In today’s business world, automated packaging systems are readily apparent in various industries. Packaging systems are becoming more complex, just like the machines used in robotics, AI, and the Internet of Things. From product identification to sorting, labeling, sealing, and even palletizing, the entire procedure is now automated. Such systems not only mitigate the costs associated with manual workforce, but also optimize profitability by reducing error margins and increasing overall production. This article examines the main types, advantages, challenges, and factors to consider when using automated packaging systems in business for adequate growth and sustainability.
What are automated packaging solutions and how do they work?
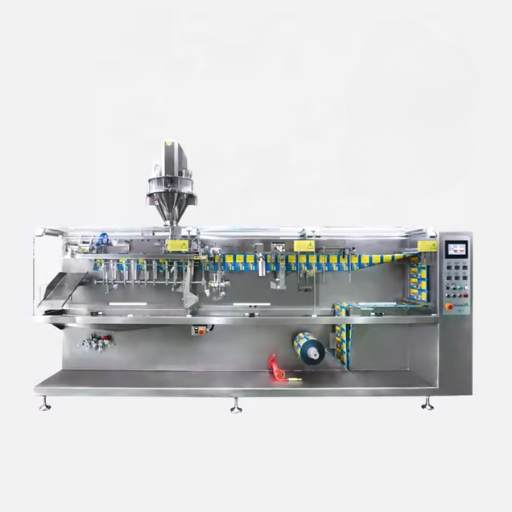
Advanced machinery and software are used to produce automated packaging machines to make preparing goods for shipment easier and faster. Along with sensors, mechanical parts, and PLCs, intelligent software and robotics is utilized. These components work together to take care of processes like packaging, sealing, and labeling with high accuracy and efficiency. Due to the reduction of manual labor needed, workflows improve, and packaging operations have more consistency. Systems can be easily customized to fit a company’s needs based on how specific a product is and its volume requirements.
Break Down Components of Automated Packaging Systems
Conveyor Systems
The main conveyors of the automated packaging solutions are conveyor systems, which also allow for packaging transitions in diverse stages. To enable transitions with no interruptions and minimize handling, these systems are customizable for a variety of products, speeds, and layouts.
Robotic Arms
Using robotic limbs, a wide range of products and sizes can be picked, placed, stacked, and organized without errors. With today’s advanced sensors and robotic grippers, throughput, along with the accuracy and speed of replacing products, have drastically improved.
Programmable Logic Controllers (PLCs)
The PLC serves as the core of the automated system since it can control multiple devices in the automated process and coordinate their interaction and sequence. It’s exceptionally trouble-free and flexible, which permits it to control procedures in great detail regarding the particular requirements of the production.
Sensors and Vision Systems.
Vision systems and sensors are essential for quality assurance and process monitoring. For example, the components can establish the element’s position, size, and defects and adapt parameters and conditions to achieve optimum process reliability and consistency.
Packaging Machines.
These comprise form-fill-seal machines, carton erectors, and shrink wrappers. These machines work together with the other components to ensure that the products are packaged appropriately according to industry and distribution standards.
Labeling Equipment.
Automated systems that apply labels or barcodes to packages or products for branding or regulatory purposes ensure that products are well identified. These machines work precisely to fasten compliance processes while significantly reducing manual labor requirements since they can process large amounts of items swiftly.
Software and Integration Platforms.
Modern software controls all units of the system by linking them together, communicating with the machines, and monitoring their performance. These platforms also combine multiple functions into one platform for easier access to the operators, who control the processes and make decisions based on the information gathered through the user-friendly interface.
How automation improves the effciency of packing products
Automation improves the efficiency of packing products by maintaining the same level of speed and productivity throughout the process and providing a maximum reduction in inaccuracies and mistakes. Nowadays, with advanced software and machines, handling materials, filling out containers, sealing, and attaching labels on packages are performed much faster than people can do by hand. This saves money, reduces waste, and provides product quality consistency. In addition, integration enables real-time monitoring of the systems, so operators can quickly pinpoint and fix issues to boost productivity. Furthermore, Automation improves scalability, which helps businesses meet varying production levels without risking efficiency or industry regulation compliance.
