In the modern pharmaceutical and nutraceutical market, accuracy and speed are crucial elements of capsule production. This detailed manual seeks to provide you with adequate information that will assist you in the selection process of a capsule-filling machine. We will review the different types of machines available, consider the scales of production and the machine requirements, examine each machine’s parameters, and highlight crucial aspects that should be considered before buying a machine. Additionally, you will learn about the pros and cons of semi-automatic and fully automatic machines, how to maintain them, and some mistakes to avoid. Therefore, such an understanding will help you optimize your production process using the most appropriate capsule-filling machine.
What is a capsule-filling machine, and how does it work?
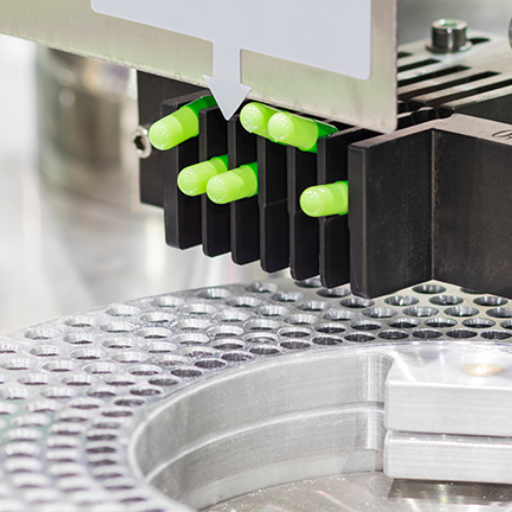
A capsule-filling machine is a kind of machine that is designed to fill empty capsules with a range of substances, such as powders, granules, and liquids, accurately and efficiently. These machines are very important components on the production lines of the pharmaceutical and nutraceutical industries, where there is a need for high consistency and quality. Capsule-filling machines today function as more universal automatic systems, including capsule filling and sealing and exposing capsules to orifices. The initial stage involves capsule ‘dosing’ whereby the capsules face up and the two parts are pulled apart. The filling material’s volume is measured and placed inside the body of the capsules. Then, the two parts are replaced to their original position, enclosing the capsule filling in place. There exist varieties of capsule-filling machines for different volumes of production. Some are considered to be semi-automatic or manual, which will need considerable operator skills, while others are automatic and will perform similar functions at high speed with incredible accuracy and lower human intervention, making production rates much more effective.
Understanding the basic components of a capsule filler
To begin, it’s worth noting that a capsule filler is customarily composed of several key parts, and to the best of our understanding of how this apparatus operates, it is ideal for dissecting these parts. Apportioning predicaments are the centermost aim of the capsule orienting device, which is part of every capsule filler and which makes certain that the parts of capsules are correctly separated for assembling purposes. Then, there is a mechanism in which the capsule is separatory, and its purpose is to unassemble stocks into their cap and body.
Then, as it may be obvious, comes the dosing system. This system’s purpose is critical as it carries out the common function of measuring and dispensing the correct amount of substance into respective capsules. So far, in our work, the most common, however, have been musk enl sheet letter roll and the taper meznith, which use tampons, doctor and allow for bullet-type fillings to contain paste or liquid materials. Wherein, technical parameters don’t vary a lot since there are few options; dosing volume range which usually is set between 5mg to a 1000mg and the fill weight agreement which stands at & plus or minus 3.
Under the dosing system sits another system called the closing system. The reason for this mechanism is to ensure that the two ends of the capsule are reconnected securely without exposing the fill. In the end, though, the use of the ejection system in the capsule ejects the filled parts and allows filling heads’ daunting processes to repeat again.
All the parts of the capsule, start off as empty shells until the entire system fits together properly, thus cycles of efficiency and productivity remain steady. One thing that has to always stay in mind while working on the optimization of production for capsules in accordance to the technical specification is that these elements are necessary.
How does an automatic capsule-filling machine operate?
