Flow pack technology is a breakthrough in modern packaging industries as it provides an effective solution to various industries. Primarily, this is used for fast and clean packaging of food, pharmaceuticals, cosmetics, and consumer goods. Its form, fill, and seal method ensures that every product sealed within it attains optimal freshness. This article looks at the primary advantages of flow packs, such as increased production speeds, lowering of materials used in the products, waste reduction, and targeting brand recognition through design. Also, it looks on other sectors that it is valid, emphasizing the importance of modern packaging and its requirements on consumers and industries for efficiency, effectiveness, and sustainability.
What is Flow Wrap Packaging and How Does it Work?
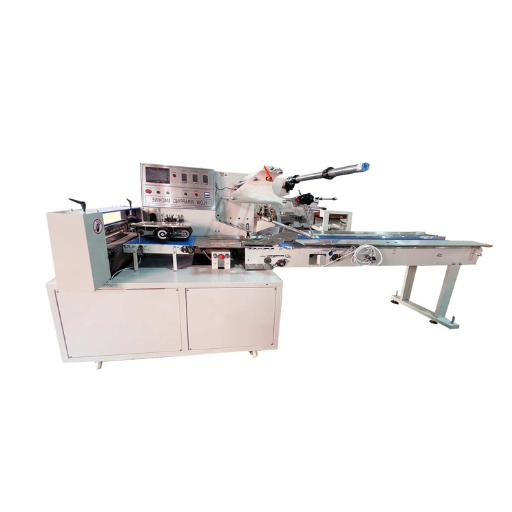
The process of flow wrap packaging, which is sometimes referred to as horizontal form-fill-seal (HFFS) packaging, is one of the most efficient methods of packing products using flexible film. In flow wrapping, a roll of film is fed into a machine that wraps it around a product and seals the edges while cutting it into individual packages. This technique forms a tight protective barrier, or wrapper, around the product, preventing contamination, moisture, and physical damage. Flow wrap packaging is often used for snacks, baked goods, and even some medical products. It is a highly effective method of packaging due to its speed, accuracy, and flexibility in accommodating a variety of shapes and sizes of products.
Understanding the basics of flow pack technology
Flow pack technology operates on horizontal motion, where products are continuously moved through a machine that applies a flexible film around them. The process includes forming the film into a tube, sealing it longitudinally, and cutting it to create individual, airtight packages. This system uses precise temperature and pressure controls to ensure robust seals, making it ideal for preserving product integrity while maximizing efficiency.
Key components of a horizontal flow wrapper
Infeed Conveyor Section
The infeed conveyor section is an essential component of a horizontal flow wrapper. Its role is to ensure that products are fed into the machine at a certain speed so that they do not misalign, whether the machine is engaged in operation or not. This is done to effectively space the control products. Product alignment is very important in ensuring the tangible and operational requirements for the desired packaging are met.
Film Unwind System
The Film Unwind System is a component that maintains the roll of the packaging film while dispensing it. It has tension controls to guarantee high standards of film feeding. This helps prevent the film from creasing, slack, or other issues that can compromise the seal and appearance of a package.
Forming Collars
Products of different sizes and shapes can now be designed with new technology and machines placement. Forming collars are responsible for modifying the flat sheath into a round form. This will make sure that the wrapping is done effectively regardless of the shape or size of the product packed inside.
Longitudinal Sealing Unit
The longitudinal sealing unit is one of the most important parts of the machine. It makes it easy to wrap products using film. Heating devices like electric Heating elements and electric crimpers help seal a seam along the package length effectively using the right amount of temperature and pressure.
Cutting and End-Sealing Unit
This module ensures that the package’s closure seals are intact and cuts single wraps from the continuous tube. The apparatus’s cutting part is linked with the product feeding system, which allows it to achieve the required dimensions and secure seals on both ends of the package.
Control Panel
The control panel contains interfaces guiding the user and programmable options allowing the operators to control sealing time and temperature, product speed, etc. Higher versions might have touch-screen monitors and self-diagnostics, which help with running and troubleshooting tasks.
Product Detection System
Cameras and sensors are integrated to identify the product’s position and enable proper wrapping. Such systems save costs by eliminating incomplete packaging or items being not packed at all.
