Used in various industries such as aerospace and custom fabrication, laser cutting is arguably the most accurate technique of mechanized manufacturing and versatile as well. The success of the laser cutting process is contingent upon the machine’s ability to carry out the design steps accurately while observing the set limits and tolerances. The limits of precision and tolerances are essential metrics that ultimately determine the dimensional quality and accuracy of the product. This article aims to break down the major aspects of laser cutting accuracy starting with how tolerances are set, what factors impact precision, and what systems on the market are available to improve accuracy from a reliability standpoint.. Understanding these concepts will help readers appreciate the reasons behind the unparalleled levels of detail achieved with laser cutting and its implications on practical uses and mass production.
What factors impact the accuracy of laser cutting?
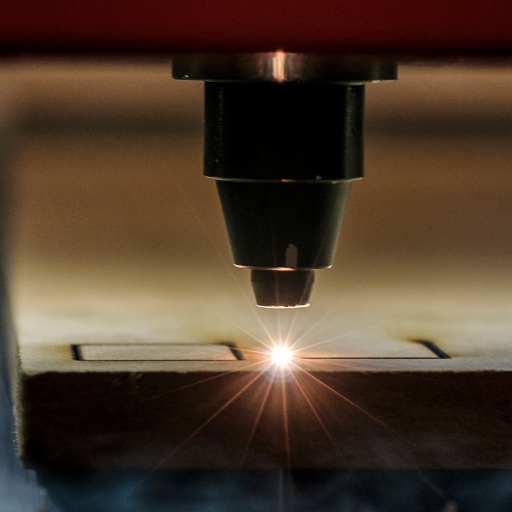
Several factors affect the accuracy of laser cutting. Material parameters such as thickness, reflectivity, and thermal conductivity are important in determining the quality of the cut. Furthermore, the power and wavelength of the laser also affect the precision which, in the case of thick materials, can be set to higher levels. Lens position and focus adjustment, machine calibration, and other maintenance activities are also essential for precision. The cutting process can also be affected by temperature and humidity. Finally, the perfection of the software in programming the path and speed of cutting guarantees constancy in the process and accuracy of operations.
In what ways does the size of the laser beam spot affect the precision of the cuts made?
The spot’s size, shaped like a laser beam, determines cutting precision as it determines the width of the cut and how much energy is delivered to the material. A smaller beam results in focusing more power towards the center. This increased power allows for finer detailing and cutting features. The width of kerf produced will also be lower. However, more energy needs to be focused to achieve more minor kerf results. Factors such as the focal length of the lens and the collumation of the beam greatly affect this. For example, a focus lens with a shorter focal length will produce a smaller laser spot, while the beam parameter product (BPP) guarantees consistent energy. Depending on the type of optics used, a typical industrial laser might achieve a spot size ranging between 0.01 to 0.2 milimeters. This directly affects the level of detail and the sharp edges that can be achieved while cutting. Adjustments to spot size must also consider material type and thickness to ensure optimal cutting performance without efficiency loss.
The Relationship Between the Two: Accuracy, Laser Power, and Cutting Speed.
Cutting accuracy heavily relies on two factors: cutting speed and laser power. High laser power can easily penetrate materials because it has the energy needed, but the power must always be adjusted precisely to avoid material deformation and overheating issues. Slow precision cuts are also determined by cutting speed, but too much cutting precision can result in poor quality cuts or fading cuts. A delicate dance balancing both parameters, cutting speed and laser power, is required. It must also be catered to the material type and thickness and should always ensure efficiency and surface quality is optimal.
What’s the level of precision of different classses of laser cutters?
CO2 lasers have a very high degree of accuracy and are commonly used in cutting non-metallic materials where clean edges are required, like acrylic and wood. Fiber lasers, however, can outperform others in cutting metals like thin sheets of steel because they have better energy efficiency and focus. Finally, diode lasers have the least power but are useful for delicate work on soft materials. The precision and type of material needed for the project is what dictates which laser type should be used.
What are typical tolerances in laser cutting?
