Now a favorite in residential and industrial drainage applications, corrugated high-density polyethylene (HDPE) pipe is unmatched in its efficacy and versatility. Durable and economical, HDPE pipes offer the best performance in stormwater, wastewater, and other fluid conveyance systems. This article will elaborate on the fundamental attributes of the corrugated HDPE pipe, what gives it an edge over other traditional materials, and the wide scope of its use from single-home landscaping projects to large-scale infrastructural systems. Learning HDPE’s technical properties and practical utility will allow readers to understand why it has become the material of choice in varying environments.
What is Corrugated HDPE Pipe and How Does It Work?
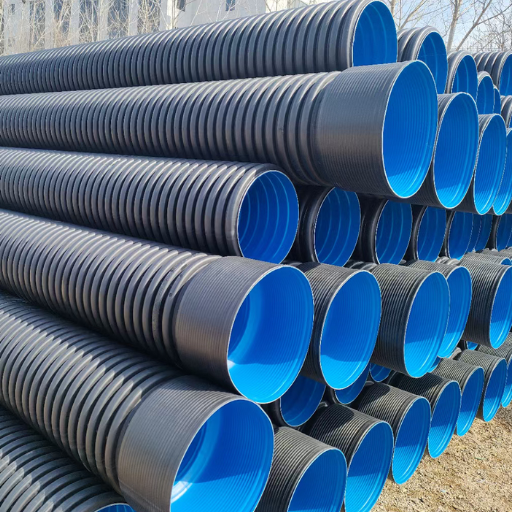
Quickly Dissipating HDPE pipes are light in weight, easily pliable and have ridges on the outer surface. The ridged surface provides better durability while the inner smooth surface ensures a rapid water flow. Being made precisely from high-density polyethylene allows it to transport water while being tough as well easily. Quick dissipating pipes find application in managing storm weather, drainage of agricultural lands, and infrastructural development in urban areas because of their durability. They are not corroded or easily damaged by chemicals, ensuring long term use in varying conditions. Heavy-duty flexible pipes are regularly used as corrosion-resistant, wear-resistant, and chemical-resistant pipes.
Initial Description of Corrugated HDPE pipe
The structure has one inner and one outer layer. The latter is smooth, while the one closer to the outer side is corrugated. Both of these layers have separate functions. While the inner layer is smooth to reduce friction and ensure better water flow, the outer layer is corrugated to give it better structural strength and allow it to be more flexible under pressure from soil and people walking over it. This variation in layers allows the pipe to function under extreme operational and environmental conditions easily.
Advantages of Using High-Density Polyethylene (HDPE)
High-density polyethylene (HDPE) boasts major benefits for various applications due to unique material properties. First, HDPE has an impressive strength-to-density ratio which helps it maintain structural integrity while remaining lightweight. In addition, this makes it easy to handle and install. Moreover, it has exemplary chemical resistance and enduring exposure to various substances, including acids, alkalis, and salts, making it valuable in extreme environments. HDPE guarantees longevity under mechanical stress, as it has a tensile strength of 21 to 37 MPa. Its low friction coefficient, approximately 0.03 to 0.05, increases the flow efficiency in piping systems. This friction reduction decreases energy costs over time.
Furthermore, HDPE is outstandingly resistant to UV radiation and temperature changes. It can function effectively within a temperature range of -40°F to 140°F (-40°C to 60°C) . Combined with the fact that HDPE is a recyclable material and environmentally friendly, these attributes make it the ideal construction material for agricultural and industrial infrastructure.
The Role Worse Materials Is Toughening The Performance Of HR Pipes
Due to its unique performance features, pipes have received one of the highest indexes of corrugation. Soil pressure, which is external to the ribbed design, is transferred to a larger area. Therefore, structural resistance to deformation improves, and the durability under compressive stresses is achieved for many years. Corrugated pipes exhibit much higher stiffness ratings, such as Ring Stiffness Constant or Ring Flexibility, which is essential for strenuous load tolerance applications. The spaced grooves permit pipes to flex more to accommodate ground movements or thermal expansion without losing functional integrity. The US Department of Transportation states that the lightweight nature of structures also simplifies transportation and installation and reduces overall project costs. These combined strength, robustness, and adaptability characteristics make these pipes perfectly suited for versatile applications.