Discharge Conveyor
The conveyor removes the packed goods from the machine to the next stage within the production line. It ensures the proper treatment for the packages in mechanical handling and segregation, which further processes them like packaging, marking, or forwarding.
Elaboration on the flow wrap packaging process
A continuous roll of film is fed into the machine during the flow wrap packaging process. The film is wrapped around the product and then subsequently shaped into a tube. The product is then placed into the film using a product detection system that appropriately aligns the film for sealing. The machine then heat seals the longitudinal seam and both ends of the package to create an airtight seal. Afterwards, a discharge conveyor transfers the sealed, individual packages out of the machine for further handling. This technique promotes efficient and consistent packaging of a wide variety of products while ensuring that the products are protected and presented professionally.
What Are the Benefits of Using Flow Pack for Packaging?
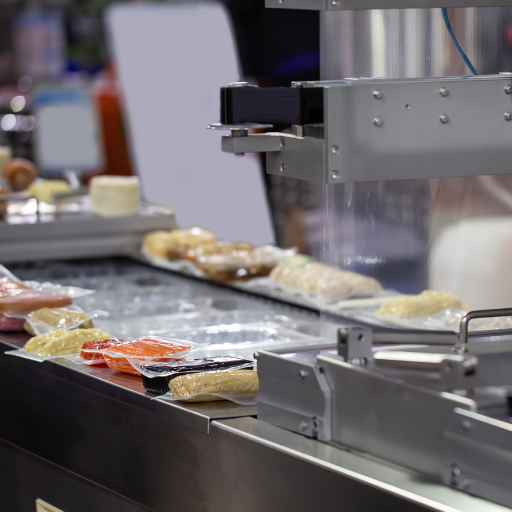
One of the ample benefits of flow pack packaging is its ease of use across various industries such as food and medicine. This seal can keep contamination out while preserving the product within and keeping the contents fresh and uncontaminated. With everything being adequately sealed, businesses can benefit from low production and operation costs since packaging items is easy and quick, regardless of the product size and shape. The bonus of using printed films improves the quality of the final product and can attract the consumer’s attention. Because of the various benefits flow pack packaging offers, many industries have started using it.
Adapts easily to different shapes and sizes
Another distinct advantage of flow pack packaging is its adaptability to ever-changing business needs. Along with food and pharmaceuticals, flow pack packaging can also be used in consumer goods. The film used is flexible enough to form a tight seal so downtime is minimal and production efficiency is high. This, combined with rapid production machinery, results in a secure seal for any product with little to no delay in production. Furthermore, the wide variety of brands give a customization option through prints or transparent films, which improves the shelves’ visual presence. Flow pack packaging is an excellent utility with countless advantages that different businesses can take benefit from.
Efficient Production Capabilities
The combination of modern horizontal flow wrap machines with pack flow envelopes allows for swift production. Depending on the type of product, type of film, and the configuration of the system, these machines can typically run at a speed of 60 to 300 packs per minute. Some of the technology’s key features are automation drives for controlled motion, automatic downtime splice film roll, and adjustment seals, which change according to film type and thickness. Furthermore, the modular design of the new machinery makes it possible to easily design them to meet precise production line specifications, ensuring continuous production without quality dips or seal breaks. Flow pack packaging simultaneously enables for a remarkable amount of speed and flexibility and makes it the preffered choice for industries with high levels of throughput and consistent output.
Efficiency When Dealing With Bulk Produced Products
The economic benefits of using flow pack packaging for bulk production are even greater due to effective material consumption, waste reduction, and efficient processes. The efficiency with which the system can manage a wide range of product sizes and shapes with little changeover time minimizes operational costs and high-speed automation lowers labor costs. In addition, the reduced material consumption associated with the use of specialized flow pack designs reduces long-term costs. Together with the ease of use, these features significantly lower operational costs for businesses that must package large product volumes.
Which Types of Products Are Suitable for Flow Wrapping?