Interestingly, an automatic capsule-filling machine adopts a complete array of automatisms designed to fill a large number of capsules reliably and accurately. To begin, the machine supplies the production side with empty capsules which are placed in the orienting device within the filler for proper positioning. For each veterinarian using capsules, a capsule combiner handiwork tool removes the cap with dexterity from the capsule’s case. After the secretion, the fill materials, which are mostly in powder or pellet forms, are introduced into the powder’s circle through the dose induction unit.
The filling system could have the following features: the machine can run from capsule volumes of 50mg up to 1500mg, the dose weight can vary by ±3% of the filled dosages, the throughput of the machine depends on its size, typical maximum is around 200.000 tabs/hour. The closing mechanism of the machine skillfully closes the half of the filled capsule with the other half so perfectly that there is no possibility of leakage while in transit. Last but not least, the ejection system that effortlessly communicates the finished capsules to the outside environment moving around and the waiting time being minimal to none. The entire process requires exact measurement and adjustment of various factors involved in making the final quality of the currently produced capsules satisfactory to the standards set by the industry.
The role of sensors in modern filling machines
Currently, in filling machines, most sensors are the core of precision, efficiency, and safety. Sensors are used in my understanding regarding the actual operation of the filling machines to oversee the fill amount for each of the capsules. They help capture possible deviations and send notifications to the control systems in real time for corrective measures. In addition, sensors assist in controlling the correct orientation and position of the capsules over the entire operating cycle of the filling machine. Advanced sensor technologies enable machines to work with less human control thus reducing the chances of errors and enhancing the quality of production processes.
How to select the right capsule size for your needs?
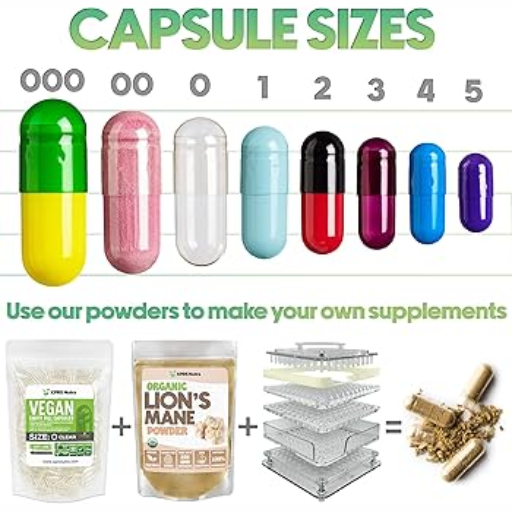
Filling even the tiniest capsule poses a challenge in this production process owing to accuracy, dosage, and user consumption. Capsules are available in six possible sizes: 000, 00, 0, 1, 2, 3, 4, and 5 — the largest being 000 and the smallest being 5. The volume and weight of the filling material are important aspects to consider for selecting the correct size. Consumers may have difficulty swallowing larger capsules, for instance, the 000-sized capsules, which, on the positive side, may contain a greater quantity of fill material. Customers who prefer smaller doses, such as the 4 or 5 sizes, may be able to swallow them more easily but may not get the desired dosage in one go. As a last observation, end-user preferences and potential dislike for a given capsule size and the volume of medication to be consumed are also noteworthy. Looking at a capsule size chart will provide a good idea regarding the volume of various sizes of capsules, and more often than not, it is a good practice to prepare test batches to see how different sizes suit your product.
Comparing sizes 00, 0, and 1 for gelatin capsules
Weighing in the important factors between dimensions 00, 0, and 1 of gelatin capsules can be troubling for consumers. However, just a few considerations would help narrow down the right size for the users. First size 00 has an approximate capacity of 0.95mL, which makes it suitable for containing a higher content and, therefore, enables consumption that targets a specific fill material. Consequently, this high capacity makes 600 to 1100 mg feasible within these capsules, depending on the density of the material. The second size of capsules which are size 0 can accommodate more than 400 and below 800 milligrams or 0.68mL of fill material. It would be safe to assume that size 0 are slightly sleeker than size 00. However, both sizes are popular among consumers as they don’t choke and are easy to swallow. For higher dose applications, size 1 capsules are not as effective as they only accommodate 300 to 600 mg of material, having a point-five mL capacity. Each size varies as per the consumer’s need, for example size 00 is not ideal for all contractors as it offers a broader size which some users may not be able to work with, in contrast 0 and 1 are better suited for easier consumption. Conducting evaluation tests with the required fillers can optimize user consumption and make it more feasible.