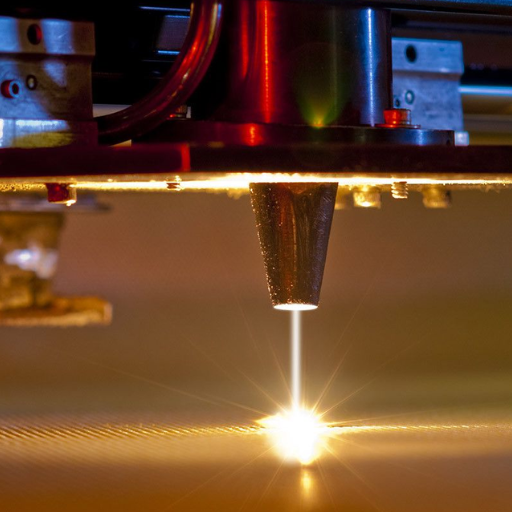
The tolerances in laser cutting depend on material type, thickness, and the performance of the laser cutter used. Most industrial-grade laser cutting machines have standard tolerances between +/- 0.1 to 0.2 mm. Generally, thinner materials like sheet metal have tighter tolerances because of less thermal distortion or warping,while thicker materials will often have looser tolerances. Additional variables such as machine focus, kerf width, and machine stability also affect the precision. Proper functioning of the machine and maintenance significantly affects the tolerances that can be achieved in various cuts.
Understanding dimensional accuracy in laser cutting
Kerf width, which is controlled by the diameter of the beam and its settings, is critical towards achieving high accuracy. In laser cutting, it is significantly affected by the laser beam’s strength, the material’s properties, and the laser cutter’s settings. Accuracy of the beam penetration alongside the potential thermal distortion provides further complications when accounting for the material’s properties, like density and thickness. The more complicated the cuts, the more you have to worry about the dimensional variations. Systems that can precisely focus the beam and contain high quality optics are the best at performing advanced cuts.
What are the difference in tolerances when using a laser cutting machine compared to other methods?
Because of its focus precision, laser cutting tolerances typically outdo many of the ordinary cutting patterns such as plasma cutting or mechanical saw cutting. Typical industrial laser machines have settings with cutting tolerances of ±0.003 inches (±0.075 mm). This largely hinges on the material type and the machine setup. On the other hand, plasma cutting often provides tighter tolerances than 0.5-2.5 mm (±0.02–0.1 inches), but this is significantly dependent on the material’s thickness and its arc stability. Just like lasers, mechanical cutting techniques such as water jet or sawing offer high precision too but more often than not, do no achieve the same repeatability and edge quality as laser cutting.
Standard technical parameters for laser cutting that dictate cutting tolerances include the kerf width (for laser cutting, 0.1–0.5 mm based on the material, diameter, and focus settings) and stability of the laser power output which will maintain constant distribution of the thermal energy. Compared to mechanical techniques, where tooling wear can certainly lower precision, laser cutting really has no physical tool wear, which allows for enhanced tolerances.
What precision is possible with laser cutting technology?
Depending on material type, thickness, and machine calibration, laser cutting technology tolerances range around ±0.075 millimeters, which is approximately ±0.003 inches. This accuracy is achieved with the help of a focused laser beam, which creates a narrow kerf while simultaneously minimizing heat distortion. Automated sensors, additional beam control, and more precise cutting parameters incorporated in advanced systems further increase the precision of the cut. Such factors lead to uniformity in cuts and replicated quality even in complex designs and sophisticated geometries.
How can you improve laser cutting accuracy?
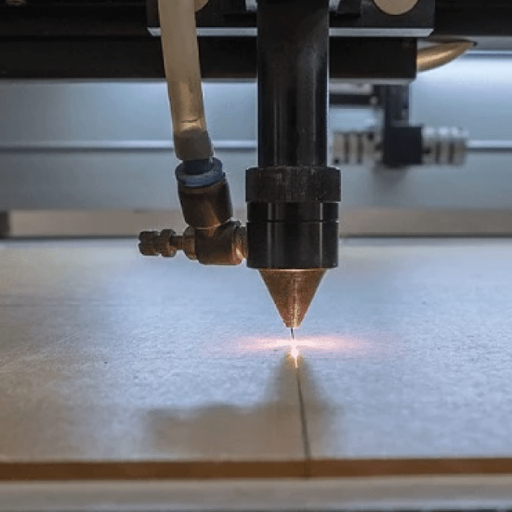
Accuracy in laser cutting can be improved by optimizing the use of high-end technologies and software while paying attention to specific details such as laser power, speed, and focus settings. However, proper machine calibration and ensuring that the machine is regularly maintained is critical since adjutants that misalign optics or worn components can make precision challenging to achieve. Additionally, using high-quality materials without surface imperfections and consistent thickness are also necessary for ensuring optimal accuracy and the best results possible. Fine-tuning parameters such as laser power, speed, and focus are paramount to enhance accuracy even further. They allow the machine to perform optimally depending on the material type and its design complexity. Furthermore, modern technologies such as real-time monitoring sensors and automated height adjustment systems account for variations in material flatness or thickness during operation. This greatly improves accuracy, making incorporating advanced solutions necessary for optimal results. By integrating these approaches, the precision of laser cutting is guaranteed to improve drastically.