What Are the Advantages of Using Corrugated HDPE Pipe for Drainage?

The corrugated HDPE pipes benefit drainage applications due to their durability, affordability, and effectiveness. Corrugated HDPE pipes were proven to resist chemicals, abrasion, and corrosion, ensuring long-term reliability in various environments. Being lightweight and cheaper makes construction transportation much more efficient, reducing overall equipment, labor effort, and cost. Furthermore, the flexible structure of HDPE pipes enables them to endure soil and ground movement without cracking or breaking. Moreover, the smooth interior surface helps increase hydraulic efficiency and reduces the risk of blockages. All these factors combine making them the best possible choice for sustainable and efficient drainage systems.
Better durability and service life than standard materials
When put up against traditional materials such as concrete or metal, it is clear that Corrugated HDPE pipes are far more durable and last longer. Its high denial polyethylene composition is stress resistant to things like UV radiation, chemicals, and extreme temperature changes. In contrast to metallic pipes, which rust or corrode over time, HDPE pipes have a much longer life expectancy because of the superior structural integrity maintained in harsh environments. For example, technical benchmarks suggest that HDPE pipes have a lifespan of approximately 100 years under normal conditions. Moreover, HDPE’s strength and resistance to the wearing away and fracturing increases their long-term efficacy which, in turn, significantly lessens the frequency of maintenance and replacements needed. Because of these reasons, modern drainage systems are much more reliable and efficient.
Effective fight against corrosion and abrasion
Corrugated HDPE pipes have remarkable efficiency because of their high-performance materials. The corrosion resistance originates from the high density polyethylene high.It is chemically inert, which allows for compatibility with a variety of substances like acids, bases, and salts, which makes it suitable for both industrial and drainage uses. They are also capable of enduring abrasion, and tests show that minimal material will be lost when exposed to high velocities of abrasive particles.
Their tensile strength, which ranges from 22 to 37 MPa, is a particularly relevant technical feature owing to the robustness under stress. Moreover, they are flexible enough to be deformed without fracture, so elongation at break can reach more than 600%. This enables them to thrive in fluid and shifting surroundings. HDPE pipes prove to have low thermal conductivity, about 0.45 W/m.K, as well which helps relieve stress induced by temperature. These factors combined position corrugated HDPE pipes as a superior engineering choice for long-lasting infrastructure.
Easy to handle and install – a design makeover
There are very few materials that can be considered as suitable alternatives to HDPE pipes and their corrugated variety excels with an especially low weight. This helps with transportation, handling at the site, and even the installation. Compared to standard materials like concrete and steel, these reduce the project’s timeline and costs due to the lesser machinery requirements. Implementations in remote or difficult-to-reach areas with heavy equipment aid construction and combat easily accessible countryside. In addition, the flexibility offered by these pipes allows them to be imposed in curved or uneven trenches without any additional efforts or alterations in the installation. In tandem, these features increase work efficiency on site while preserving the structure’s integrity after installation.
How Does Corrugated HDPE Pipe Compare to Other Drainage Solutions?
