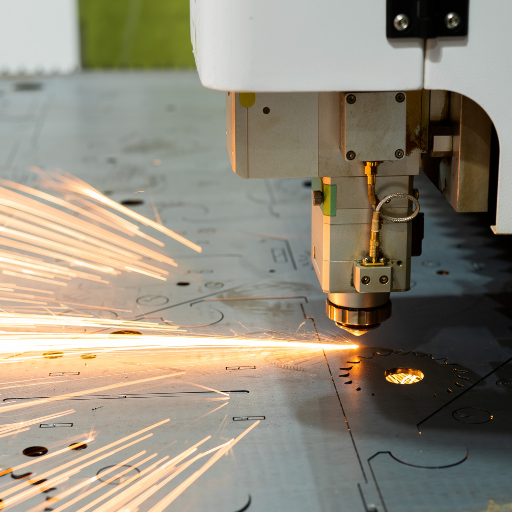
A 40W laser lacks the output energy to penetrate solid metal effectively. This type of laser is usually categorized as a low-power device as it is only designed to engrave wood, acrylic, and plastic. It can also mark metal surfaces, albeit with a specialized coating. In order to engrave metal, lasers with a power rating of 500W or more are more effective as they will easily depend on the type and thickness of the metal. Furthermore, a 40W laser cuts and etches slowly, lacks precision when used on hard materials, and cannot penetrate high-density materials. Fiber or CO2 laser systems are ideal for cutting metals, especially those with a higher power rating.
Studying the cutting potential of low-power lasers on thin metals
Lasers with lower wattages, like the 40W systems, are very limited in cutting thin metals. With the aid of coating or marking sprays, these types of lasers can engrave or even mark certain metals, but they typically do not have sufficient energy to remove material. That said, low-power lasers can engrave or partial cut metals like aluminum using other optimal conditions, including using very weak lasers with a power level of less than 0.5 mm. The accomplishment of such tasks takes great care and attention, as the settings need to be overly precise such as slower speeds, the inclusion of assist gases like oxygen to increase cutting ability, and multiple passes.
Other uses of 40W lasers in processing metals
Lasers with 40W of power have special marking sprays or coatings that can enhance their ability to surface mark and engrave metals. These lasers are useful in placing complex patterns, serials or barcodes in some metals and other high precision operations. Some of these lasers are also frequently used in cleaning or surface etching or other preparatory tasks for materials where only thin layers of material require removal. Moreover, 40W lasers can also be controlled and employed for artistic and exquisite metalworking by performing intricate designs on softer metals or plated surfaces.
Improving metal cutting efficiency with a new laser.
For someone using a 40W laser, exchanging it for a higher wattage model will drastically improve the range of metal cuts. Higher wattage means cutting power, energy output, and penetration depth increases, boosting the cutting speed. Better models typically have better beam quality, autofocus, and more advanced assist gas systems, leading to faster and more accurate cuts. By switching to a stronger laser, the user will be able to process more materials with greater thicknesses. Doing so will improve overall operational efficiency and quality.
How does laser power affect cutting speed and quality in metal fabrication?

The amount of power a laser emits dictates both the speed at which the laser cuts and the quality of the cut during metal fabrication. Higher-powered laser beams have higher energy intensity, cutting through materials and melting or vaporizing them at a higher rate. This lowers processing time and boosts productivity. In addition, higher laser power translates to better edge quality owing to reduced heat-affected zones (HAZ), which ensures clean cuts on thick or dense materials. On the other hand, the use of higher power settings must be well balanced since too much power can lead to material destruction and rough edges. Using the right power levels alongside correct focus and assist gas significantly improves fabrication precision and the overall quality.
Improved cutting speed and productivity due to higher laser power
Powering the laser beam allows for clearer precision visibility. The balance between speed and power determines the productivity level as well. The HAZ is not able to withstand higher laser powers when increased, therefore adjusting the productivity and cutting speed. This boost in power increases productivity cycle time while cutting rough or thick materials. On the contrary, extreme power can lead to hidden thermal effects which can be reduced by strategically increasing the speed settings, assist gas pressure and focus level alongside the power settings.