Understanding vegetarian and vegan capsule options
The increasing awareness of dietary restrictions and ethical issues has triggered the interest in vegetarian and vegan capsule options. Unlike their bovine or porcine subspecies counterparts, vegetarian capsules are not derived from gelatin, but instead from Hydroxypropyl Methyl Cellulose (HPMC), which is plant-based. Similar capsules are the so-called “vegan” capsules that do not contain any animal-derived components. They also provide the same stability and functionality as gelatin capsules, enhancing features such as non-GMO claims and satisfying dietary needs. With regards to a broad spectrum of formulations, these capsules will be applicable, however it is important to always seek to check the certifications or specifications of suppliers’ products to ensure that the customers’ needs will be adequately satisfied. Also, for vegetarian or vegan end-users of the product, a test batch will be useful to check the sustainability and efficiency of the fill material against the capsule’s vegetative or vegan contents to give satisfaction.
Choosing between different capsule sizes for varied applications
In determining the appropriate capsule size for a given application, there are requirements to be met to achieve the dosage requirements. Generally, capsule sizes are 000 as the largest to 5 the smallest, which correlate with the specific volume and type of the ingredient(s) being filled within them. For example, size 00 capsules are suitable for powders that require high doses as they can hold up to between 600mg to 1100mg whereas size four consisting of around 120 – 240mg will hold lower dose powders only. To select the best capsule size that meets your needs, assess the flow properties, density and particle size of your fill material. Make sure to verify these parameters during test runs validation to make certain that they are suitable and feasible for manufacturing purpose. For patients to feel comfortable with the product, its efficiency needs to be accurate, hence the need to use the appropriate capsule size. To broaden one’s understanding, it may also be important to communicate with your supplier regarding registries and working documents, which is also crucial in the selection of the target consumer.
What are the benefits of using a fully automatic capsule-filling machine?

In the pharmaceutical and supplement sectors, automatic capsule-filling machines are a positive change in the reasoning process of the machinery and the workload balance. Due to this, the output volume significantly increases compared to the volume generated via manual labor. Advanced technology and sensors are employed to eliminate wastage, and fill weights are constant in each capsule, thus improving dosages. There is a reduction in labor, which can better be utilized in other important activities, and at the same time, human blunders are minimized. Also, the automatic process complies with high sanitary standards, which are important in the manufacturing of any drug. The great benefit of switching to fully automatic systems for large-scale manufacturers is speed, precision, and quality since these machines provide the most effective balance.
Increased production capacity with fully automatic systems
The manufacturing process becomes a lot easier with the use of fully automatic capsule filling systems therefore increasing production capacity. According to some of the best industry knowledge, these systems are capable of working at high speed and constantly increasing the number of capsules produced on a time scale. Robotics and real-time monitoring are cutting-edge technologies these machines use to provide efficiency while minimizing downtime from maintenance or manual work. In addition, they also allow the operation to be flexible, enabling fast and quick changeovers from one product formulation or batch size to another. Such responsiveness does not only enable manufacturers to respond to different market needs within quick time frames but also enables long production runs without loss of quality and accuracy. As such, adopting fully automatic systems becomes a great step forward for manufacturers who want to grow their operations efficiently.
Ensuring quality and precision in capsule-filling
My aim is to utilize industry best practices and the latest technological developments to achieve accuracy and quality for capsule-filling jobs. In this regard, I always give precedence to equipment that has installed high-end control systems which allow overseeing of the production processes at each stage. This guarantees the uniformity of the produced capsules’ weight and durability, which all comply with the required regulations. Also, I carry out regular equipment servicing and employee retrainings to improve the effectiveness of the operations and reduce the chances of errors. When new changes are introduced in capsule-filling machines and jet technology, I make sure the quality and accuracy of the capsule-filling processes remain unaffected by the changes on a batch scale.
