The development of flow wrap technology has revolutionized the way products are packaged today by providing unparalleled efficiency and flexibility across numerous sectors. By encasing products in a continuous film, flow wrap packaging properly seals the product to provide evidence of tampering while protecting the goods from any damage during transportation and, at the same time, micro-managing the workflow. With the help of automation and material science, flow wrap systems can operate at astonishing speeds while significantly lowering the amount of waste created. The food and beverage, pharmaceutical, and consumer goods industries have a continuous need for low-cost solutions and flow-wrapping systems efficiently fulfill these needs. This article will address the principles, advantages, and applications of flow-wrapping, enabling the reader to appreciate how modern-day packaging processes are made more efficient and sustainable through flow-wrap technology.
What is Flow Wrap Technology and How Does It Work?

The flow wrap technology is an advanced horizontal packaging technique that covers products with a continuous film of plastic cut with a heat seal. The process beggins with flat film fed through rollers and shaped into a tube. Then the product is stuffed inside the film after longitudinal and transverse sealing mechanisms apply heat and pressure, creating “thin” airtight seals. This system totally envelopes and protects the product destined for a prolonged shelf life, making those systems highly effective for fast-moving consumer goods and perishable products.
Some Features of Flow Wrapping Machines
Flow wrapping machines consist of several key components that work together to automate the packaging process. These include a film feeding system, a forming collar that shapes the film into a continuous tube, and synchronized infeed conveyors to place products accurately. Sealing jaws perform transverse sealing at consistent intervals, while longitudinal heaters secure seals along the length of the package. Modern machines often incorporate advanced features such as programmable logic controllers (PLCs) for precise adjustments, sensors for detecting film alignment, and high-speed operations designed to handle varying product sizes and packaging materials efficiently.
An explanation of the wrapping step-by-step the flow technique
The flow wrapping process commences with the film’s insertion into the machine, where it is unwound and then shaped into a tube-like form with the help of the former. Then, the product is fed into the system through the infeed conveyor, where it is placed in the tubular film. Afterwards, the longitudinal sealing subsystem heats and presses the film throughout its length to create a seam. Afterward, cutting sealer is used to create seams at the ends of the package to encase the product fully. The whole package is then cut into single pieces for further processes, all while ensuring an uninterrupted and steady operation of the entire machine.
Important parts of a horizontal flow wrapper unit
Former
The former is the part of the machine used to form the packaging film into a tubular shape. It is of particular importance. This ensures that the film wraps around the product correctly and is ready for the sealing stages of the process. The former must be constructed with extreme accuracy to incorporate various sizes of products with different packaging requirements.
Infeed Conveyor
This conveyor’s primary task is to transport goods into the flow wrapper and it does this with precision. Products are kept at an equal distance from each other and in the correct position, enabling seamless continuation of packaging processes. This equipment also comes with add-ons that allow handling varying product sizes.
Film Unwinding System
This solution controls the packaging film roll – it supplies the film to the machine without any stresses. The more sophisticated film unwinding systems are equipped with devices that track how much film has been used and are programmed to deliver the film at certain rates.
Longitudinal Sealing System
Longitudinal sealing systems heat seal the packaging film along the perimeter of the package. This part of the machine is designed to provide maximum sealing efficiency while permitting the use of different stocking materials of varying weights.
Transverse Sealing Jaws
These jaws seal both sides of the package, marking the completion of the packaging process. They operate in a highly efficient manner, sealing at set cycles per minute, which helps protect the product from shifts during storage and transportation.
Cutting Mechanism
Once the sealing is completed, the cutting mechanism separates the continuous stream of products into single units. This component is responsible for making clean and precise cuts so that the professional quality of the packaged goods is retained.
HMI (Human-Machine Interface)
The HMI panel permits operators to control and monitor the flow wrapper at some level. A fingertip touch can control the machine’s speed, film tension, and sealing temperatures for adjustments that vary from one packaging need to another.