Power, speed, and cut quality trade-offs – How to achieve optimal results
On the achieving results part – power, speed, and cut quality tradeoffs is just not that simple. The cut energy needs to match the thickness of the material. Overheating or damaging the material is not an option. The same goes with the cutting speed. An equally balanced value must be maintained.
Effective strategies to reduce time spent cutting and make cuts with high quality efficient and effective
Impressive results from precision parameter control are how you maximize cutting speed without sacrificing quality. The first step is optimal laser power configuration; you need just the right amount of energy for an effective cut, but not enough to overheat and throttle damage the material. Increase focus cutting speed, but not the level with rough and uneven edges. Changing the type and pressure of assist gas also needs to be carefully calibrated because removing the molten material efficiently and quick will throttle edge quality if not set to the right levels. Focal position also needs careful tuning for the energy to be set in the right positin. All of these need regular updates to the variable parameters to ensure immaculate results are delivered.
What laser types and power levels are best for cutting thick metal?

Fiber and CO2 lasers are widely used because of their effectiveness and accuracy when cutting thicker metal. Fiber lasers are more effective than CO2 lasers when cutting reflective metals like aluminum and copper since they have shorter wavelengths and higher absorption rates. Even though CO2 lasers are less effective on reflective metals, they still work well in a broader variety of materials like thicker steels. For cutting thick metals, power levels of 4kW and above are recommended. Higher power enables deeper penetration and faster processing rates. The selection of laser type and power should consider the material properties, thickness, and desired cutting quality.
Cutting Thick Steel and Aluminum with High Power Fiber Lasers
High-power fiber lasers are praised for their efficiency and precision when cutting thick pieces of steel and aluminum. They are ideal for both cutting and welding thick pieces of steel or aluminum. High-power fiber lasers are classified as high-efficient lasers which function at about 1 µm, a range which allows for more absorption by reflective metals like aluminum and stainless steel. For example, a fiber laser with a power rating between 10 and 50 mm for steel and 3 and 30 mm for aluminum depending on the alloy, will allow effective cutting. Moreover, fiber lasers’ focus is easier to control, and with the addition of high beam quality, advanced cooling systems, and high spoke capacity, performance is greatly improved. Dross is reduced allowing for a cleaner cut. Additionally, using these systems with nitrogen or oxygen to assist the cutting process helps in removing the abundant molten material for precision and minimal thermal impact to the material.
Applications of thick metal cut Plasma cutters and High Power Lasers Differently
While plasma cutters should be compared with high-power lasers in thick metal applications, many significant factors should be considered for both. For one, Plasma cutters are cheaper and economically effective tools for steel and aluminum cutting with material thickness of up to fifty millimeters. They utilize an ionized gas jet to melt and remove materials. This process gives the fastest cutting speeds while operating at a cost effective level. Nevertheless, the precision of plasma cutters is not nearly as accurate as that of high-power lasers, as there is a wider kerf and more heat distortion.
The best cut edges and minimal post-processing are done using high-power lasers like fiber lasers. They work efficiently on stainless steel and aluminum, especially on aluminum 30 mm thick and steel 50 mm thick. Due to their narrow kerf width, reduced thermal impact, and ability to hand reflective metals provides an advantage over plasma systems. They can produce double the results than before. However, using laser systems requires high initial investments, leading to complex maintenance needs over time. The complexity and cost efficiency should be considered before choosing any of these methods. Each of them would solve different sets of issues.
Using Laser Technology to Achieve Clean Cuts on Thick Metal
When cutting thick metal with a laser, you need exteme optimization. First, the position of focus is critical, and you need to ensure that the cut produced isn’t cruel. Utilizing oxygen or nitrogen assists in improving cut quality as it helps transfer energy to the material while minimizing slag formation. Moreover, using a steady feed rate concerning the thickness of the material allows for a reduction in heat distortion. Lastly, when ununderstanded, regular maintenance of the laser cutting system, such as cleaning its lenses and ensuring nozzle alignment, greatly enhances its precision.