What are the best practices for achieving precise cuts?
In order to achieve accurate cuts, the following factors must be taken into consideration. The first has to do with the selection of the type of laser that is appropriate for the material being cut. For example, CO2 lasers work well with non-metals such as wood, plastics and acrylics, while fiber lasers work best when cutting metals because of their wavelength. The other set of criteria involves optimization of power, the speed of the cutting and the laser focus position. For example, higher laser power is appropriate for cutting thick materials; however, the speed must be regulated to avoid burns or distortion. Also, adjusting the focal point at a distance equal to or slightly less than the material thickness guarantees a finer cut.
The preparation of materials is crucial as well. Selecting clean and flat sheets free from any forms of warping or impurities enhances the repeatability of cutting processes. Also, using high caliber assist gases like oxygen for carbon steel or nitrogen for stainless steel and plastics helps in edge retention and oxidation reduction. Furthermore, the cutting nozzle must be free of obstructions and correctly disposed to allow proper flow and uniformity of the laser beam. Last, but not least, the innovative software tools can improve the cutting path and eliminate excessive movements that may cause high thermal strain on the object. All of them, in concert, help to perform cutting laser with a very narrow tolerance.
How do cutting parameters influence accuracy?
The setting of cutting parameters greatly influences the cutting accuracy of the laser processes because edge quality, kerf width, and dimensional accuracy are directly affected. Laser power, cutting speed, assist gas pressure, and focus position, among other parameters, need to be calibrated according to the material’s properties. Overpowering may cause overburning while cutting at low speeds may cause unclean cuts. On the other hand, the smoother edge finishing of lower thermal distortion can also be a product of slower cutting speeds. Assist gas pressure, however, is crucial in removing the molten material; therefore, it needs to be set to the required amount so that edge oxidation does not occur. Finally, the proper setting of focus position helps achieve the maximum intensity of the laser beam, which is intended to minimize deviations. Continuous monitoring and maintenance of these criteria improves accuracy and is repeatable for many cuts.
Which maintenance procedures allow for a laser cutter to operate at the highest precision possible?
I focus mainly on cleaning and calibration to guarantee that a laser cutter works with utmost precision. I often clean the lens and mirrors to eliminate dust and dirt that can block the laser beam. Periodic alignment of the optics is done to ensure that the beam is accurately focused. I regularly check and replace poor performing, consumable nozzles and filters as required. Furthermore, these actions enhance performance. Overheating is avoided by monitoring and adjusting the cooling systems, while more advanced software and firmware updates will reduce the risk of overheating. Consistent checking of the drive system and mechanical parts lubrication further enhances accuracy and reliability, as well as the practices above.
Which materials offer the most accurate laser cutting results?
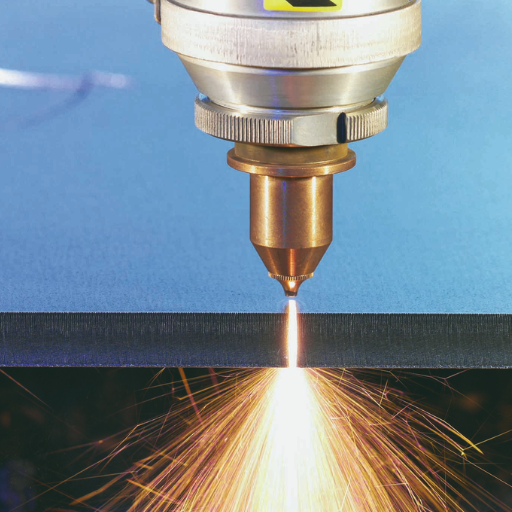
The best results for accuracy in laser cutting are achieved with materials such as acrylic, wood, stainless steel, and aluminum. Acrylic is most popular due to its clean cuts and very detailed edges. Softer wood types like balsa and birch plywood cut very cleanly and scorch minimally when properly selected and prepared. Stainless steel and aluminum, like other metals, offer high cutting accuracy due to their uniform density which is compatible with laser cutting technology.
How does laser cutting accuracy differ between metals and non-metals?