Cost-effectiveness in high-volume capsule production
Similarly, there are a lot of injections that are popular throughout the world. We will examine the usage of tuberculin syringes and injections in the dermatology section of the paper. Tuberculin syringes and injections are used in dermatological allergic reactions. Tuberculin syringes and injections can easily work fast, making them quite popular and appealing. Tuberculin syringes and injections can be used practically in transitional areas where status inconsistency exists. In cases of Tuberculin syringes, the volume of injected solutions is usually very small which is why they are also appealing. We can also see from the previous sections that Tuberculosis is seen as a global health concern affecting many people around the world. This is a worrying sign as It would make it seem as if tuberculin injections have a wide scope to prove their value in the global market. The Tuberculin injections market has a lot of potential worldwide. This means Tuberculin has a huge potential to be the solution people need. If we also consider the cases around the world, it only makes sense for this product to be widely used in places that have a high population density. Areas which already have a lot of health concern have been pointed out, population density would only make everything more concerning. Mexico, Vietnam, and the UK are a few countries that are already expecting an increase in the cases of Tuberculin injections.
What materials can be used in capsule filling?

Hydroxypropyl methylcellulose (HPMC) and gelatin are the two most popular raw materials for capsule filling. Traditionally, gelatin, which comes from animal collagen, would be considered the best, as it enables the formation of thick and pliable shells that can dissolve flawlessly in the stomach. This particular characteristic makes it great for materials that need to be broken down quickly. HPMC, on the other hand, is a plant-based capsule filling without the use of any animal products, so this is ideal for vegans and vegetarians as well. Moreover, they have very strong stability across various temperatures and humid conditions so that they do not compromise on the contents. In this way, each material has its own advantages; hence, the selection largely depends on the intended diet and storage conditions. Moving on, using technical excipients such as fillers, binders, and lubricants to enhance the flow and fill of the substance was also helpful and contributed to the capsulation process.
Using powders and granules in capsule fillers
While using powders and granules in capsule fillers, I emphasize on the material’s flow properties so as to deliver precise doses in every single case. This means that the relevant binders have to be used to enhance the flow properties of the powder mass and avoid its segregation during encapsulation. Also, I am interested in the size and shape of the particles as these affect the uniformity and density of the mass and, eventually, of the final dosage form. In order to increase the efficiency of the process, I use modern methods such as vibration compaction and electrostatic charging, which help prevent cell blockage by providing a uniform feed and maintaining low moisture levels. After controlling these factors, I can obtain good-quality capsules developed according to international standards.
Filling with liquid and other non-traditional materials
As an expert in Capsule Filling Machines, I recognize that the most arduous task that one would be faced with would be how to fill capsules with unconventional or highly viscous fluids. The question arises as to how to extract capsules that do not lose their structural integrity. Using oil gel caps or polymer capsules would be ideal when filling with a liquid, especially something reactive with the capsule’s contents. Unarguably, gel caps work best for filling liquids, although it is vital to ensure that the capsule doesn’t reach a temperature lower than 0 degrees Celsius. Other technical information for the effective encapsulation of fluids ensures that the fluid encapsulated will flow and change shape easily. Providing optimal time between 1,000 and 10,000 cP ensures effective fissuring and provides filling below the rotational point. Methods for sealing like LEMS Capping or Banding Tubes Removing or at least minimizing Electrostatic Transference are also considered. For other unique materials, the capsule barrier and the barrier material’s mechanical strength and composition mustn’t change over time. Lowering after compression by employing a vacuum helps to fill the capsule consistently and increase the liquid volume of the capsule. On account of paying attention to these factors, I design capsules that can withstand diverse liquids for different applications.
