Timely productivity and low costs are desired sides of the supply chain management coin, which is why Modern packaging solutions are crucial, considering they influence cost-effectiveness and product safety. In the processes of packaging, one of the main tools is carton sealing machines. These tools mechanize the closure of cartons to ensure uniformity, security, and speed in the operations. These machines do more than streamline and automate the wrap and seal processes. Because of these machines, overall efficiency improves, and material waste for these tasks, alongside error rates, is reduced. This article covers the crucial features of carton sealing machines, the advantages of their functioning, and their role in various businesses’ cost-efficient packing processes.
What are carton sealing machines and how do they work?
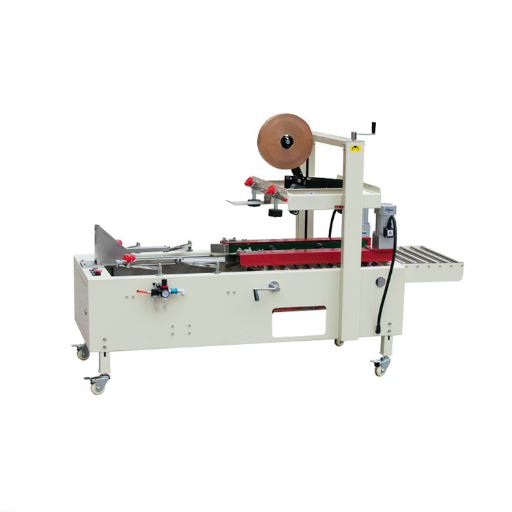
The automated sealing of boxes and cartons, using adhesive tape, is done efficiently by carton sealing machines, which are robots. These machines function by guiding a carton through a series of rollers and belts which automatically apply tape to seal the box flaps. In addition, they can work with many different carton sizes as well as adjustable settings for different materials and dimensions, guaranteeing both accuracy and speed in the packaging process.
Understanding the basics of carton sealers
The sealers of cartons automate the entire process of sealing the cartons since these machines use adhesive tape. The first step of the process involves feeding a carton onto a conveyor belt which pulls it through the machine. Usually, sensors will check if the carton is correctly positioned although manual adjustments can be done too. Rollers then apply tape on the flaps of the carton to seal it. These machines are effective for precision work and can be designed to accommodate numerous carton dimensions, making them an invaluable addition to any industrial packaging system.
Various Kinds of Carton Sealing Machines
Uniform Carton Sealers
This uniform carton sealer type is used for operations where cartons to be sealed are of a particular size. Machines of this type require hardly any setup and can efficiently manage significant operations after being calibrated. These machines are widely used in industries of standardized sizes such as food and beverages and pharmaceuticals.
Random Carton Sealers
This type of random carton sealers does not require manual adjustment between boxes as these machines are equipped with sophisticated sensors and adjustable mechanisms that allow them to detect the dimensions of each carton. Random carton sealers are a lot more flexible and efficient since they can work with boxes of various sizes without needing to be set for each box individually. These machines are most effective somewhere specializing in a wide range of products.
Side-Belt Carton Sealers
This side belt carton sealer type uses drives in the form of belts mounted on both sides of the machine to guide the cartons through the sealing process. Side belt carton sealers are ideal for applications involving tall and narrow or lightweight boxes that tend to be unstable on top-driven systems. The construction offers better alignment and stability of the hinged side during the sealing process.
Carton Sealers with Top and Bottom Belt
These machines feature belts at the top and bottom, which assures uniform pressure distribution on the cartons being processed. This dual-belt system guarantees accuracy and consistency, making them suitable for sealing heavy or bulky cartons.
The sealing Process in Detail
The sealers are remarkably accurate since the steps and processes are interrelated and automated. To begin with, the carton is loaded on the machine, which has a certain set of sensors. The sensors measure the carton’s size and dimensions, allowing the machine to configure itself accordingly to ensure sealing it without manual adjustments. The type of sealer used determines how the carton will move through the machine. Side belt carton sealers, for example, provide belt support from the sides and are used for narrower cartons while top and bottom belt systems apply pressure evenly on the carton for heavy package cartons.
How can carton sealing machines improve packaging productivity?