Discharge Conveyor
The discharge conveyor picks the completed packages from the machine for further processing. This component ensures that the movements are smooth and gentle so that the sealed products are not damaged.
What Are the Benefits of Using Flow Wrapping for Product Packaging?

Flow wrapping’s flexibility makes it the most popular option for product packaging in different industries due to a myriad of benefits it provides. It is an economical approach because it cuts down on material waste and increases production output. The process consistently forms sturdy seals that are tamper proof, ensuring product safety and prolonging shelf life. Furthermore, flow wrapping protects products from contaminants, moisture, and other environmental factors, thus maintaining product quality. The process is also versatile as it allows for different shapes and sizes of products to be packaged, all of which significantly increases throughput. Additionally, the end package is attractive to the consumer because it is colorful, yet sturdy.
Increased packaging speed and efficiency
Automatically and continuously flowing wrapping improves both speed and efficiency of the process significantly. The system also minimizes manual handling and downtime of products by efficiently sealing each of them quickly. This high-speed operation works well for large volumes and guarantees constant packaging with the utmost care for the products. By streamlining the process, it also reduces labor expenses and optimizes the use of resources which results in astonishingly low production costs as well a rapid time to market.
Ability to Deal With Different Varieties of Products
Systems for wrapping in flow packs allow high degrees of flexibility in regard to product shapes, dimensions and materials used. The flexibility embedded in the design makes it easy to modify the product size and irregularly shaped goods without any hurdles. Packaging technologies of this sort function exceptionally well in sectors where versatility is a key factor. This approach guarantees adequate packaging for even the daintiest pieces, from breasted delicate items to sizeable, sturdy goods, while maintaining ideal sealing and uniformity. Furthermore, flexibility increases the range of equipment that can be used without fundamentally changing machines, thus enhancing efficiency and workflow.
Improved Protection of The Product and Its Longevity
Systems for wrapping in flow packs enhance significantly the protection of items by encasing the product within an airtight barrier. This prevents moisture, oxygen or particulates from damaging the product directly. It ensures that the product is at peak condition during transportation and storage. Moreover, the product is sealed so securely that the risk of breakage from mishandling is significantly reduced thereby increasing the product’s longevity and reducing wastage.
Which Industries Can Benefit from Flow Wrapping Solutions?

The great flexibility and efficiency of flow wrapping solutions makes them invaluable across various industries. The food sector excels at using flow wrapping for baked goods, chocolates, and fresh produce as it maintains both freshness and protection against contamination. The flow wrapping technology is also used in the pharmaceutical and medical fields where it is needed to securely encase syringes, tablets, and other medical devices in sterile wrappings ensuring that all safety standards are first met. Moreover, the consumer goods sector also uses flow wrapping for cosmetics, electronic devices, and even stationery as these can be adequately safeguarded while still allowing for appealing presentation in stores. This remarkable versatility of flow wrapping within many different industries makes it very popular.
Food packaging applications: From baked goods to candy bars
In food packaging, flow wrapping is primarily used to extend the product’s shelf life, maintain hygiene, and provide aesthetic value. For example, it is highly effective in preserving the flavor and texture of baked goods, such as bread, pastries, and cookies as it protects them from moisture and airborne contaminants. Flow wrapping is also a favored choice for the packaging of candy bars as it enables tamper-proofing and is very easy to handle. In the commercial transportation of such food items, flow wrapping helps to prevent damage during shipping. Also, it ensures compliance with health and food safety standards making it an invaluable option.
Non-food sectors utilizing flow wrap technology
Flow wrap technology has grown popular in non-food sectors because it offers protection, durability, and effective packaging. Electronics manufacturers frequently use flow wrapping to keep dust, static, and physical damage away from cables, batteries, and small gadgets, thereby keeping them in perfect condition while stored or transported. Similarly, in the pharmaceutical sector, flow wrapping is essential for the hygienic packaging of syringes, medical devices, and blister packs to meet sterilization standards and prevent contamination. This technology is also used in the packaging of other consumer goods, such as cosmetics, where it serves for tamper-evident sealing and improves the product’s professional look and market appeal.