Considerations for empty gelatin and veggie pill capsules
In the past, I would consider several factors before settling on either empty gelatin capsules or empty veggie pill capsules, which I now realize can be resolved by looking up leading websites. First, you need to consider the customers’ dietary limitations and preferences, as gelatin capsules are animal-derived and not suitable for vegans or vegetarians, while veggie capsules are more suitable. Then I look into the dissolution characteristics as gelatin capsules have a rapid stomach dissolution, which is helpful in the case of rapid releases. In contrast, the veggie capsules can be somewhat quicker but more controlled regarding the breakdown. Further, I consider the fill material that is compatible since some liquids and hygroscopic entities react differently when in contact with each capsule; hence, their stability and shelve life vary. Such factors help determine the most appropriate capsule type that meets the product’s demands and the consumer’s requirements.
How do you maintain and troubleshoot a capsule-filling machine?

To extend the life and longevity of a capsule-filling machine, it is paramount to maintain it properly. Regular maintenance procedure should include cleaning after every batch production, all contact parts should be cleaned to avoid contamination and smooth production processes. Also, lubrication of moving parts should maintain a schedule by the manufacturer’s recommendations to reduce wear and tear on parts. Additionally, rubber gaskets, O-rings, and even rusted filters are known to be part of the life cycle of the machine to reduce downtime.
When resolving some of the simple issues, taking things step by step helps. For specific cases, when capsules do not dispense properly and get choked on the way through feeding parts, jams of capsules occur. Automatic settings of the machine alter the filling weight and, therefore, should be adjusted at times manually. If the machine does not work correctly – I mean, does not turn on, or stops working mid-sequence – check the source of power, the power source can be the problem or just loose fuses. Most – if not all – machine operational problems are solved with the help of proper – or some might argue, regular – software updates. If possible, maintain and document all troubleshooting for future information needs.
Routine maintenance tips for capsule-filler machines
The efficacy of any capsule-filling machine is dependent on its robust maintenance schedule. A thorough daily clean-up of the machine’s interiors and exteriors is fundamental to curtail dust and other dirt from settling therein, which has the potential to compromise on the processes and even the quality of operations performed. Use appropriate cleaning products to remove all cleaning agents, including soap. Routinely maintain and provide lubrication to dynamic portions of the machinery alongside horsepower, as instructed by the maintenance schedule, as this will reduce mechanical wear. Maintain precision by checking the alignment of the capsule loading area and filling portion to cut the differences in capsule weight. Conduct timely inspections on seals and gaskets to establish their level of wear and judiciously replace them when necessary to eliminate unplanned idle times. Ascertain that all safety guards and features for stopping a machine in an emergency are acceptable. Lastly, maintain all the maintenance logs, specializing them for inspections, repairs, and replacements of different parts, hence achieving easier future diagnosis and guaranteeing the greater efficiency of the machine.
Common issues and solutions for automatic capsule filler machines
There are several capsule filling and sealing machine problems and issues that may be encountered, which may disrupt the operations of such machines even though advanced technology designs may automatically operate them. One of these problems is the filling of the capsules to the desired weight, which hardly comes out as anybody would expect. More often than not, this is hard due to an improper calibration or an incorrect powder flow setting of the filling system. In this regard, it’s suggested that, as per the instruction manual, the powder’s appropriate particle size and moisture are to be located and maintained. Furthermore, fine-tune the filling point according to the technical instructions given from the manufacturer, for instance, fill weight may usually be variably set by ± 2 – 5 percent based on volume taken as the standard. Insufficient dispensing or blockage due to reinforcement pins and doctor designs are other concerns, and an aggravating concern is the capsule jamming. Regular maintenance and upkeep of machines will solve these capsule problems because they can help maintain proper alignment and component wear and tear. Vibrations of machines can be a cause of many operational errors, and these are quite frequent due to improper mounting of the machines. The basic aim should be to provide rollover and secure a constant direction of machine load. As these have a compressing force, they should be maintained through timely preventive maintenance and operations to keep them within 1.5 mm/s to 3.5 mm/s. For example, they are stabilizing with a locking clip, using a pin controller or Protector brands such as Alex products of rest bands models. Outlining these concerns in an organized manner will enable any organization to have an optimal production time and avoid any unwanted delays due to these machine problems.