Types of automated packaging machines: from semi-automatic to fully automated
Semi-automatic machines are designed in a way that requires assistance from a person before any mechanization is performed. These machines can automate many tasks but people still have to perform some steps like initiating the packaging, placing the materials into the container, etc. Unlike fully automated systems, these machines are more cost effective and can also be used aside from intermediate and advanced packaging. Other examples are semi-automatic shrink-wrapping machines and manual aid-sealing machines capable of wrapping around 10 to 30 packages per minute per the configurations.
Automated packaging machines are built as autonomous systems that complete the entire packaging cycle with minimum human input for maximum productivity. These machines have sensors, robots, and programmable logic controllers (PLCs) to automate product feeding, weighing, sealing, and even barcode printing. These machines achieve high throughput rates, often exceeding 100 packages per minute, during large scale production and ensure a high degree of accuracy and uniformity. Fully automated systems have critical technical requirements that need to be met like capacity (output rate), material compatibility for films or cartons, and even power requirements that must match the specifications of the production line. These machines are crucial for industries with extreme volume demand that need high efficiency and uniformity.
How can automated packaging systems boost productivity in your business?
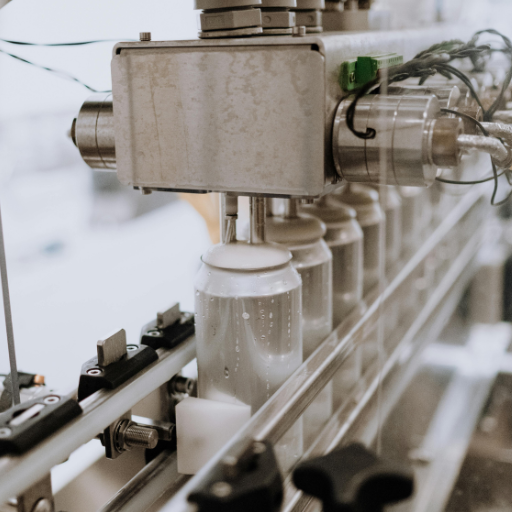
Automated packaging systems improve the way the production process is run. They eliminate manual labor, Errors, and inefficiency along with other inefficient processes. These systems enable greater production effectiveness by automatically filling, sealing, or labeling containers. With such tools at hand, the overall time needed for production drops significantly. By ensuring that packaging meets predefined standards, waste is minimized while output reliability is strengthened. Besides, they allow companies to adjust to sudden changes in demand without affecting overall performance. With automatic systems, operational costs can be reduced in the long term as reliance on human power is diminished, and equipment is actively monitored through diagnosing in real time.
Increasing throughput with high-speed packaging machinery
High-speed packaging machines increase production effectiveness through their ability to operate on a higher scale without sacrificing packaging precision and consistency. Multi-step processes like filling, sealing, and labeling simultaneously eliminate bottlenecks and other slow downs. Advanced servo systems greatly improve the machines’ monitoring capabilities and reduce the maintenance required, making them far more efficient. These machines further support a variety of packaging formats and materials, increasing the overall production capability.
Saving people costs and diminishing human mistakes when packing
Saving people costs and reducing human mistakes during packing processes can be done by automated systems that reduce reliance on human input. Automated packaging systems minimize errors due to neglect and maintain a steady level of productivity thanks to embedded sensors and advanced software. Moreover, while the system can greatly improve quality, it can also complete monotonous tasks at an extraordinary pace, therefore saving on labor costs. Reliability and cost-effectiveness can further be enhanced during the packaging process by integrating machine learning and real time monitoring, which will identify problems and solve them before they get out of hand.