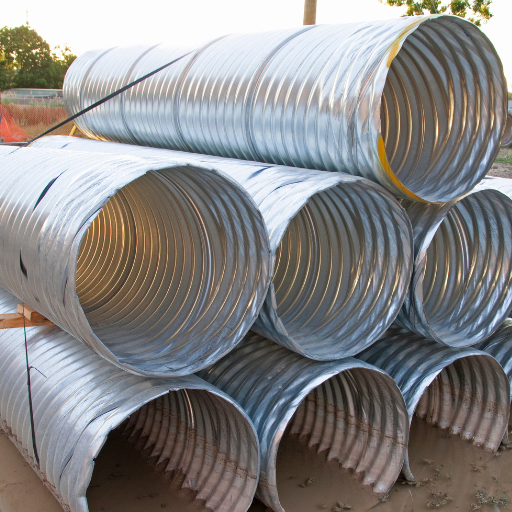
Because of its flexibility, strength, and internal and external corrosion resistance, corrugated HDPE pipes have better drainage solutions than most traditional options. Unlike concrete pipes, HDPE options are lightweight, making transportation and installation significantly more efficient. Additionally, hydraulic resistance is nearly absent in smooth walled pipes, unlike corrugated metal pipes, which means that flow capacity is maximized. Through temperature extremes and soil movement, HDPE works great because it is flexible and has strong joints, so the likelihood of leaking or structural failure is minimized. All these features make it economical and require less maintenance for numerous drainage functions.
Corrugated HDPE Pipe versus Reinforced Concrete Pipe (RCP)
Performance, expenses, and area of use compatibility between reinforced concrete pipe (RCP) and corrugated HDPE pipe (CHDPE) are relative extremes. RCP is popular for its extremely high strength and load-bearing ability, enabling use in places with many traffic movements like highways or airports. On the other hand, RCPs have the downside of being cumbersomely heavy, resulting in longer and more expensive projects since specialized transportation and installation equipment is required. Furthermore, unless protection liners are used, RDP is known to worsen in conditions containing acid and corrosion, which increases operational maintenance.
Its polyethylene composition makes corrugated HDPE pipes free from rusting and chemical attacks. These characteristics enable its use in processes involving harsh effluents or environments containing fluctuating pH levels. Because it is lightweight, it can be installed quicker and does not need heavy machinery, which reduces labor costs. Moreover, the material’s flexibility helps it endure shifting soil without cracking, which makes it last longer in unstable conditions.
In terms of hydraulic performance, smoother interior surfaces and higher flow rates are characteristic of HDPE pipes, which means lower Manning’s coefficient values (n=0.009-0.015 for HDPE; n=0.012-0.015 for RCP). Also, HDPE pipes are available in long sections, which makes them easy to install without joints, this minimizes the chances of leakage or failure over time. RCP may be preferred for extreme load applications, but HDPE pipes are cost-effective and low maintenance for other standard drainage systems.
Advantages over corrugated metal pipe (CMP)
HDPE pipes, unlike corrugated metal pipes, have greater advantages concerning CMPs. This is because HDPE is not easily affected by corrosion. CMP is damaged when there is a long term chemical and moisture exposure because it lacks adequate protection. However, HDPE is more durable than CMP in high temperatures and hostile conditions. Moreover, it also lasts longer. Because of the low roughness of HDPE pipes, energy consumption and the water flow draft are decreased because of increased hydraulic efficiency. HDPE is easier to use since it is lighter and flexible compared to the black and stiff CMP. These features increase the productivity of HDPE, making it suitable for many piping and drainage problems.
Differences between single wall and dual wall HDPE pipe
Single and double walled HDPE pipes serve different purposes regarding their construction features and ability to perform hydraulically. Unlike dual-wall HDPE pipes, single-wall HDPE pipes come with a rough surface and easy-to-use design, which makes them perfect for hand use and increases agricultural drainage and residential usage without being concerned about added weight. The amount of flow produced is lower than dual wall HDPE pipes due to the high friction single wall pipes face.
The dual-wall HDPE pipes have a corrugated outer layer for structural strength, while the inner layer is smooth for better hydraulic performance. This enhances the load bearing and the flow efficiency, which makes it suitable for heavy-duty applications like stormwater management, highways, and large-scale drainage systems. Dual wall pipes usually have a greater stiffness rating (The Structural standards like ASTM F2648 and AASHTO M294 often apply) so they can tolerate heavier soil loads along with some external pressure. Now, choosing between those options depends on the specific project demands, like the actual soil conditions, the desired flow rate, and the weights they will expect.
What Are the Different Types and Sizes of Corrugated HDPE Pipe Available?