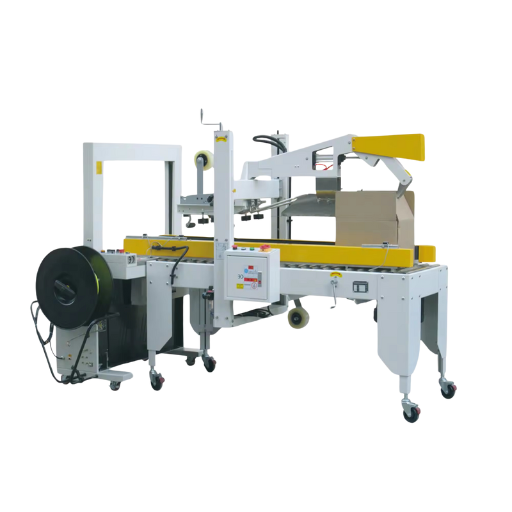
The productivity of packaging processes increases with the use of carton sealing machines as the seals are automated, which lessens manual labor and human error. The machines provide an effective and dependable seal, so the amount of rework and waste associated with badly sealed cartons is minimized. Moreover, these machines function at very high speeds, enabling the company to complete more packaging work in minimum time. The speed of the machines can be adjusted to suit various carton sizes so that there is no reconfiguration downtime, which saves time. It allows for greater efficiency in the packaging operation and cost savings while simultaneously improving operations’ throughput and quality control.
Streamlining automation during the sealing process
The sealing process can be automated through the use of machines which integrate carton sealing into packing lines for precision and efficiency. Such devices incorporate advanced techniques such as belts and pressure systems which can be adjusted to seal cartons of different sizes. Depending on the machine model, barriers can be sealed at speeds as high as 30 cartons per minute, which is immensely faster than doing the process manually. In addition to these faster speeds, automation also increases quality control by removing the inconsistencies associated with manual sealing where pressures and adhesiveness differ from seal to seal. Many machines are also equipped with user friendly control panels and adjustable sealing heads to improve productivity further, as operators can easily modify their adjustments when changing carton size. Automatic carton sealers prove invaluable for organizations trying to achieve higher operational effectiveness.
Increasing packaging speed and efficiency
Applying automated equipment to the packaging lines greatly boosts the speed and efficiency of the entire packaging process. Automated carton sealers work much more quickly than humans, further enhancing the overall output. These systems lower the risk of human errors, offer great productivity, and greatly reduce the need for rework or wastage. Also, new developments in machine design, including accurate seals and changes in carton size, make the entire packaging process more efficient and flexible. Well-designed automation also lowers labor expenses and increases output, allowing businesses to respond to greater demand in less time.
Saving on workforce expenditure and the margin of error
Automated packaging systems aim to reduce the dependency on manual work during repetitive tasks like carton sealing, sorting, or labeling. Modern sensors and programmable controls ensure that the operations are performed accurately, minimizing the chance of human error. Moreover, the use of real-time monitoring and diagnostic capabilities assists in solving issues instantly, thus improving operational accuracy even further. Innovations of this nature not only boost the workforce’s productivity but also contribute to saving costs due to reduced errors, waste, and the burden of supervision. Businesses that switch to automated working methods can consistently achieve set targets of efficiency and quality, even in a high production setting.
What are the key features to look for in a carton sealing machine?
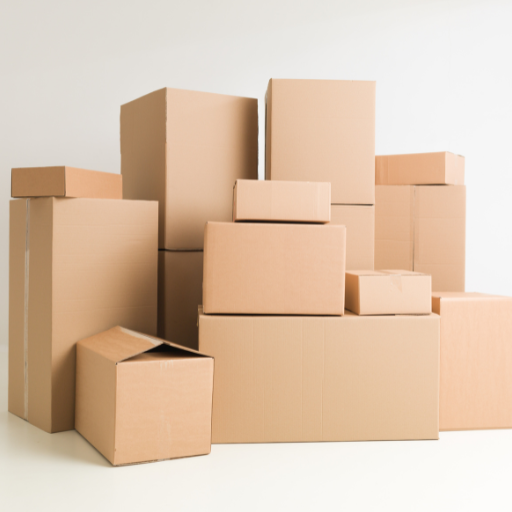
There are crucial features to evaluate while choosing a carton sealing machine. Such machines need to be capable of handling different carton sizes without recalibrating the machine manually. Sealing will remain secure during varying conditions due to high-quality sealing mechanisms that fasten tape, adhesive, or high-quality clips. These must operate at critical speed and throughput, so the machine should provide customizable settings that consider production targets. The machine needs to require minimal maintenance, as these factors directly influence long-term operational expenses. Making the machine easier to use by having advanced features like emergency shut off, will ensure operator safety while the machine is in operation. More sophisticated models with automation, such as programmable controls and sensors, guarantee higher efficiency and less error, ensuring impeccable results in tedious overworked tasks.
