In today’s rapidly advancing food industry, the production of cereal bars has witnessed significant innovation, particularly with the introduction of the full automatic cereal bar production line. This guide aims to provide an insightful exploration of this state-of-the-art technology, offering readers a detailed understanding of its overall framework and functionality. We will delve into the key components and processes involved, from ingredient mixing to packaging, highlighting the efficiency and precision that modern automation brings to the table. Additionally, we’ll discuss the benefits of such advancements, including increased production capacity, enhanced product consistency, and reduced labor costs. By the end of this post, readers will not only appreciate the complexity and capabilities of a fully automated cereal bar production line but also recognize its transformative impact on the industry.
What is a Cereal Bar Production Line?

Cereal bar production line is an automated system set up to process cereal bars in a more consistent and efficient manner. It includes a variety of automated machines that undertake different processes of production such as blending ingredients, forming, baking or cooling, cutting to specific sizes or shapes, and packing the end product. This mechanization not only boosts the rate of production and its precision and quality of work, but it also reduces the amount of man power required and expenses incurred.
Comprehending the Production Process of Cereal Bars
The manufacturing of cereal bars begins with mixing raw materials like oats, nuts and sweeteners in a mixer. This helps to ensure a mix of all the ingredients and more. Then the mixture is transported to the forming machine which flattens the mixture into a sheet. A conveyor moves this sheet to the cutting machine that cuts the sheet into single bars. The recipe might require the bars to be baked or cooled to achieve the desired end product. Lastly, the bars arrive at the point where packaging of bars is done, where machines wrap the bars for sale. This whole procedure reduces the amount of human mistakes, increases efficiency, and ensures product quality.
Components of a Cereal Bar Making Machine
Over the years, the processes of production, packaging, and distribution for cereal bars have shifted as a result of advancements in technology. Automated machines have made it easier to create and distribute products all over the globe. In addition, the nutritional value of having a bar that provides energy on the go has allowed for a diverse market. There are many components that come together to form the complete structure of the machine and they include;
Mixer: This device combines ingredients such as oats, nuts, sweeteners and other necessary items into a mixture that is then enriched with additional similar components to create a homogenous mixture.
Forming Machine: It prepares the mixture for uniform cutting by first transforming it into a sheet which makes it easier to obtain consistent bar sizes
Cutting Device: It helps slice the sheet into pieces in the shape of bars so that the required size can be maintained throughout the production process.
Baking/Cooling System: Depending on the recipe, this component either bakes the bars to the required texture or cools them to hold their shape.
Packing Machine: This machinery wraps each bar such that it preserves its freshness while waiting to supply consumers.
Benefits of Using a Full Automatic Production Line
A fully automatic production line offers numerous advantages to manufacturers, primarily revolving around efficiency, consistency, and cost-effectiveness. First, it significantly reduces labor costs by automating repetitive tasks, allowing companies to allocate human resources to more strategic areas. Second, automation guarantees uniformity and precision in every batch, minimizing errors and ensuring that each product meets quality standards. Third, it speeds up production rates, meeting higher demand and reducing lead times. Additionally, such systems are often equipped with advanced monitoring features, enabling real-time tracking of production metrics and quick adjustments. Automated lines also enhance workplace safety by limiting human interaction with machinery, reducing risks of accidents. Overall, adopting a full automatic production line improves profitability through more efficient and reliable operations.
How Does a Granola Bar Production Line Work?