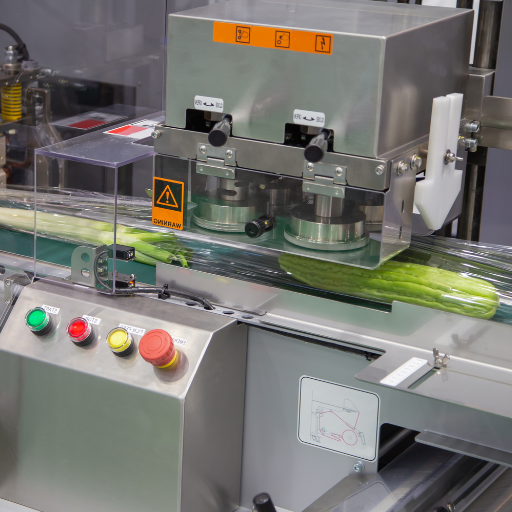
Flow wrapping serves a range of purposes across different industries. It is helpful in the food industry for items such as chocolate, candy bars, fresh produce, baked goods, and snacks because it helps seal the item and preserves its freshness. Additionally, flow wrap is utilized in the medical, veterinary and cosmetic industries because of the tamper-evidence seal that ensures product safety. Flow wrap is also ideal in the bait and tackle and automotive industries because it deals with parts of different shapes and sizes. Flow wrapping is beneficial for any business because it is simple and efficient, making it suitable for various product types.
Food items: From baked goods to fresh produce
- Chocolates and Candy Bars: Flow wrapping protects bars and candies from harm during transportation and storage, preserving their taste and allowing branding and health compensation to be added more conveniently.
- Fresh Produce: Flow wrapping also helps prolong the shelf life of fruits and vegetables by keeping moisture and dirt away. The perforated films allow for regulate air flow to prevent the buildup of condensation that could lead to spoilage.
- Baked Goods: Flow wrapping an airtight seal is instrumental in keeping bread, cookies, and pastries fresh for extended periods. Apart from trapping the target’s taste and texture, the flow wrapping is ideal for attracting new customers because it displays the product well.
- Snack Foods: Ready-to-eat foods, chips, and crackers are perfectly preserved while being wrapped flow-way. This ensures freshness and prevents spillage. The wrapping can be designed to be user-friendly and easy to open, further adding to the consumer’s experience.
Non-food applications: Electronics, pharmaceuticals, and more
Aside from the food industry, flow wrapping is essential in packaging numerous other products like electronics and pharmaceuticals. Flow wrapping provides an airtight seal for electronic devices that safeguards delicate parts from dust, moisture, and electrostatic discharge during storage or transportation. In the pharmaceutical industry, flow wrapping guarantees safety and cleanliness for objects such as syringes, medical devices, and blister packs. Products like mechanical spare parts and cosmetics also take advantage of flow wrapping’s benefits, such as packaging speed, product protection, and extended shelf life. These can incorporate different shapes and requirements flexibly and efficiently with the flow wrapping.
Constraints and factors influencing product choice
The process of selection of products for flow wrapping entails several constraints and considerations that must be addressed to achieve maximum efficacy and appropriateness. One of the key limitations is the compatibility of materials for the actual flow wrapping product, with the wrapping film. Some products, particularly those with irregular shapes or sharp edges, are likely to tear or puncture the film, rendering it useless. Furthermore, delicate products may not perform well during the heat sealing stage of flow wrapping, as this process may result in deterioration or alteration in structure.
Another critical factor is the consistency regarding the shape and size of the product as significant inconsistencies may affect the precision of the wrapping machine, leading to poor quality of wrapping or destruction of the product. Environmental factors are of equal significance especially the required barrier properties of the film which include the inhibition of moisture, oxygen, or light. Such films are significant for products that are intended for use and require sterility, like in pharmaceuticals, where there is a need to observe regulatory standards such as ISO 11607 with strong validation tests for seal integrity.
In conclusion, variables such as machine throughput, type of film (polyethylene, polypropylene, etc.), film gauge, which is typically measured in microns or mils, and other operational parameters need to be coherent with production processes and financial limitations. These parameters highlighted above will assist in creating the proper selection process for the product and the packaging system.
How to Choose the Right Flow Wrap Materials for Your Products?