On the technical side, flow wrap machines are versatile in terms of the responsive speed at which they can operate and the type of seal the product requires, be it air-tight or perforated. The materials used are often polypropylene film, which has heat-sealing properties and provides good durability. The wraps’ width and thickness can be customized to fit the item’s dimensions. Most machines are able to accommodate multiple different sizes while maintaining a consistent standard of output. These factors and flow wrapping efficiency makes it the popular option in fast and industrial packaging.
Comparing flow wrapping to other packaging methods
When comparing Flow wrapping to methods such as shrink wrapping, vacuum sealing, and other techniques, it can be observed that flow wrapping has a significant advantage in terms of speed, flexibility, and cost. Shrinkwrapping requires an application of heat to wrap the film around an item tightly. Therefore, there is a higher usage of energy, leading to material burns. Flow wrapping does not require a high temperature process, saving more energy and reducing the risk of distortions in the material. Furthermore, flow wrapping can seal products without losing their integrity, which makes it ideal for high-speed operations as it can wrap over 100 to 200 products per minute, depending on the machine’s specifications.
When set against vacuum sealing, flow wrapping uses air in the wrapping process, unlike vacuum wrapping where oxygen is eliminated. Therefore, vacuum sealing can be more ideal for preserving a certain life span for perishable foods but can be less effective for presentations. In contrast when branding is required, flow wrapping can be superior to vacuum sealing as it can also employ the use of printed films. In addition to this, Flow wrap machines provide adjustable parameters such as seal width, film thickness from 20 to 100 microns, and package dimensions, which gives Flow wrapping a higher adaptability to the different industries compared to vacuum sealing machines.
From a technological aspect, flow wrapping is more favorable for automation. These machines are inserted into production lines with product-feeding automation features, eliminating the need for manual work. This combination of efficiency, ease of operation, and flexibility ensures that flow wrapping remains a top option for many applications.
How to Choose the Right Flow Wrapping Machine for Your Needs?
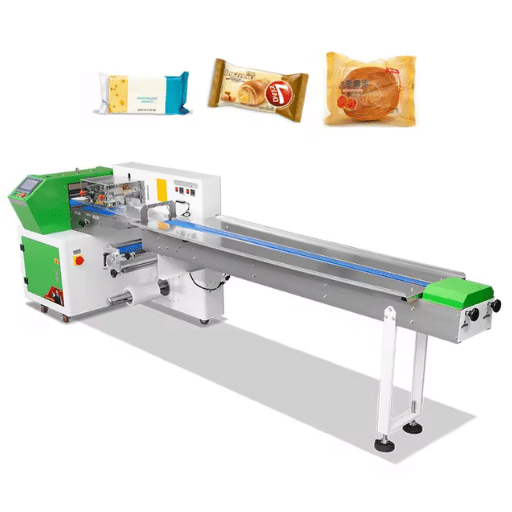
When opting for a flow wrapping machine, it would be wise to analyze the product size, production efficiency, and materials that can be used. Understand the characteristics of the item being wrapped, such as whether it is rigid, fragile, or heat sensitive. This is to ascertain that the machine can provide the necessary seal strength and flow control for active packaging. Also consider the output requirements and the desired packaging style to enhance productivity. Always view the issue from the perspective of protection and advertisement. Also, consider the type of packaging film necessary, such as thickness and barrier properties. Lastly, consider the possibility of integreting his equipment with other machines in the production line to achieve a smooth workflow.
Aspects to Keep in Mind While Choosing a Flow Wrapper
When choosing a flow wrapper, businesses need to consider the product’s dimensions. The machine has set dimensions it can function with, so things like candy bars and loaves of bread are good examples. Make sure the machine is able to handle the item’s length, width, and height while also maintaining wrapping quality. Also consider production speed. It is essential to have specific output requirements, since machines can wrap anywhere between 30 and over 300 items a minute. The machine being used should be able to wrap items over 20 and under 100 microns for seal guarantees and compatibility to multiple films such as polyethylene, laminated films, and polypropylene.