How can I determine the right laser power for my specific metal cutting needs?

Before dialing in the laser power to cut metal, it is essential to understand the material type, thickness, and cut quality desired. Higher laser power is usually required for efficient and clean cuts on thicker metals, while thinner materials can be cut at lower power settings. The manufacturer’s guidelines and suggestions should be consulted for more effective power usage. Different pieces can be configured for testing in order to find the best balance between speed, edge quality, and distortion due to heat. Furthermore, power usage can be enhanced and cutting accuracy increased for different metals with the use and employment of assist gases oxygen and nitrogen.
Evaluating the production volume and the requirements of metal cutting
Evaluating the metal cutting requirements starts with assessing the material type, thickness, and the quality of the cut for a given application. For example, carbon steel, aluminum, and stainless steel all have distinct properties that affect how the material is cut with a laser. Carbon steel is cut with oxygen assist gas to obtain sharp edges. In contrast, nitrogen assist gas is used to cut stainless steel and aluminum to avoid oxidation and ensure clean finish.
The production volume should directly define the efficiency and power level of the selected laser system. The most effective systems for rapid cutting speeds for high-volume production would be fiber laser systems with power output ranging between 2kW to 10kW, especially when used with thicker materials (for example, 10 mm or more). For lower volumes with thinner materials like those below 3mm, CO2 lasers with lower power ratings are enough to cut the materials with precision and without wasting energy. Throughput and cycle time considerations are the most important. These calculations of expected machine operation hours and required runtime per part can help select the most appropriate equipment for the work to be done.
Some important technical factors are the power of the laser (in kilowatts), the position of focus for the beam (to determine the edge accuracy), and the cutting rate (meters per second or millimeters per minute). To achieve consistent results, optimal focus, power density, and travel velocity must be ensured. Routine production lens cleaning and gas supply maintenance are also machine maintenance that can aid in accuracy and efficiency over prolonged production cycles.
Working Together with Manufacturers of Laser Cutting Machines for Personalized Assistance
When working together with manufacturers of laser cutting machines, it is important to provide as much information as possible on how the machines will be used. Make sure to specify what materials will be used, their thickness range, and the required cutting tolerances. Furthermore, outline the expected production volume and any other specific fabrication concerns, like complicated structures or fluctuating workloads. The manufacturers can help determine the best and most useful laser power and technology, whether fiber or CO2 lasers are best suited, and the cooling and gas supply auxiliary system needs. Also, ask about the necessary operating system software, after-sale care, and how the equipment will be looked after so that it remains functional and suitable for your goals in the long run.
Looking At Sufficient Expansion And Multi-Purpose Functionality In Laser Output Power Choosing
While setting the output power of the laser, one should consider future scaling possibilities and flexibility on selection as per application requirements. Choose a machine with adjustable power ranges to make sure a wider variety of materials and thicknesses are easily cut or engraved. High power cutting lasers are more efficient in cutting thick and hard materials, but lower setting should also be effective for tender jobs. Flexibility in range outputs enhances operational effectiveness and enables business expansion into new fields without purchasing new appliances. Systems with modular upgrades to maintain pace with the changing industry needs should be on top of the list.
Reference sources
Frequently Asked Questions (FAQs)
Q: How much power does a laser cutter need to cut metal?
A: The power requirements for a laser cutter to cut metal depend on several factors, including the type and thickness of the metal. Generally, for cutting metals, you’ll need a laser with at least 150-200 watts for thin materials, while thicker metals may require 500 watts or more. Fiber laser cutting machines are often used for metal cutting and can range from 500 watts to several kilowatts for superior cutting results.
Q: Can a CO2 laser cut metal effectively?