There is a difference in the accuracy of laser cutting by metals and non-metals, owing to the difference in material properties, such as density, thermal conductivity, and melting points. Denser metals like stainless steel and aluminum, allow precision cutting since they absorb the laser energy evenly. Non-metals can also be cut accurately, but precise adjustments are necessary since they can char or melt with laser energy. A delicate edge quality may also be compromised. In all cases, proper calibration and an understanding of the specific material is required for effective laser cutting.
What are the precision capabilities of fiber laser cutting for sheet metal?
The precision capabilities of fiber laser cutting may be unrivaled for sheet metal. Focusing laser beams allows fiber lasers to achieve an accuracy in cutting parts of ±0.03 mm while repeatability is done at ±0.01 mm. Because of the heat-affected zone’s restriction, accuracies such as these are achievable. The precision is attributed to the high power density, focus of fiber lasers, and advanced motion control systems. The technical parameters of fiber lasers for cutting fiber sheets include a beam quality (M²) of ≤1.2 while power output can be as low as 1 kW or as high as 12 kW. The cutting speed also varies due to material thickness, being approximately 35 m/min for thin sheets. The parameters provided ensure that ease of processing sheet metal fibers does not compromise edge quality.
In what ways do CO2 lasers accurate to different materials?
The performance of CO2 lasers with metal, plastic, wood, and other organic materials is notable. The accuracy is within the range of ±0.1 mm Accuracy in cutting is limited only by the equipment and material grade. The beam quality and power output helps to determine the accuracy of the laser. Typically, standard systems have a power output between 20 W and 1 kW. Assistive gases like oxygen and nitrogen also help to increase accuracy. CO2 lasers provide an economical option for cutting non Metallic and thicker items, but they do not outperform Fiber lasers in precision for ultra-thin sheet metal cutting and complex shapes.
How does laser cutting accuracy compare to other cutting methods?
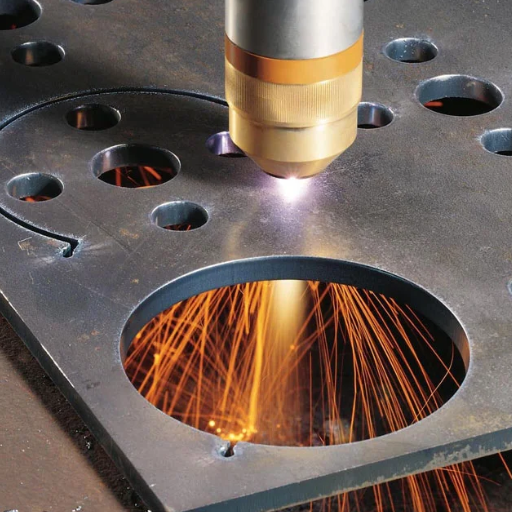
Laser cutting is regarded as one of the most accurate forms of machining, with tolerances of around ±0.1 mm depending on the type of laser used. Its accuracy is superior to that of plasma cutting or waterjet cutting due to the advanced automation, energy beam focus, and the types of machinery used to perform the processes. Though plasma cutting is very effective for cutting thick metals, it typically has a broader kerf and is less accurate. While waterjet cutting is able to cut with high accuracy, it is slower than laser cutting. Furthermore, it is less useful for metals that need to be processed quickly. Even with these competing methods available, laser cutting is able to maintain its superiority due to its ability to cut highly complex geometries without substantially distorting the material.
Laser cutting vs. plasma cutting: A precision comparison
Laser cutting is better than plasma cutting when only precision is considered, due to its narrow and focused energy beam. With a laser cutting machines, the width of the cut (kerf) may be as narrow as 0.1 mm, with tolerance often achieving ±0.1 mm. This works best for laser-cutting intricate patterns and designs. With plasma cutting, the kerf width is usually between 1.5 mm and 3 mm, with tolerances of ±0.5 mm to ±1 mm. Although it is not very precise the kerf width is thick, it is good enough for applications with thicker materials.
Furthermore, laser cutting produces very low amounts of heat-affected zones (HAZ), which ensures edges are cleaner and materials are less warped. Plasma cutting, on the other hand, has a larger HAZ due to increased thermal output. For very thin and delicate materials as well as highly detailed designs, laser cutting is more precise and allows better dimensional accuracy while plasma cutting works best when low cost and speed is an issue and for thicker metals.
In what ways do laser cutters surpass mechanical cutting techniques?
- Precision and Accuracy: Traditional mechanical cutting methods are less precise than laser cutters. Laser machines often make kerf widths of 0.1 mm with tolerance levels of about ±0.1 mm. Sawing or milling, on the other hand, makes deeper cuts than laser cutters, which comes alongside low tolerance levels. This poses problems for more intricate designs and detailed work. Because of this, laser machines are far superior.