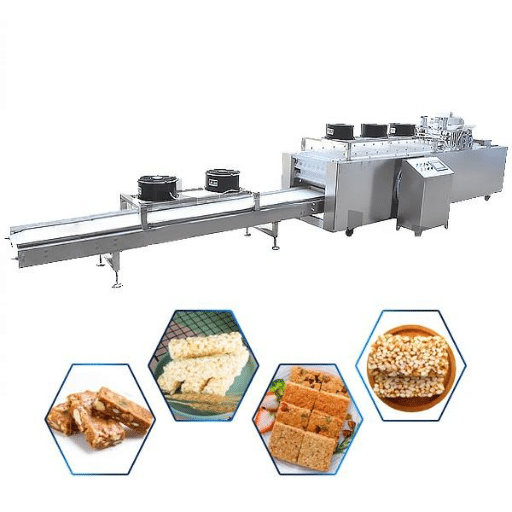
A granola bar production line operates through a series of coordinated steps to transform raw ingredients into packaged bars ready for distribution. Initially, the process begins with the precise measuring and mixing of ingredients to form a homogenous base. This mixture is then transferred to a molding section, where it is shaped into bars with consistent dimensions. Depending on the recipe, the bars are either baked to achieve the desired texture or cooled to solidify their form. Once set, the bars move to the packaging machine, where they are individually wrapped to ensure freshness. Throughout the process, advanced automation technology ensures uniformity, quality control, and efficiency, minimizing the need for manual intervention and reducing production costs.
The Role of Bar Forming and Cutting Machines
Bar forming and cutting machines play a pivotal role in the granola bar production process by ensuring efficiency, consistency, and precision. These machines streamline the shaping of mixtures into uniform bars, minimizing human error and increasing production speed. They achieve exact dimensions and weights, which helps in maintaining portion control and adherence to product specifications. The cutting machines precisely divide the molded sheets, ensuring every bar meets quality standards. Their automated nature not only boosts productivity but also maintains hygiene, reducing contamination risks. The integration of these machines in production lines enhances overall throughput and facilitates large-scale manufacturing operations.
Packaging and Finalizing the Cereal Bars
Once the production of the cereal bars has been completed, both attractiveness and the packing process has to be efficient. Automatic machines ensure that each bar is safely wrapped which provides adequate protection and gives it increased shelf life. This means that the bars are wrapped in materials which are clean and do not allow any gaseous exchange that can lead to degradation of band product while at the same time the wrapping ensuring ease of use to the consumer. During packaging, strict controls are applied to ensure that each bar has the right seals and accurate labels in order to facilitate easy identification and enhance customer satisfaction. Ideal packing speed and reliability will result in a scenario whereby the products are quickly rolled into the market meeting consumer demands without compromising on the standards.
What Are the Key Features of an Automatic Cereal Bar Production Line?
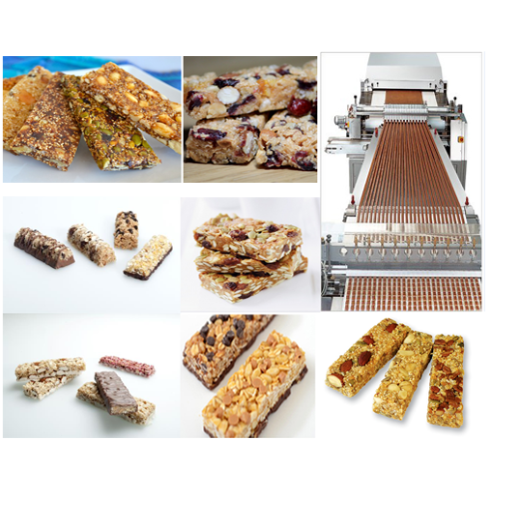
An automatic cereal bar production line is equipped with several key features that enhance its efficiency and functionality. First, it consists of an advanced mixing system that ensures uniform ingredient distribution, critical for product consistency. Secondly, its precise molding and cutting machines allow for the accurate shaping and sizing of bars, which is essential for maintaining consistent product dimensions and weight. The line also includes automated packaging systems that wrap bars efficiently to preserve freshness and prolong shelf life. Moreover, integrated quality control mechanisms provide continuous monitoring, ensuring that each product meets the required standards. These features collectively ensure high productivity, quality assurance, and seamless operation within cereal bar manufacturing.