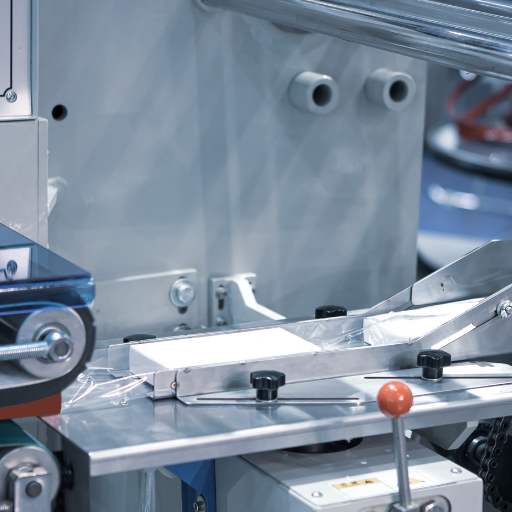
The selection of flow wrap materials calls for a meticulous evaluation of product needs, packaging requirements, and operational effectiveness. It is best to start with the task of identifying unique issues related to protecting the product from environmental factors such as moisture, light, and even oxygen that tend to spoil its quality and reduces shelf life. Considering the nature of the product, be it food, pharmaceutical, or industrial, certain requirements, such as packaging grade and sterility, must be fulfilled.
Next, evaluate the available materials in terms of their performance characteristics and acceptability for the intended application, such as film strength, flexibility, and seal integrity. Gas permeability is an example of barrier properties that must be balanced against the product’s shelf life and storage conditions. In addition, operational attributes such as the fit to existing equipment, throughput requirements, and material handling during production should be taken into account to avoid operational inefficiencies.
Lastly, economic factors such as cost of materials, supply availability, and sustainability issues are equally important. Adjusting these elements guarantees effective fulfillment of the technical requirements within the flow wrap material, achieving the set production objectives while also remaining within budget ceilings.
Common packaging films: Polypropylene, polyethylene, and recyclable options
Mono-line films use easy-to-recycle materials like polypropylene due to their excellent clarity, endurance, and moisture-proofing. Along with these features, it also has low gas permeability, which helps in effectively packaging foods and snacks. Snugly-fit polyethylene, especially in its less dense forms, offers flexibility and rigidity making it effective for packaging different kinds of products. Recyclable options comprising single-material films are mono-centric and do little to satisfy sustainability concerns, unlike more recently developed alternatives. These films require barrier protection and seal strength, which makes them complicated to recycle, unlike mono-material films, which provide benefits that non-single materials offer.
Matching material properties to product requirements
Matching film materials available for different conditions need essential components such as sealing toughness, mechanical endurance, and barrier capability. For example, products that need low moisture exposure are best with garments made of BOPP or biaxially oriented polypropylene, as they perform well with low WVTR. In cases of needing a low gas exchange environmental seal, multi-layered single-use polyethylene materials or EVOH lamination aid greatly.
The parameters of tensile strength and elongation at break must also be relevant to the packaging process so that there is no material loss during high speed processes. For example, Polypropylene films have tensile strength values between 20 and 40 MPa, depending on the formulation, which enables the automated cutting and sealing of the film. In addition, sealing requirements must consider operating temperatures and peel strength to ensure that the closure is tight and consistent throughout. However, LDPE films are sealed effectively at places between 120 degrees Celsius to 160 degrees Celsius where the seal is strong, but the process is also efficient.
Finally, these features must be considered in terms of the selection’s impact to the environment. When designing mono-material recyclable films, one of the main challenges that must be overcome is ensuring that the films have the appropriate attributes of thermal stability and resistance to puncturing while also complying with stringent recycling requirements.
Sustainable packaging solutions in flow wrapping
Using biodegradable or compostable films made from renewable materials such as PLA and cellulose significantly improves over conventional plastics, especially if a manufacturer wants to be environmentally friendly. This is especially useful in flow wrapping where mono-material films increasingly become popular as they provide improved functionality. Barrier protection, seal integrity and functional performance work hand in hand towards increasing a wrap’s effectiveness. Manufacturers are also testing thinner gauge materials that still retain the necessary mechanical strength. Adopting these measures not only ensures compliance with regulations, but also responds to the consumers’ requirements for eco-friendly packaging.
What Are the Different Types of Flow Wrapping Machines Available?