Optimizing and maintaining the quality of a product using automation
Using automation is key in optimizing the quality of a product and ensuring consistency in detail by maintaining uniformity in production and reducing any variability. Cutting-edge automated systems that utilize calibrated instruments and real-time data take precision to a whole new level. In addition to increasing production uniformity, they significantly reduce quality defects across different batches manufactured. In addition, other modern quality control methods, such as optical sensors and AI, can be used to monitor manufacturing processes in real time and react immediately to any strange changes. Automation guarantees persistent quality while maximizing effectiveness in the processes of production.
What are the key benefits of integrating automated packaging solutions?
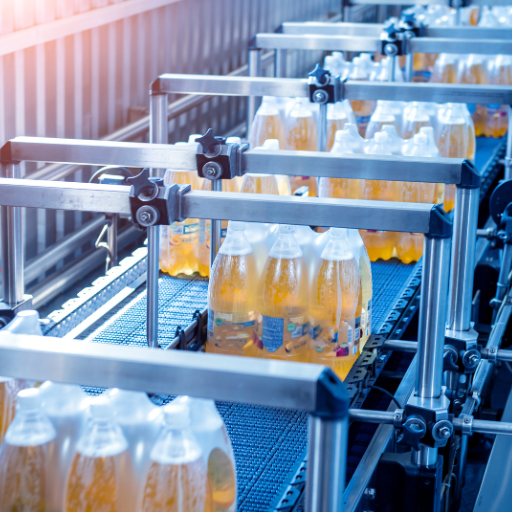
Adding automated packaging provides essential benefits that improve operational efficiency and productivity. These systems boost production by automating repetitive tasks, allowing companies to increase their output while using less labor. Reducing manual input also minimizes errors, resulting in greater accuracy and consistency in the packaging process. In addition, savings are achieved from reduced resource and material waste, and advanced monitoring and predictive maintenance systems further provide maximum uptime. Moreover, these solutions improve safety at work because they automate dangerous tasks, thereby improving employees’ overall health.
Smoothly integrating robotics and new technology in existing production lines
It is crucial to ensure great compatibility, efficiency and minimal interruptions when integrating automation into a production line. The first step in the automation process is carrying an assessment of the current systems being utilized in the company. The assessment is done to identify specific tasks which, in this case, are the most efficient for automation. In addition, it is also essential to evaluate the parameters such as equipment compatibility, load capacity, speed, and accuracy that the automation tools are specific to the demands of the line. For example, these days, conveyor systems and robot arms used in application are customized to the application needed. Robot arms for example, are made in different payload capacities from 5kg to 200kg which matches the application need. In addition, conveyor systems must match the speed and weight specifications of the production line.
Another aspect of system integration is including new automation tools with other machinery through programmable logic controllers or PLCs. ‘Talking’ between devices are frequently done using networking standards like Ethernet/IP or Modbus TCP for fast communication. To decrease the chances of system failure and improve reliability, detailed testing, and phased implementation can be carried out. In conclusion, continuous training of the staff members and monitoring of the system ensures that the operators will be able to take control over the automated processes and improve the overall performance of the system while remaining flexible to future changes efficiently and effectively.
Improving efficiency across the entire workflow and packaging process
Enhancing productivity across the workflow and packaging process necessitates the modification of layout designs, improvement in machine compatibility, and the upgrading of automation systems. Using synchronized machinery combined with intelligent software can facilitate the integration of phases. While predictive maintenance systems help reduce unexpected downtimes, data analytics tools help with real-time performance monitoring and bottleneck detection. Besides, the standardization of processes and materials eliminates inefficiencies and saves costs while increasing throughput. Regular enactments based on set performance metrics guarantee sustained productivity improvements over time.
Optimizing supply chain operations with automated packaging
Automated systems improve Supply chain processes significantly because efficiency and operational costs are optimized. A robotic programmable system facilitates the capture of more processing time because of its high speed, accuracy, and decisiveness during packaging-related activities. Reductions in errors and increased adaptability toward changing markets can also be achieved through systems automation. Additionally, logistics lead times are eliminated through integration of real-time tracking and management systems. Streamlined workflows, improved product quality, and waste reduction gives companies an edge over competitors.