- Material Versatility: While one may argue that laser cutting is less customizable compared to metals, plastics, wood, or ceramics, it can in fact outperform more conventional methods. Mechanical cutting methods face serious challenges with material compatibility since brittle or harsh products suffer severe tool wear or even fracturing.
- Speed and Efficiency: Compared to mechanized methods, laser cutters excel with their faster working speeds, which dramatically reduce the time needed for production. Unlike laser cutters, physical contact methods such as mechanical cutting are significantly slowed down because of the need to maintain tool durability and manage materials.
- Edge Quality: Laser cutting edges need almost no finishingc processes, as they are clean and smooth. This is possible because of laser’s focused energy beam and the lesser degree of mechanical interference. In comparison, mechanical cutting tends to be rough around the edges. It carries over the parts of cutting tools, including burrs, which brings in the need for additional finishing processes including sanding or deburring.
- Tool Wear and Maintenance: Easer cutters are not contact tools, meaning minimal wear on the tool. This reduces maintenance costs in the long run. Unlike laser cutters, mechanical cutting tools suffer from excessive wear, which leads to the need for regular load and replacement, in addition to recalibrating the tool.
- Heat-Affected Zones (HAZ): Laser cutting typically results in smaller heat-affected zones, meaning less warped material, and maintains the integrity of heat-sensitive components. In contrast, mechanical cutting methods do not subject the material to thermal effects; however, some degree of mechanical stress will be induced, which can lead to distortion or uneven cuts in some situations.
- Automation and Integration: Integrating with CAD/CAM software and modern production line automation is extremely easy with laser cutting systems. This eases incorporation into ready-perfected production lines. On the other hand, mechanical cutting processes can be automated, too, although not to the same degree of accuracy and finesse when programmed cutting is concerned.
What makes laser cutting technology offer faster and more accurate results?
Laser cutting technology is vital in many industries because of its speed and precision. A high energy beam is capable of taking a shot at a beam of focus and can heat it up to extremely high temperatures which will enable clean cuts to be performed. Additionally, since these cuts are done through a concentrated beam of heat as opposed to traditional tools, there will be a significantly lower amount of material wasted. It is also important to mention that by using CNC (computer numeric control) lasers, designers can make highly intricate designs with unbelievable accuracy and repetition. Also, no physical tools come in contact with the material, which means they will not undergo wear and tear, thus improving efficiency. These characteristics make laser technology ideal for great precision and rapid speed applications.
What are the limitations of laser cutting accuracy?
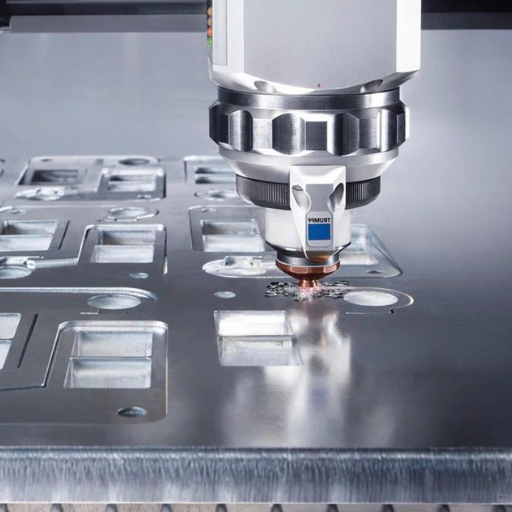
Several components can impact the accuracy of a laser cut. The type of material used for cutting is primary as well. Reflecting materials like aluminum can scatter the laser beam and subsequently decrease the accuracy of the cut. Another limitation is the thickness of the material. Lasers cut extremely well through thinner materials while cutting thicker sheets tends to cause difficulty maintaining accuracy due to beam divergence. Furthermore, other factors like environmental change, power output fluctuations, and improper calibration of the laser system can lead to inconsistencies. Finally, while cutting heat-sensitive materials, the edge quality and details of intricate patterns deteriorate due to heat distortion.
Finding the balance between the cutting accuracy and speed
The balance between cutting speed and accuracy dances between efficiency and precision. Emphasizing speed allows the laser to make precise cuts in intricate and detailed designs, but at the cost of accuracy. On the other hand, a slower speed allows for greater cut precision and cleaner edges; however, it can distort the material if the slow speed generates too much heat. This trade-off can be optimized through a deep understanding of the material properties and setting the machine parameters to hedge the project’s needs.