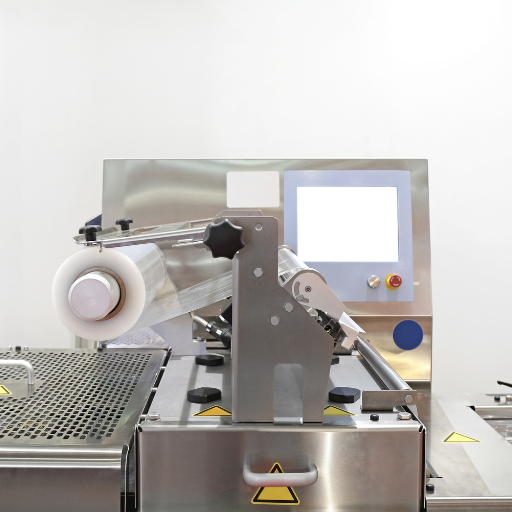
Packaging machinery of this type may be divided based on their functional features and particular uses. The majority type are horizontal flow wrappers. These machines efficiently wrap bakery products, candy bars, and medical items through a horizontal feeding system. Vertical wrappers serve bulk or small sized products. They have a vertical flow of products which is appropriate for granules, powders, and the like. More general types of flow wrappers are those for modified atmosphere packaging, which enhances shelf-life by changing the packaging environment. These types of flow wrappers include high-speed versions, which are utilized for mass packaging. Each type is developed to support diverse and particular production needs and assured packaging quality.
Comparison Between HFFS and Other Packaging Types
HFFS machines designs put them in a contrarian position among other formats. HFFS is specifically designed for specific units operations in which the motion of the package is continuous, unlike vertical packing machines that are designed for bulk and loose powdered products. HFFS also makes the exact wrapping placement that is needed which is great in protecting and showcasing the product. HFFS machines operate much quicker than tray sealers or thermoforming devices. High speed models can reach up to 400 packages per minute. However, the throughput differs on the pack size and film type.
HFFS machines utilize adjustable sealing temperatures, which makes them compatible with various films between 100°C to 250°C. They also have servo-driven motors and customizable roll widths that range from 250 mm to 600 mm. Often included as well is a touch screen for monitoring and quick changes. The true power of HFFS programming is displayed in its capacity to address a vast range of films, from industrial grade polypropylene to biodegradable alternatives. The efficiency with which HFFS can simultaneously meet industrial and ecological needs is impressive. HFFS allows other formats used in different industries to be replaced due to the increase in versatility and precision required for highly populated areas.
Automatic vs Semi-Automatic Flow Wrap Machines
Automatic flow wrap machines feature virtually no human input and work with the use of advanced technologies like PLC controls, servo motors, and automated film feeding systems. They are ideal for large and consistent output production. On the other hand, semi-automatic machines utilize manual processes for product feeding and film changes, which makes their production functions more cost-efficient for lower-volume operations. Semi-automatic machines can be inflexible and have unreliable up front costs; however, they maximize efficiency and customization for inconsistent production targets. Automatic systems, while providing accurate and effortless results for high volume business tasks, can become overly rigid.
Customization options for specific packaging needs
For example, it is possible to customize the machine to process different sizes and shapes or materials of products with different packaging types such as resealable bags, vacuum packs, and multi-layer films. Matching the operation’s parameters may also include improved sensors for accurate alignment, modular extras for integrated labeling or printing, and flexible film sealing for various thicknesses and types. These modifications increase efficiency within the company’s operations and allow the business to meet market needs ranging from specific branding to longer shelf lives for fresh products.
How to Get Started with Flow Wrap Packaging for Your Business?

To implement flow wrap packaging for your business needs, first identify the product dimensions, materials specifications, and the expected output units per hour. Determine whether your business requires a manual, semi-automatic or fully automatic flow wrap machine and if it fits within the budget. Following the feature assessment, consider whether precision sealing, film flexibility, and system integration with labeling or codes are required. Choose suppliers that provide adequate maintenance, training, and customization and enable reliable facilitation. Lastly, run initial tests to monitor the equipment functionality. This way, you can make adjustments before fully transitioning into streamlined operation.