Customizable packaging box dimensions
Customizable packaging box dimensions are vital to maintain a desired operational efficiency in the packaging processes. These machines can be set to various sizes of cartons and boxes with little manual effort enabling quick changes during alterations. These machines also have adjustable side openings and height adjustments, improving work flow and saving the operator’s energy. This type of adaptability increases productivity while maintaining a reliable and cost-effective package to pack sealable products into, regardless of the complexity of the packaging.
Mechanisms for rolling out and applying tape
On the other hand, mechanisms for rolling out and applying tape aim to achieve a high level and accuracy of tape coverage on the packaged items. They normally consist of a tension managing system, a cutter, and rollers that help achieve proper coverage and minimize waste. Some systems come with powered pneumatic components for greater control in fast paced commercial settings. Other functions, such as sensors for automatic alignment and adjusting the rate at which tape is dispensed, greatly aid the changing demands of packaging materials. All these features help create tamper proof seals for the tape, improve workflow, and reduce manual work in the industrial setting of packaging institutions.
Considerations for Durability and Maintenance
- Material Robustness: Corrosion-resistant durable tape dispensing systems are commonly made from stainless steel or reinforced plastics, ensuring reliability even in the most demanding industrial settings.
- Component Longevity: Regular inspection and replacement of components are critical to maximizing operational efficiency. Quality blades, rollers, and tensioning systems are designed for longer service life, preventing breakdowns.
- Ease of Cleaning: Systems with smoother surfaces and easy-to-reach components require less effort to clean and, therefore, better control the build-up of debris or adhesives that can hinder performance over time.
- Lubrication Requirements: Periodic lubrication achieves smooth functioning and fast operation with minimal friction on moving elements such as rollers and cutting blades.
- Maintenance Accessibility: Part dis- and reassembly in modular systems is simplified, reducing the time needed for maintenance activities. Comprehensive manuals make maintenance easier.
- Preventive Maintenance Plans: Preemptive maintenance, like regular calibration of alignment and tension control mechanisms, ensures the prompt addressing of the system parts that show wear or malfunction.
- Environmental Resistance: Products and methods of isolation optimized for variation in temperature, humidity, dust, or chemical exposure provide reliability. Protective coatings and sealing enhance durability.
Semi-automatic vs. fully automatic case sealers: Which is right for your business?
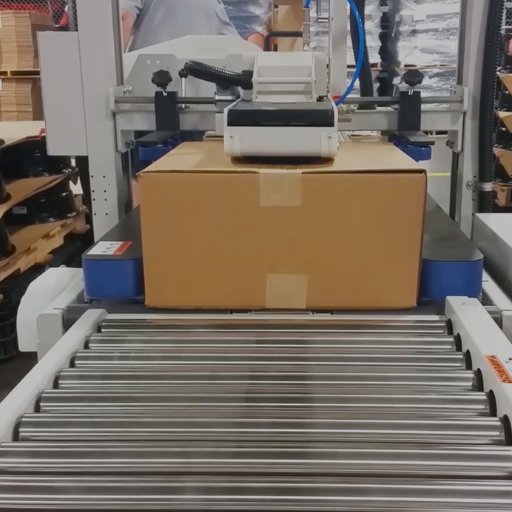
Using a semi-automatic or an automatic case sealer requires understanding your company’s operational goals and production capacity. Semi-automatic case sealers are economical and most suitable for low to medium production levels since they need the help of an operator for case feeding. These sealers suit businesses with moderate volume throughput and different case size requirements. Fully automatic case sealers are intended for fast operations requiring little human input, greatly increasing efficiency and accuracy. These systems are designed for large production facilities where higher output and lower labor costs are essential. Considering expense and the production speed needed helps narrow down the suitable option for your company.