Corrugated HDPE Pipes are created and stocked in various types and sizes to accommodate different uses and applications. They have been grouped based on their intended use and wall structure. Single wall pipes can be produced within smaller diameters that range between 3 to 24 inches and are used in agricultural drainage and light residential activities. Dual wall pipes are made in larger diameters ranging from 4 to 60 inches or more for stormwater systems requiring higher load capacities and more efficient water infrastructure management. Moreover, other custom sizes or fittings are also available for special applications. The availability of sizes and types will depend on meeting the industry standards provided in the ASTM and AASHTO. These standards guarantee that the needed strength is met and consistency is ensured across various projects.
Single wall corrugated HDPE pipe specifications
Pipes with a single wall have a smooth exterior surface and a spiral groove within. They are lightweight, flexible, and versatile, making them useful in constructing water pipelines as these structures overcome undue pressure. Their wall thickness ranges from 50mm to 600mm and HDPE pipes come in widths between 75 mm and 600 mm. Pipes with a diameter of 3 inches are also popular for agricultural drainage and leachate collection purposes. Because they are lightweight, high in strength, and flexible, they are easy to install. Being chemically inert, these pipes will not undergo hydrolysis under UV or B irradiation. In addition, they are easily transportable. Because of these factors, single walled corrugated pipes make great options for any drainage solution.
Ready diameters and lengths for different uses
Single-walled corrugated HDPE pipes are offered in many varieties of diameters and lengths to suit different needs. Diameters usually range from 3 to 24 inches, although larger sizes can be made to fit the project’s requirements. These pipes are produced in coils with standard lengths of 100 to 500 feet for smaller diameters while larger sizes are made in straight lengths of 10 to 20 feet. These size variations meet needs for agricultural drainage, stormwater management, and underground water conveyance. These pipes are also highly durable and can be installed in different environmental conditions such as open trenches or even subsurface layering. Technical parameters such as strength, longevity, and resistance to external factors also make them efficient for long-term operational performance.
How HDPE pipe extrusion machines affect product variety
The HDPE pipe extrusion machines are essential for producing different product variants due to their accuracy and flexibility in manufacturing. These machines allow the manufacture of pipes of different diameters, wall thicknesses, and lengths to suit various applications. Technical parameters that are set during extrusion such as extrusion pressure, melt temperature, and screw rotational speed all have a bearing on the pipe’s dimensional accuracy and surface finish. In addition, advanced machines are provided with automated control and calibration systems which reduce errors during production and guarantee compliance with industrial standards like ASTM D3350 regarding polyethylene piping materials. These systems can also incorporate co-extrusion and multi-layer pipe structures to increase strength and chemical or thermal resistance. This means extrusion machines can keep up with the demand for specialized HDPE components from municipal and industrial applications.
What Are the Environmental Benefits of Using Corrugated HDPE Pipe?

Like other forms of corrugated pipe, corrugated HDPE pipe has significant environmental benefits because of its long service life, light weight, and ability to be recycled. Because of the long service life of the pipe, resource consumption is significantly lowered as the amount of times the pipe needs to be replaced becomes infrequent. This also means a reduction in emissions, energy usage from transportation, and the installation of pipes. Additionally, numerous corrugated HDPE pipes are produced from waste materials, which positively impacts the environment. Wastes are not only reused but also lowered the total pollution produced. Their lightweight construction helps reduce emissions further. The containment of these pollutants helps achieve infrastructure sustainability and prevent contamination. In addition, the pipes are resistant to corrosion and chemicals, ensuring reliability in waste management systems.
Use of Energy and Resources
The processes involved in producing corrugated HDPE pipes tend to focus on both energy and emission reduction by combining a post-consumer, as well as post-industrial form of HDPE to maximize useable materials and lower the overall impact on the environment. Advanced methods such as extrusion with optimized energy efficiency not only aid in reducing waste, but ensure that the production process meets the goal of sustainability at a global level. These processes and techniques allow the use of and replacement of materials without the fear of the infrastructure application suffering.