A: While CO2 lasers excel in cutting non-metallic materials, they are less effective for cutting metals compared to fiber lasers. CO2 lasers can cut thin metals (up to 1mm) with proper settings, but they struggle with thicker or reflective metals. For precise and efficient laser cutting of metals, fiber lasers are generally preferred due to their ability to cut through tough materials and provide better cutting results.
Q: What factors affect the cutting process and power requirements for metal laser cutting?
A: Several factors influence the cutting process and power requirements for metal laser cutting: 1. Type of metal (e.g., steel, stainless steel, aluminum) 2. Thickness of the metal 3. Desired cutting speed 4. Surface finish requirements 5. Laser type (CO2, fiber, or other) 6. Focused laser beam quality 7. Assist gas used 8. Power supply stability These factors determine the laser cutting power needed for optimal results.
Q: How does the thickness of the steel affect laser cutting power requirements?
A: The thickness of the steel directly impacts the laser cutting power requirements. Thicker steel will require more power to cut through effectively. For example, a 500-watt fiber laser might be able to cut 3mm mild steel, while cutting 10mm steel may require a 2000-watt or higher power laser. As the thickness increases, you’ll need a more powerful laser or may need to reduce cutting speed to maintain quality.
Q: What type of laser is best suited for cutting metal?
A: Fiber lasers are generally considered the best type of laser for cutting metal. They offer several advantages for metal cutting: 1. Higher absorption by metals 2. Greater efficiency 3. Ability to cut reflective metals 4. Faster cutting speeds 5. Lower operating costs Fiber lasers are well-suited for cutting various metals, including steel and stainless steel, and can handle a wide range of thicknesses.
Q: How does laser cutting power affect the quality of metal cuts?
A: Laser cutting power significantly influences the quality of metal cuts. Adequate power ensures: 1. Cleaner, more precise cuts 2. Reduced heat-affected zone 3. Minimal dross or slag 4. Ability to cut thicker materials 5. Faster cutting speeds Insufficient power can lead to incomplete cuts, rough edges, or increased heat damage. It’s crucial to match the laser cutting power to the specific metal and thickness for optimal results.
Q: Can laser cutters be used for metal engraving as well as cutting?
A: Yes, laser cutters can be used for both metal cutting and metal engraving. While cutting requires higher power to penetrate the material, engraving typically uses lower power settings to mark the surface without cutting through. Fiber lasers are particularly effective for metal engraving, offering high-quality, permanent marks. The laser head can be adjusted to focus the beam for either cutting or engraving tasks.
Q: How do laser cutting machines compare to traditional cutting tools for metal?
A: Laser cutting machines offer several advantages over traditional cutting tools for metal: 1. Higher precision and accuracy 2. Ability to cut complex shapes 3. No tool wear 4. Faster production for intricate designs 5. Reduced material waste 6. Non-contact process, minimizing workpiece distortion However, traditional cutting tools may still be preferred for very thick metals or in situations where the initial investment in laser technology is not justified.
Q: What safety precautions should be taken when using high-power lasers for metal cutting?
A: When using high-power lasers for metal cutting, important safety precautions include: 1. Proper enclosure of the laser cutting area 2. Use of appropriate eye protection 3. Adequate ventilation to remove fumes and particles 4. Regular maintenance of the laser machine and power supply 5. Training for operators on safe use and emergency procedures 6. Implementing safety interlocks and emergency stop systems 7. Proper disposal of waste materials 8. Following all relevant safety regulations and guidelines
Q: How can I determine the right laser power for my metal cutting needs?
A: To determine the right laser power for your metal cutting needs, consider: 1. The types of metals you’ll be cutting 2. The maximum thickness you need to cut 3. Required cutting speeds and production volume 4. Budget constraints 5. Available space for the laser cutting machine 6. Future expansion plans Consult with laser cutting machine manufacturers or experienced professionals to get specific recommendations based on your unique requirements and the materials you’re going to cut.