Also, think about how functional pillow packs and fin seals will help promote the business. In terms of integration, many modern flow wrappers now come with programmable logic controllers (PLCs), allowing for easy and accurate automation and connectivity with current systems such as conveyors or inspection devices. For items that are sensitive to temperature, look for seal jaw features which can adjust the temperature to maintain film integrity without damaging it.
High-speed versus Standard Flow-Wrapping Machines
High-speed flow wrapping machines are meant to cater to production rates over 300 packages per minute, which is ideal for large-scale manufacturing. These machines integrate advanced servo drives and electronic control of film feeding and closing systems to enable accurate sealing and feeding of the film at high speeds. Standard flow wrapping machines range between 30 and 150 packages per minute and are suited for small—to medium-sized enterprises, thus providing an affordable solution for most mid-sized firms.
When designing high-speed machines, some of the key parameters include the width of the film roll (which is usually over 600 mm) and the ability to use different types of films ranging from 20 to 80 microns in thickness. Other key parameters include adjustable temperature range between 100 degrees Celsius and 250 degrees Celsius for effective, efficient, and reliable seals without compromising the film. Also, these modern systems are increasingly incorporating automatic feeders, date coders, and inspection devices for more streamlined operations.
Standard flow wrapping machines that have basic automation features such as manual feeding and can operate with narrower rolls (less than or equal to 400 mm) are undoubtedly suitable for less nuanced workflows. When appropriate, both categories should meet food-grade packing regulation, while the aforementioned factors must support the machines’ reliability over time. By matching the machine features with production objectives, businesses can greatly increase productivity and achieve high uniformity of packaging standards.
Customization options for specific packaging requirements
Customization of machine packing features have a direct relationship with the product’s packaging and the production environment. Key features are modifications to accommodate different product dimensions, use of distinct types of bags for packing to maintain the integrity of the product, and modular assemblies that allow operational flexibility. More advanced options often include programmable control systems for setting specific operational parameters which allow for adjusting speed, sealing technique, and grabbing sequence. Inline printing, labeling, and inspection modules are often integrated to comply with regulatory and marketing needs. These features ensure that the machines can be agile, modular, and compliant with rigid production and quality requirements.
What Are the Different Sealing Methods Used in Flow Wrapping?
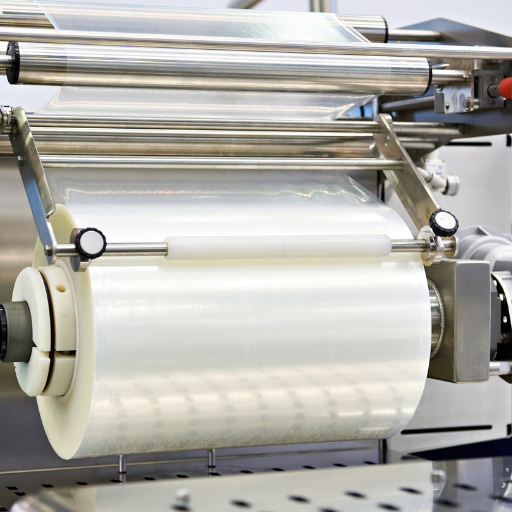
Flow wrapping uses various key sealing techniques to ensure packages seal tightly with high levels of preservation and protection. These methods involve edges such as fin seals and lap seals which are selected based on the packaging material and its usage. Fin seals provides robust security and resistance to tampering by folding the packaging material and sealing it along the edges using heat and pressure. Lap seals, on the other hand, overlap the edges of the material, sealing it in a flat and aesthetic manner, making it very suitable for thin films. However, unlike fin seals, lap seal requires the material to be compatible. For perishable goods that require airtight protection and sealing, lap seal can be used. Achieving the best packaging performance while before the goods reach the final consumer relies heavily on the type of sealing implemented.