Нow Advanced Forming Machine Technology Changed the Industry
Today we can see the advanced forming machines that shift the focus of cereal bar making. These machines mix the ingredients to ensure that they are properly homogenized and that the product’s texture and taste are the same. The improved cutting systems cut the bars to precise shape and size, cutting the corners. In addition, forming machines have high speeds also which help to increase output and reduce cycle time. They are easy to use, and require usual adjustment quick changes to improve overall efficiency. What is more important is the fact that these machines have been constructed in a way that allows users to have a long-term utilisation of them without having to worry about costs of maintenance or readily available technicians due to the nature of their operations.
Integration of Chocolate Coating Machines
Chocolate coating machines in cereal bar production enhance product appeal and flavor. These machines heat and temper chocolate to optimal consistency, ensuring smooth coverage on each bar. They feature precise control systems for adjusting chocolate thickness and application speed, crucial for uniform coating. Automated processes minimize handling, reducing the risk of contamination and preserving product quality. These machines also incorporate cooling tunnels to harden the coating quickly, maintaining the bar’s shape and structure. Designed for easy cleaning and maintenance, chocolate coating machines help streamline production, increase efficiency, and ensure consistent high-quality output.
Efficiency and Speed in Full Automatic Systems
In using full automatic systems, I focus on maximizing efficiency and speed. These systems are designed to handle large production volumes swiftly, drastically cutting down processing time. With automated operations, I ensure that tasks are completed consistently and reliably, minimizing the margin of error. The swift transition between production stages is seamless, helping me maintain a steady workflow. Such systems also allow me to make quick adjustments on-the-go, reducing downtime and keeping the production line moving efficiently. This high level of automation not only speeds up the process but also saves resources, making the entire operation more cost-effective and reliable.
Why Choose a Full Automatic Cereal Bar Production Line?
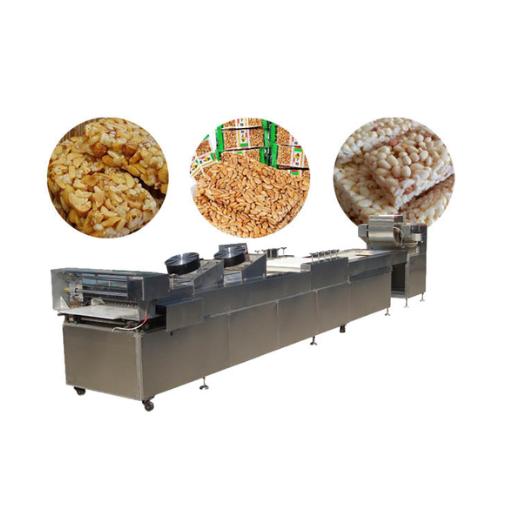
A full automatic cereal bar production line offers numerous advantages that make it an ideal choice for manufacturers. Primarily, it boosts productivity by significantly increasing output while maintaining high quality. The precision and consistency provided by automation ensure that each cereal bar is produced to exact specifications, reducing waste and product rejects. Moreover, the labor costs are minimized as the system requires fewer manual interventions, leading to substantial savings. The ability to quickly adapt to different product requirements further enhances flexibility, making it easier to introduce new products to the market. Overall, investing in a full automatic production line streamlines operations, enhances product quality, and provides a competitive edge in the industry.
Cost-Effectiveness of Automatic Systems
Automatic systems prove highly cost-effective by optimizing resources and reducing labor expenses. First, they enhance productivity by eliminating manual errors and ensuring consistent product quality. With automation, companies decrease workforce costs, as machines handle repetitive tasks efficiently. Furthermore, automated lines minimize waste by accurately measuring and producing exact quantities. This precision reduces raw material costs and limits defective products. Maintenance costs are lower due to the durability and reliability of modern automated equipment, contributing to overall savings. Thus, by investing in automation, manufacturers achieve faster production rates and gain significant economic benefits, ensuring a strong return on investment.