Which automated packaging machines are right for your production needs?
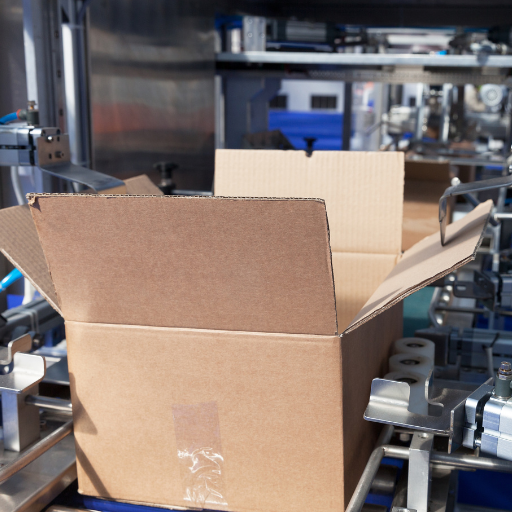
When looking for automated packaging machines, consider product type, volume of production, type of package material, and necessary automation. Semi-automatic case sealers will ease the manual effort for businesses that require some packaging. Form-fill-seal Machines and robotic palletizers are best for high-volume businesses. This will ensure precision and speed. Another critical point is flexibility; changes in production needs can be dealt with modular systems. Making sure that the new systems works with preexisting systems and evaluating maintenance requirements will help meet your workflow needs.
Reviewing the Various Types of Packaging Equipment Available
Carton Sealers
This piece of machinery seals cartons using tape or glue as efficiently as possible. Both semi-automatic and fully automatic models of these machines can be found. Case sealers are beneficial to many industries, including food and e-commerce, because they improve sealing effectiveness and reduce manual effort. Adjustable models attempt to improve adaptability with different-sized cartons.
Form-Fill-Seal Machines (FFS)
For snacks, drinks, and powders, form-fill-seal machines may be the ultimate option as they allow for three steps: forming the packaging, filling the packaging with product, and sealing the package. The machines are available in horizontal and vertical options whose specific configurations are designed for different products. Using form-fill-seal machines greatly reduces the amount of materials wasted during filling and increases production speed.
Robotic Palletizers
These machines are good for large-scale operations as robotic palletizers are known to work with high precision and speed to stack goods on pallets. Robotic palletizers are flexible, adjusting to both the shape and size of the packed goods, reducing inefficiencies caused by repetitive movements while at the same time, reducing workplace injuries.
Shrink Wrapping Machines
Shrink wrapping machines are versatile and are the best option when trying to cover items with tight and soft plastic films. They come in manual, semi-automatic, and automatic models. Often used for bundling multiple products or keeping a single item safe, shrink wrapping machines increase the appeal of the product while ensuring the item won’t be damaged during shipping.
Stretch Wrappers
Stretch wrap machines wrap plastic film around items stacked on pallets to keep them safe during storage and shipping. Stretch wrappers, which improve load stability regardless of load size and speed, come in various forms, from turntable models to high-speed rotary arm systems.
Cartoning Machines
A cartoning machine can erect, fill, and seal a carton automatically. These machines are widely used in the pharmaceuticals, cosmetics, and food & beverages for packaging tubes, bottles, or sachets. They also come in horizontal and vertical models to meet efficiency and precision requirements.
Vacuum Packaging Machines
A vacuum packaging machine removes air from packages containing perishable goods such as meat and cheese, extending the products’ shelf life. These machines come in chamber and external models that facilitate quality control by minimizing oxidation and preventing spoilage.
Labeling Machines
Automated labeling machines apply labels for products, packages, or pallets with high speed and accuracy. They can accept multiple label types, such as pressure-sensitive, shrink-sleeve, and wrap-around labels. Upstream and downstream systems can be integrated with them for a smooth flow of operations.