Heat Sealing vs Cold Sealing: Evaluation of Benefits and Constraints
The two various methods each have their own pros and cons, taning into account both the type of packaging and materials to be used: heat sealing and cold sealing. Heat sealing, for example, is the most common method that uses electric energy in the form of heat and pressure to bond together materials, usually thermoplastic materials. This method guarantees strong, durable seals. Its usefulness is seen in many settings, such as on high-speed production lines. Some critical technical parameters include the sealing temperature which is usually between 250-400°F depending on the material being used, the line dwell time of the seal, and the sealing pressure. However, heat sealing needs rigid rules to control so that weak seals and materials damage does not occur, all while consuming high amounts of energy.
Cold sealing does not rely on electric energy and is, therefore, ideal for sensitive products like healthcare items. The biggest advantages of cold sealing is that it can seal at room temperature, making it a lot faster and lower in energy consumption than heat sealing. Other products, such as chocolates that are sensitive to heat, will also benefit from this technique as the risk of damaging temperature-sensitive films is lowered. While there are advantages to cold sealing, the cold sealing materials tend to be more expensive and poses some alignment challenges. Though cold sealing works well for certain products, it comes with durability limitations under high humidity and circumstances of high manipulation.
Both methods have specific requirements to fulfill, with heat sealing ranking the highest in strength and versatility. Cold sealing is unparalleled in speed and is best suited for fragile packages.
Fin seal and lap seal options explained
Fin seal and lap seal are two of the many sealing techniques available that are often used in flexible packaging processes. A fin seal is a method of sealing wherein the edges of the material are folded inwards and then sealed along the edges, creating a strong and tamper-resistant seam often used on items that need to withstand higher mechanical manipulation. A lap seal, on the other hand, is precisely the opposite, where the edges of the material are not folded but rather overlap and are sealed by directly adhering one surface to the other, which saves materials but binds using compatible materials. In general, fin and lap seal selection is dependent on the aesthetic, strength requirements, and properties of the packaging material.
What Are the Latest Innovations in Flow Wrap Technology?

The newest innovations in automation and flow wrap technology incorporate areas such as sustainability and efficiency and offer better packaging results. New materials are being developed to produce recyclable or biodegradable films that can provide for environmentally-friendly operations. In terms of efficacy, contemporary flow wrappers incorporate procedures and systems for automation and monitoring in real-time which enhances production output while minimizing downtime caused by mechanical failures. Also, improvements in the sealing mechanism technology provide better or more reliable seals, even in the use of thinner or eco friendly materials. These advancements all add to flow wrap solutions’ improved efficiency and environmental friendliness.
Shifts in packaging materials: Polypropylene and paper
Because of its strength, durability, and moisture resistance, polypropylene has been widely accepted for flow wrap packaging. Currently, however, there is a marked movement towards more sustainable options. New innovations target decomposable and compostable substrates such as bio-based polymers that still maintain the functional integrity typical of plastics, but have less environmental impact. Furthermore, paper-based materials are moving to the forefront while adding coatings and treatments to provide barrier properties that equal those of plastic, but are completely recyclable. These shifts are in line with the increasing requirements for environmentally friendly and efficient streamlined packaging.
Integration of smart packaging solutions with the industry
Smart packaging is changing the world with cutting-edge technologies that increase usability, traceability, and consumer interaction. New inventions such as QR codes, RFID tags, and NFC Technology make it possible to automatically capture and monitor information in real time through the supply chain, thus assuring product quality and authenticity. Besides, such smart packaging solutions complement data analytics systems perfectly as they grant businesses actionable understanding of consumer behavior as well as efficient business operations. Active packaging that interact with the product and its environment to lengthen shelf life along with intelligent packaging that provides crucial information marks rapid progress towards intelligent and adaptable smarter packaging systems. These are transformative changes that not only satisfy the increasing demands of consumers but also improve processes with smart technologies and systems integration in the industry.