Enhanced Performance on Floodwater Control
Additional corrugated HDPE pipes will react best with flooding due to their excellent strength-to-weight ratio, durability, and robust random flow direction. The smooth interiors help to minimize friction, enhancing the hydraulic effectiveness of the pipes. Their structural shape also allows them to perform optimally for different load conditions. Additionally, these pipes outperform other materials in controlling flooding and erosion in urban and rural areas. These structures provide sustainable drainage systems because they capture a lot of water without harming the environment.
Less Fuel Emission & Greater Pipe Recycling Efficiency
The combination of pipe materials and designs ensure that these pipes are efficient in recycling other previously used materials. These pipes lead to less fuel emission as they use less energy during the production of polymer pipes compared to traditional metal and concrete structures. In addition, lighter-weight high-density polyethylene corrugated pipes lower transportation emissions, minimize fuel during construction and are easy to install more efficiently. Ultra High Pipe with an improved cross-sectional area will utilize energy from recycled materials in a much less damaging way as they are not cast nor require other damaging processes and still retain quality for performance.
Which Industries and Applications Benefit Most from Corrugated HDPE Pipe?
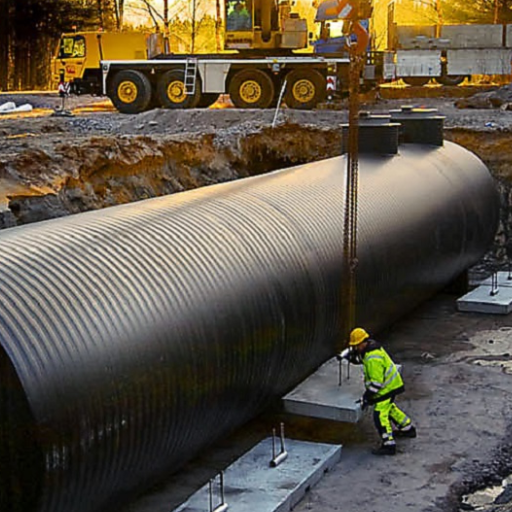
Various business sectors employ corrugated HDPE pipes due to their high durability, cost benefits, and ecological value. In the construction industry, these pipes are used for drainage systems, culverts, and stormwater management. Municipalities and city planners use them extensively in waste and water systems because of their chemical corrosion resistance and long life span. Moreover, the agricultural sector uses HDPE pipes in farmlands for irrigation and drainage purposes. These pipes aid in effective water management. Their flexibility and efficiency make them ideal for various infrastructure and environmental management projects.
Residential and commercial drainage systems
The lightweight construction, corrosion resistance, and simple installation methods of corrugated HDPE pipes makes them extremely effective in residential and commercial drainage systems. These pipes efficiently manage stormwater runoff with minimal water pooling and excess groundwater. Moreover, their flexibility and toughness ensures long-term performance in harsh environmental and load conditions, making them suitable for all sizes of drainage systems.
Solutions for Agricultural and Industrial Water Management
Water management in agriculture and industry is made easier by using Hdpe and high-density polyethylene (Hdpe) pipes, which do well in different conditions. In agriculture, efficient irrigation systems are made possible by minimizing water loss through proper distribution thereby increasing the crop yield. They also withstand chemicals and fertilizers, making them ideal for sustainable farming practices. In industrial applications, the use of HDPE pipes is beneficial because of their ability to withstand high pressure systems, endure chemical reactions, and bear extreme temperatures. These attributes assist in maintaining the industrial processes, reducing the cost of maintenance in the long term.
Municipal and Infrastructure Projects
Training data Infrastructure and Municipal projects involve a variety of systems or facilities necessary for a community’s function, as defined by transportation, energy distribution, water supply, and even waste management. Factors such as population density, urban growth, resource availability, and other detailed technical assessments are considered when planning and executing these projects.