All of these equipment choices are designed for a specific production requirement, and they function best when the operational needs are thoroughly analyzed. Chosen properly, they increase productivity and cut costs while remaining flexible to the ever-changing market dynamics.
Solutions For Packaging Placement Lists For Unique Product Needs
When determining the appropriate packaging solutions for a product, it is imperative to check certain aspects to ensure that the solutions chosen will perform well. Other significant considerations include the kind of product, its expected shelf life, volume of production, and the specific environmental conditions that will be encountered. For instance, vacuum packaging systems are optimal for extending the freshness of perishables because they limit oxygen levels, thus curbing microbial growth and capturing great amounts of the product when it is being sealed. Vacuum level in mbar or Torr, sealing bar length, and chamber size are all direct constrains of usability and effectiveness.
If a customer requires precise branding on a product, computerized labeling machines will need to be custom-tailored to the product size, shape, and material to label them. Some of the key technical parameters are the pace of labeling, that is, labels per minute, accuracy (in millimeters or microns), and type of labels that can be used, which may include pressure sensitive and shrink sleeves. PLCs make it possible to link labeling machines with other parts of production lines for automatic operations, thereby reducing the time of stops.
Adhering to operational specifics allows positioning the new piece of work equipment in such a way that it will best meet the enterprise’s specific packaging production needs, achieving maximum efficiency, complying with the law, and minimizing costs. Such systems also can meet volume and flexibility changes to production demand, which is why they are so vital to today’s manufacturing systems.
Comparing the advantages of semi automatic and fully automatic packaging systems
Every business has different operational needs. Semi-automatic packaging systems are best for small to medium scale operations with moderate throughput requirements. These systems are cost-effective and can handle a wide range of product types. On the other hand, fully automatic systems are ideal for high-volume production because all aspects, from feeding and labeling to sealing, are automated, ensuring the utmost precision. Such fully automatic machines come at a much higher cost; however, the investment pays off in the long run due to the reduced labor and time required. Ultimately, the choice comes down to the production volume, the complexity of packaging needs, and certain budget parameters.
How to implement automated packaging solutions in your facility?
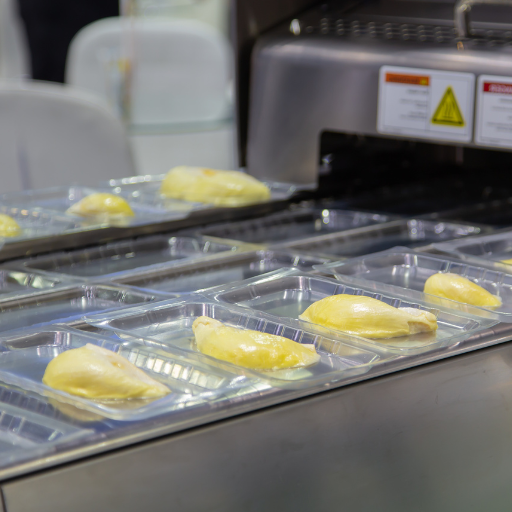
Automated packaging processes can be incorporated at your facility through a carefully designed process that considers the business’s operational goals and budgetary limitations. For starters, analyze the current workflow and packaging system to understand and pinpoint inefficiencies, bottlenecks, and problems that automation can solve. Establish specific goals such as an increase in throughput, accuracy, or reducing costs that will help you through the selection process. You also need to analyze and choose a system that gives the best production value and considers the speed, scalability and compatibility with other devices. After the purchase, devote your energy towards proper implementation and ensure layout changes and integration with other systems are done correctly. Build a set induction that focuses on the system operators and maintenance personnel to allow smooth transitioning and efficient operation, subsequently increasing the system uptime. Continuously track the system performance and adjust settings whenever necessary to ensure maximum efficiency.