To what extent does thickness affect precision in cutting lasers?
In laser cutting, thickness of the material directly correlates to the level of precision that can be achieved. Thinner materials tend to provide higher levels of precision as the depth of laser penetration is less, and the heat-affected zones (HAZ) are practically non-existent. For example, in stainless steel metals stainless steel, the focus point of the laser beam is less than 1 mm, which further translates to lower kerf widths and finer edges. But as the thickness increases, the precision achieved in cutting reduces because wider kerfs and larger HAZ are created as more laser power is required in deeper penetration cutting.
To achieve this, machine parameters such as laser power, cutting speed and focal point should be set appropriately. Regarding thinner materials, lower, faster cut speeds tend to be the most ideal. In thicker materials, above 10 mm, slower feed rates help intrude deeper, while lacking edge quality. By aligning parameters, with the materials properties, such as absorption rate and thermal conductivity, one can ensure precision is maintained within tolerable ranges.
What are the difficulties faced while upholding the accuracy of detailed designs?
Upholding accuracy for detailed designs is problematic because of the complexities involved in precision work. One primary issue is the alignment and measurement of finer details, often required with highly sophisticated equipment and well-done calibration. Moreover, inconsistencies in the material can lead to inaccuracies in capturing the original requirements, which calls for intensive quality control procedures. In addition, other issues such as changes in working conditions or even the depreciation of the equipment can negatively affect the accuracy of the designs produced, thereby necessitating constant monitoring and balancing adjustments.
Reference sources
Frequently Asked Questions (FAQs)
Q: How accurate are laser cutters compared to traditional cutting methods?
A: Laser cutters are extremely accurate compared to traditional cutting methods. The level of accuracy achieved by a laser cutting machine is typically within 0.1mm or less, making it an ideal choice for precision laser cutting in metal fabrication and other industries.
Q: What factors affect the accuracy of a laser cutter?
A: Several factors can affect the accuracy of a laser cutter, including the type of laser (e.g., CO2 laser cutter, fiber laser cutting machine), material being cut, laser settings, condition of the laser head, and the quality of the CAD software used. Environmental factors such as temperature and vibration can also impact precision.
Q: How does the accuracy of a fiber laser cutter compare to a CO2 laser cutter?
A: Fiber laser cutters generally offer higher accuracy than CO2 laser cutters, especially when it comes to metal cutting. Fiber lasers can achieve tighter tolerances and offer faster cutting speeds, making them ideal for high-precision applications in metal fabrication.
Q: What are some tips for improving laser cutting accuracy?
A: To improve laser cutting accuracy, consider the following tips: use high-quality CAD software, ensure proper material fixation, regularly maintain and calibrate your laser machine, optimize laser settings for each material, use a stable work surface to minimize vibrations, and consider using a fibre laser cutter for metal cutting applications.
Q: How does material thickness impact laser cutting accuracy?
A: Material thickness can significantly affect the accuracy of laser cutting. Thicker materials may require multiple passes or higher-powered lasers, which can impact precision. Generally, thinner materials are easier to cut accurately, while thicker materials may require more specialized techniques to achieve supreme accuracy.
Q: What role does software play in laser cutting accuracy?
A: Software plays a crucial role in laser cutting accuracy. High-quality CAD software allows for precise design and conversion of files for laser cutting. Additionally, advanced laser cutting software can optimize cutting paths, adjust laser settings automatically, and compensate for material variations, all of which contribute to improved accuracy and precision.
Q: How do laser cutting services ensure consistent accuracy across projects?
A: Professional laser cutting services maintain accuracy by employing skilled operators, using well-maintained and calibrated equipment, implementing quality control measures, and leveraging advanced software. They also stay updated with the latest developments in the world of laser cutting to offer the best possible accuracy and precision to their clients.
Q: Can laser cutters achieve the same level of accuracy for both cutting and engraving?
A: While laser cutters are known for their accuracy in both cutting and engraving, the level of precision can vary. Laser cutting typically achieves higher accuracy due to the complete separation of material. Laser engraving can also be highly precise, but factors such as material properties and depth of engraving can influence the final accuracy.
Q: How does the accuracy of a laser cutter compare to other precision manufacturing methods?
A: Laser cutting offers exceptional accuracy compared to many other manufacturing methods. It can achieve tolerances comparable to CNC machining for many applications. In some cases, especially for intricate 2D designs, laser cutting can even surpass the accuracy of traditional machining methods, making it a preferred choice for precision manufacturing.