For instance, the contemporary transport system synergistically integrates multi-modal systems like highways, railways, and public transport. It also considers key parameters like traffic volume capacity, axel load limits for roads, and rail gauge compatibility. Likewise, water supply systems are constructed considering pipe material strength, diameter specifications for optimal flow, and reasonable pressure limits so as not to damage the structures. Depending on the energy requirements, substations must comply with the required voltage level range and the existing thermal limits for transformers for secured and reliable electricity provisioning.
The observance of these technical considerations guarantees the system’s efficient performance and sustainability, addressing most current challenges and anticipating emerging ones.
Reference sources
Frequently Asked Questions (FAQs)
Q: What is corrugated HDPE pipe and what are its main applications?
A: Corrugated HDPE (High Density Polyethylene) pipe is a versatile plastic pipe used for various drainage solutions. It’s commonly used in both residential and industrial settings for subsurface drainage, stormwater management, and agricultural applications. The corrugated design provides strength and flexibility, making it ideal for underground installations. HDPE drainage pipes are available in single wall and N-12 dual wall configurations, offering different levels of durability and performance for various project requirements.
Q: What are the advantages of using corrugated HDPE pipe over other drainage pipe materials?
A: Corrugated HDPE pipe offers several advantages over traditional materials like concrete or PVC pipe. These include: 1. Lightweight and easy to install 2. Excellent chemical and corrosion resistance 3. High flexibility, allowing for better ground movement accommodation 4. Long service life 5. Cost-effective solution for many drainage applications 6. Available in perforated options for enhanced drainage 7. Meets industry standards such as AASHTO M252 and ASTM D3212
Q: What are the different types of corrugated HDPE pipe available?
A: There are two main types of corrugated HDPE pipe products: 1. Single wall pipe: Lighter weight and more flexible, suitable for many agricultural and residential drainage applications. 2. N-12 dual wall pipe: Features a smooth interior wall and corrugated exterior, providing improved flow characteristics and increased structural strength. This type is often used in more demanding applications such as highway drainage systems.
Q: How does the manufacturing process for HDPE pipe differ from other plastic pipes?
A: HDPE pipe is manufactured using an HDPE pipe extruder, which melts and forms the high-density polyethylene material into the desired shape. The corrugated profile is created by molding the pipe while it’s still hot, creating the characteristic ridges and valleys. This process differs from the production of smooth-walled pipes like PVC, which are typically extruded in a continuous process without the corrugation step. The manufacturing process for corrugated HDPE pipe allows for the creation of both single wall and dual wall configurations.
Q: What are the typical product specifications for corrugated HDPE drainage pipe?
A: Product specifications for corrugated HDPE drainage pipe can vary depending on the manufacturer and intended use. However, some common specifications include: 1. Diameters ranging from 4 inches to 60 inches 2. Available in various lengths, typically 10 to 20 feet 3. Perforated or non-perforated options 4. Meets AASHTO M252 and ASTM D3212 standards 5. Available with plain ends or bell and spigot connections 6. UV-resistant for above-ground applications 7. Manning’s “n” value of 0.012 for N-12 dual wall pipe
Q: How does corrugated HDPE pipe compare to corrugated polypropylene pipe?
A: Both corrugated HDPE and polypropylene pipes are used in similar applications, but they have some differences: 1. HDPE is generally more flexible and has better low-temperature impact resistance. 2. Polypropylene pipe often has higher stiffness and better high-temperature performance. 3. HDPE pipe is typically more cost-effective. 4. Both materials offer excellent chemical resistance and long service life. 5. The choice between the two often depends on specific project requirements and local availability.
Q: What resources are available for proper installation and design of HDPE drainage systems?
A: Several resources are available for proper installation and design of HDPE drainage systems: 1. Manufacturer’s installation guides and product literature 2. The Drainage Handbook published by industry associations 3. ASTM and AASHTO standards for pipe installation 4. Technical support from manufacturers like Advanced Drainage Systems or Lane Enterprises 5. Engineering design software for drainage system calculations 6. Local regulations and building codes for specific requirements 7. Professional consulting services from civil engineers specializing in drainage design