When to contact a capsule filling machine supplier for support
Whenever I experience ongoing problems with my capsule filling machine after performing the required troubleshooting and maintenance, I communicate with my supplier. Unexplained faulty machine operations, reduced production effectiveness, and whenever machine discrepancies appear, and taint quality, sent by machine and my solutions do not help. Moreover, if the machine needs to be professionally repaired or parts not provided in the manual need to be replaced, it is better to consult a supplier about it. I send them requests whenever I need assistance with updating software or changing the equipment, which can be quite complex and require skills that my available workers lack. Keeping in touch with the supplier also helps in keeping the machine in good working condition for a longer period.
References
Frequently Asked Questions (FAQ)
Q: What factors should I consider when choosing a capsule-filling machine?
A: When choosing a capsule filling machine, consider factors such as the type of capsules you plan to use (gelatin or vegetarian), the size of the capsules (such as size 000 or 2 3 4 5), the filling material (powder, pellets, or liquid), production capacity, the level of automation (manual, semi-automatic, or automatic), and your budget. It’s also important to evaluate the machine’s compatibility with your pharma specifications and the ease of changeover and maintenance.
Q: How do I determine the right size for empty pill capsules?
A: The right size for empty pill capsules depends on the medication dosage or supplement you plan to fill. Common sizes include 000, 00, 0, 1, 2, 3, 4, and 5, with size 000 being the largest and size 5 being the smallest. When selecting the appropriate capsule size, consider the volume of the active ingredient and the filling capacity of the capsule machine.
Q: What is the difference between gelatin capsules and vegetarian pill capsules?
A: Gelatin capsules are made from animal by-products, primarily collagen, commonly used in the pharmaceutical industry. Vegetarian pill capsules, on the other hand, are made from plant-based materials such as hydroxypropyl methylcellulose (HPMC) and are suitable for those with dietary restrictions or ethical concerns. Both types are available in various sizes and can be used with a capsule machine.
Q: How does a semi-automatic capsule-filling machine work?
A: A semi-automatic capsule-filling machine combines manual and automated processes. The operator typically loads empty capsules into the machine, automatically separating the capsule’s upper and lower halves. The filling material is placed into a hopper, and the machine uses a dosing disc and tamping pin to fill the capsules. The operator then manually closes the capsules. This type of machine offers a balance between speed and precision.
Q: Can a capsule machine fill both powders and liquids?
A: While most capsule machines are designed to fill powders, some models, especially automatic liquid filling machines, can handle liquids. It’s important to check the machine’s specifications to ensure it meets your specific filling needs, whether for powders, liquids, or both.
Q: What is a pill filler, and how is it used in capsule filling?
A: A pill filler, also known as a capsule filling device, is used to accurately and efficiently fill capsules with powder or other materials. It typically consists of a base with holes to hold the capsules empty, a dosing tray for the filling material, and a tamping pin or mechanism to ensure the capsule is filled evenly. Pill fillers are used in both manual and automated capsule-filling processes.
Q: How do I maintain and clean a capsule-filling machine?
A: Regular maintenance and cleaning of a capsule-filling machine are essential to ensure its longevity and performance. Follow the manufacturer’s guidelines for disassembling parts such as the dosing disc, hopper, and tamping pin. Use appropriate cleaning solutions to remove any residue or buildup, and inspect the machine for wear and tear. Proper maintenance helps prevent capsule rejection and ensures high-precision filling.
Q: What is the importance of capsule closing in the filling process?
A: Capsule closing is a crucial step in the filling process, ensuring the contents are securely enclosed within the capsule. Properly closed capsules prevent leakage, contamination, and degradation of the filling material. Capsule machines are designed to close capsules tightly, and it is important to regularly check and adjust the machine’s closing mechanism to maintain the integrity of the filled capsules.
Q: What are the advantages of using a high-precision capsule-filling machine?
A: High-precision capsule filling machines offer several advantages, including accurate dosing, consistent fill weights, and reduced product waste. They are particularly beneficial for pharmaceutical applications where dosage accuracy is critical. These machines often feature advanced technologies such as dosing discs and tamping pins to ensure precise filling and are suitable for both R&D and large-scale production.