Evaluating the Characteristics of Semi-Automatic and Fully Automatic Options
Their technical parameters and operational benefits in specific applications should also be evaluated when evaluating semi-automatic and fully automatic case sealers. Semi-automatic sealers generally need an operator to place the cases and set the machine to the required configurations for boxes of different sizes. Depending on the model, they can achieve sealing speeds of 10 to 20 cases per minute. For these machines, industrial production in small to medium scales is ideal. These machines are cheaper, require little investment, and are easy to maintain, but they require constant manual labor.
Fully automatic case sealers, however, do not allow for changes to be made manually, thus they free operators from any additional work other than maintenance and setup. They have advanced methods for case feeding, adjusting size, and sealing, which allows them to reach a production capacity of anywhere between 20 to 40 cases per minute or above, depending on the configuration. These systems usually include such options as automatic flap folding, accuracy in gluing, the ability to integrate into a production line, which makes them more cost-effective, though they are still more expensive. These systems can operate at maximum loads with little expenditure on scale optimization.
Guidelines for making decisions must involve considerations related to the production volume, budget, and the level of uniformity in the boxes. While semi-automatic models are ideal where there are lower throughput needs and variable case sizes, fully automatic systems are best suited for large, consistent workflows because they minimize downtime and maximize output.
Evaluating your packaging requirements and volume
When evaluating the requirements and volume of your developed packaging, start by considering the current production levels and the anticipated growth. Determine the average number of cases processed monthly or daily and track any seasonal variations in demand. Consider the uniformity of case sizes about the standard range of boxes or highly diverse assortment handled by your operation. For low to
Factors impacting cost considerations and return on investment
In analyzing the cost considerations, I start with the upfront capital needed for the assets, including their installation. Next, I assess the non-fixed costs incurred in maintenance, energy, and labor, as well as their complexities. To obtain an accurate return on investment, I determine how the assets will impact labor costs and overall business productivity in the long term. Finally, I consider the extendable nature of the system along with its longevity to ensure it corresponds with my operational objectives.
How to integrate a carton sealing machine into your existing packaging line?
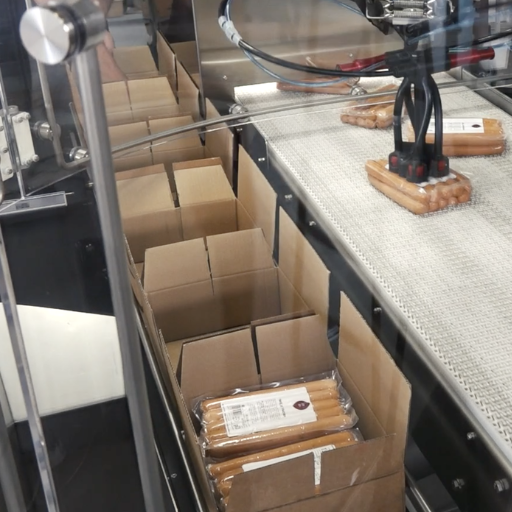
Incorporating a carton sealing machine into an active packaging line requires great precision and coordination to suit your existing operational workflow. First, evaluate how well the machine integrates with your current conveyor system regarding size and throughput. Place the machine where it can be fully utilized, for example, right after the product packing station. Calibrate the sealing machine to your carton dimensions, adjust the sealing materials, and run tests to ensure that the performance meets the requirements of standard production conditions. In addition to enhancing the machine’s operational efficiency, it is also essential to train the staff on the proper operation and maintenance of the machine to reduce unnecessary downtime.
Compatibility with conveyor systems
To begin with integration to conveyor systems, the width and height of the carton sealing machine must be appropriate for the conveyor’s dimensions. Second, the operating speed of the sealing machine must be equal to the conveyor’s throughput to guarantee a steady inflow of packages. Ensure that the conveyor, as part of the sealing system, provides stable movement so that there are no misalignments at the time of sealing. Also, inspect the machine’s infeed and outfeed requirements and ensure there are no areas in the packaging line that can result in bottlenecks and misalignments. Evaluation and fine-tuning modifications is also essential for achieving synchronized operations.