Estimating the requirements of packaging alongside the expected production volume
To analyze the top boundaries of your estimates and the overall parameters of your packaging expectations, begin by establishing the weight, dimensions, and breakability of the products themselves for the type of material and film needed. For products with sharp, irregular-shaped, or particularly fragile edges, more robust materials must be utilized. Further, the estimated output units per day or hour are measured to help analyze the production volume.
Choosing the best flow wrap machine and materials
When choosing flow wrap machinery and materials, always pay attention to what the machines offer regarding production requirements such as speed, package sizes, and the desired level of automation. Also, check whether the packaging materials you intend to use work with the machine’s heat sealing capability, flexibility, and barrier properties. Consider the machine’s ability to be adjusted for different products and its overall ease of use to reduce downtime. Finally, long-term operational factors such as energy consumption and maintenance needs should be considered for greater efficiency and economy.
Achieving optimal performance through training and maintenance structure
Achieving sustainable performance in maintenance and training requires systematic planning and uninterrupted execution of training plans. Training plans should stretch the athlete’s limits gradually to provide a proper foundation for improved performance while avoiding overtraining scenarios. Improvement of performance should be monitored regularly in order to aid in identifying weak spots and tailoring the workloads accordingly. Rest is a vital component, as is proper nutrition and hydration, and hydration alongside appropriate structures should improve perseverance and mitigate the chances of injury or failure while amplifying output. From a mechanical side, looking after the equipment and conducting checks on a periodic basis, as well as actively touching up on areas that wear out, greatly improves the effectiveness of the machinery observation along with toggling default settings.
Reference sources
Frequently Asked Questions (FAQs)
Q: What are the main benefits of flow packaging?
A: Flow packaging offers several advantages, including increased production efficiency, reduced labor costs, and versatility in packaging various products. It’s suitable for packaging a wide range of items like chocolates, snack bars, and biscuits. This packaging technique also helps in reducing packaging waste and can be used with recyclable materials, making it an environmentally friendly option.
Q: What is horizontal packaging and how does it work?
A: Horizontal packaging, also known as HFFS (Horizontal Form-Fill-Seal), is a versatile packaging technique where products are wrapped horizontally. The process involves forming a tube from a flat film, sealing it longitudinally, filling the product, and then sealing the ends. This method is highly efficient and suitable for packaging various items without the need for constant manual intervention.
Q: What types of products are commonly packaged using flow packaging?
A: Flow packaging is used for a wide range of products. Common applications include packaging items like chocolates, snack bars, biscuits, and other bakery items. It’s also suitable for non-food items that require protective packaging. The versatility of flow packaging makes it an ideal choice for many industries.
Q: What materials are typically used in flow packaging?
A: Flow packaging films are typically made from materials like polyethylene, polypropylene, or polyester. These materials offer good barrier properties and can be customized to suit different product needs. Some packaging films also come in recyclable or biodegradable options, contributing to more sustainable packaging solutions.
Q: How does an automatic horizontal flow wrapper work?
A: An automatic horizontal flow wrapper forms a continuous tube of film around the product, seals it longitudinally, and then creates cross seals to form individual packages. The machine automatically feeds products, forms the package, and seals it, all in one continuous process. This automation greatly increases packaging speed and efficiency.
Q: What factors affect the speed of flow packaging?
A: The speed of flow packaging depends on several factors, including the type of product being packaged, the packaging material used, the complexity of the package design, and the capabilities of the packaging machine. Generally, flow packaging is known for its high-speed operation, which can significantly boost production rates compared to manual packaging methods.
Q: How does flow packaging contribute to reducing packaging waste?
A: Flow packaging contributes to reducing packaging waste in several ways. It allows for precise control over packaging material usage, minimizing excess. Many flow packaging materials are recyclable or made from sustainable sources. Additionally, the efficiency of the process means less waste during production. Some flow packaging solutions also offer resealable options, extending product life and reducing food waste.
Q: Why is flow packaging a preferred choice for many food manufacturers?
A: Flow packaging is a preferred choice for many food manufacturers due to its versatility, efficiency, and ability to maintain product freshness. It provides a good barrier against moisture and contaminants, extends shelf life, and offers attractive packaging options. The high-speed nature of flow packaging also allows for increased production capacity, making it economically advantageous for large-scale manufacturing.