Eco-friendly flow wrapping solutions for environmentally responsible brands
Eco-friendly flow wrapping solutions for environmentally responsible brands include the use of biodegradable, compostable, and recyclable materials. Biodegradable films, such as those made from plant-based polymers, are designed to decompose under certain conditions. An even greater step is represented by compostable materials, which break down into non-toxic, natural elements in a compost environment. Additionally, recyclable films, often made from mono materials such as polypropylene (PP), are manufactured to be compatible with existing recycling systems which greatly reduce their environmental impact. These approaches effectively mitigate environmental harm while ensuring that the products are properly packaged and can remain on the shelf for some time.
Reference sources
Frequently Asked Questions (FAQs)
Q: What is flow wrap technology and how does it work?
A: Flow wrap technology, also known as horizontal form fill seal (HFFS), is a packaging method used to wrap individual products in a continuous process. It works by forming a tube of packaging material around the product, sealing it lengthwise, and then sealing and cutting it at both ends to create a finished package. This technology is commonly used for a wide range of products, including food items, cosmetics, and household goods.
Q: What are the main differences between flow wrapping and overwrapping?
A: Flow wrapping and overwrapping are two distinct packaging methods. Flow wrapping creates a sealed package from a single roll of film, while overwrapping typically involves wrapping a pre-formed tray or box with a layer of film. Flow wrapping is generally more versatile and can handle a wider range of product shapes and sizes, while overwrapping is often used for products that require additional protection or rigidity.
Q: What types of packaging formats can be achieved with flow wrapping?
A: Flow wrapping can produce various packaging formats, including pillow pouches, gusseted bags, and fin-sealed packages. The most common format is the pillow pouch, which is ideal for products like biscuits, bars, and other food items. Gusseted bags provide more stability for standing products, while fin-sealed packages offer a sleek appearance and are often used for premium products.
Q: What are the benefits of using flow wrapping for product packaging?
A: Flow wrapping offers numerous benefits, including high-speed production, versatility in handling various product sizes and shapes, excellent moisture and oxygen barrier properties, and the ability to create attractive, retail-ready packaging. It’s also cost-effective for both small start-ups and large companies, as it requires less material than some other packaging methods and can be easily scaled to meet production needs.
Q: What types of products are commonly packaged using flow wrap technology?
A: Flow wrapping is widely used for packaging a variety of products, particularly in the food industry. Common items include biscuits, chocolates, energy bars, bakery products, frozen foods, and confectionery. It’s also used for non-food items such as disposable cutlery, medical supplies, and household products. The versatility of flow wrapping makes it suitable for both primary packaging and secondary packaging applications.
Q: How does flow wrapping contribute to efficient product distribution systems?
A: Flow wrapping enhances product distribution efficiency by creating uniform, easy-to-stack packages that maximize space utilization during transportation and storage. The sealed packages provide protection against moisture and contaminants, extending product shelf life. Additionally, flow-wrapped products are often easier to display in retail environments, improving overall supply chain efficiency from production to point of sale.
Q: What materials are commonly used in flow wrapping?
A: Flow wrapping can utilize various materials, including plastic films, laminates, and paper-based substrates. Common materials include polypropylene, polyethylene, and metallized films for products requiring higher barrier properties. Sustainable options like compostable films and paper packaging are becoming increasingly popular as companies focus on eco-friendly packaging solutions.
Q: How does horizontal flow wrapping compare to vertical form fill seal (VFFS) packaging?
A: Horizontal flow wrapping, also known as horizontal bagging, differs from vertical form fill seal (VFFS) packaging in its orientation and product handling. Horizontal flow wrapping is ideal for products that are stable and can be easily fed into the machine horizontally, such as bars or biscuits. VFFS, on the other hand, is better suited for products that can be measured by volume, like powders or liquids. Horizontal flow wrapping generally offers higher speeds and better control over product orientation in the finished package.