Steps to evaluate your packaging procedure and find automation processes to improve it
Starting with the flow of your packaging process, I break it down into stages which range from preparing the materials to delivering the final product. After, I evaluate performance metrics such as throughput volumes, error rates, and overall spending levels to find any inefficiency or usually occurring issues. Automation tasks using technology tools can be beneficial in repetitive or monotonous tasks. Finally, I consult relevant parties like the operators and the supervisors to understand their challenges and ideas for improvement.
Merging Automatic Machinery with Pre-Existing Technology
Merging an automatic system with existing machinery requires an analysis to ensure the automation software may be used. Check the level of your current equipment and the automation system to find possible needs for interface requirements or limitations. Use programmable logic controllers (PLCs) to bridge the gaps between systems when necessary. The equipment vendor or automation seller can assist in this by providing support to enable integration. These extra steps help make the integration process less disruptive. Integration should eliminate downtime and operational interruptions and ensure efficiency over a long period.
Preparing and Training Employees for Efficient Automated Packging Processes
When training staff on systems for automated packaging, begin with a detailed explanation of the equipment, including its operating procedures and safety measures. Practical training should focus on operation systems, troubleshooting, and regular care to ensure effectiveness. Furthermore, managers should develop easy-to-understand documentation such as operational manuals and quick reference materials for the unit. Emphasizing the workflow processes requires knowing what documents and systems can be automated and what needs human inervation. Some methods are so complex that they require a combination of multiple systems to perform it effectively. Know how to schedule the work and allocate resources to maximize the system’s capabilities. Periodically reviewing and soliciting feedback from staff will further sharpen the efficiency of operations while enhancing the ability to adapt to the improvements.
How to calculate the ROI of investing in automated packaging solutions?
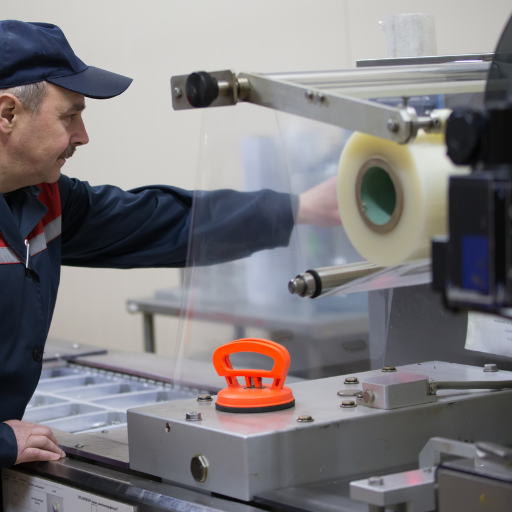
To calculate the ROI of automated packaging solutions, a comparison has to be made between the ROI benefits and costs. The first step is to assess the investment level, including expenses such as equipment purchasing, installation, and staff training. From there, determine the benefits of such savings, including increased efficiency, reduced expenditures, lower material wastes, and increased output movements. Other contributors to value in the long term include improved quality of goods and reduced downtimes. Afterward, the total cost investments alongside the initial expenditures will be determined. Use the formula ROI = (Net Benefits / Total Investment) * 100 to analyze. This ROI evaluation shows the impact of the investment and makes a strong case for it.
Evaluating labor, material, and time cost reductions
For this reason, when estimating cost savings, the core points of interest are always labor, materials, and time. Automation in packing processes dramatically reduces labor costs due to low reliance on manual processes, oftentimes achieving better results when there are lesser personnel. It also reduces the expenditure of material components by eliminating wastes on cuts and folds that would have otherwise been produced with simple processes. Savings in time are realized through smoothing workflows alongside lessened delays from bottlenecks and human mistakes. These changes transform into tangible monetary savings, emphasizing automation’s value.
Measuring improvements in productivity and output
Productivity and output improvements are measured with key performance indicators (KPIs) like cycle time, production throughput, and defect rates. If there is more automation, processing times are lower, and the number of finished products is higher. Further, consistent quality control ensures less rework and discarded items so resources can be used effectively. These indicators prove the operational benefits gained through automation and how efficient the investment can be for the outcomes achieved through automation compared to resources used.