Training operators for optimal use
Effective operator training is essential for extending the life and improving the performance of carton sealing machines. Start with on-the-field training where operators learn crucial functions of the machine, from setting it up, performing the necessary operations, and troubleshooting in case something goes wrong. Cover methods of ensuring safety while operating the machine like proper evacuation procedures, moving components, and other emergency handling measures. Teach operators how to perform essential maintenance, such as cleaning parts, lubricating, and adjusting the settings for different carton sizes. Finally, validate that they know how to approach issue recognition, the diagnostic indicators, and the standard operating procedure for solving them. Regular refresher training and access to clear documentation ensure the works operate effectively and efficiently.
Effortless Streamlining of the Packaging Process
To maximize the efficiency of the packaging process, consider adopting a focused approach to operations that reduces downtime due to machine upkeep and integration. Install automated carton sealing equipment that is able to seal packages at a high speed and maintain quality control to ensure that the production line is in sync with the rest of the process. For instance, machines that are capable of sealing up to thirty packs every minute and have rapid dismantling features for tape rolls help eradicate bottlenecks in the system.
In addition, material usage optimization is just as crucial. Invest in high-quality and durable carton tape and machines that offer precise control over adhesive application. Ensure that settings are quick to match carton perimeter since loose adjustment leads to frequent jamming and idle machines, which result in wasted materials.
Regular maintenance reinforcement is essential for efficiency improvements over an extended period. Periodically, belts, blades, and rollers should be detailed to check for damage and replace parts as needed. To prevent unexpected failures and reduce downtime, consider applying systems with diagnostic sensors to keep track of performance metrics like motor torque and tape usage.
Ultimately, facilitating cooperation between the operating personnel and the maintenance crews guarantees that processes are streamlined and disruptions are addressed efficiently. An ideally trained employee operating the machinery at optimum settings will guarantee an effortless, highly productive, and trouble-free packaging process.
How to choose the right carton sealing machine for your specific needs?
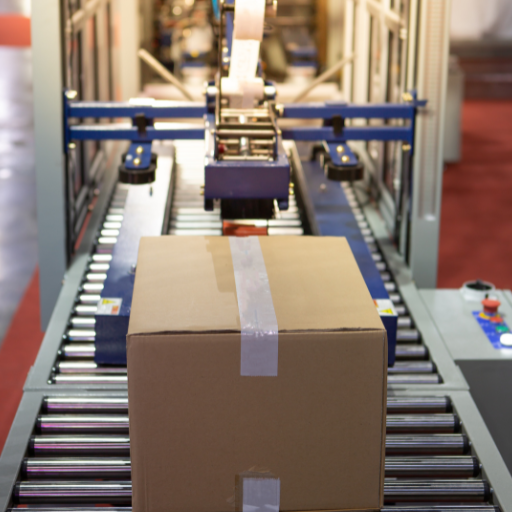
To find the best carton sealing machine, determine the volume and type of packages your business handles. Businesses that operate at a much higher production rate should use fully automatic machines to maximize output. In contrast, companies that have low to medium output environments could benefit from semi-automatic machines. Consider the size and shape of your cartons to ensure the machine has the adjustable features to box the selected cartons. Also, consider the type of sealing material required, like pressure-sensitive tape versus water-activated tape, depending on your packaging. The machine has to be looked at in terms of build quality, maintainability, and extra features such as advanced diagnostic systems that provide greater insights and help increase uptime. Balance solutions and services that are within your price range while still allowing for growth within your business in the future.
Understanding the Need for Packages
When looking for a carton sealing machine, you must pair your operation’s needs with the machine’s capabilities. With a throughput of over 20 cartons per minute, fully automatic machines have integrated conveyor systems connected to sensors that adjust to different box sizes. Alternatively, moderate throughput environments of around 5 to 20 cartons per minute often utilize semi-automatic machines which are more cost-effective as they require manual positioning of boxes.
For sealing materials, general-purpose applications can use pressure-sensitive tape dispensers, as they are easy to use. Water-activated tape (WAT) is ideal for heavier and high-value packages due to its stronger bonding capability and ability to self-seal. Make sure the machine’s tape width capability matches your packaging requirements, as standard model machines only support widths of 48 to 72mm.