Customization and Flexibility in Production
Automation in production systems significantly enhances customization and flexibility. These systems allow for rapid adjustments to meet varying product specifications and market demands. As a result, manufacturers can quickly adapt to new trends and customer preferences. Automated technology enables precise control over production variables, facilitating the introduction of diverse product lines without extensive downtime or retooling. This flexibility ultimately boosts market competitiveness, as businesses can offer tailored solutions efficiently. Investing in automation not only optimizes production but also empowers companies to satisfy individual client needs and swiftly respond to changes.
Quality and Consistency in Manufacturing
Ensuring quality and consistency in manufacturing involves implementing rigorous standards and continuous monitoring. Automated systems enhance precision by reducing human error, which leads to more consistent product quality. Real-time analytics and feedback loops allow immediate adjustments to maintain standards. Additionally, robots and machines work reliably without fatigue, maintaining steady performance across shifts. This approach diminishes variations in output, helping maintain brand reputation and customer satisfaction. Furthermore, regular maintenance and updates to machinery ensure longevity and optimal functioning, securing the consistency required in competitive markets.
References
-
2024 Nutrition Cereal Bar Processing Line – Offers details on full automatic nutrition and energy cereal bar production lines.
-
Full Automatic Cereal Bar Production Line – Papa – Describes a multi-functional production line capable of producing various snack bars.
-
Complete Cereal Bar Production Line – Provides information on the components of a complete cereal bar production line.
Frequently Asked Questions (FAQ)
Q: What is a full automatic cereal bar production line?
A: A full automatic cereal bar production line is a comprehensive system designed to efficiently produce cereal bars, protein bars, energy bars, and other similar products. It involves various machines like the cereal bar forming machine, bar cutting equipment, and automatic packaging systems to streamline the cereal bar production process.
Q: What components are included in a cereal bar production line machine?
A: A cereal bar production line machine typically includes several key components such as the extruder machine, cereal bar forming machine, puffing machine, bar press machine, and granola bar cutting machine. These components work together to ensure efficient and consistent production of cereal bars.
Q: How does the cereal bar processing line work?
A: The cereal bar processing line works by combining ingredients, forming the mixture into bars, and then cutting them into the desired shapes. The process includes mixing, cooking, pressing, cooling, and packaging, all of which are managed by various cereal bar machinery components.
Q: Can I find a line for sale for producing peanut candy bars?
A: Yes, there are lines for sale specifically designed for producing peanut candy bars as well as other types of cereal bars. These production lines are equipped with specialized machinery to handle different ingredients and bar shapes.
Q: What types of bars can be made with a cereal bar machine?
A: A cereal bar machine is versatile and can be used to make a variety of bars, including protein bars, energy bars, nut bars, puffed rice bars, and peanut candy bars. The machine can be adjusted to produce different shapes and sizes according to the recipe requirements.
Q: What is the role of the cereal bar forming machine section?
A: The cereal bar forming machine section is crucial in shaping the mixture into bars. It ensures that each bar is consistent in size and shape, which is important for packaging and quality control. This section is part of the larger cereal bar production line machine.
Q: Are used cereal bar production lines a viable option?
A: Used cereal bar production lines can be a cost-effective option for businesses looking to enter or expand in the cereal bar market. They allow companies to save on initial capital investment while still obtaining reliable bar manufacturing equipment.
Q: How does an automatic packaging system benefit the cereal bar production line?
A: An automatic packaging system enhances efficiency by quickly and accurately packaging bars, reducing the risk of human error and contamination. It is an essential part of a fully automatic cereal bar production line, ensuring that the final product is ready for distribution.
Q: What advantages does Loyal’s cereal bar production line offer?
A: Loyal’s cereal bar production line offers advanced technology and high efficiency, featuring state-of-the-art cereal bar machinery. It is designed to optimize the cereal bar production process, ensuring high-quality output with minimal downtime.