Long-term benefits of scalable automated packaging systems
Scalable automated packaging systems bring long-term advantages by enhancing operational efficiency and decreasing labor costs. The systems increase throughput while minimizing errors, achieving quality and reliability at scale. Furthermore, automation increases flexibility to adapt to changes in production volume and packaging styles over a business lifecycle. The adoption of such systems could also result in considerable material savings through precise usage, which aids in sustainability and waste reduction. Most importantly, these systems lead to improved supply chain management and a better ROI.
Reference sources
Frequently Asked Questions (FAQs)
Q: What are the benefits of using automated packaging solutions?
A: Automated packaging solutions offer numerous benefits, including increased efficiency, reduced labor costs, improved accuracy, and a smaller environmental footprint. These packing machines streamline the entire process, allowing for faster production rates and consistent packaging quality. By investing in an automatic packing machine, businesses can enhance their productivity and reduce waste, ultimately leading to cost savings and improved customer satisfaction.
Q: How do automatic packing machines work?
A: Automatic packing machines are designed to handle various stages of the packaging process without manual intervention. These machines typically include conveyors, sealing machines, and other components that work together to package products efficiently. The process often starts with product sorting and alignment, followed by wrapping or bagging, sealing, and labeling. Packaging automation ensures that every package is consistently packed and sealed, reducing errors and improving overall quality control.
Q: What types of industries can benefit from packaging automation?
A: Packaging automation can benefit a wide range of industries, including food and beverage, pharmaceuticals, cosmetics, electronics, and e-commerce. Any business that deals with high-volume packaging or requires precise and consistent packaging can gain advantages from automated packing solutions. These machines are versatile and can be customized to handle different products and packaging materials, making them suitable for various applications across multiple sectors.
Q: How can automated packing machines improve efficiency in my production process?
A: Automated packing machines can significantly improve efficiency by increasing production speed, reducing downtime, and minimizing human error. These machines are capable of handling high volumes of products consistently, working at speeds that surpass manual packaging methods. By integrating packaging automation into your production line, you can achieve higher throughput, better resource utilization, and improved overall operational efficiency.
Q: What factors should I consider when choosing an automatic packaging machine for my business?
A: When selecting an automatic packaging machine for your business, consider factors such as production volume, product specifications, packaging materials, available space, and budget. It’s essential to choose a machine that can handle your current production needs and accommodate future growth. Additionally, consider the machine’s flexibility to package different products, ease of operation, maintenance requirements, and compatibility with your existing production line. Consulting with packaging technology experts can help you find the right machines for your business needs.
Q: Are there eco-friendly options available in automated packaging solutions?
A: Yes, many automated packaging solutions offer eco-friendly options. Some machines are designed to work with sustainable packaging materials, such as biodegradable films or recycled corrugate. Additionally, automated systems can help reduce waste by optimizing material usage and minimizing packaging errors. By investing in packaging automation that supports sustainable practices, businesses can reduce their environmental impact while still maintaining efficient operations.
Q: How can fully automated packaging systems integrate with existing production lines?
A: Fully automated packaging systems can be integrated with existing production lines through careful planning and implementation. This often involves assessing your current setup, identifying integration points, and selecting machines that are compatible with your existing equipment. Many packaging automation providers offer customizable solutions that can be tailored to fit seamlessly into your production process. It’s important to work closely with the equipment supplier to ensure smooth integration and minimal disruption to your operations during implementation.
Q: What kind of return on investment can I expect from investing in an automatic packing machine?
A: The return on investment (ROI) for an automatic packing machine can vary depending on factors such as production volume, labor costs, and efficiency gains. However, many businesses report significant ROI through reduced labor costs, increased production capacity, improved product quality, and decreased waste. While the initial investment may be substantial, the long-term benefits of packaging automation often outweigh the costs. To get a clearer picture of potential ROI for your specific situation, it’s advisable to conduct a thorough cost-benefit analysis or consult with packaging automation experts.