Furthermore, assess the construction of an industrial-grade carton sealing machine with materials such as stainless steel or heavy-duty alloys that guarantee high durability in demanding industrial settings. Seek machines equipped with adjustable sealing heads and side guides for cartons measuring approximately 5 to 24 inches in width. More sophisticated machines may offer digital control panels or automated error detection systems for improved operational efficiency and reduced downtime. As a rule of thumb, invest in tools and equipment that meet current projects, but also can scale in the future.
Analyzing a popular product line
In analyzing popular brands of carton sealing machine, look for products that are reliable, adaptable, and efficient. Leading models often boast of rugged design, adjustable settings for work with carton sizes, and support for both pressure sensitive and water-activated tape. Some of the more advanced options include automation features, such as self-calibration or error detection, to further increase productivity and decrease maintenance needs. These brands offer long term value due to their reputation, extensive warranties, and reliable technical support for seamless integration into your packaging process.
Looking for professional guidance and explanations
One’s approach toward professional guidance and demonstrations should be methodical. First, the explanation provided should have the subject matter defined, and the definition should be corroborated with reliable information. One should start off by stating clearly what the primary question or problem that needs to be addressed is and make certain that the responses provided are actionable and attested by relevant evidence or precedents. Reduce overlap and distractions, and work towards highlighting the primary points that need addressing, and do it in a precise manner that showcases authority. Make use of graphics, and or explain in steps whenever necessary so as to aid comprehension and participation.
Reference sources
Frequently Asked Questions (FAQs)
Q: What is a carton sealing machine and how does it work?
A: A carton sealing machine, also known as a case sealer or box taping machine, is a piece of packaging equipment designed to seal boxes or cartons automatically. It typically uses sealing tape to secure the flaps of a box, ensuring consistent sealing and improving efficiency in packaging operations.
Q: What are the benefits of using a case sealing machine?
A: Case sealing machines offer several benefits, including increased productivity, consistent sealing quality, reduced labor costs, and improved packaging efficiency. They can handle different size boxes and provide secure sealing, making them ideal for various industries and packaging needs.
Q: What types of case sealers are available?
A: There are several types of case sealers available, including semi-automatic case sealers, random case sealers, and standard case sealers. Some common variations include top and bottom tape sealers, side belt sealers, and random semi-automatic sealers. The choice depends on your specific packaging requirements and production volume.
Q: How do I choose the right case sealing machine for my needs?
A: To choose the right case sealing machine, consider factors such as your production volume, box sizes and types, sealing tape preferences, and available space. It’s also important to evaluate features like adjustable height and width settings, tape head options, and whether it’s a random or uniform case sealer. Consulting with a packaging equipment supplier like Interpack can help you find the best solution for your needs.
Q: What is a random case sealer and when should I use one?
A: A random case sealer is designed to seal boxes of varying sizes without manual adjustments. This type of machine is ideal for operations that handle different size boxes frequently. Random case sealers use sensors to detect box dimensions and automatically adjust to seal each box correctly, improving efficiency in packaging lines with diverse product sizes.
Q: How can 3M sealing tape improve my packaging process?
A: 3M sealing tape is known for its high-quality adhesive and durability. Using 3M tape with your case sealing machine can help improve the security and reliability of your package seals. It offers strong adhesion to a variety of surfaces and can withstand different environmental conditions, ensuring that your packages remain securely sealed throughout the shipping process.
Q: What maintenance is required for case sealing machines?
A: Regular maintenance of case sealing machines typically includes cleaning the tape heads and rollers, checking and replacing worn parts, and ensuring proper lubrication of moving components. It’s also important to regularly inspect the machine for any signs of wear or damage. Proper maintenance helps ensure consistent sealing quality and extends the life of the machinery.
Q: Can case sealing machines be integrated with other packaging equipment?
A: Yes, many case sealing machines can be integrated with other packaging equipment to create a complete packaging line. They can work in conjunction with case erectors, conveyors, and labeling machines to form a comprehensive packaging solution. This integration can significantly improve overall packaging efficiency and throughput.
Q: How can semi-automatic case sealers help improve packaging efficiency?
A: Semi-automatic case sealers can help improve packaging efficiency by reducing manual labor and increasing sealing consistency. These machines require an operator to feed boxes into the sealer, but they automatically apply tape to seal the box. This semi-automated process is faster and more consistent than manual taping, making it an excellent solution for businesses looking to boost productivity without fully automating their packaging line.